Прототипы алюминиевых отливок:ключевой инструмент от проверки конструкции до мелкосерийного производства
Прототипы алюминиевых отливок — это алюминиевые образцы или модели, изготовленные методом литья, которые в основном используются для проверки дизайна, функционального тестирования и мелкосерийного производства.
В последние годы применение новых технологий, таких как 3D-печать, интеллектуальное производство и моделирование, сделало процесс изготовления алюминиевых отливок более эффективным и точным. В этой статье мы рассмотрим ключевые технологии, выбор материалов, контроль качества, их преимущества и ограничения при изготовлении прототипы алюминиевых отливок, чтобы помочь тем, кто участвует в процессе, лучше понять причины создания прототипов.
1. сценарии применения для прототипы алюминиевых отливок
Прототипы алюминиевых отливок широко используется в аэрокосмической, автомобильной, электронной, машиностроительной и других областях. Оно играет важную роль на всех этапах разработки продукции в этих областях, и основные сценарии его применения включают:
(1) Проверка конструкции
На ранних стадиях проектирования изделий прототипы алюминиевых отливок используются для проверки осуществимости и функциональности конструкции. Благодаря реальному производству и испытаниям конструкторы могут выявить и устранить проблемы в конструкции, чтобы избежать дорогостоящих ошибок при массовом производстве.
(2) Функциональное тестирование
Прототипы алюминиевых отливок также используются для проверки работоспособности изделий в реальных условиях. Например, в автомобилестроении критически важные компоненты, такие как блоки двигателей и корпуса коробок передач, часто нуждаются в функциональных испытаниях спрототипы алюминиевых отливок для обеспечения их надежности и долговечности.
(3) Мелкосерийное производство
При изготовлении продукции по индивидуальному заказу или тестировании на рынке прототипы алюминиевых отливок представляют собой экономически эффективное решение для мелкосерийного производства. Выпуская небольшие партии, компании могут собрать отзывы пользователей и оптимизировать свою продукцию, прежде чем приступать к крупносерийному производству.
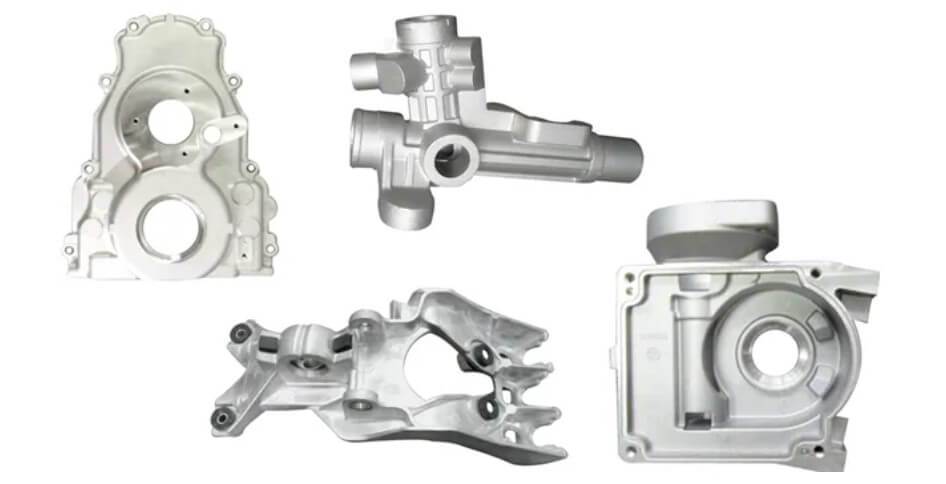
2. Какой процесс наиболее подходит для литья прототипы алюминиевых отливок?
Выбор наиболее подходящего процесса для литья прототипы алюминиевых отливок зависит от конкретных потребностей, включая такие факторы, как объемы производства, сложность деталей, требования к точности, бюджетные расходы и циклы разработки. Ниже приведены преимущества и недостатки нескольких распространенных процессов литья и сценарии их применения, которые помогут вам выбрать наиболее подходящий метод:
(1) Литье в песок
1) Плюсы:
Низкая стоимость: форма проста в изготовлении, а стоимость материала низкая.
Высокая гибкость: подходит для единичного или мелкосерийного производства, легко изменяет дизайн.
Подходит для крупных деталей: позволяет отливать детали больших размеров.
2) Недостатки:
Низкая точность: отливки с большими допусками на размеры и плохой отделкой поверхности.
