Коррозионностойкие отливки в нефтехимической промышленности в применении к детальному анализу
Коррозионностойкие отливки, являясь основными компонентами нефтехимического оборудования, широко используются в корпусах насосов, клапанах, трубопроводах, теплообменниках и других устройствах. Разумный выбор материала, передовой производственный процесс и эффективные меры защиты являются залогом долгосрочной стабильной работы отливок.
В данной статье основное внимание будет уделено выбору материала для коррозионностойкие отливки и оптимизации их характеристик, процессу изготовления, конкретным областям применения, анализу отказов и мерам защиты для всестороннего обсуждения.
1. Что такое коррозионностойкие отливки?
(1) Определения
Коррозионностойкие отливки — это литые детали, которые могут стабильно работать в течение длительного времени в агрессивных средах благодаря специальному подбору материалов, технологиям изготовления и обработки поверхности. Такие отливки обычно используются в промышленном оборудовании, подверженном воздействию кислот, щелочей, солей, газов и других агрессивных сред, могут эффективно противостоять химической коррозии, электрохимической коррозии, коррозионному растрескиванию под напряжением и другим видам коррозии.
(2) Характеристики коррозионностойкие отливки:
1) Свойства материала:
●Использование коррозионностойких сплавов, таких как нержавеющая сталь, сплавы на основе никеля, титановые сплавы и высококремнистый чугун.
●Материал обладает высокой коррозионной стойкостью, высокой прочностью и хорошими механическими свойствами.
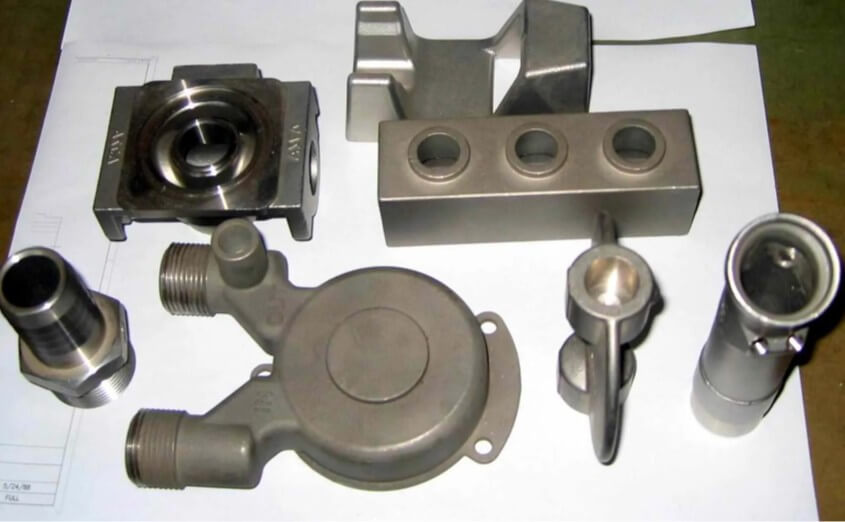
2) Процесс производства:
●Технологии точного литья, такие как литье по выплавляемым моделям, гравитационное литье, литье под низким давлением и литье под давлением (широко используемое для алюминиевых металлических материалов), используются для обеспечения высокого качества и сложных форм отливок.
●Коррозионная стойкость дополнительно повышается за счет термообработки и обработки поверхности (например, напыление, гальваническое покрытие).
3) Среда применения:
●Подходит для экстремальных условий работы с высокой температурой, высоким давлением и сильной коррозионной средой.
●Широко используется в нефтехимической, судостроительной, электроэнергетической, фармацевтической и других отраслях промышленности.
2. распространенные формы коррозии компонентов в нефтехимической промышленности
(1) Равномерная коррозия
Коррозия происходит равномерно по всей поверхности металла, что приводит к постепенному истончению толщины материала.
Общие сценарии:
Внутренние поверхности резервуаров и трубопроводов подвергаются воздействию кислотных или щелочных сред.
