Stainless steel investment casting: advantages, challenges and analysis of influencing factors
As a metal precision casting method, stainless steel investment casting technology has significant advantages in the production of stainless steel complex components. This article aims to explore the advantages, challenges, factors affecting the dimensional accuracy of stainless steel investment casting parts, and corresponding measures to improve the dimensional accuracy of parts.
And at the end of the article, several typical stainless steel investment casting parts will be listed to further illustrate the significant advantages and wide application of investment casting technology in the production of stainless steel complex components.
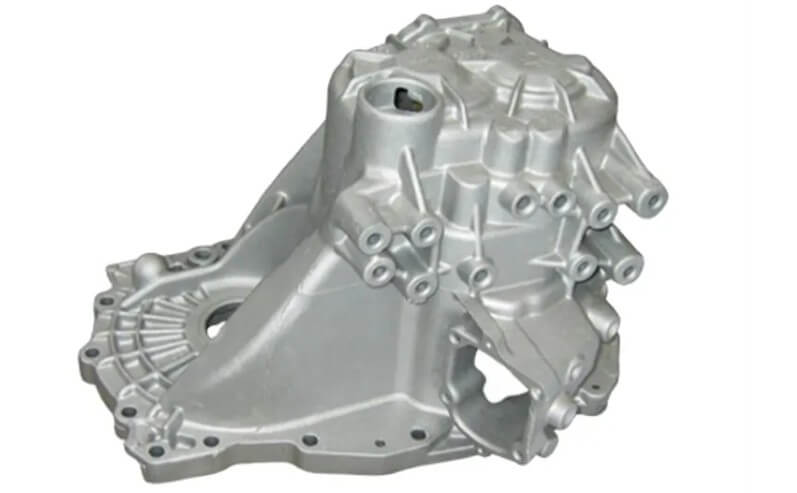
1.Introduction to investment casting process
The basic process flow of investment casting includes: making wax molds, wax mold combination, coating refractory materials, hardening and drying, melting lost wax molds, roasting shells, pouring molten metal, cooling and shelling, post-processing and other steps. Among them, the production of wax molds and the pouring of molten metal are important links in the whole process, and their dimensional accuracy directly affects the dimensional accuracy of the final casting.
2.Advantages of stainless steel investment casting
(1) Excellent corrosion resistance:
Stainless steel contains elements such as chromium and nickel, which make it have excellent corrosion resistance and can be used for a long time in harsh environments. This is especially important for parts that need to work in corrosive media.
(2) Good mechanical properties:
Stainless steel has high strength and hardness, as well as good plasticity and toughness. At the same time, there are many types of stainless steel, and different alloy compositions can meet specific performance requirements.
(3) High precision and surface finish:
The investment casting process can achieve the production of castings with complex shapes and high precision, and the fluidity and filling capacity of stainless steel are good. Therefore, the plasticity of stainless steel makes this advantage more obvious, which helps to obtain castings with smooth surfaces and precise dimensions.
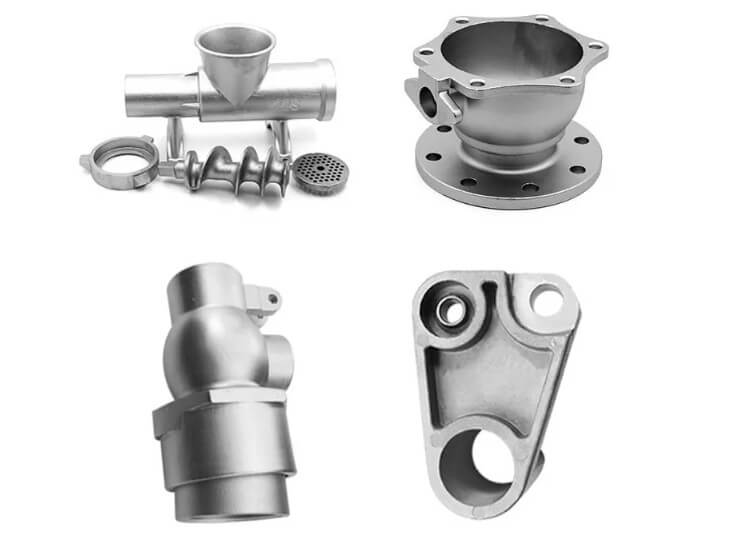
(4) Wide range of applications:
Due to the excellent properties of stainless steel, stainless steel investment castings produced by investment casting are widely used in aerospace, chemical industry, medical equipment and other fields.
