Точеных деталей из нержавеющей стали:трудности,выбор инструмента и оптимизация процесса
В области механической обработки точеных деталей из нержавеющей стали считаются «трудной костью». Ее склонность к упрочнению при обработке, сила резания, износ инструмента и другие характеристики, эффективность обработки и качество обработки создают большие проблемы.
В этой статье мы подробно расскажем вам о трудностях обработки точеных деталей из нержавеющей стали и предложим полный спектр решений — от выбора инструмента до улучшения качества поверхности и оптимизации процесса, — которые помогут вам легко справиться с проблемами токарной обработки нержавеющей стали.
1. Применение и задачи обработки точеных деталей из нержавеющей стали
Как высокопрочный, устойчивый к коррозии металлический материал, нержавеющая сталь широко используется в аэрокосмической промышленности, автомобилестроении, производстве медицинского оборудования, точных машин и других отраслях. Особенно в высокоточной и востребованной сфере производства точеных деталей из нержавеющей стали предпочитают за их хорошие механические свойства и долговечность.
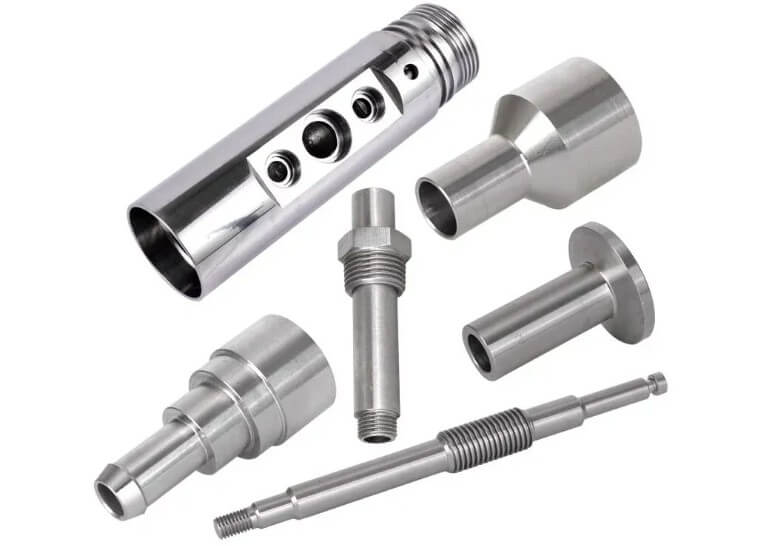
Однако процесс точения нержавеющей стали более сложен, в основном в следующих аспектах:
(1) Высокая твердость и прочность:
Увеличение силы резания и ускоренный износ инструмента.
(2) Сильное упрочнение при работе:
Поверхность заготовки легко затвердевает под воздействием теплового эффекта процесса резки, что затрудняет последующую обработку.
(3) Плохое рассеивание тепла:
В процессе резки температура быстро повышается, что негативно сказывается на стойкости инструмента и качестве поверхности.
