Analysis of Usual Manufacturing Defects in High Pressure Die Casting
As an efficient metal forming technology, high-pressure die casting occupies an important position in modern manufacturing.
However, when producing, usual manufacturing defects in high pressure die casting often trouble production companies. How to effectively prevent these defects and improve the quality of castings has become the focus of industry attention. This article will deeply explore the causes and preventive measures of usual manufacturing defects in high pressure die casting, and provide a full range of solutions from the technical and operational levels to help companies create flawless castings.
1.Introduction to die casting technology
(1) Basic principles of die casting technology
High-pressure die casting is an efficient metal forming technology. Its basic principle is to inject liquid metal into the mold cavity at high temperature, high pressure and high speed, and quickly cool and solidify to form a casting. This technology can produce metal parts with complex shapes and precise dimensions, and is widely used in many fields such as automobiles, electronics, and aerospace.
(2) The importance of die casting technology in modern industry
In modern industrial production, die casting technology plays a vital role. With the continuous advancement of industrial technology and the changes in market demand, die-casting technology has become an indispensable process for manufacturing high-performance and lightweight products because it can produce complex-shaped and thin-walled metal parts. In the fields of automobiles, aerospace, etc., the application of die-casting has greatly promoted their lightweight process, which is of great significance to improving fuel efficiency and reducing emissions.
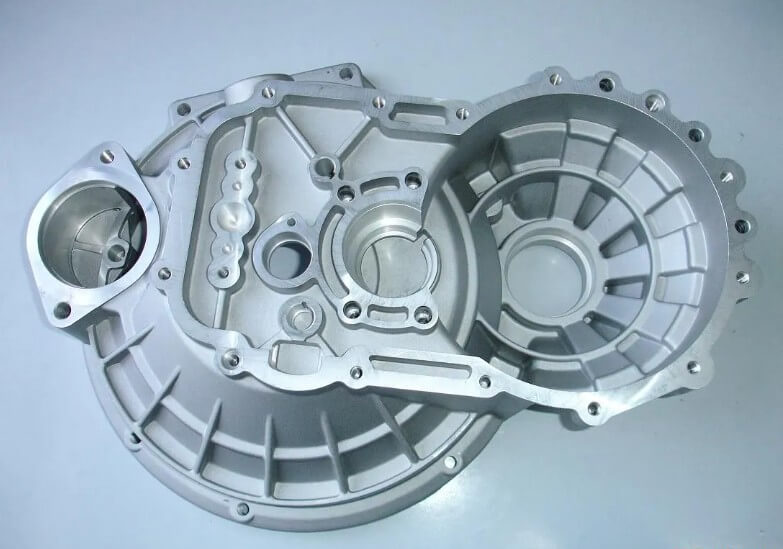
2.Usual manufacturing defects in high pressure die casting
Although high-pressure die-casting technology is advanced, the manufacturing defects that come with it cannot be ignored. Common defects such as shrinkage, cracks, bubbles and patterns seriously affect the performance of castings. The following will comprehensively analyze the causes of these defects and propose targeted strategies from the aspects of mold optimization, process parameter control, machine maintenance, etc., aiming to reduce the occurrence of defects and improve production efficiency.
(1) Usual manufacturing defects in high pressure die casting: cold shut and pattern
1) Defect characteristics:
Cold shut is manifested as irregular smooth stripes on the surface of the casting, and the pattern is a stripe that is consistent with the flow direction of the molten metal. The color is different from the metal matrix and there is no development trend.

2) Causes:
- The molten metal temperature is too low.
- Punch speed is too slow.
- Die casting mold temperature is too low.
- Poor exhaust.
- Unreasonable gate design.
3) Solution:
- Maintain the correct molten metal temperature and check the temperature control device.
- Determine the correct injection speed and keep it constant.
- Ensure that the temperature of the die casting mold is appropriate.
- Add or modify vents and overflow grooves.
- Improve gate design to avoid splashing into the cavity.
(2) Usual manufacturing defects in high pressure die casting: sticking mold
1) Defect characteristics:
Metal adheres to the surface of the die casting mold, resulting in rough casting surface or metal falling off.