3.Challenges of stainless steel investment casting
(1) Complex casting process:
Stainless steel has a high melting point and poor fluidity, which can easily lead to casting defects such as shrinkage cavities and shrinkage. Therefore, it is necessary to strictly control the casting process parameters to ensure the quality of the casting.
(2) High cost:
The relatively high cost of stainless steel, coupled with the complexity of the investment casting process itself, leads to a high production cost of stainless steel investment casting parts.
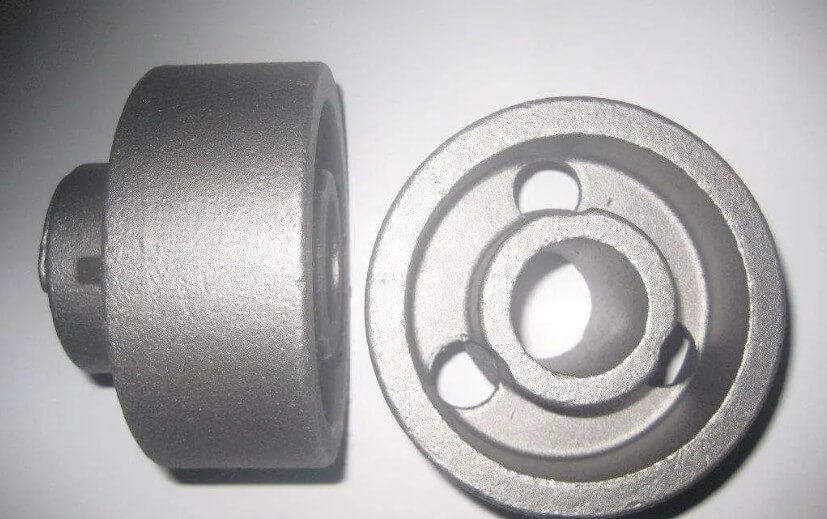
(3) Difficult heat treatment:
The heat treatment process of stainless steel is relatively complex, and it is necessary to accurately control parameters such as heating temperature, holding time and cooling rate to obtain ideal structure and performance.
(4) Oxidation problem:
At high temperatures, stainless steel is prone to oxidation reaction and generates oxide scale, which affects the surface quality and performance of the casting. Therefore, effective protective measures need to be taken, such as inert gas protection.
4.Factors affecting the dimensional accuracy of stainless steel investment casting parts
(1) Wax pattern material and production process
1) Wax pattern material properties:
The shrinkage rate, thermal stability, strength and other properties of the wax pattern material have a significant impact on the dimensional accuracy of the wax pattern.
The commonly used wax pattern materials for stainless steel investment casting include paraffin-based wax and synthetic wax. The performance of different wax materials varies greatly, so it is crucial to choose the right wax.
2) Wax pattern manufacturing process:
The wax pattern manufacturing methods include compression molding and injection molding. The compression molding method has higher dimensional accuracy, but lower production efficiency;
The injection molding method has higher production efficiency, but the dimensional accuracy is greatly affected by factors such as injection pressure, temperature, and time.
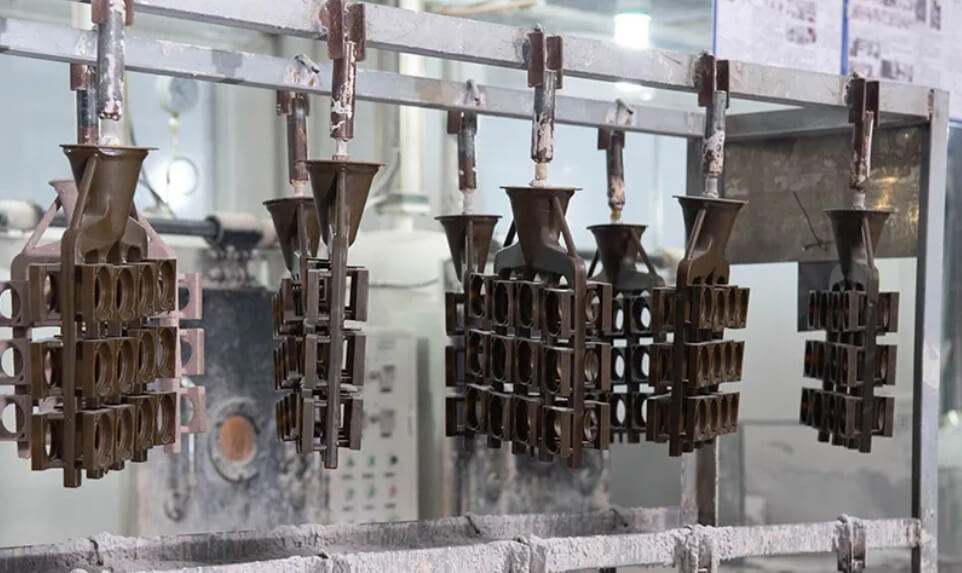
(2) Shell material and manufacturing process
1) Shell material properties:
The properties of the shell material, such as particle size, strength, and thermal expansion coefficient, have an important influence on the dimensional accuracy of the shell.
