Titanium alloy investment casting: technology, advantages and disadvantages, and applications
As a key metal material processing technology, titanium alloy investment casting has played an increasingly important role in the fields of aviation, aerospace, and medical treatment in recent years. This article will focus on the summary of titanium alloy investment casting technology, key technical issues, advantages and disadvantages, and application fields.
1.Overview of titanium alloy investment casting technology
(1) Characteristics and applications of titanium alloys
Titanium alloy is a metal material with excellent performance. It is widely used in many fields due to its unique properties. The following are the main characteristics of titanium alloys:
1) High strength and low density:
The tensile strength of titanium alloy can be as high as 1300 MPa, while its density is only 4.5 g/cm3, which is about 60% of steel. This high specific strength makes titanium alloy very advantageous in fields that require strength and lightweight design, such as aerospace and automotive industries.
2) Good corrosion resistance:
A dense oxide film is easily formed on the surface of titanium alloy, which makes it have excellent corrosion resistance in harsh environments such as seawater and strong acid. Therefore, titanium alloys are often used in chemical equipment, marine engineering and medical equipment.
3) Excellent thermal properties:
Titanium alloys have excellent high temperature stability and low thermal expansion coefficient. Its melting point exceeds 1650 degrees Celsius, and it can maintain stable mechanical properties even in high temperature environments above 600°C. In addition, titanium alloys also show good toughness at low temperatures and are suitable for extremely cold environments.
4) Good biocompatibility:
Titanium alloys are non-toxic and have excellent compatibility with human tissue and blood. Therefore, they are widely used in the medical field to manufacture artificial joints, dental implants, etc.
5) High hardness and low elastic modulus:
Titanium alloys have a high hardness (HRC is 32-38), and their elastic modulus is about 57% of that of steel, which makes it have better fatigue resistance when subjected to alternating stress.
6) Unique physical properties:
Titanium alloys are non-magnetic and have strong anti-damping properties. These characteristics make them have special application value in audio equipment, medical ultrasound equipment and other fields.
7) Good processing performance:
Titanium alloy has good weldability and machinability, and can be made into complex parts through various processes such as casting, forging, welding, etc.
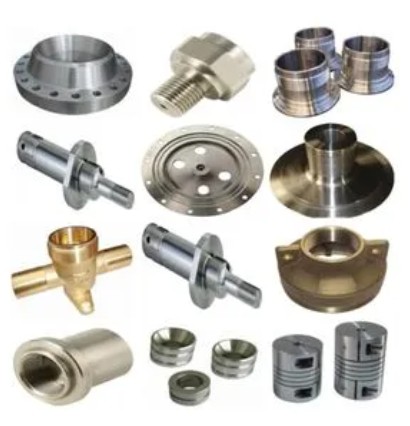
(2) Basic principles and processes of investment casting
Investment casting, also known as lost wax casting, is a precision casting method. Its basic principle is to use fusible materials (such as wax or plastic) to make a model, then coat the surface of the model with refractory materials, harden it to form a shell, and then melt the model by heating to discharge it, so as to obtain a casting without a parting surface, and finally pour molten metal to obtain a casting. The following is the basic process of investment casting:
1) Mold making:
First, you need to make a wax mold or plastic mold with the same shape as the required casting. This process can be completed by pressing, injection molding, etc.
2) Mold shell making:
Multiple layers of special refractory coating are applied to the surface of the wax mold, and sand is sprinkled after each layer to increase the strength of the shell. This process needs to be repeated many times until the shell reaches the required thickness.
3) Demolding:
After the shell is dried and hardened, the wax mold is melted and flows out of the shell by heating (such as using hot water or steam), thereby forming a casting cavity inside the shell.
4) Firing:
The shell after demolding is placed in a high-temperature furnace for baking to remove residues and improve the strength and high-temperature resistance of the shell. The baking temperature is usually between 800-1000℃.
5) Pouring:
Put the baked shell into a sand box, fill it with dry sand for molding, and then pour molten metal. The metal liquid evaporates or melts the foam plastic in the shell at high temperature to form a casting.
6) Cleaning and grinding:
After the metal cools and solidifies, break the shell, take out the casting, and clean and grind it to remove surface defects such as sand sticking and flash to obtain the final precision casting.
