Zinc alloy casting: Process and technology guide
Zinc alloy casting is a metal processing technology widely used in modern manufacturing. With its excellent fluidity and plasticity, it has shown unique advantages in many fields. This article will explore in depth the process types, surfaces and applications of zinc alloy casting in different industries.
1.Definition, classification and characteristics of zinc alloy
(1) Definition
Zinc alloy is an alloy material formed by adding aluminum, copper, magnesium and other elements to zinc as a matrix. It not only has good mechanical properties, but also has excellent processability and corrosion resistance. It is widely used in the manufacture of various precision parts and structural parts.
(2) Classification
1) Classification by alloy composition:
Zinc alloys can be divided into Zn-Al series, Zn-Cu series, Zn-Pb series and Zn-Pb-Al series.
2) Classification by processing method:
Zinc alloys can be divided into two categories: casting alloys and deformation alloys. Casting zinc alloys are divided into pressure casting zinc alloys and gravity casting zinc alloys according to different casting methods.
3) Classification by performance and use:
Zinc alloys can be divided into creep-resistant zinc alloys, superplastic zinc alloys, damping zinc alloys, mold zinc alloys, wear-resistant zinc alloys, anti-corrosion zinc alloys, structural zinc alloys, etc.
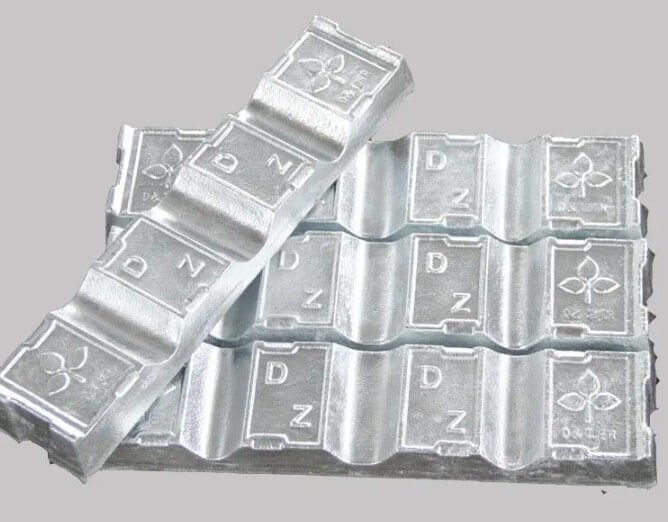
(3) Features
1) Good corrosion resistance:
A stable oxide film is easily formed on the surface of zinc alloys to protect the substrate from corrosion, and is suitable for applications that require corrosion resistance.
2) Good machinability:
Zinc alloys are easy to process and form, and can be made into various shapes and structures by hot press casting, cold press casting, injection molding, etc.
3) Excellent mechanical properties:
Zinc alloys have high strength and hardness, which can meet the requirements of various engineering and application requirements.
4) Low melting point:
Zinc alloys have a low melting point, are easy to process and cast, and are suitable for use under low temperature conditions.
5) Environmental protection:
Zinc is a recyclable material, so zinc alloys have good environmental protection.
6) Lightweight:
Zinc alloys are lighter than traditional cast iron and steel materials and are suitable for manufacturing lightweight components.
2.Zinc alloy casting process
According to the different casting methods, zinc alloy casting can be divided into pressure casting zinc alloy and gravity casting zinc alloy. There are significant differences between these two methods in process characteristics, application fields and product performance.
(1) Pressure casting zinc alloy
Pressure casting is a high-speed, high-pressure casting process. In this process, the molten zinc alloy is quickly pressed into the mold cavity under high pressure and cooled and solidified in a short time. The main features of this method include:
1) High-efficiency production:
Due to the fast filling speed and short production cycle, it is very suitable for large-scale production.
2) High dimensional accuracy:
The metal flow under high pressure makes the casting size precise and the surface finish high.
3) Complex shape adaptability:
It can produce thin-walled and complex-shaped parts.
4) Strength and hardness:
Due to rapid cooling, zinc alloy casting parts have fine structure and good mechanical properties.
5) Diverse surface treatment:
Die castings can be subjected to various surface treatments such as electroplating and spraying to improve product aesthetics and corrosion resistance.
