A complete analysis of stainless steel turned parts processing: difficulties, tool selection and process optimization
In the field of mechanical processing, stainless steel turned parts have always been regarded as a “tough nut to crack”. Its characteristics such as high tendency to work hardening, high cutting force and easy tool wear have brought great challenges to processing efficiency and processing quality.
This article will take you to a deep understanding of the difficulties in stainless steel turned parts processing, and provide you with a full range of solutions from tool selection to surface quality improvement to process optimization, helping you to easily cope with the challenges of stainless steel turning.
1.Application and processing challenges of stainless steel turned parts
Stainless steel, as a high-strength and corrosion-resistant metal material, is widely used in aerospace, automobile manufacturing, medical equipment, precision machinery and other industries. Especially in the field of high-precision and high-requirement manufacturing, stainless steel turned parts are highly favored due to their good mechanical properties and durability.
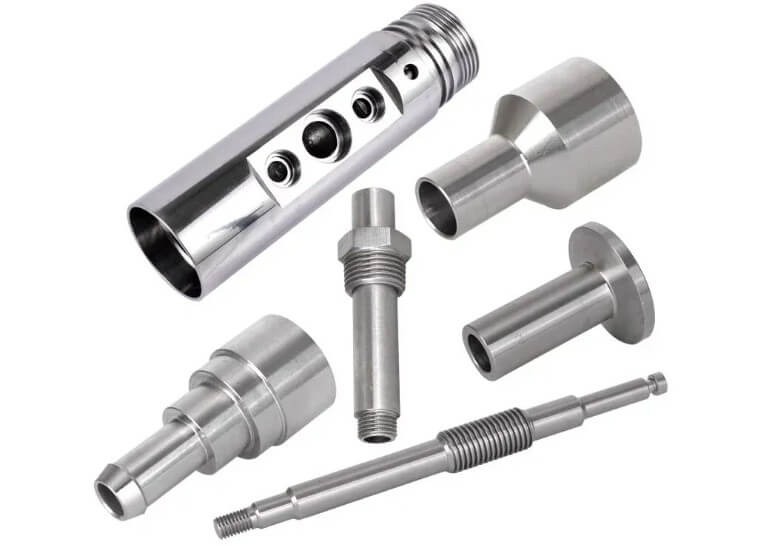
However, the turning of stainless steel is relatively complex, which is mainly reflected in the following aspects:
(1) High hardness and high strength:
Increased cutting force accelerates tool wear.
(2) Severe work hardening:
The surface of the workpiece is easily hardened due to the thermal effect of the cutting process, making subsequent processing more difficult.
(3) Poor heat dissipation:
The temperature rises rapidly during the cutting process, which is not conducive to tool life and surface quality.
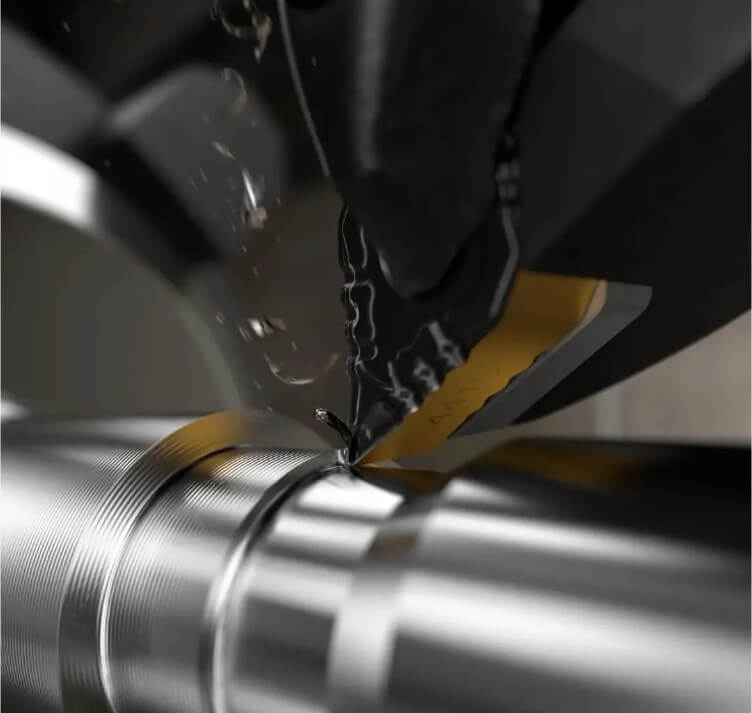
(4) Difficult surface quality control:
Affected by factors such as vibration and built-up edge, the surface finish of the product is difficult to guarantee.