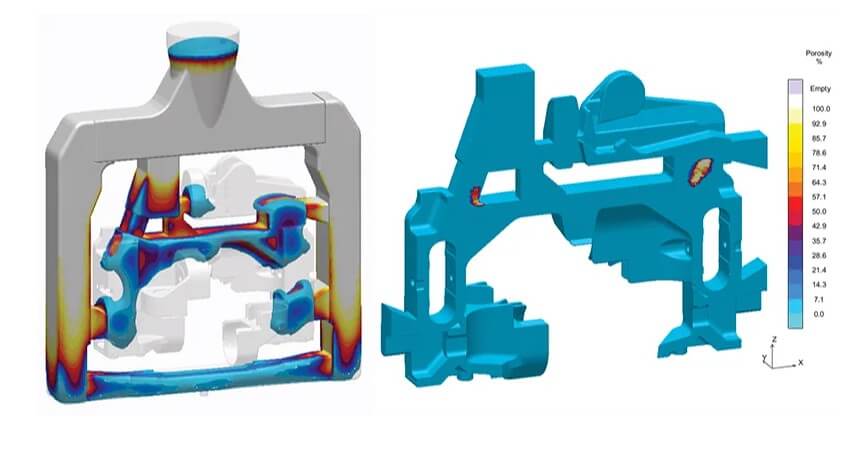
2.Key technologies of titanium alloy investment casting
Titanium alloy investment casting is a precision casting technology that can produce castings with high dimensional accuracy and low surface roughness, especially for parts with complex shapes. The following are the key technical points of titanium alloy investment casting:
(1) Selection of shell material:
Since titanium alloy has high chemical activity at high temperature and easily reacts with refractory materials, it is crucial to select a suitable shell material. Commonly used shell materials include graphite, refractory metal powder and inert oxide shell. Graphite shell has high refractoriness and low thermal expansion coefficient, but has certain reactivity to molten titanium alloy. Oxide ceramic materials such as zirconium oxide (ZrO2) and yttrium oxide (Y2O3) have better chemical stability, but the cost is higher.
(2) Selection of binder:
The binder is used in the preparation of the shell and has a direct impact on the quality of the casting and the production cycle. Commonly used binders include synthetic resins, colloidal graphite, zirconium acetate, etc. They need to generate stable oxides such as Al2O3, ZrO2, CaO and Y2O3 after calcination to ensure the inertness of the shell surface layer.
(3) Melting process:
The melting of titanium alloys is usually carried out under vacuum or inert gas protection to prevent titanium from reacting with oxygen, nitrogen, etc. in the air. Commonly used melting methods include consumable electrode arc furnace melting, electron beam furnace melting, etc. The temperature needs to be precisely controlled during the melting process to ensure the uniform composition and stable performance of the titanium alloy.
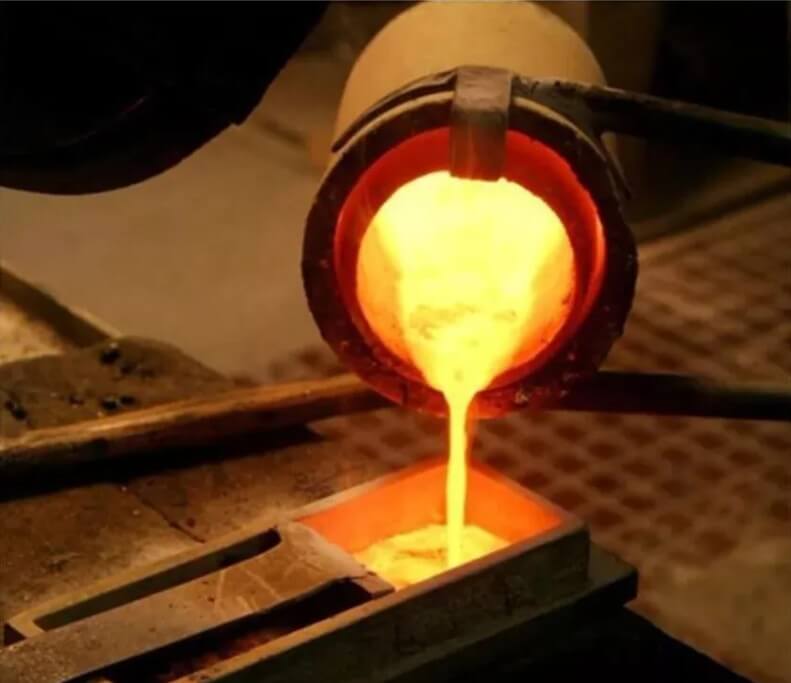
(4) Casting process:
During the titanium alloy investment casting process, it is necessary to control parameters such as pouring temperature and pouring speed to reduce casting defects such as shrinkage cavities and cracks. At the same time, the casting may generate large thermal stress during the solidification process, so appropriate cooling measures, such as hot isostatic pressing (HIP) treatment, are required to improve the mechanical properties and dimensional stability of the casting.