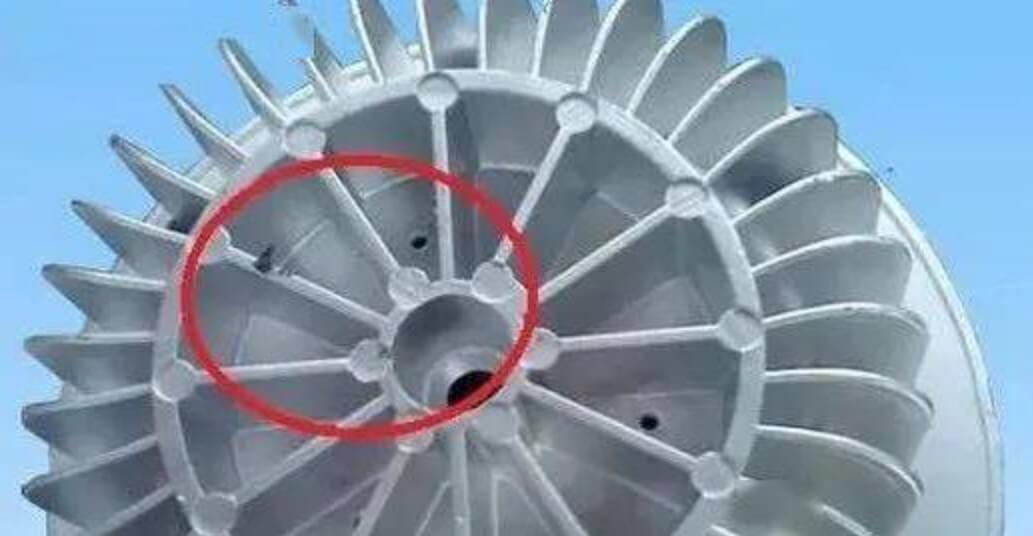
2) Causes:
- Molten metal temperature is too high.
- Die casting mold temperature is too high or too low.
- Improper use of release agent.
- There is a hot spot in the die casting mold.
- The iron content in the aluminum alloy is too low.
3) Solution:
- Maintain the correct pouring temperature.
- Maintain the correct die casting mold temperature.
- Use mold release agent correctly.
- Ensure cooling water flow or increase cooling rate.
- Increase iron content in aluminum alloy to 1.0%.
(3) Usual manufacturing defects in high pressure die casting: bubbles
1) Defect characteristics:
There are pores on the surface or inside of the casting, and the subcutaneous pores bulge to form bubble-like defects.
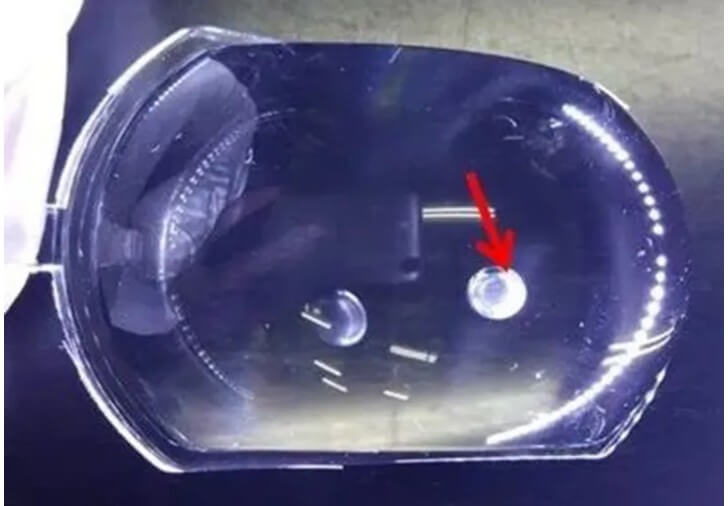
2) Causes:
- Too much gas entrained in the metal.
- The temperature of the die casting mold is not high.
- Too much die casting coating.
- The pouring system is unreasonable and the exhaust is not smooth.
- The mold is opened too early.
3) Solution:
- Add overflow grooves and exhaust holes to the defective parts.
- Maintain the correct temperature of the molten metal and die casting mold.
- Reduce the amount of coating and ensure uniform spraying.
- Modify the pouring system to ensure smooth exhaust.
- Extend the pressure holding time and mold retention time.
(4) Usual manufacturing defects in high pressure die casting: Cracks
1) Defect characteristics:
Straight or wavy cracks appear on the surface or inside of the casting, with narrow and long lines, and tend to develop under the action of external force.
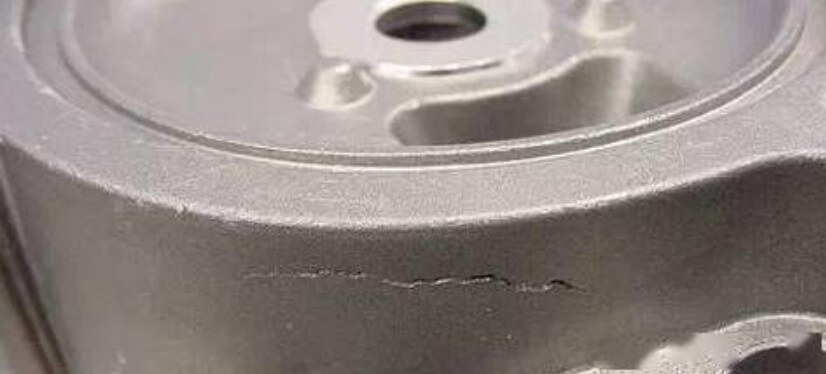
2) Causes:
- The fillet is too small.