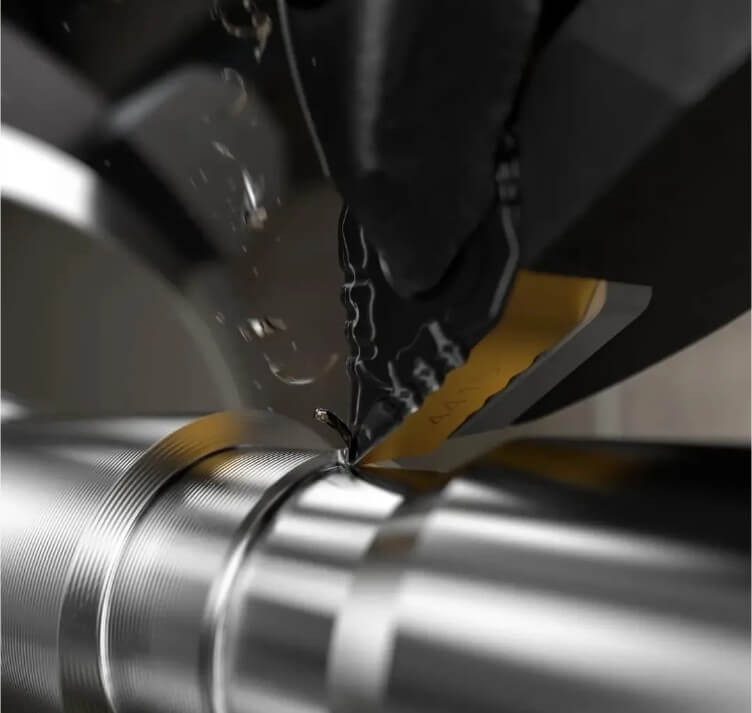
(4) Контроль качества поверхности затруднен:
Качество поверхности изделия трудно гарантировать из-за вибрации, скопления стружки и других факторов.
Для повышения эффективности и качества обработки точеных деталей из нержавеющей стали ниже будут подробно рассмотрены вопросы выбора инструмента, оптимизации параметров резания и стратегий обработки.
2. Основные трудности при токарной обработке нержавеющей стали
(1) Явление закалки на производстве
Нержавеющая сталь в процессе резания склонна к рабочей закалке, то есть в режущей части образуется слой закаленного слоя, так что инструмент труднее резать, что приводит к увеличению силы резания, еще больше ускоряя износ инструмента. Это явление закалки особенно существенно для аустенитной нержавеющей стали (например, 304, 316). Чтобы уменьшить влияние закалки, можно выбирать острые инструменты, больший передний угол и соответствующую скорость резания.
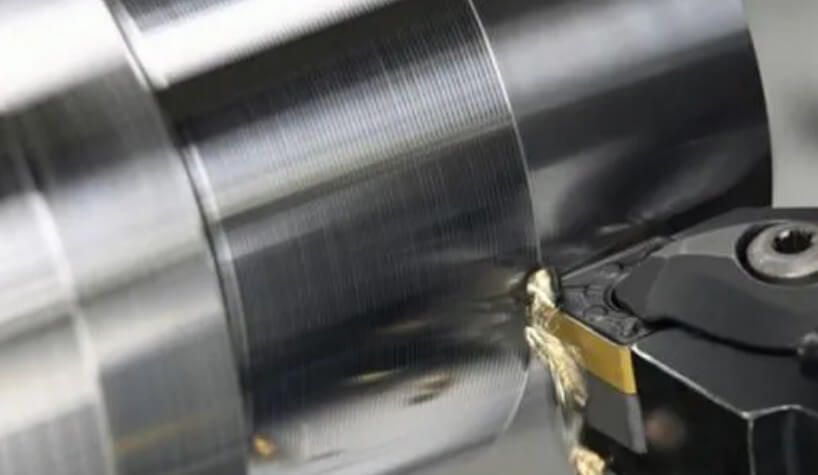
(2) Быстрый износ инструмента
Высокая прочность и твердость нержавеющей стали подвергает инструмент большим нагрузкам в процессе резания, что приводит к ускоренному износу передней и задней поверхностей инструмента. К распространенным видам износа инструмента относятся:
1) Изношенные полумесяцы на передней поверхности лезвия:
При высокотемпературной резке на поверхности инструмента происходит химическая диффузия и связывание.
2) Износ задней поверхности лезвия:
Влияет на точность обработки и качество поверхности.
3) Обломок инструмента:
вызванное сочетанием высоких сил резания и закалки.
Кроме того, износ инструмента не только влияет на качество обработки, но и увеличивает стоимость производства, поэтому необходимо использовать более износостойкие инструментальные материалы и разумно оптимизировать параметры резания.