Стены реактора подвергаются воздействию агрессивных химических веществ.
(2) Питтинг (локализованная коррозия)
Глубокая коррозия возникает на локальных участках металлических поверхностей, образуя небольшие отверстия или ямки.
Общие сценарии:
Оборудование из нержавеющей стали в средах, содержащих хлорид-ионы (например, морская и соленая вода).
Трубопроводы, клапаны, теплообменники и другие компоненты.
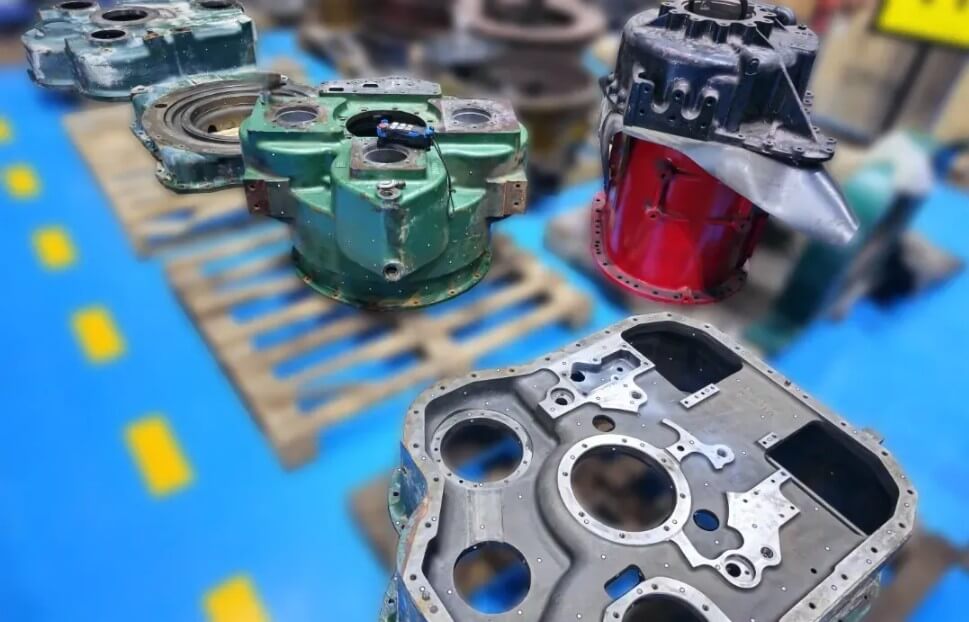
(3) Коррозионное растрескивание под напряжением (КРН)
Под совместным воздействием растягивающего напряжения и коррозионной среды на поверхности металла появляются и расширяются трещины.
Общие сценарии:
Реакторы и трубопроводы, работающие в условиях высоких температур и высокого давления.
Оборудование, подверженное воздействию коррозионных сред, таких как сероводород и хлорид-ионы.
(4) Межкристаллитная коррозия
Коррозия протекает по границам зерен металла, что приводит к преимущественной коррозии в приграничных областях.
Общие сценарии:
Сварные соединения или неправильно термически обработанные детали.
Оборудование, подверженное воздействию кислотных сред.
(4) Коррозия с вымыванием
Высокоскоростной поток жидкости вызывает сочетание механического истирания и химической коррозии металлических поверхностей.
Общие сценарии:
Трубные колена, корпуса насосов, рабочие колеса и другие компоненты.
Системы транспортировки жидкостей, содержащих твердые частицы.
(5) Водородное охрупчивание
Металлы поглощают атомы водорода в водородной среде, что приводит к охрупчиванию и растрескиванию материала.
Общие сценарии:
Реактор гидрогенизации, водородный трубопровод высокого давления.
Оборудование, работающее в кислой среде (например, сероводород).
Резюме:
В нефтехимической промышленности детали подвергаются коррозии в различных формах, в основном из-за наличия высокой температуры, высокого давления, сильных агрессивных сред в окружающей среде (таких как кислоты, щелочи, соли, сероводород, хлорид-ионы и т.д.) и сложных условий работы.