Низкая эффективность производства: подходит для мелкосерийного производства, не подходит для крупносерийного производства.
3) Применимые сценарии:
Изготовление прототипов из одной детали или небольшой партии.
Большие детали или детали сложной формы.
Сцены, не требующие высокой точности и качества поверхности.
(2) Инвестиционное литье
1) Плюсы:
Высокая точность: способна производить отливки с точными размерами и гладкими поверхностями.
Сложные формы: подходит для литья деталей со сложной геометрией.
Высокая степень использования материалов: практически не образуется отходов.
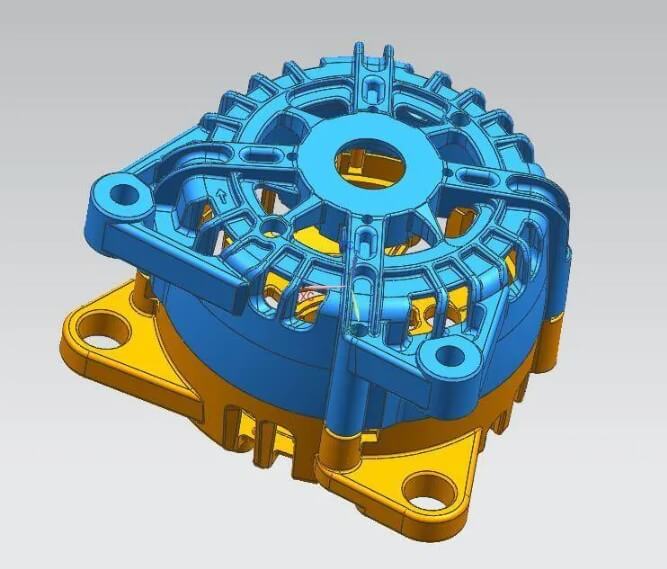
2) Недостатки:
Более высокая стоимость: восковые формы и керамические оболочки стоят дороже.
Длинный производственный цикл: больше технологических операций, относительно длинный производственный цикл.
3) Применимые сценарии:
Высокоточные детали сложной формы.
Аэрокосмическая промышленность, медицинское оборудование и другие области, где требуется высокое качество.
Высокоточное изготовление прототипов малыми партиями.
(3) Металлическая форма для гравитационного литья
1) Плюсы:
Более высокое качество: отливки с высокой плотностью и хорошими механическими свойствами.
Среднесерийное производство: Подходит для средних производственных потребностей.
Лучшее качество поверхности: более высокое качество поверхности по сравнению с песчаным литьем.
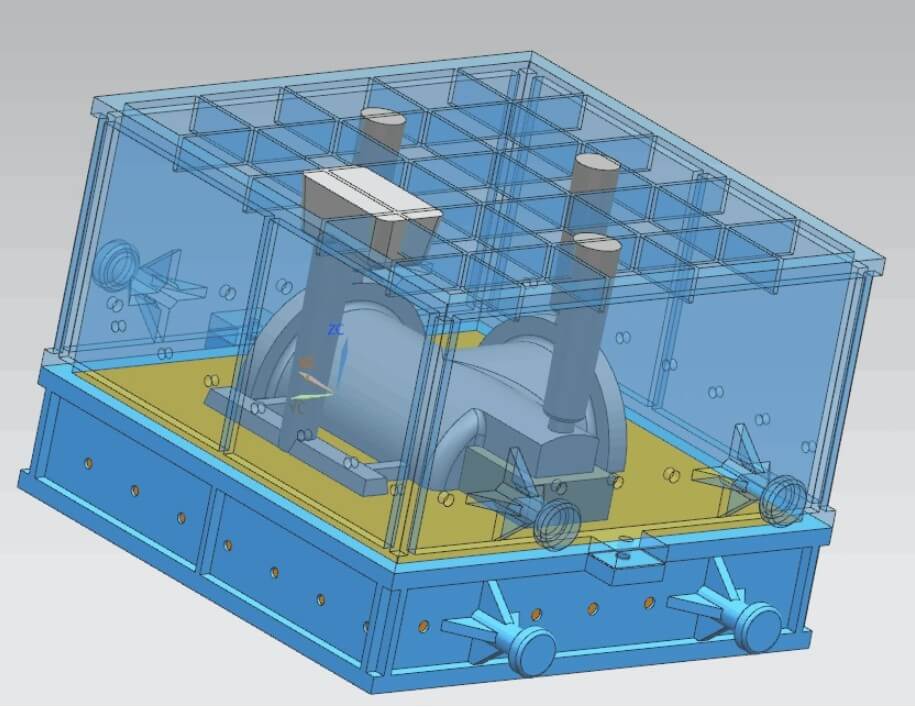
2) Недостатки:
Более высокая стоимость пресс-форм: изготовление металлических пресс-форм обходится дороже.