The commonly used shell materials for stainless steel investment casting include quartz sand, zircon sand, corundum sand, etc. The performance of different materials varies greatly. It is critical to choose the right shell material and make a reasonable ratio.
2) Shell manufacturing process:
The shell manufacturing process includes coating, sanding, hardening, and drying. The thickness of the coating layer, the uniformity of sanding, and the conditions of hardening and drying will affect the dimensional accuracy of the shell.
(3) Lost wax mold melting and shell firing
1) Lost wax mold melting:
Improper control of the temperature and time of the lost wax mold melting will cause the wax mold to deform or remain, affecting the dimensional accuracy of the shell.
2) Shell firing:
Improper control of the temperature and time of the shell firing will cause the shell to deform or lack strength, affecting the dimensional accuracy of the entire stainless steel investment casting part.
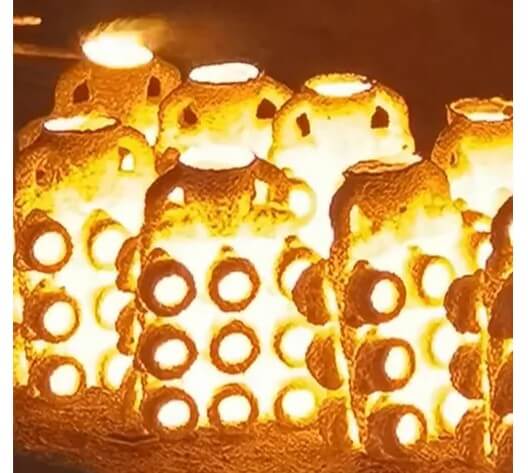
(4) Pouring and cooling
1) Pouring temperature and speed:
Pouring temperature that is too high or too low, pouring speed that is too fast or too slow will affect the dimensional accuracy of the casting.
Pouring temperature that is too high will increase the shrinkage rate of the casting, and pouring temperature that is too low will cause insufficient filling of the casting;
Pouring speed that is too fast will cause internal defects of the casting, and pouring speed that is too slow will cause the surface of the casting to be rough.
2) Cooling speed:
Cooling speed that is too fast will increase the internal stress of the casting and even cause cracks; cooling speed that is too slow will cause coarse grains in the casting, affecting the mechanical properties.
(5) Post-processing
1) Cutting and cleaning:
Improper operation during cutting and cleaning can cause deformation or damage of stainless steel investment casting parts, affecting dimensional accuracy.
2) Heat treatment:
Improper heat treatment process can cause deformation or structural changes of castings, affecting dimensional accuracy.
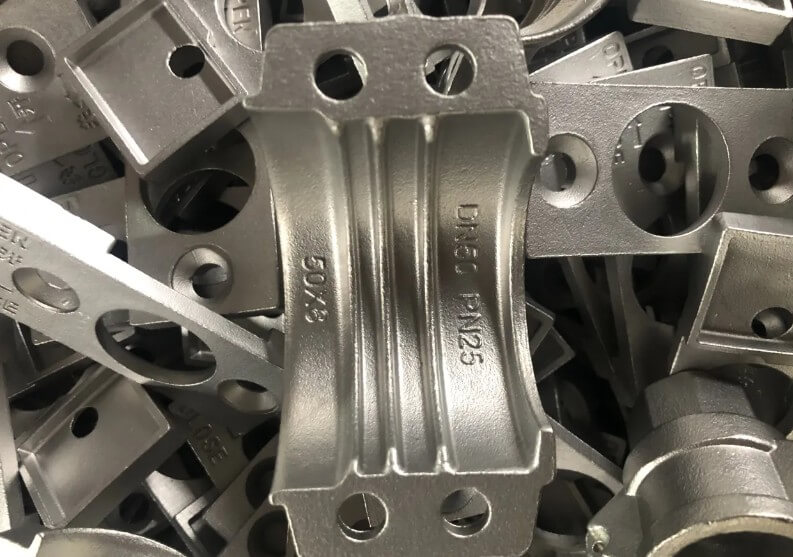
5.Measures to improve the dimensional accuracy of stainless steel investment casting parts
(1) Optimize wax pattern materials and production processes
1) Select high-performance wax pattern materials:
Select wax pattern materials with low shrinkage, good thermal stability and high strength, such as modified paraffin-based wax materials, polymer synthetic wax materials, etc.