Поэтому необходимо повышать коррозионную стойкость отливок за счет разумного выбора материалов, передовых производственных процессов и эффективных защитных мер, чтобы продлить срок службы оборудования. Ниже будет подробно рассказано о том, как с помощью коррозионностойкие отливки продлить срок службы химического оборудования:
3. Выбор материала и оптимизация характеристик коррозионностойкие отливки
(1) Основные коррозионно-стойкие материалы и характеристики
Коррозионностойкие отливки материалы, обычно используемые в нефтехимической промышленности, включают следующие категории:
1) Нержавеющая сталь (304, 316L, 2205 дуплексная нержавеющая сталь)
Она обладает хорошей стойкостью к кислотной и щелочной коррозии, особенно молибденсодержащая 316L хорошо работает в сильных кислотных средах. Дуплексная нержавеющая сталь, с другой стороны, имеет преимущества в стойкости к точечной коррозии и коррозии под напряжением, и подходит для конвейерных трубопроводов, теплообменников и другого оборудования.
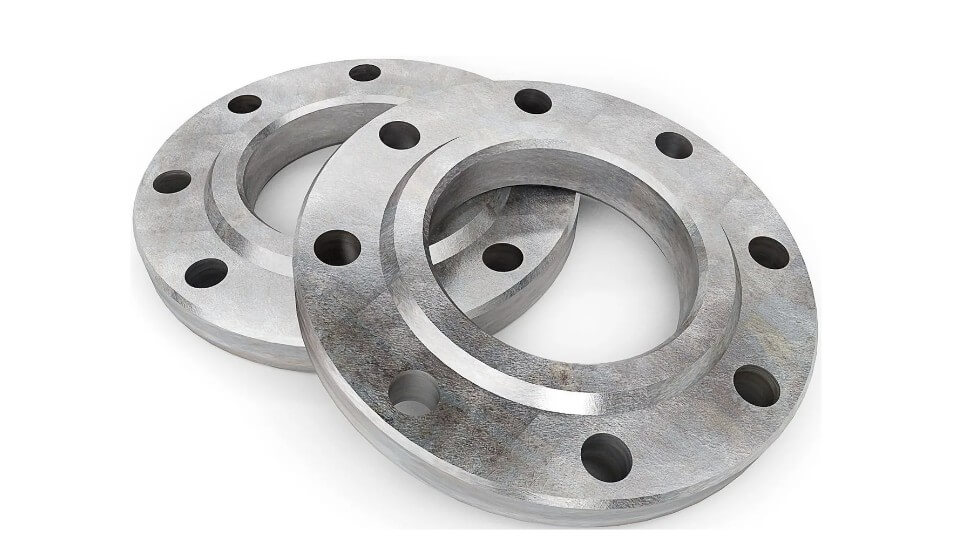
2) Высококремнистый чугун (Si≥14%)
Высококремнистый чугун в концентрированной серной кислоте и других сильных кислотных средах обладает отличной коррозионной стойкостью, широко используется в передаче сильных кислотных насосов и трубопроводов, но его хрупкость велика.
3) Сплавы на основе никеля (инконель, хастеллой, монель)
Обладает отличной стойкостью к высокотемпературному окислению и коррозии ионами хлора, широко используется в оборудовании каталитического крекинга и трубопроводах теплообменников.
4) Сплав на основе кобальта (стеллит)
В основном используется в высокотемпературных износостойких деталях, таких как уплотнительные поверхности клапанов, подшипники и т.д. Он хорошо работает в условиях высоких температур.
5) Титан и титановые сплавы
Благодаря своей исключительной устойчивости к хлоридной коррозии она широко используется в ключевых коррозионностойкие отливки для морских нефтяных платформ, систем охлаждения, трубопроводов и других критически важных коррозионностойкие отливки.