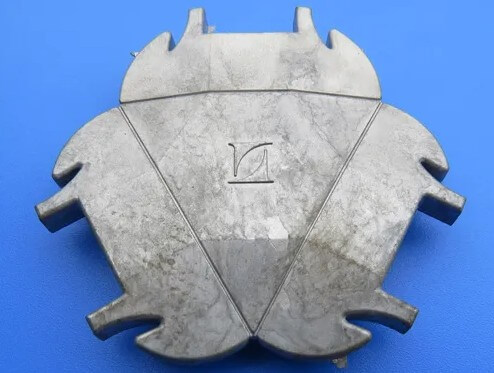
(2) Gravity casting zinc alloy
Gravity casting relies on the gravity of the molten metal to flow into the mold for molding. This method is relatively simple and low-cost. Its main features include:
1) Cost-effectiveness:
The equipment investment and operating costs are relatively low.
2) Suitable for thick-walled parts:
Gravity casting is suitable for the production of castings with thicker walls because the molten metal can better fill the thick-walled parts under the action of gravity.
3) Defect control:
With proper control, casting defects such as pores and shrinkage holes can be reduced.
4) Production flexibility:
Suitable for small batch and multi-variety production needs.
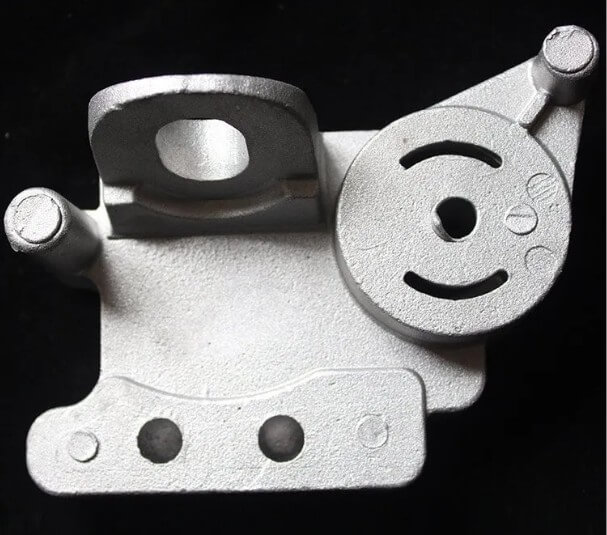
(3) Application areas
1) Pressure casting zinc alloy:
Widely used in automotive accessories, electronic components, some mechanical parts, home appliance housings, toys and decorations.
2) Gravity casting zinc alloy:
Commonly used in the production of lamps, furniture accessories, certain mechanical parts and some electrical components.
Summary:
Pressure casting and gravity casting each have their own unique advantages. The choice of method depends on the product design requirements, production scale and cost considerations. Pressure casting is suitable for large-scale production of thin-walled, precise and complex-shaped zinc alloy casting parts, while gravity casting is more suitable for small-scale production of zinc alloy casting parts with thicker walls and higher cost control requirements. Understanding these differences can help companies make the best choice based on specific needs and improve production efficiency and product quality.
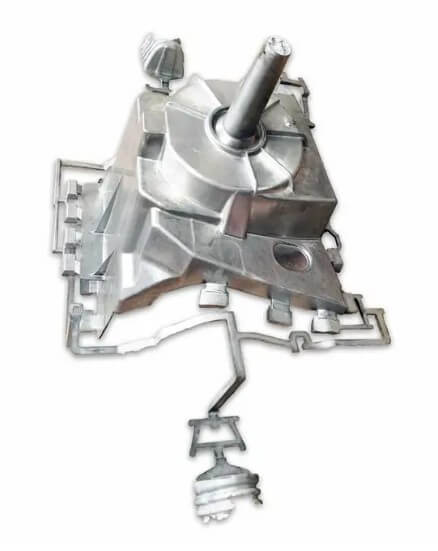
3.Common problems and solutions for zinc alloy casting
(1) Surface blistering:
1) Causes:
Porosity (pores and shrinkage cavities), harmful impurities in zinc alloy components (lead, cadmium, tin).
2) Solution:
Control the generation of pores and reduce the amount of gas mixed into the casting; control the content of harmful impurities in the alloy raw materials, especially lead <0.003%.
(2) Cracks:
1) Causes:
Water marks, cold shut marks, hot cracks, uneven thickness of castings, premature ejection, uneven force during ejection, and excessive mold temperature.
2) Solution:
The thickness of the die casting should not change drastically to reduce stress; adjust the relevant zinc alloy casting process parameters; reduce the mold temperature.
(3) Surface patterns and metal flow marks:
1) Reason:
The flow channel leading to the casting inlet is too shallow and the injection pressure ratio is too large.
2) Solution:
Deepen the gate flow channel and reduce the injection pressure ratio.
