The Development of Die Casting in the Automotive Industry: Technology, Materials and Market Trends
In recent years, automakers have strived to build lightweight vehicles while ensuring durability, and die casting has become one of the most valuable key technologies in the automotive parts industry. Today, the number of die castings used in automobiles is increasing every day.
1.Reasons for the sharp increase in die casting demand among automakers
(1) Optical device production
The automotive industry is now facing stricter fuel economy standards, and the pressure to produce more efficient vehicles continues to grow. Against this backdrop, automakers have adopted aluminum die casting technology to achieve this goal. Aluminum, as a lightweight metal with an excellent strength-to-weight ratio, has become the first choice for casting engine and wheel parts. By ensuring the quality of both external and internal components, manufacturers can create lighter and safer vehicles.
(2) Improving Automation and Flexibility
The popularity of die casting in the automotive industry continues to grow with the increasing use of advanced technologies. Automation of the production process makes it more efficient and productive, ensuring that more automotive cast parts can be manufactured. Moreover, this method is very effective in developing complex automotive parts with unique designs. The technology helps in producing parts of complex shapes and sizes and can easily install them in vehicles.
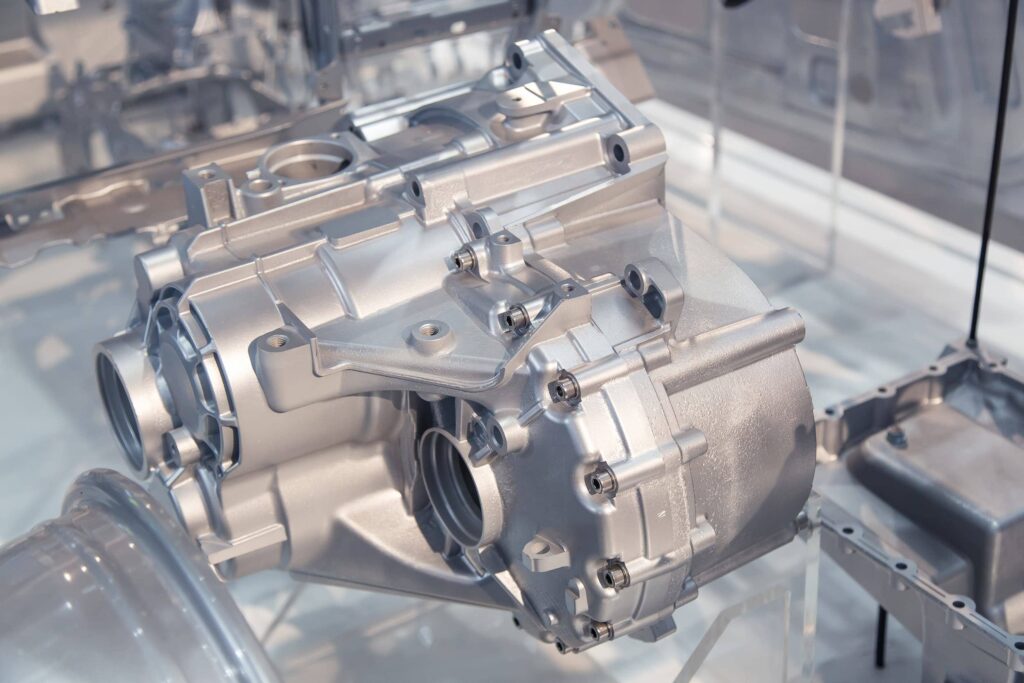
(3) Improve component stability
Automotive die casting can also produce environmentally friendly and sustainable automotive parts. This means that the process of casting automotive parts does not harm the environment. At the same time, the ability to recycle the materials used in these components makes them more valuable. For example, recycled aluminum can be recycled indefinitely.
Materials and advantages widely used in die casting in the automotive industry
(1) Zinc die castings
Zinc die castings account for nearly 28% of automotive die castings. Although it was mainly used in the industrial field in the past and was valued for its high toughness and ductility, it is now widely popular in the automotive industry. Because it can be cast in a hot chamber die casting machine, the process can achieve nearly 100% accuracy and produce parts with smooth surfaces without further processing.
Advantages of zinc die casting include:
1) Enhanced flexibility.
Zinc is superior to other casting materials in terms of fluidity. Although aluminum is lighter than zinc, zinc can help produce complex parts with complex shapes and thin walls.
2) High corrosion resistance.
Zinc reacts very little in the atmosphere, and parts made from it are usually durable and require little maintenance for long-term use.
3) Excellent thermal and electrical conductivity.
In the era of modern cars and smart machines, zinc can effectively conduct heat and electricity, making it an ideal choice.
4) Sustainable development and environmental friendliness.
Zinc is environmentally friendly and easy to recycle, which can prevent excessive waste and the release of harmful substances into the environment.
5) Dimensional stability.