(2) Методы оптимизации свойств материалов
1) Оптимизация легирующих элементов:
Увеличение содержания Cr, Mo, Ni и других легирующих элементов для улучшения коррозионной стойкости и высокотемпературной стабильности материала.
2) Процесс термической обработки:
Оптимизация микроструктуры материала путем обработки твердым раствором и отпуска для повышения коррозионной стойкости под напряжением.
3) Технология модификации поверхности:
Азотирование, PVD/CVD-покрытие, керамическое напыление и другие методы используются для повышения коррозионной и износостойкости.
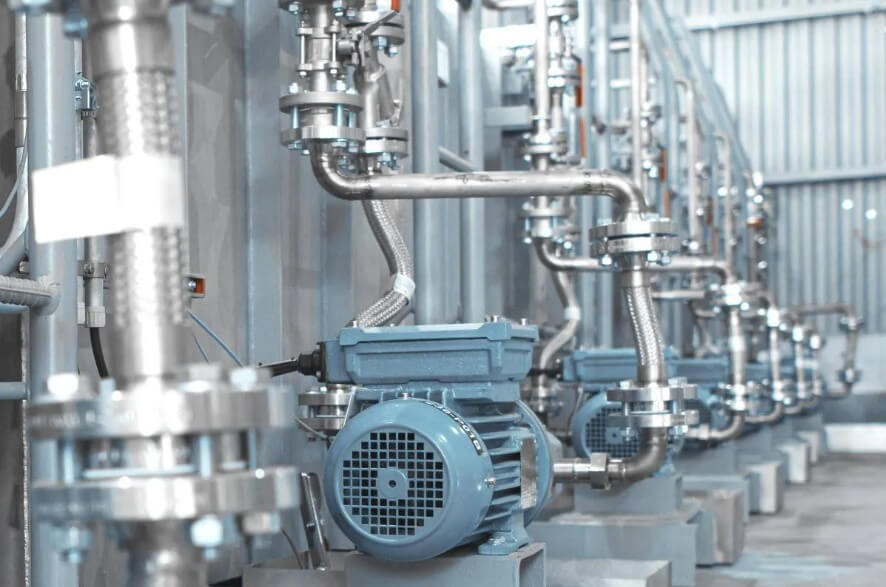
4. Обзор процесса механической обработки нефтехимических коррозионностойкие отливки
В соответствии с различными требованиями, предъявляемыми нефтехимическим оборудованием к коррозионностойкие отливки, в основном используется следующий процесс литья:
(1) Гравитационное литье
1) Применяемые части:
Толстостенные коррозионностойкие отливки для корпусов крупных насосов, корпусов клапанов, опор теплообменников, деталей основания реакторов и т.д.
2) Характеристики процесса:
●Заполнение полостей под действием силы тяжести самого жидкого металла, без дополнительного давления, является относительно простым процессом.
●Она подходит для производства крупногабаритных отливок с более равномерной толщиной стенок, подходит для углеродистой стали, нержавеющей стали и некоторых высоколегированных материалов.
●Благодаря более медленной скорости охлаждения внутренняя структура отливки становится однородной, что снижает риск концентрации напряжений и образования трещин.
●Обладает высокой гибкостью, так как может быть сформован из песка и металла.

3) Случаи применения:
●Корпус большого нефтехимического насоса:
Требования выдерживать длительную высокую температуру и давление и коррозионную среду эрозии, использование гравитационного литья для обеспечения прочности отливок и коррозионной стойкости.
●Основание и опора реактора:
Крупные несущие конструкции требуют высокой несущей способности и коррозионной стойкости, а гравитационное литье обеспечивает их целостность и механическую прочность.
●Корпус клапана для нефтехимического оборудования:
Гравитационное литье уменьшает такие дефекты, как усадочные отверстия, и повышает герметичность и срок службы корпуса клапана.