(3) Высокая температура резки, трудно отводить тепло
Из-за плохой теплопроводности нержавеющей стали большое количество тепла, выделяющегося при резке, трудно быстро отвести, что приводит к повышению температуры инструмента, ускоряет его износ и влияет на точность размеров точеных деталей из нержавеющей стали.
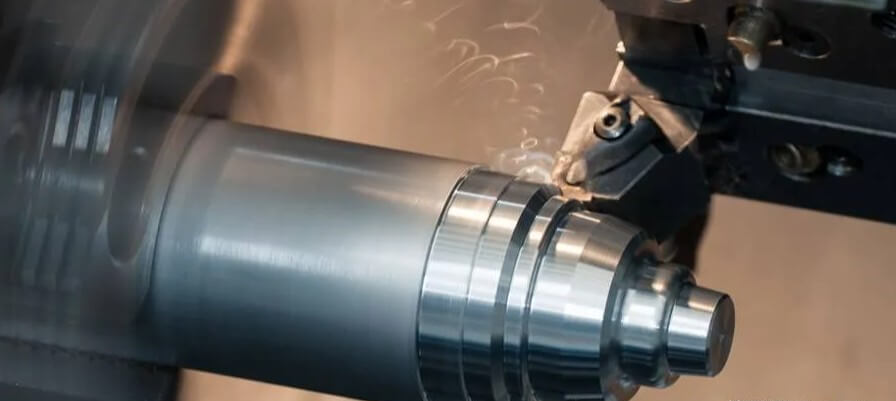
Поэтому использование СОЖ имеет решающее значение. Правильные меры по охлаждению и смазке могут эффективно продлить срок службы инструмента и улучшить качество обработки.
(4) Сложность контроля шероховатости поверхности
В процессе токарной обработки нержавеющей стали из-за закалки, тепла резания и образования стружки на поверхности заготовки появляются царапины, следы от инструмента или заусенцы, что влияет на качество конечного продукта.
Для улучшения качества поверхности можно использовать инструменты с высокой чистотой обработки, оптимизировать параметры резания и применять смазочно-охлаждающие жидкости с эффективным смазыванием.
3. выбор подходящих материалов для инструментов и технологий нанесения покрытий
(1) Выбор материала инструмента
Для изготовления точеных деталей из нержавеющей стали обычно используются следующие инструментальные материалы:
1) Твердосплавные инструменты (инструменты с покрытием):
Например, инструменты с покрытием TiAlN и TiCN обладают высокой износостойкостью и термостойкостью.
2) Керамические инструменты:
Подходит для высокоскоростной резки, обладает отличной износостойкостью, но хрупкая.
3) Инструменты из кубического нитрида бора (CBN):
Используется для отделки нержавеющей стали высокой твердости по более высокой цене.
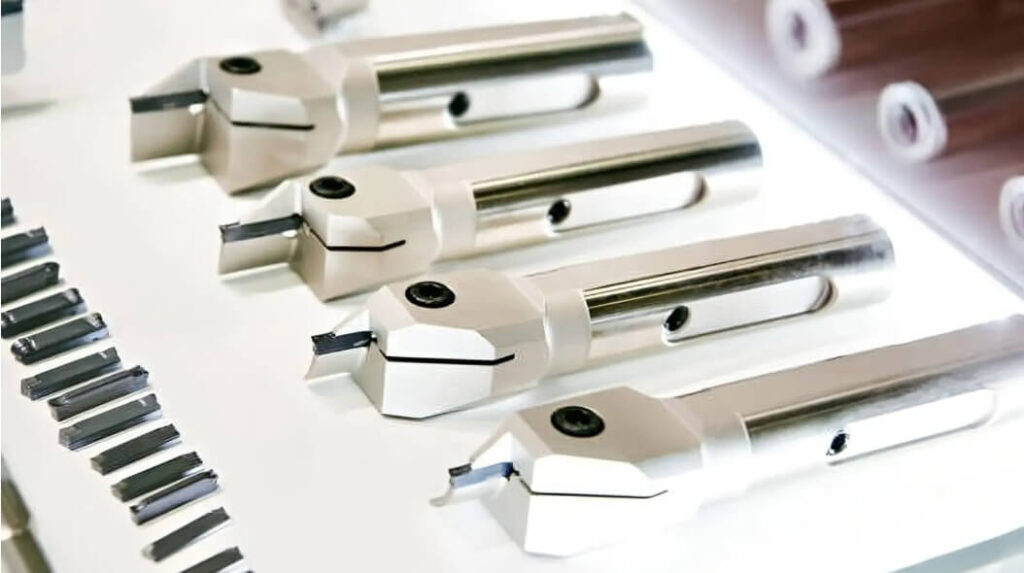
(2) Оптимизация геометрических параметров инструмента
1) Передний угол (γ):
Соответствующее увеличение угла наклона уменьшает силы резания и снижает влияние закалки.