Менее гибкие: не подходят для изготовления единичных деталей или небольших партий прототипов.
3) Применимые сценарии:
Среднесерийное производство.
Детали с высокими требованиями к механическим свойствам.
Детали, требующие высокого качества поверхности.
(4) Литье под давлением (литье под высоким давлением)
1) Плюсы:
Высокая точность: способна производить отливки с точными размерами и гладкими поверхностями.
Высокая эффективность производства: подходит для массового производства.
Тонкостенные детали: позволяет отливать тонкостенные детали сложной формы.
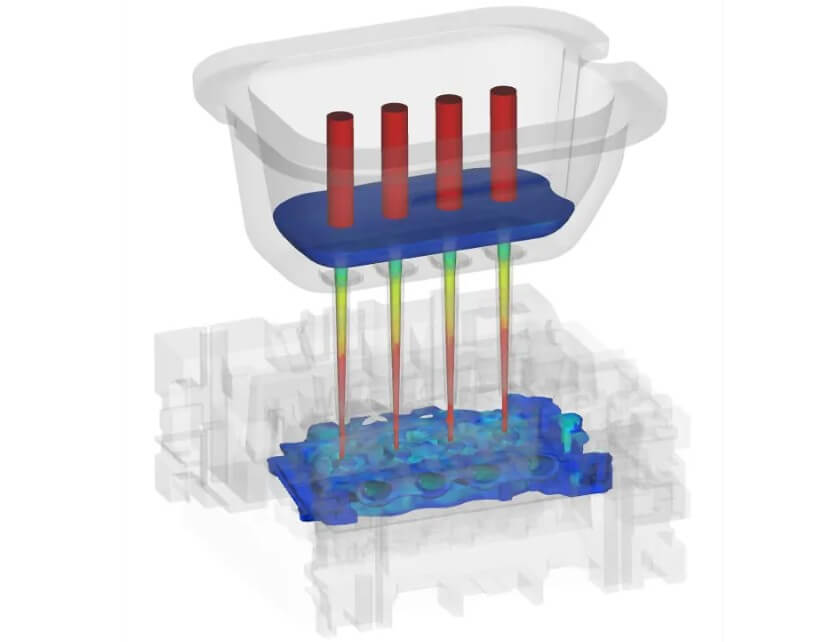
2) Недостатки:
Высокая стоимость форм: стоимость производства форм для литья под давлением очень высока.
Не подходит для небольших партий: не подходит для создания небольших прототипов из-за высокой стоимости пресс-форм.
3) Применимые сценарии:
Массовое производство.
Детали с высокими требованиями к точности и качеству поверхности.
Тонкостенные детали сложной формы.
(5) 3D-печать+ Процесс литья
1) Плюсы:
Быстрое создание прототипов: значительно сокращает цикл разработки и подходит для быстрого создания прототипов.
Высокая гибкость: возможность быстро изменять конструкции для деталей сложной формы.
Недорогая мелкосерийная продукция: подходит для мелкосерийного или штучного производства без больших затрат на оснастку.
2) Недостатки:
Ограниченная точность: 3D-печатные формы или восковые модели могут быть не такими точными, как традиционные методы.
Ограничения по материалу: свойства материала для 3D-печати могут повлиять на качество конечной отливки.
3) Применимые сценарии:
Быстрое создание прототипов.
Производство небольших партий или единичных изделий.
Детали сложной формы.
(6) Наиболее подходящий процесс для литья прототипы алюминиевых отливок:
3D-печать в сочетании с процессами литья и литья в песчаные формы является наиболее подходящим процессом для изготовления прототипы алюминиевых отливок, если учитывать стоимость, гибкость, точность и сроки изготовления:
1) 3D-печать в сочетании с литьем:
Подходит для быстрого создания прототипов и способна быстро реагировать на изменения в дизайне.
Нет необходимости в дорогостоящих пресс-формах, подходит для мелкосерийного или штучного производства.
Способность обрабатывать детали сложной формы.