In order to improve the processing efficiency and quality of stainless steel turned parts, the following will discuss in detail tool selection, cutting parameter optimization and processing strategy.
2.Main difficulties in stainless steel turning
(1) Work hardening phenomenon
Stainless steel is prone to work hardening during the cutting process, that is, a hardened layer is formed at the cutting part, making it more difficult for the tool to cut in, resulting in increased cutting force and further accelerated tool wear. This hardening phenomenon is particularly significant in austenitic stainless steel (such as 304, 316). To reduce the impact of work hardening, you can choose a sharp tool, a larger rake angle, and an appropriate cutting speed.
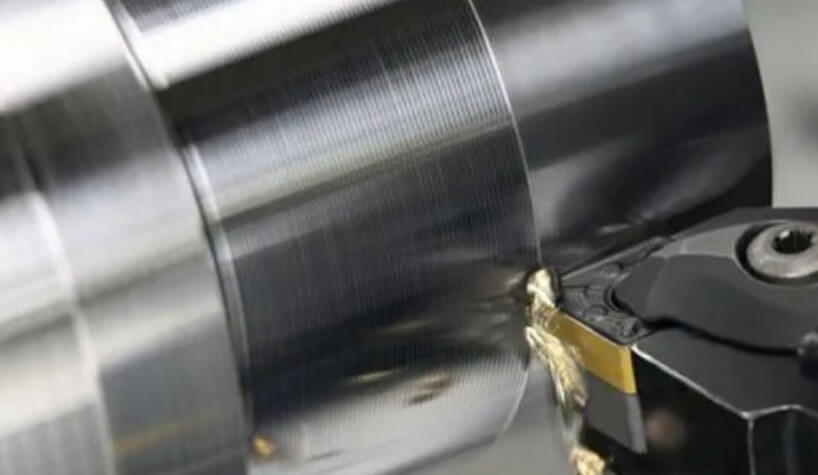
(2) Rapid tool wear
The high toughness and hardness of stainless steel cause the tool to bear greater pressure during the cutting process, resulting in accelerated wear of the front and back faces of the tool. Common types of tool wear include:
1) Crater wear on the front face:
Due to high-temperature cutting, chemical diffusion and bonding occur on the tool surface.
2) Flank wear:
Affects machining accuracy and surface quality.
3) Tool chipping:
Caused by high cutting force and work hardening.
In addition, tool wear not only affects machining quality, but also increases production costs. Therefore, it is necessary to use tool materials with better wear resistance and reasonably optimize cutting parameters.
(3) High cutting heat and difficult heat dissipation
Due to the poor thermal conductivity of stainless steel, the large amount of heat generated during cutting is difficult to dissipate quickly, resulting in increased tool temperature, accelerated tool wear, and affecting the dimensional accuracy of stainless steel turned parts.