- The ejector layout is unreasonable.
- The temperature of the aluminum liquid or mold is too low.
- Improper operation when removing the gate.
- The iron content in the aluminum liquid is too high.
3) Solution:
- Negotiate with the customer to increase the fillet.
- Optimize the ejector layout and try to arrange the ejector at the stress position.
- Check and adjust the temperature of the aluminum liquid and mold.
- Use a saw or punch to remove the gate.
- Reduce the iron content in the aluminum liquid.
(5) Usual manufacturing defects in high pressure die casting: Deformation
1) Defect characteristics:
The shape of the casting changes and cannot meet the design requirements.
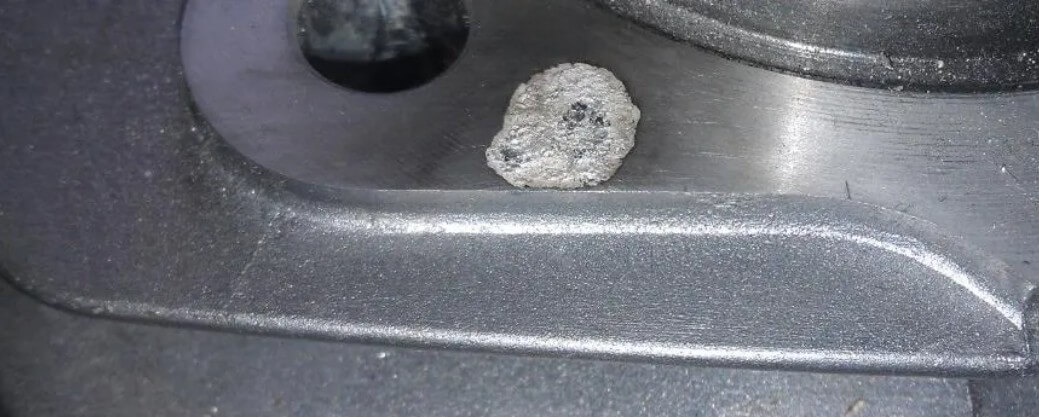
2) Causes:
- Unbalanced ejection.
- The product naturally cools and deforms after leaving the mold.
- Sticking to the fixed mold causes deformation.
- Improper method of removing the gate.
- Improper product placement.
3) Solution:
- Check whether the ejector layout is reasonable and optimize the ejector position.
- Strengthen mold cooling, especially cooling around the product.
- Add undercuts to the corresponding part of the movable mold or increase the draft angle of the fixed mold.
- Use a punch or saw to remove the gate.
- Correct the deformed product later.
(6) Usual manufacturing defects in high pressure die casting 6: shrinkage and shrinkage
1) Defect characteristics:
Irregularly shaped holes appear inside or on the surface of the casting. Large and concentrated holes are shrinkage holes, and small and scattered holes are shrinkage holes.
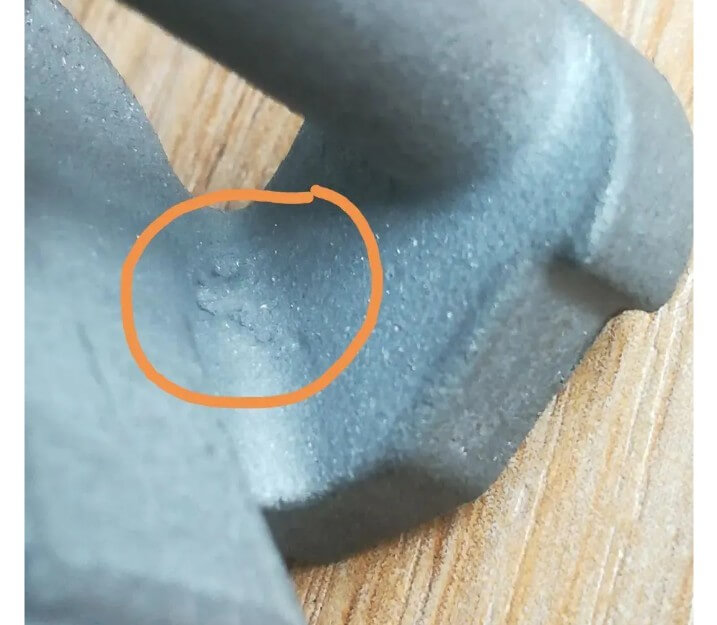
2) Causes:
- Pouring temperature is too high.
- Low injection pressure.
- Poor casting structure, hot spots, uneven wall thickness.
- Small inner gate.
3) Solution:
- Change the casting structure to eliminate metal accumulation and large cross-sectional changes.