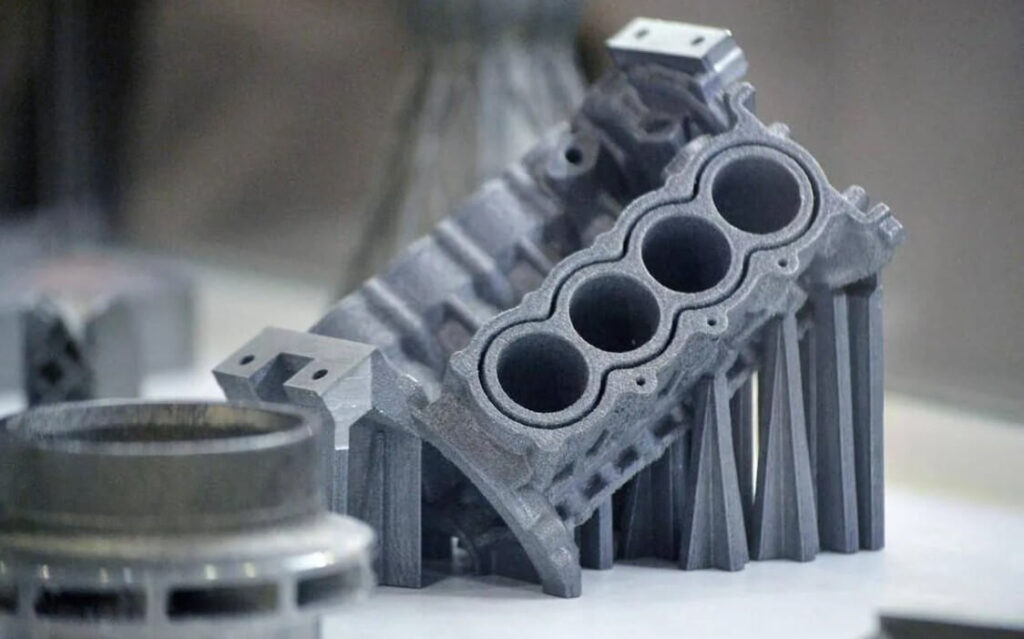
2) Литье в песок:
Низкая стоимость для проектов с ограниченным бюджетом.
Очень гибкие и подходят для производства как отдельных деталей, так и небольших партий.
Возможность отливки крупных деталей.
(7) Резюме:
Если требуется быстрая разработка и высокая гибкость, выбирайте 3D-печать в сочетании с литьем.
Если у вас ограниченный бюджет и вам не требуется высокая точность, выбирайте литье в песок.
Если требуется высокая точность и сложные формы, выбирайте литье по выплавляемым моделям.
При средних объемах производства и высоких требованиях к качеству можно выбрать гравитационное литье в металлические формы.
Если необходимо массовое производство и требуется высокая точность и качество поверхности, выбор падает на литье под давлением.
Выбор наиболее подходящего процесса для конкретных требований позволяет максимально увеличить ценность прототипы алюминиевых отливок и оптимизировать процесс разработки.
3. Как проверить, что прототипы алюминиевых отливок соответствует требованиям?
Проверка соответствия прототипы алюминиевых отливок — это систематический процесс, требующий всестороннего тестирования и оценки по ряду аспектов, включая конструкцию, материал, функциональность и качество поверхности. Ниже подробно описаны этапы и методы проверки:
(1) Проверка конструкции
Цель проверки конструкции — убедиться, что геометрия, размеры и структура прототипы алюминиевых отливок соответствуют чертежам и функциональным требованиям.
1) Контроль размеров
Инструменты: штангенциркули, микрометры, координатно-измерительные машины (КИМ) и т. д.
Метод: Измерьте основные размеры (например, толщину стенок, расположение отверстий, монтажные поверхности и т.д.) и сравните с проектными чертежами.
Фокус: Обеспечьте соблюдение допусков на размеры, особенно в критических зонах посадки.
2) Определение геометрической формы
Инструменты: 3D-сканер или оптическое измерительное оборудование.
Методы: Отсканированные данные сравнивались с 3D-моделью для анализа отклонений.
Основная задача: проверка сложных поверхностей, углов и контуров на соответствие проектным требованиям.