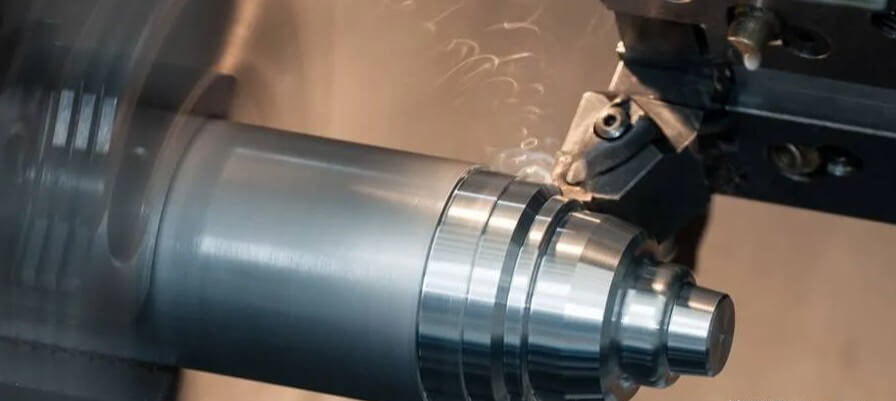
This makes the use of coolant very important. Proper cooling and lubrication measures can effectively extend tool life and improve machining quality.
(4) Difficulty in controlling surface roughness
During the stainless steel turning process, due to work hardening, cutting heat and the formation of built-up edge, scratches, tool marks or burrs are prone to appear on the workpiece surface, affecting the quality of the final product.
In order to improve the surface quality, high-finish tools can be used, cutting parameters can be optimized, and cutting fluids with high lubrication efficiency can be used.
3.Selecting suitable tool materials and coating technology
(1) Selection of tool materials
Common tool materials used in the manufacture of stainless steel turned parts include:
1) Carbide tools (coated tools):
Such as TiAlN and TiCN coated tools, which have strong wear resistance and high temperature resistance.
2) Ceramic tools:
Suitable for high-speed cutting, excellent wear resistance, but relatively brittle.
3) Cubic boron nitride (CBN) tools:
Used for finishing of high-hardness stainless steel, the cost is relatively high.
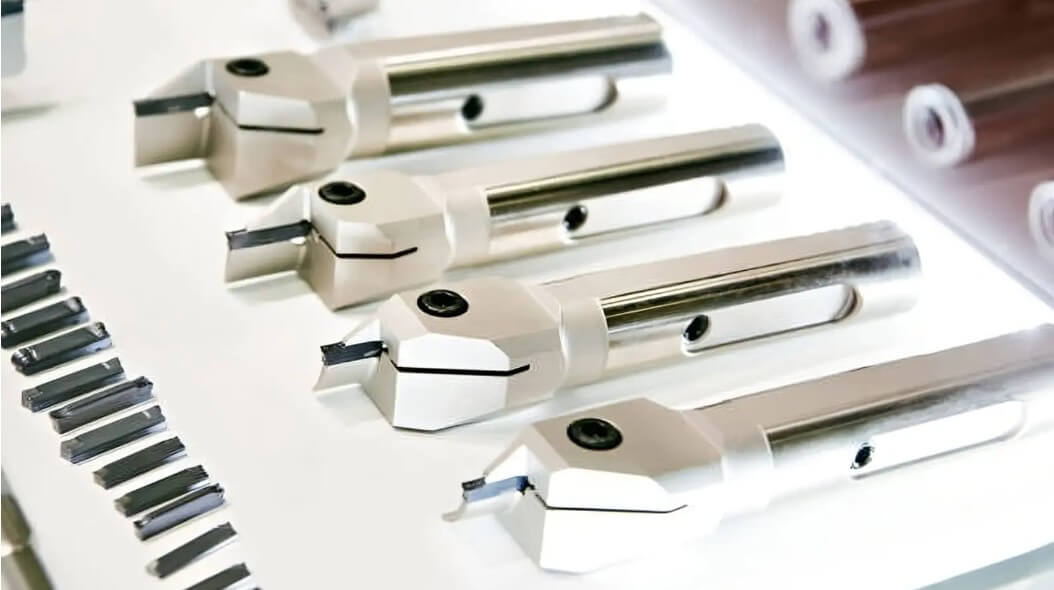
(2) Optimization of tool geometric parameters
1) Rake angle :
Properly increasing the rake angle can reduce cutting force and reduce the impact of work hardening.