- Reduce the pouring temperature if possible.
- Increase the injection pressure.
- Improve the pouring system appropriately to better transmit the pressure.
(7) Common manufacturing defects in high-pressure die casting: inclusions
1) Defect characteristics:
Irregularly shaped holes on the surface or inside of the casting contain debris.
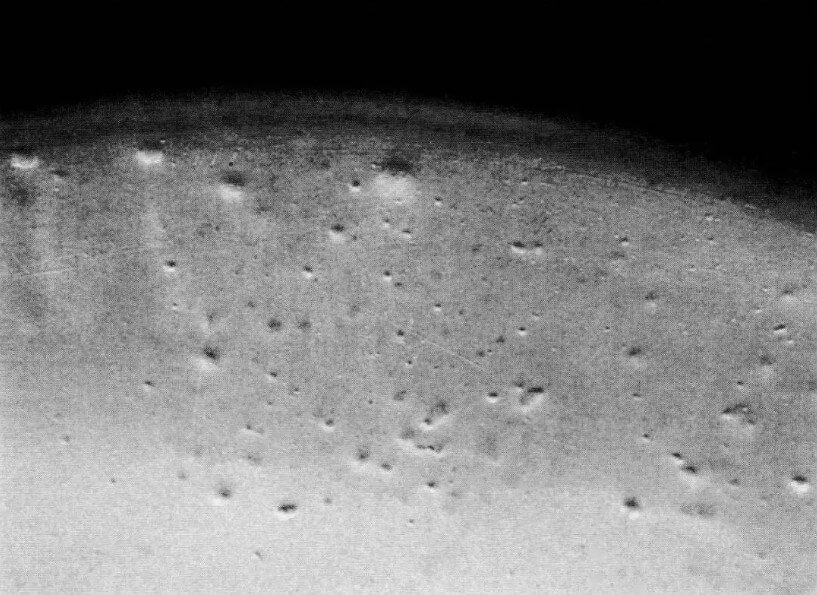
2) Causes:
- Impure charge.
- Insufficient alloy purification or slag removal.
- Die casting mold is not clean.
- Too much graphite inclusions in the coating.
3) Solution:
- Ensure that the charge is clean.
- Alloy purification, choose a flux that is easy to remove slag.
- Pay attention to die casting mold cleaning.
- Graphite coating must be mixed evenly and kept pure.
(8) Usual manufacturing defects in high pressure die casting: flying material
1) Defect characteristics:
Excess metal appears on the edge of the casting, forming flash or burrs.
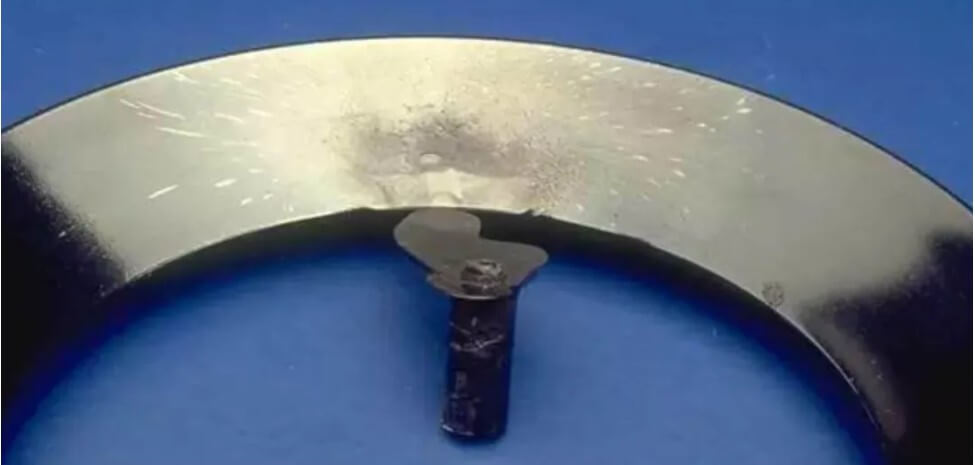
2) Causes:
- Insufficient clamping force.
- Unbalanced force on the mold.
- There are debris on the parting surface.
- The casting pressure is too high.
3) Solution:
- Calculate and verify the projection area and check the machine working condition.
- Adjust the injection center to confirm the center position of the product on the die casting machine plate.
- Clean the parting surface regularly during production.
- Adjust the machine to check the process parameters to ensure that the evaluation before mold making meets the standards.
3.Summary
Through the above detailed analysis of Usual manufacturing defects in high pressure die casting, it can be seen that each defect has its unique characteristics and causes. To solve these defects, it is necessary to start from mold design, die casting process parameters, metal liquid quality, mold maintenance and other aspects, and make systematic improvements and optimizations. Only in this way can the quality of die castings be effectively improved and meet customer needs.