2) Угол спины (α):
Правильный задний угол помогает уменьшить износ задней поверхности инструмента.
3) Притупление края:
Повышает прочность инструмента и снижает риск сколов.
(3) Технология нанесения покрытий на инструменты
Инструменты с покрытием позволяют эффективно снизить износ инструмента и повысить эффективность обработки:
1) Покрытие TiAlN:
Высокая термостойкость, подходит для высокоскоростной резки нержавеющей стали.
2) Покрытие TiCN:
Подходит для обработки на низких и средних скоростях с хорошей износостойкостью.
(3) DLC-покрытие (алмазоподобное покрытие):
Снижает коэффициент трения и уменьшает образование опухолей на стружке.
4. Основные параметры резания, влияющие на качество точеных деталей из нержавеющей стали
(1) Скорость резания (Vc)
Скорость резания оказывает значительное влияние на качество точения нержавеющей стали. Слишком низкая скорость может легко привести к образованию опухолей стружки, что ухудшит качество поверхности заготовки, а слишком высокая скорость может увеличить износ инструмента и сократить срок его службы. В целом, рекомендуемый диапазон скоростей резания следующий:
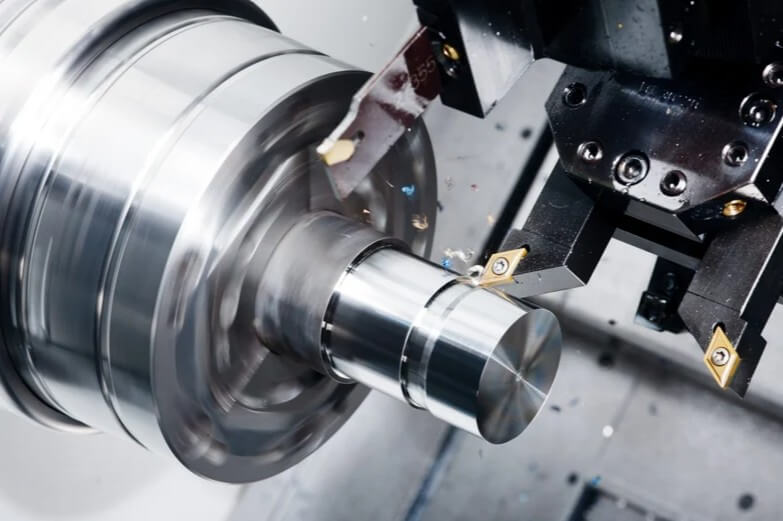
1)Твердосплавный инструмент: 80-200 м/мин
2)Керамический инструмент: 200-400 м/мин
3) Инструменты CBN: 300-500 м/мин.
Для достижения наилучших результатов резания необходимо оптимизировать скорость резания в зависимости от конкретного материала и типа инструмента.