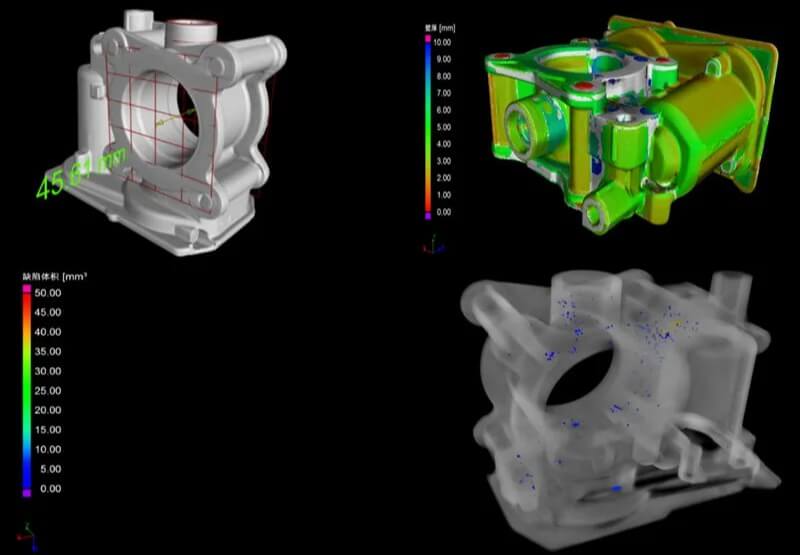
3) Проверка сборки
Метод: Соберите прототипы алюминиевых отливок с другими деталями и проверьте их на соответствие.
Цель: Проверка расположения монтажных отверстий, зазоров и общей эффективности сборки.
(2) Испытание характеристик материала
Испытания свойств материала используются для проверки того, что материал прототипы алюминиевых отливок соответствует проектным требованиям.
1) Анализ химического состава
Инструменты: спектральный анализатор (например, рентгенофлуоресцентный спектрометр).
Методы: Проверьте химический состав алюминиевых отливок, чтобы убедиться, что состав сплава соответствует стандарту.
2) Испытания механических свойств
Испытание на растяжение: проверяет прочность на разрыв, предел текучести и удлинение.
Испытание на твердость: измерение твердости с помощью твердомера по Бринеллю или Роквеллу.
Испытание на удар: проверяет ударопрочность материалов.
3) Металлографический анализ
Инструмент: металлургический микроскоп.
Методы: Наблюдайте за микроструктурой материала и проверяйте наличие дефектов, таких как пористость, усадка и включения.
(3) Функциональное тестирование
Функциональные испытания используются для проверки работоспособности прототипы алюминиевых отливок в реальных условиях эксплуатации.
1) Испытание нагрузкой
Метод: Приложите к отливкам реальную рабочую нагрузку, чтобы проверить их деформацию и несущую способность.
Внимание: Проверьте, нет ли трещин, деформации или поломки.
2) Испытание на усталость
Метод: Моделирование циклического нагружения в реальных условиях эксплуатации для проверки усталостной долговечности отливок.
Внимание: Проверьте, нет ли усталостных трещин или изломов.
3) Испытание на герметичность
Метод: Проведите испытание воздухом или водой под давлением на герметизируемых деталях (например, на блоке двигателя).
Внимание: проверьте, нет ли утечек.
4) Испытание на тепловые характеристики
Метод: Испытание на термоциклирование для радиаторов или деталей, используемых в высокотемпературных средах.
Направление: проверка свойств термической деформации и термической усталости.
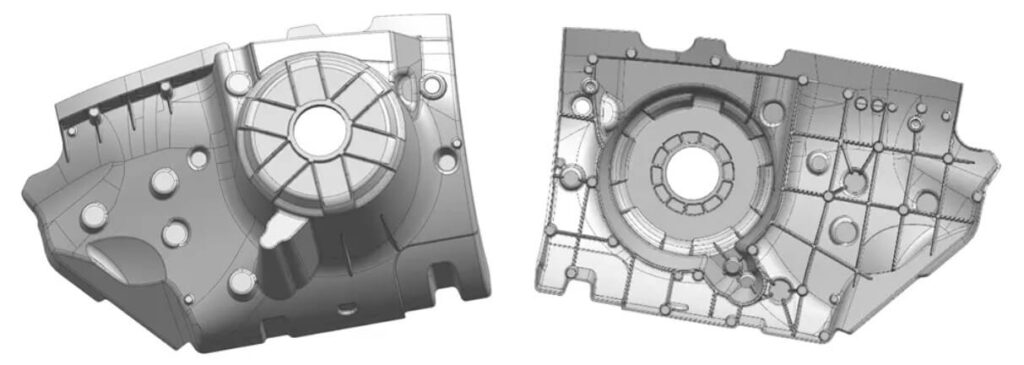
(4) Проверка качества поверхности
Контроль качества поверхности используется для проверки соответствия внешнего вида и свойств поверхности отливок установленным требованиям.