2) Optimize wax pattern production process:
Reasonably control parameters such as injection pressure, temperature, and time to improve the dimensional accuracy of wax patterns. Use advanced wax pattern detection equipment to promptly detect and correct dimensional deviations of wax patterns.
(2) Optimize shell materials and production processes
1) Select high-performance shell materials:
Select shell materials with uniform particle size, high strength and small thermal expansion coefficient, such as zircon sand, corundum sand, etc., and mix them in a reasonable ratio.
2) Optimize the shell manufacturing process:
Strictly control the thickness of the coating layer, the uniformity of sanding, the conditions of hardening and drying, etc., to improve the dimensional accuracy of the shell. Use advanced shell detection equipment to timely detect and correct the dimensional deviation of the shell.
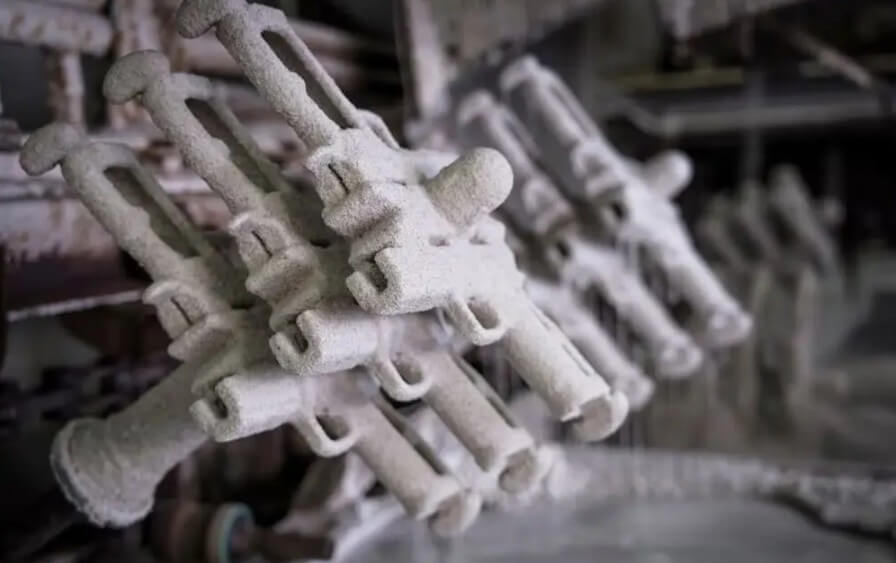
(3) Accurately control the temperature and time of the lost wax mold and the fired shell
1) Accurately control the temperature and time of the lost wax mold:
According to the properties of the wax mold material, reasonably control the temperature and time of the lost wax mold to ensure that the wax mold is completely lost without deformation or residue.
2) Accurately control the temperature and time of the fired shell:
According to the properties of the shell material, reasonably control the temperature and time of the fired shell to ensure that the shell has sufficient strength and dimensional accuracy.
(4) Optimize the pouring and cooling process
1) Optimize the pouring temperature and speed:
According to the properties of the stainless steel material, reasonably control the pouring temperature and speed to ensure that the stainless steel investment casting parts are well filled and have no internal defects.
2) Control cooling rate:
According to the shape and size of stainless steel investment casting parts, reasonably control the cooling rate to avoid excessive internal stress or coarse grains in the casting.
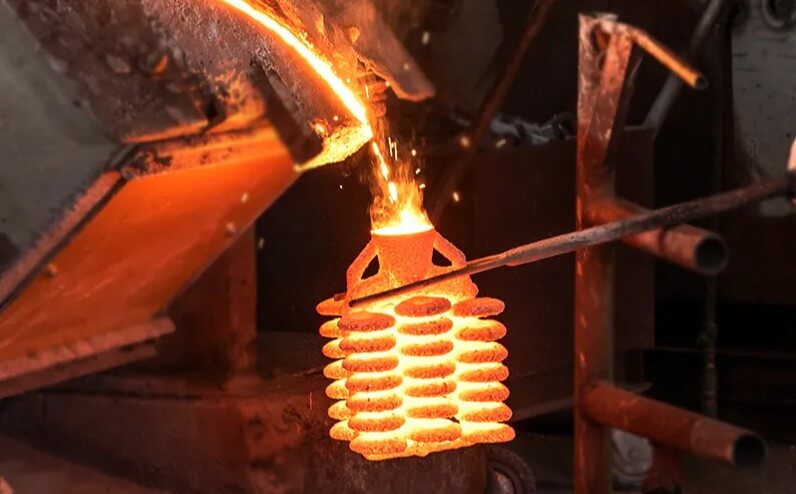
(5) Strengthen post-processing quality control
1) Standardize cutting and cleaning operations:
Use advanced cutting and cleaning equipment and standardize operations to avoid deformation or damage of castings.