(4) Small bulges on the surface:
1) Reason:
The surface is rough, and there are scratches or pits and cracks on the inner surface of the cavity.
2) Solution:
Polish the cavity, replace the cavity or repair it.
(5) Impurities:
1) Reason:
The metal liquid is not clean, the alloy composition is impure, and the mold cavity is not clean.
2) Solution:
Remove impurities and slag before pouring, replace the alloy, and clean the mold cavity.
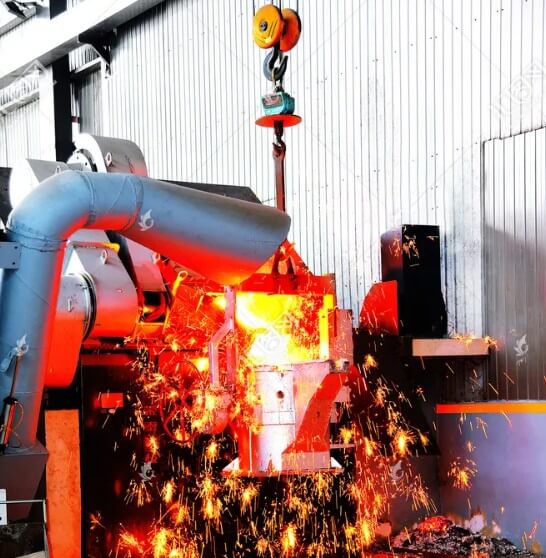
(6) Surface cracks or local deformation:
1) Cause:
The ejector pins are unevenly distributed or insufficient in number, the ejector pin fixing plate is tilted during operation, and the casting wall is too thin.
2) Solution:
Increase the number of ejector pins, adjust their distribution position, adjust and reinstall the ejector pin fixing plate.
(7) Surface pores:
1) Cause:
Too much lubricant, the vent hole is blocked.
2) Solution:
Use lubricant reasonably, add and repair vent holes.
(8) Surface shrinkage:
1) Cause:
The processability of the die casting is unreasonable, the wall thickness varies too much, and the molten metal temperature is too high.
2) Solution:
Add process holes in the thick wall to reduce the molten metal temperature.
4.Surface treatment of zinc alloy casting parts
Surface treatment of zinc alloy casting is an important process to improve the appearance, corrosion resistance and functionality of zinc alloy products. The following are several common surface treatment methods for zinc alloy castings:
(1) Electroplating:
A layer of metal, such as copper, nickel, chromium, etc., is plated on the surface of the zinc alloy by chemical methods to enhance its aesthetics and corrosion resistance. Direct chromium plating can improve the hardness and wear resistance of the casting.
(2) Painting:
Various paints, such as epoxy resin paint or amine paint, are applied to the surface of the zinc alloy to enhance its corrosion resistance and aesthetics. Phosphate or chromate solution treatment is usually required before painting.
(3) Metal spraying:
A very thin metal film is applied to the surface of the treated parts under high vacuum, which can simulate the appearance of copper, silver, brass, gold, etc., and is mostly used for die castings.
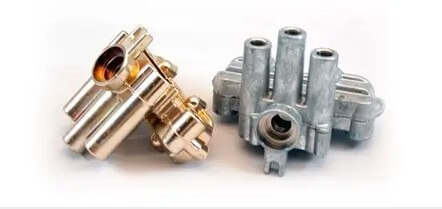
(4) Anodizing:
Anodizing is performed at a voltage not exceeding 200V to form a porous surface, which can be sealed in a heated water glass dilute solution or with an organic coating, effectively improving the corrosion resistance of the zinc alloy.
(5) Baking varnish:
The baking varnish process includes degreasing, washing, rust removal, neutralization, phosphating, drying, disk spraying, touch-up paint, preheating furnace baking and main furnace baking to improve the appearance and corrosion resistance of zinc alloy die castings.
(6) Chemical film treatment:
Chromate treatment can improve the corrosion resistance of zinc alloy products, increase the beauty of the product surface, and form a protective film on the product surface.
(7) Electrostatic spraying:
Electrostatic spraying can form a protective film for zinc alloy casting parts, making the casting surface smoother, more beautiful, more textured, and improve corrosion resistance.
5.Summary
As an important engineering material, zinc alloy is widely used in the casting industry. And zinc alloy casting parts occupy an important position in modern industry with their excellent performance and broad application prospects. By continuously optimizing the zinc alloy casting process, the application field of zinc alloy casting can be further expanded.