2) Back angle :
A reasonable back angle helps reduce tool back face wear.
3) Edge passivation:
It can improve tool strength and reduce the risk of chipping.
(3) Tool coating technology
Coated tools can effectively reduce tool wear and improve processing efficiency:
1) TiAlN coating:
It has strong high temperature resistance and is suitable for high-speed cutting of stainless steel.
2) TiCN coating:
It is suitable for medium and low speed processing and has good wear resistance.
3) DLC coating (diamond-like carbon coating):
It reduces the friction coefficient and reduces the formation of built-up edge.
4.Key cutting parameters affecting the quality of stainless steel turned parts
(1) Cutting speed (Vc)
The cutting speed has a significant impact on the turning quality of stainless steel. Too low speed can easily lead to the formation of built-up edge, thereby affecting the surface quality of the workpiece, while too high speed will aggravate tool wear and shorten tool life. Generally speaking, the recommended cutting speed range is as follows:
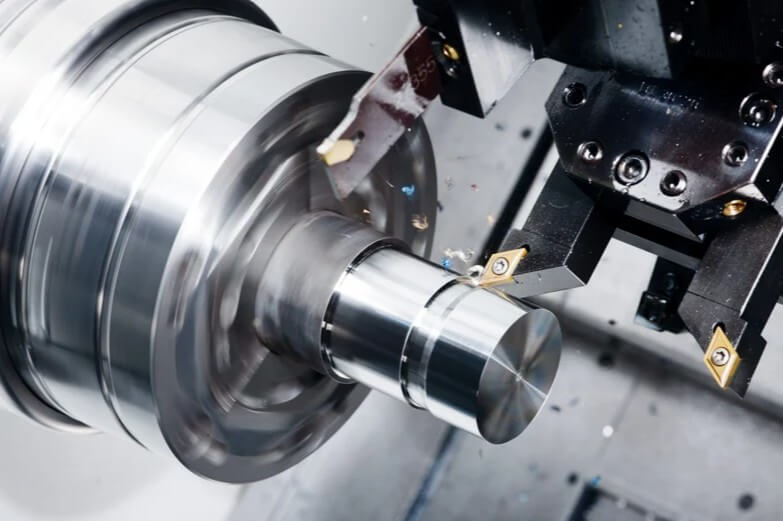
1) Carbide tool: 80-200 m/min
2) Ceramic tool: 200-400 m/min
3) CBN tool: 300-500 m/min
When optimizing the cutting speed, it is necessary to adjust it according to the specific material and tool type to obtain the best cutting effect.
(2) Feed rate (f)
The feed rate affects the chip thickness and the surface quality of the machined surface. Too large a feed rate will increase the cutting force, cause tool wear to increase, and even affect the dimensional accuracy of the workpiece, while too small a feed rate may affect the machining efficiency. The recommended feed rate range is as follows:
1) Rough machining: 0.1-0.3 mm/rev
2) Finishing: 0.05-0.15 mm/rev
Reasonable feed rate setting can ensure tool life, while ensuring cutting stability and improving surface finish.
(3) Back cutting depth (ap)
The choice of back cutting depth directly affects the material removal rate and surface quality. In the roughing stage, a larger back-cutting amount helps to improve the processing efficiency, while in the finishing stage, the back-cutting amount needs to be reduced to obtain better surface quality. The recommended back-cutting amount is as follows:
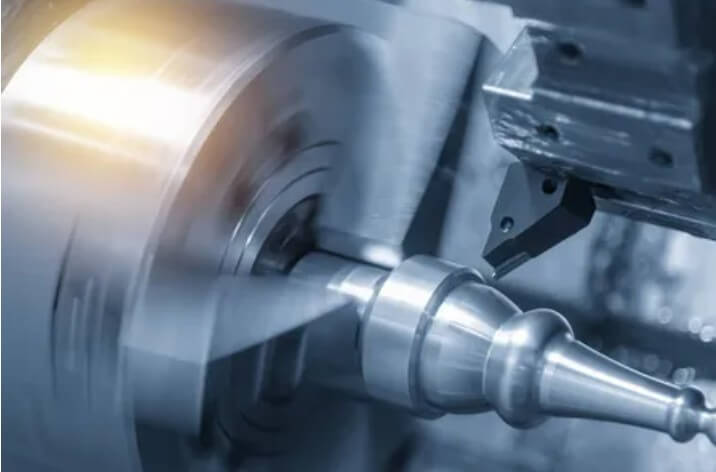
1) Roughing: 1-3 mm
2) Finishing: 0.2-0.5 mm
The appropriate back-cutting amount setting can effectively reduce the cutting force, improve the tool durability, reduce the hardening phenomenon, and improve the workpiece quality.