2) Optimize heat treatment process:
According to the properties of stainless steel materials, optimize the heat treatment process to avoid deformation or structural changes of castings.
6.List of typical stainless steel investment casting parts
(1) Impeller:
It is widely used in aircraft engines and industrial gas turbines. Its complex aerodynamic shape and efficient fluid channel design require extremely high casting accuracy. Stainless steel materials can provide good high temperature resistance and corrosion resistance.
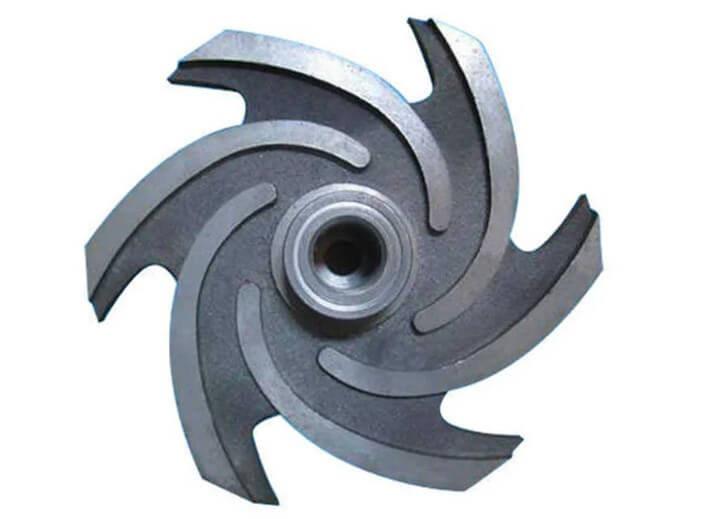
(2) Valve parts:
Including valve body, valve cover, etc. Stainless steel valves are widely used in chemical, petroleum, pharmaceutical and other industries due to their excellent corrosion resistance. Investment casting can ensure the dimensional accuracy and surface finish of valve parts.
(3) Medical device components:
Such as surgical instrument handles, orthopedic implants, etc., stainless steel has good biocompatibility and corrosion resistance. Through investment casting, medical device parts with complex shapes and high precision can be produced to meet the strict requirements of the medical industry.
(4) Pipe fittings:
Including elbows, tees, crosses, etc., stainless steel pipe fittings are widely used in food, beverage, water treatment and other fields. Investment casting can achieve complex structures and seamless connections of pipe fittings, ensuring the sealing and corrosion resistance of pipelines.
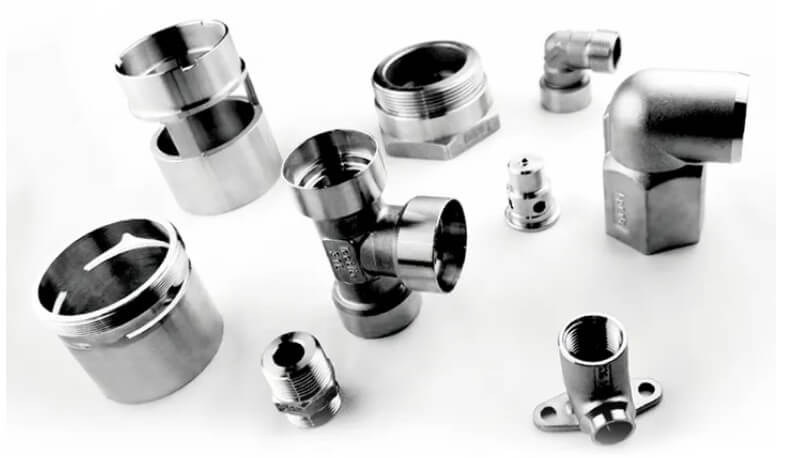
(5) Automotive parts:
For example, exhaust system components, stainless steel has excellent performance in high temperature environments. Investment casting can produce parts such as exhaust manifolds with complex shapes, improving the efficiency and emission performance of automobile engines.
7.Conclusion
In summary, the development of stainless steel investment casting technology has provided strong technical support for the widespread application of stainless steel materials. It will continue to help stainless steel products show their unique value in more fields.