(2) Подача (f)
Величина подачи влияет на толщину стружки и качество обработанной поверхности. Слишком большая подача увеличивает силу резания, что приводит к повышенному износу инструмента и даже влияет на точность размеров заготовки, в то время как слишком малая подача может повлиять на эффективность обработки. Рекомендуемые диапазоны подач приведены ниже:
1) Черновая обработка: 0,1-0,3 мм/об.
2) Финишная обработка: 0,05-0,15 мм/об.
Правильная настройка подачи обеспечивает долговечность инструмента, стабильность резания и улучшение качества обработки поверхности.
(3) Обратный проект (ap)
Выбор величины обратного хода напрямую влияет на скорость съема материала и качество поверхности. На этапе черновой обработки больший объем обратного хода помогает повысить эффективность обработки, в то время как на этапе чистовой обработки объем обратного хода необходимо уменьшить, чтобы получить лучшее качество поверхности. Рекомендуемая величина обратного хода следующая:
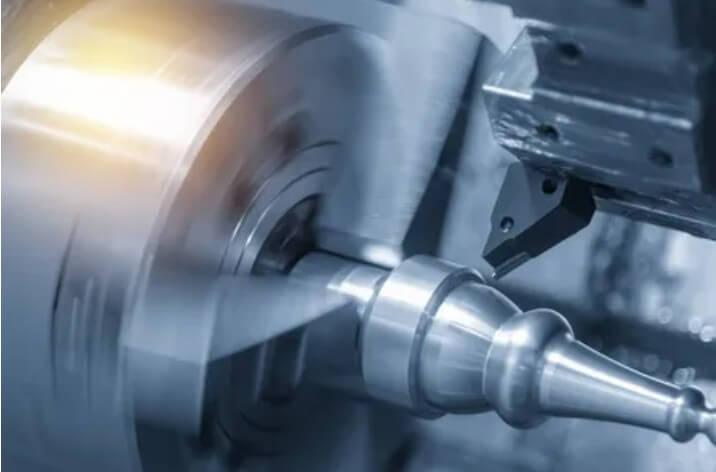
1) Черновая обработка: 1-3 мм
2) Финишная обработка: 0,2-0,5 мм
Подходящая настройка обратной тяги эффективно снижает силы резания и повышает стойкость инструмента, а также уменьшает упрочнение и улучшает качество заготовки.
5. как улучшить качество поверхности точеных деталей из нержавеющей стали
(1) Оптимизация угла наклона инструмента
Оптимизация геометрических углов инструмента необходима для улучшения качества поверхности. Разумные настройки переднего и заднего углов могут снизить сопротивление резанию, уменьшить износ инструмента и улучшить качество поверхности.
1) Передний угол (γ):
Больший угол наклона уменьшает силы резания, снижает упрочнение и улучшает качество поверхности заготовки.
2) Угол спины (α):
Правильный задний угол уменьшает износ задней поверхности инструмента и обеспечивает стабильность обработки.
3) Притупление края:
Небольшое затупление режущей кромки уменьшает сколы и увеличивает срок службы инструмента при сохранении качества поверхности.
(2) Использование высокоэффективной смазочно-охлаждающей жидкости
Использование смазочно-охлаждающих жидкостей необходимо для контроля температуры, снижения силы резания и улучшения качества поверхности. Различные типы смазочно-охлаждающих жидкостей используются для различных видов обработки:
1) Водорастворимая жидкость для резки:
В основном используется для высокоскоростной резки, хороший эффект охлаждения, может эффективно снизить температуру резки.
2) Жидкости для резки на масляной основе:
Подходит для низкоскоростной обработки, хорошо смазывается и помогает снизить трение между инструментом и заготовкой.
3) Синтетические смазочно-охлаждающие жидкости:
Сочетает в себе охлаждение и смазку для большинства сценариев обработки нержавеющей стали.