5.How to improve the surface quality of stainless steel turned parts
(1) Tool angle optimization
The optimization of tool geometry is crucial to improving surface quality. Reasonable rake angle and back angle settings can reduce cutting resistance, reduce tool wear, and improve surface finish.
1) Rake angle (γ):
A larger rake angle can reduce cutting force, reduce hardening, and improve workpiece surface quality.
2) Back angle (α):
The appropriate back angle can reduce tool back face wear and ensure stable processing.
3) Edge passivation:
Slightly passivating the blade can reduce chipping, improve tool life, and ensure surface quality.
(2) Use efficient cutting fluid
The use of cutting fluid is crucial for controlling temperature, reducing cutting force and improving surface quality. Different types of cutting fluids are suitable for different processing needs:
1) Water-soluble cutting fluid:
Mainly used for high-speed cutting, with good cooling effect, which can effectively reduce cutting temperature.
2) Oil-based cutting fluid:
Suitable for low-speed processing, with good lubrication effect, which helps to reduce friction between the tool and the workpiece.
3) Synthetic cutting fluid:
It has both cooling and lubrication effects and is suitable for most stainless steel processing scenarios.
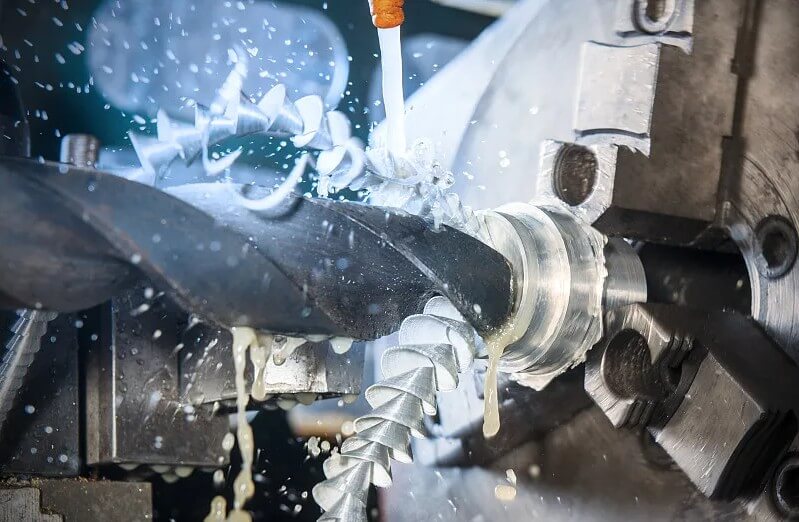
(3) Reduce cutting force
The size of the cutting force directly affects the surface finish and processing accuracy of stainless steel turned parts. Methods to reduce cutting force include:
1) Use sharp tools to reduce cutting resistance and improve surface quality.
2) Optimize feed rate and cutting speed to avoid work hardening.
3) Use vibration-damping tool holders to reduce vibration and improve processing stability.
6.Processing technology optimization of stainless steel turned parts
(1) Roughing and finishing are carried out in steps
In order to improve processing efficiency and quality, roughing and finishing are usually carried out in steps.
1) Roughing:
Use a larger back cutting amount and feed rate to improve material removal rate, and the processing allowance is usually larger.
