Casting Applications
Gravity casting is a typical permanent mold casting process where molten metal is poured into a preheated mold cavity and fills the cavity with the help of gravity. This process is suitable for large quantities or small quantities of high-quality castings. The most popular technique in this process is tilt pour casting. The metal is poured into the pouring basin while the mold is in a horizontal position. The casting machine is then raised to a vertical position for a preset cycle time, during which the metal is allowed to enter the mold cavity at a slow, continuous and steady pouring rate.
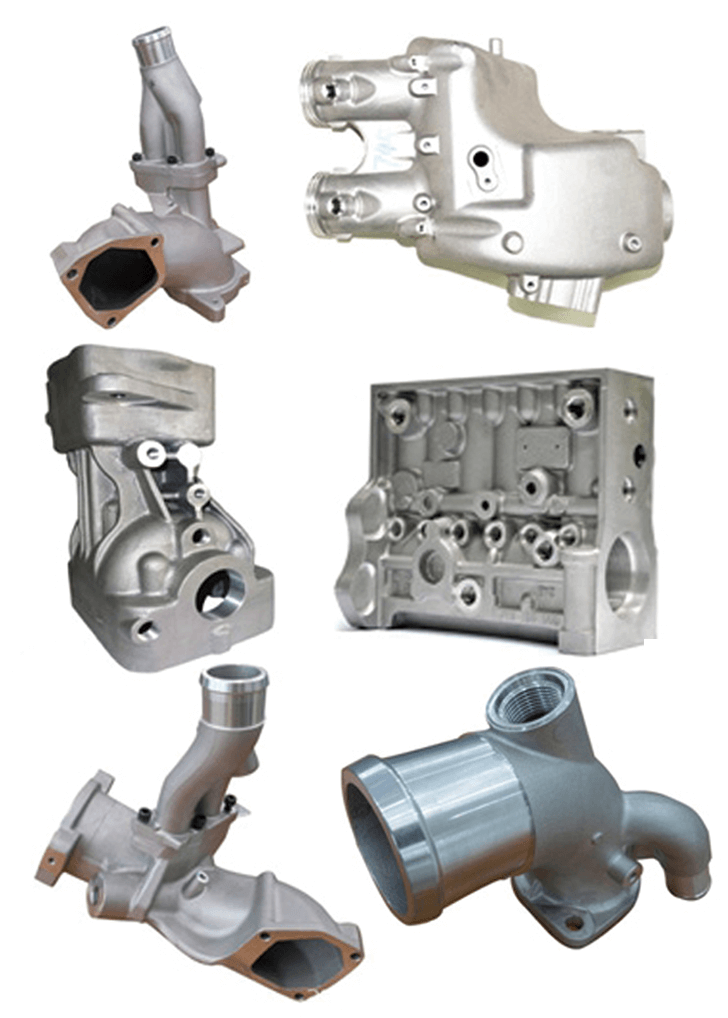
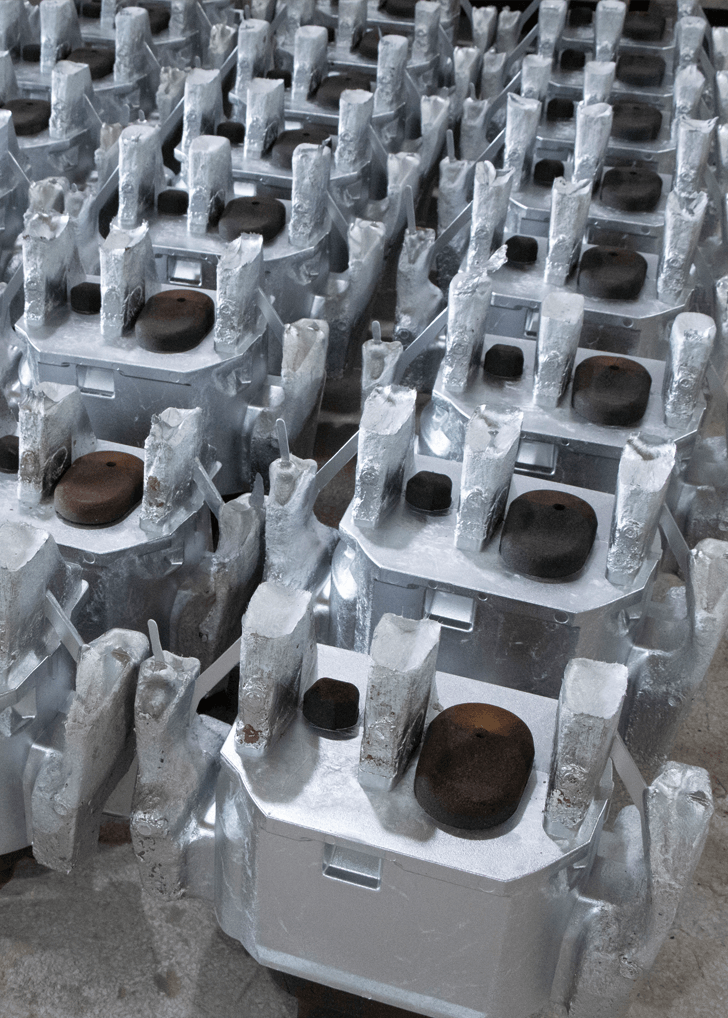
DEDICATED TO INNOVATION
In 2015, we established a gravity die casting production line. At present, we have 6 tilting gravity die casting machines and 8 cylinder head gravity casting machines, which can produce 10 tons of castings per day. The weight ranges from less than 1 kg to 150 kg/piece. Our products cover automotive parts, medical device parts, electrical housings, optoelectronic parts, etc. We design and manufacture molds by ourselves. We have the ability to design, process and assemble molds.
Advantages of gravity die casting process
Compared with sand casting, gravity casting has higher casting dimensional accuracy, better surface finish, higher production efficiency, and higher casting strength when pouring the same metal. It also performs well in air tightness tests. For example, after T6 heat treatment, the air tightness of aluminum alloy castings can reach 50kg/cm2.
Compared with high-pressure die casting, gravity die casting can produce parts with heavier weight, larger volume, and more complex structure. The mold cost of gravity die casting is lower, but the quality of the parts produced is close to that of high-pressure die casting.
Our Material Scope
ASMT Standard: A319, A356, A357, A413
GB Standard: ZL101, ZL101A, ZL102, ZL107
BS Standard: LM6, LM20, LM25
EN Standard: EN AC-42100, EN AC-42200, EN AC-43000, EN AC-43200, EN AC-43300, EN AC-43400, EN AC-44200, EN AC-44300, EN AC-46000, EN AC -46200
Mold design analysis
For some castings with complex geometries, we also have the capability of numerical computer simulation to help us achieve the most optimized design. Better design before mass production helps reduce the cost of trial and error through experimentation and put the design into production faster.