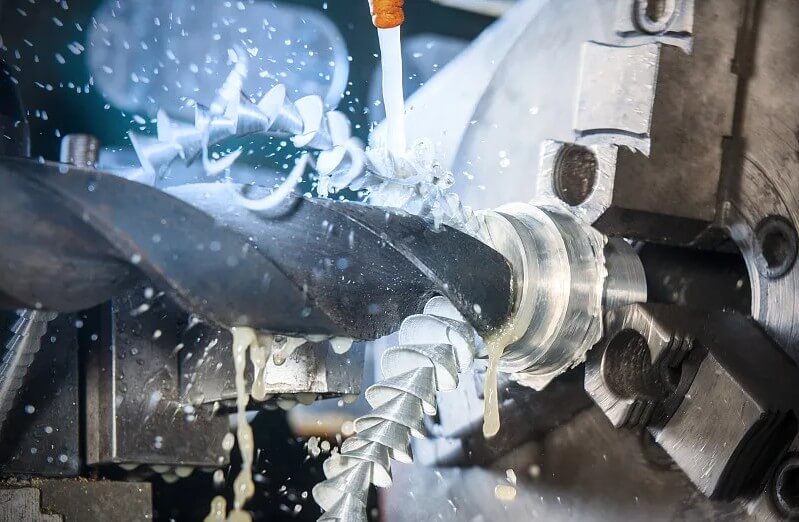
(3) Снижение силы резания
Величина силы резания напрямую влияет на качество поверхности точеных деталей из нержавеющей стали и точность обработки. Методы уменьшения силы резания включают:
1) Используйте острые инструменты, чтобы снизить сопротивление резанию и улучшить качество поверхности.
2) Оптимизируйте подачу и скорость резания, чтобы избежать закалки.
3) Применяется виброгасящий резцедержатель для снижения вибрации и повышения стабильности обработки.
6. оптимизация процесса обработки точеных деталей из нержавеющей стали
(1) Черновая и чистовая обработка в несколько этапов
Для повышения эффективности и качества обработки черновая и чистовая обработка обычно выполняются поэтапно.
1) Черновая обработка:
Для повышения скорости съема материала используются большие обратные тяги и подачи, а припуски на обработку обычно больше.
2) Отделка:
Снижение скорости и подачи резания улучшает качество поверхности, а обеспечивает точность размеров заготовки.
(2) Уменьшение частоты смены инструмента
Сокращение частоты смены инструмента не только снижает производственные затраты, но и повышает стабильность обработки. Способы оптимизации срока службы инструмента включают:
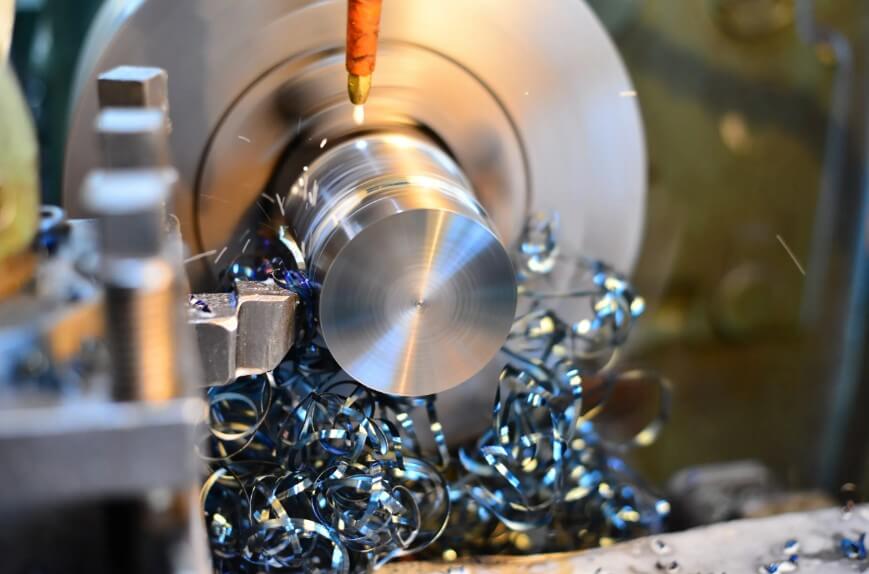
1) Выбирайте высокопроизводительные инструменты, такие как инструменты из твердого сплава с покрытием или керамики, для повышения износостойкости.