2) Finishing:
Reduce cutting speed and feed rate, improve surface quality, and ensure the dimensional accuracy of the workpiece.
(2) Reduce tool replacement frequency
Reducing the tool replacement frequency can not only reduce production costs, but also improve processing stability. Methods for optimizing tool life include:
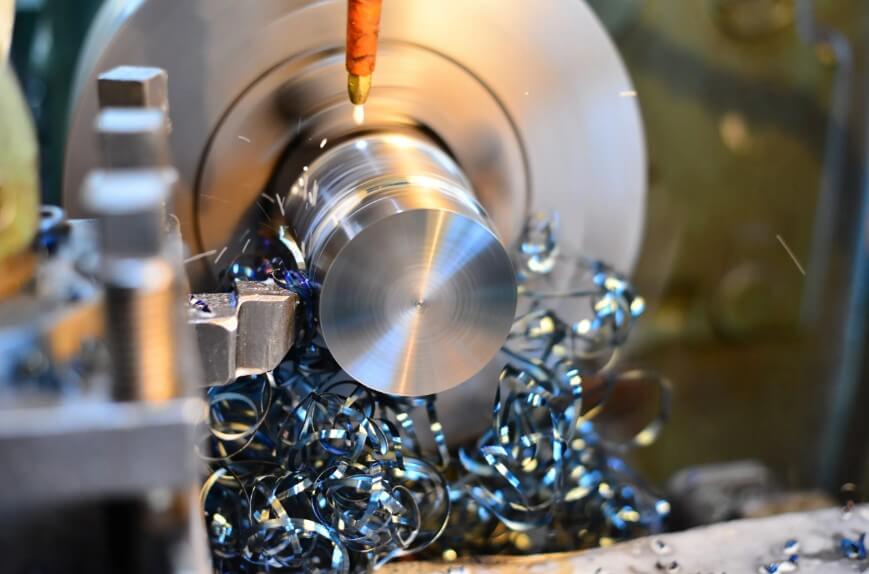
1) Select high-performance tools, such as coated carbide or ceramic tools, to improve wear resistance.
2) Regularly check and sharpen tools to avoid affecting processing quality due to excessive tool wear.
3) Optimize the use of cutting fluid, reduce cutting heat, and extend tool life.
(3) Reduce processing costs
1) Reducing costs is the key to improving competitiveness without affecting processing quality.
2) Optimize cutting parameters, improve material removal rate, and reduce processing time.
3) Use automated processing to reduce manual intervention and improve production efficiency.
4) Rationally select tools and cutting fluids to reduce consumable costs.
7.Conclusion: Summary of optimization strategies for stainless steel turned parts
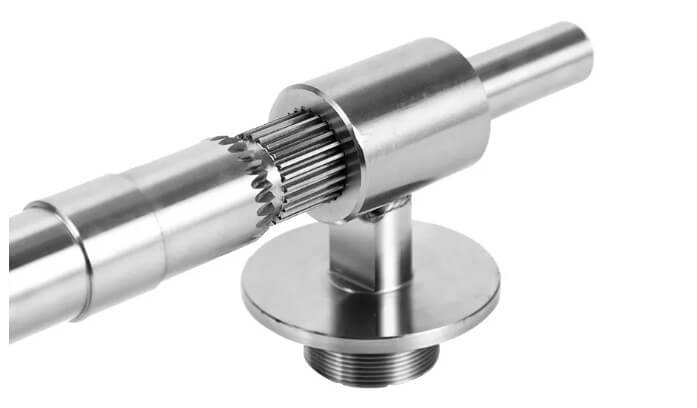
● Rationally select tools to improve wear resistance and life.
● Optimize cutting parameters to improve processing efficiency and quality.
● Use efficient cooling and lubrication technology to reduce cutting heat.
● Rationally plan roughing and finishing to improve product qualification rate.
By optimizing processing strategies and improving the level of automation, we can effectively deal with the difficulties in stainless steel processing while improving production efficiency and product quality.