1) визуальный осмотр
Метод: Проверьте поверхность на наличие трещин, пор, усадки и других дефектов невооруженным глазом или с помощью увеличительного стекла.
2) Контроль шероховатости поверхности
Инструмент: измеритель шероховатости поверхности.
Метод: Измерьте шероховатость критических поверхностей, чтобы обеспечить соответствие проектным требованиям.
3) Проверка покрытия или обработки поверхности
Методы: Испытания на адгезию и коррозионную стойкость проводились на отливках с анодированной, пескоструйной и другими видами обработки поверхности.
(5) Неразрушающий контроль
Неразрушающий контроль используется для поиска дефектов в отливке без разрушения детали.
1) Рентгеновский контроль
Внутренние дефекты, такие как пористость, усадка и трещины, исследуются с помощью рентгеновской рентгеноскопии.
2) Ультразвуковой контроль
Обнаружение внутренних дефектов с помощью ультразвука для толстостенных деталей.
3) Осмос
Поверхностные и приповерхностные трещины проверяются с помощью проникающей жидкости.
4) Испытание магнитными частицами
Контроль ферромагнитных материалов для обнаружения поверхностных и приповерхностных дефектов.
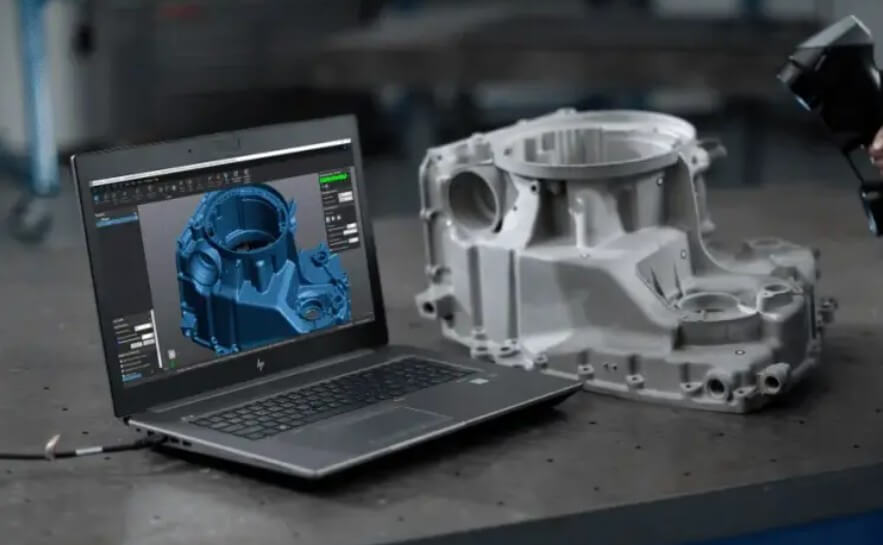
(6) Экологические испытания
Экологические испытания используются для проверки характеристик прототипы алюминиевых отливок в определенных условиях окружающей среды.
1) Испытание на устойчивость к коррозии
Для проверки коррозионной стойкости отливки подвергаются воздействию агрессивных сред, таких как соляной туман, влажность и тепло.
2) Испытание высокой и низкой температурой
Отливки подвергаются воздействию высоких или низких температур для проверки изменения характеристик.
(7) Анализ и улучшение данных
Анализ данных: сравните результаты испытаний с проектными критериями и проанализируйте причины отклонений.
Меры по улучшению: оптимизация конструкции, корректировка параметров процесса или улучшение выбора материала на основе результатов испытаний.
4. Резюме
С помощью ряда этапов, таких как проверка конструкции, тестирование характеристик материала, функциональные испытания, проверка качества поверхности, неразрушающий контроль и экологические испытания, прототипы алюминиевых отливок могут быть всесторонне проверены на соответствие требованиям. Эти испытания не только выявляют потенциальные проблемы, но и предоставляют данные для последующей оптимизации, гарантируя, что качество и характеристики конечного продукта соответствуют ожиданиям.