2) Регулярно проверяйте и перетачивайте инструмент, чтобы избежать ухудшения качества обработки из-за чрезмерного износа инструмента.
3) Оптимизируйте использование смазочно-охлаждающей жидкости для снижения нагрева при резании и увеличения срока службы инструмента.
(3) Сокращение расходов на обработку
1) Снижение затрат — ключ к конкурентоспособности без ущерба для качества обработки.
2) Оптимизация параметров резания для повышения скорости съема материала и сокращения времени обработки.
3) Внедрение автоматизированной обработки, сокращение ручного вмешательства и повышение эффективности производства.
4) Разумный выбор инструментов и смазочно-охлаждающей жидкости для снижения стоимости расходных материалов.
7. Вывод: краткое описание стратегий оптимизации для точеных деталей из нержавеющей стали
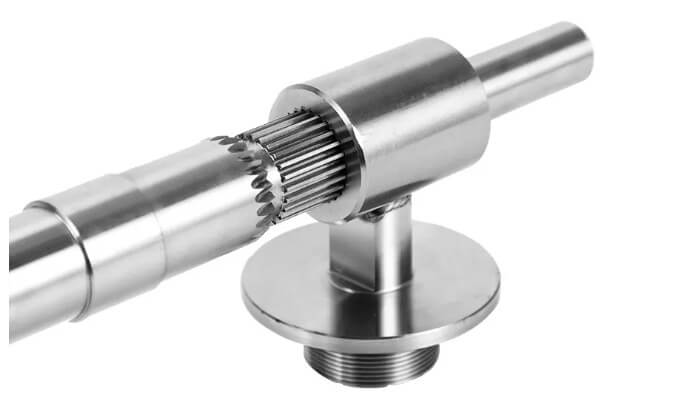
●Разумный подбор инструментов для повышения износостойкости и срока службы.
●Оптимизация параметров резания для повышения эффективности и качества обработки.
●Применяется высокоэффективная технология охлаждающей смазки для снижения нагрева при резке.
●Разумное планирование черновой и чистовой обработки для повышения коэффициента квалификации продукции.
Оптимизация стратегий обработки и повышение уровня автоматизации позволяют эффективно справляться с трудностями обработки нержавеющей стали, повышая при этом производительность и качество продукции.
What do you think?
[…] (2) Бронированные машины и защитное снаряжение […]
[…] не только мощной огневой системой и мобильностью, но и отличной защитой, чтобы противостоять угрозе различных […]
[…] баллистических материалов играют жизненно важную роль в современном обществе, причем не только в защите военнослужащих от пуль, но и в правоохранительной деятельности, обеспечении безопасности и защите гражданского населения. баллистических материалов — это материалы, способные противостоять пулям или осколкам, такие как стекловолокнистые композиты, арамид и сверхвысокомолекулярный полиэтилен. Их преимуществами являются хорошая эластичность, малый вес, простота изготовления и т. д. […]
[…] Защитный принцип брони основан в первую очередь на физических свойствах материала рассеивать и поглощать энергию удара. Благодаря высокой твердости и прочности твердые баллистические материалы рассеивают кинетическую энергию пули на большой площади и поглощают часть энергии. Мягкие баллистические материалы дополнительно рассеивают и поглощают энергию удара, преобразуя кинетическую энергию пули во внутреннюю энергию волокон за счет растяжения и деформации волокон. […]
[…] аморфных материалов для более эффективного пробития современной брони. По сравнению с традиционными боеприпасами с […]
[…] собственными характеристиками, и их применение в области баллистической защиты становится все более широким. Так кто же из них […]