(5) Surface treatment:
The surface of the casting may have some defects, such as contamination layer, pores, etc., which need to be treated by mechanical processing, chemical cleaning and other methods to improve the surface quality and performance of the casting.
(6) Quality control:
The quality control of titanium alloy castings is very important, and non-destructive testing (such as X-ray testing, ultrasonic testing) and other means are needed to ensure the quality of the inside and surface of the castings.
Summary:
Through the control of the above key technologies, titanium alloy investment casting can produce precision castings that meet the requirements of high-end fields such as aerospace, and it also helps to reduce costs, improve production efficiency and material utilization.
3.Advantages and disadvantages of titanium alloy investment casting
Advantages:
(1) High precision:
Investment casting can produce castings with precise dimensions and low surface roughness, which is suitable for manufacturing parts with complex shapes.
(2) High material utilization:
The raw material utilization rate of titanium alloy investment casting process is high, which can reach 70% to 90%, reducing material waste.
(3) Design flexibility:
Using an integral model to cover the shell to prepare the casting increases the freedom of casting design and can produce titanium castings with highly complex structures.
(4) Low thermal conductivity:
The oxide ceramic shell has low thermal conductivity, good yield, and a smooth inner surface of the cavity, which can solve the quality bottlenecks of flow marks, cold shuts and cracks in graphite titanium castings, making the filling performance and surface roughness reach or approach the level of investment casting.
(5) High dimensional accuracy:
Titanium alloy investment casting does not require a core, which can avoid the problem of uneven wall thickness caused by inaccurate position of the machined graphite core or misalignment of the mold.
(6) Cost-effectiveness:
For medium and large batch production, investment casting has better economy, especially when the casting weight is between 200g and 50kg.
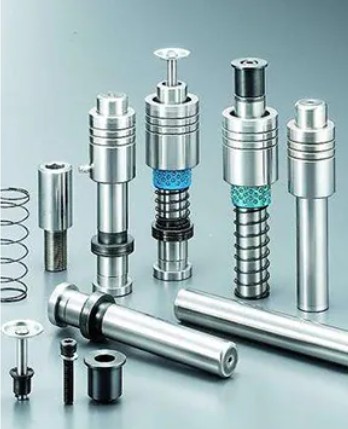
Disadvantages:
(1) High cost:
The process is complex, the production cycle is long, and the cost of wax molds, coatings, refractory sands, etc. is high, which is not suitable for small batch production.
(2) Size limitation:
The size of the casting cannot be too large, and the maximum weight can be 1000 kg. It is difficult to cast a casting that exceeds the weight.
(3) Difficulty of quality control:
There are too many factors that affect the quality of titanium alloy investment casting, and the process quality control is difficult.
(4) Technical difficulty:
Titanium alloy has high chemical activity and reacts chemically with almost all refractory materials in the molten state, which requires strict selection of shell materials and process control.
4.Application fields of titanium alloy investment casting
As an advanced metal forming process, titanium alloy investment casting technology has been widely used in many fields due to its advantages such as high dimensional accuracy and good surface roughness of castings. The following are several major application fields:
(1) Aerospace field:
Due to the characteristics of high specific strength and good corrosion resistance, titanium alloy has become an ideal material for the aerospace industry. Titanium alloy investment casting technology can produce high-precision titanium alloy parts, such as aircraft engine blades, fuselage structural parts, etc. These parts are crucial to reducing aircraft weight and improving fuel efficiency.
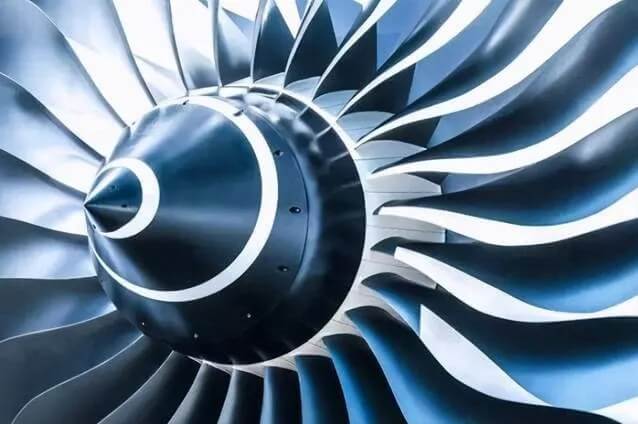
(2) Medical field:
Titanium alloys are used in the medical field to manufacture various implants, such as artificial joints, orthopedic fixation plates, etc., due to their good biocompatibility and corrosion resistance. Investment casting technology can accurately replicate the structure of complex medical devices, meet ergonomic requirements, and improve treatment effects.