Zinc is superior to other cast metals in dimensional stability, giving the product excellent finish and beauty.
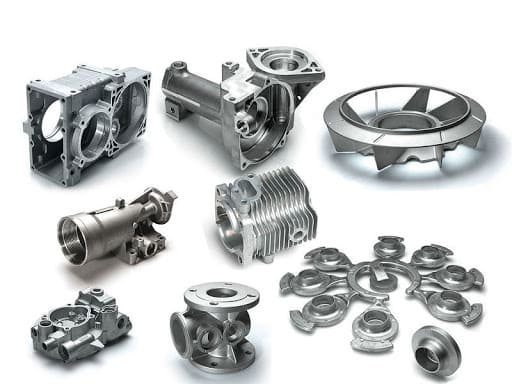
(2) Aluminum die castings
Aluminum is another commonly used metal for the production of automotive parts. It is lightweight and has good dimensional stability, making it the first choice for thin-walled mechanical parts. Low-density aluminum is more widely used in the automotive industry, and automotive castings made from it are highly durable even at high temperatures.
The aluminum die casting process can produce thousands of castings simultaneously using a single steel mold, and is suitable for manufacturing engine brackets, gearboxes, valve bodies, hydraulic cylinders and other parts.
Advantages of aluminum die castings:
1) Lightweight component manufacturing. To meet fuel economy standards, automakers are turning to aluminum castings to produce strong, efficient, durable, ultra-light components.
2) Improved flexibility. Aluminum is more flexible than many other metals, allowing for the development of complex die-cast aluminum automotive parts with unique designs.
3) Safety and reliability. Aluminum castings produce heat- and friction-resistant parts to protect drivers and passengers from accidents.
4) Environmental protection. Aluminum is easily recycled, and some aluminum alloys can be recycled indefinitely, making it more environmentally friendly. The production of aluminum parts is less polluting and more efficient.
(3) Magnesium die castings
Magnesium is another flexible, lightweight metal used in die casting. It contains other lighter metals, offering a wide range of possibilities for the production of complex, thin-walled parts. It also has an incredible strength-to-weight ratio and excellent heat resistance.
The advantages of magnesium die casting include:
1) Lightweight automotive manufacturing. Magnesium is a lightweight metal that, when combined with other lighter metals, can help produce lightweight auto parts with good performance.
2) Improved corrosion resistance. The new magnesium alloy has higher purity and better corrosion resistance than aluminum or steel alloys.
3) Environmentally friendly. Magnesium is a natural metal extracted from minerals, seawater and salt water.
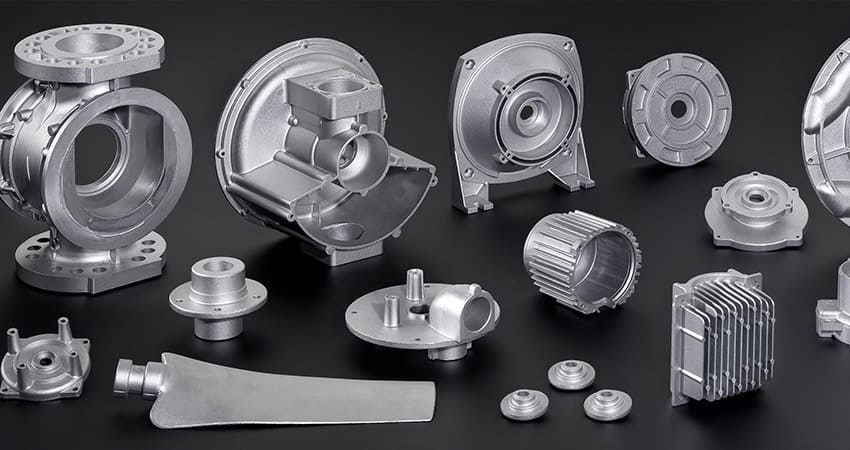
3.Various automotive die castings
Automotive die casting can produce complex parts with high strength and improved aesthetics. It has a wide range of applications, including engine parts, motor and stepper motor mounting brackets, electronic covers such as gearboxes, telematics and electronic equipment shielding, airbag sensors and housings, oil inlet parts, air conditioning systems, belt traction shaft safety, complex lock cylinders, powertrain and chassis components, autonomous vehicle connectors, sensor and lidar housings, rugged power steering and braking systems, etc.
4.Automotive die casting market trends
According to reports, the automotive die casting market is expected to exceed US$20.31 billion by 2028. Revenue in 2021 was US$11.1 billion and will grow at an annual rate of 7.8% from 2022 to 2028. The growth of automotive parts is driven by the increase in passenger car sales due to the increase in income of the middle-income group. Furthermore, die casting process helps in reducing the weight of vehicles, thereby minimizing fuel emissions and improving fuel efficiency. Green component manufacturing will lead the growth of these market trends.