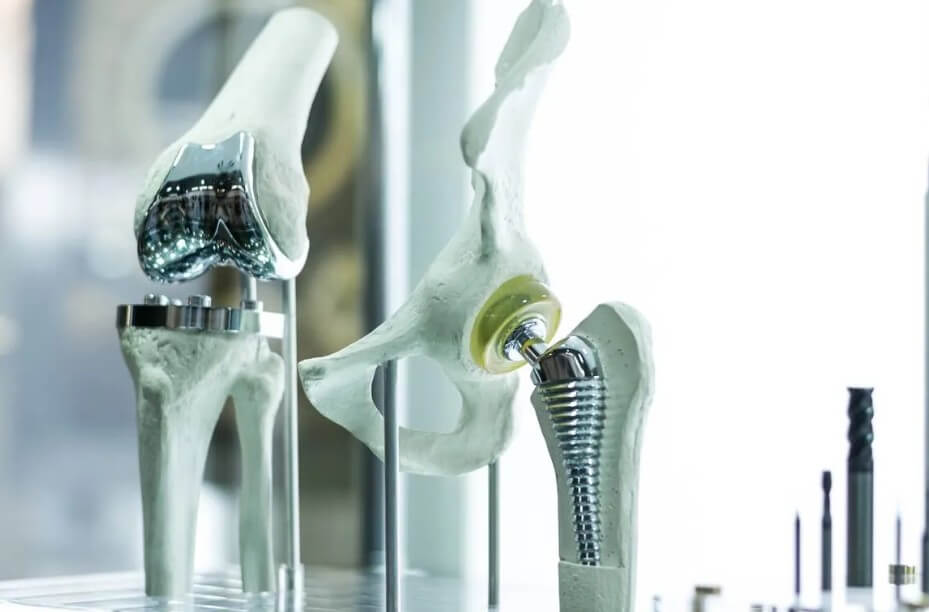
(3) Automobile industry:
In the automobile industry, titanium alloy investment casting technology is used to manufacture key components of high-performance automobiles, such as engine components and suspension systems. The use of these components helps to reduce the weight of the vehicle and improve the vehicle’s power performance and fuel economy.
(4) Energy field:
The application of titanium alloy investment casting technology in the energy field is mainly concentrated in nuclear power, thermal power generation and petrochemical equipment. For example, titanium alloy castings can be used to manufacture structural parts of nuclear reactors, turbine blades for thermal power generation, etc. Its excellent corrosion resistance and high temperature performance can meet the working requirements in extreme environments.
(5) Sports equipment:
Due to the characteristics of light weight and high strength, titanium alloys are also widely used in the field of sports equipment, such as golf club heads and bicycle frames. Investment casting technology can produce sports equipment with complex shapes and smooth surfaces, improving the performance of athletes.
(6) Marine engineering:
The application of titanium alloys in marine engineering is mainly due to their excellent resistance to seawater corrosion. Titanium alloy parts manufactured by titanium alloy investment casting technology can be used in ship propulsion systems, seawater desalination equipment, etc., to improve the reliability and service life of equipment.
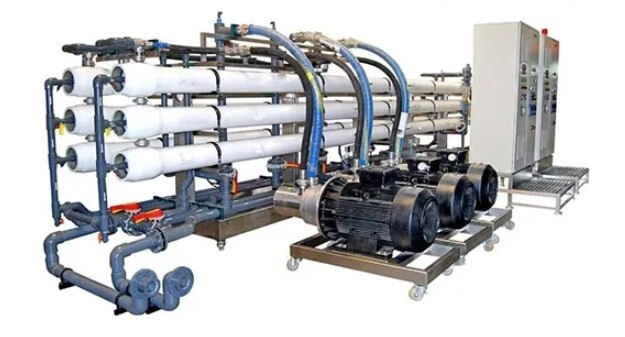
5.Summary
In summary, titanium alloy investment casting technology, as an advanced manufacturing process, has broad application prospects and development potential. Through continuous technological innovation and industrial upgrading, titanium alloy investment casting technology will inject new vitality into the development of modern industry.