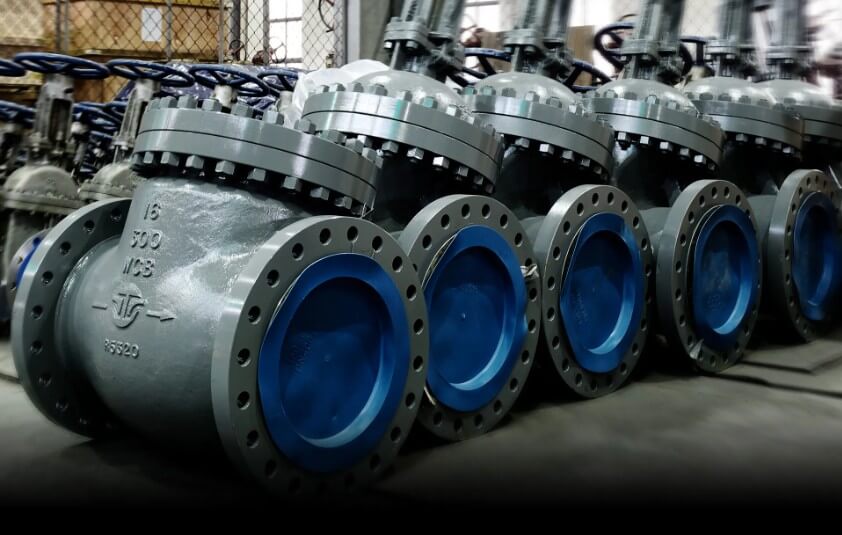
(2) Инвестиционное литье (литье по выплавляемым моделям)
1) Применяемые части:
Корпус клапана, рабочее колесо, корпус насоса, фланец и другие высокоточные сложные отливки.
2) Характеристики процесса:
●Использование восковых форм для изготовления точных оболочек позволяет производить отливки сложной формы с тонкими стенками.
●Высокая точность размеров отливок (до ±0,05 мм), сокращение объема обработки и повышение эффективности использования материала.
●Подходит для нержавеющей стали, дуплексной нержавеющей стали, сплавов на основе никеля и других высококоррозионностойких материалов.
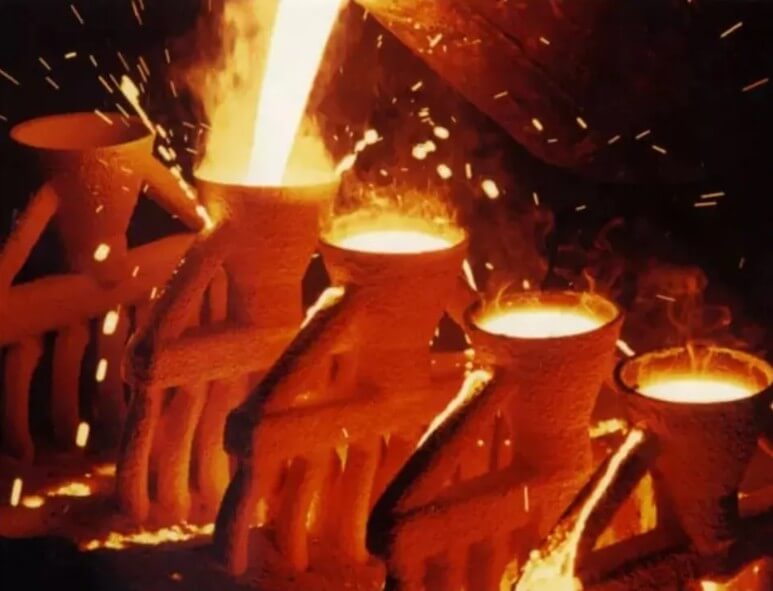
3) Случаи применения:
●Отливки корпуса клапана высокого давления:
Необходимо выдерживать высокую температуру и давление, а также сильные агрессивные среды, использование литья по выплавляемым моделям позволяет добиться бездефектной плотной формовки, избежать микротрещин в процессе обработки.
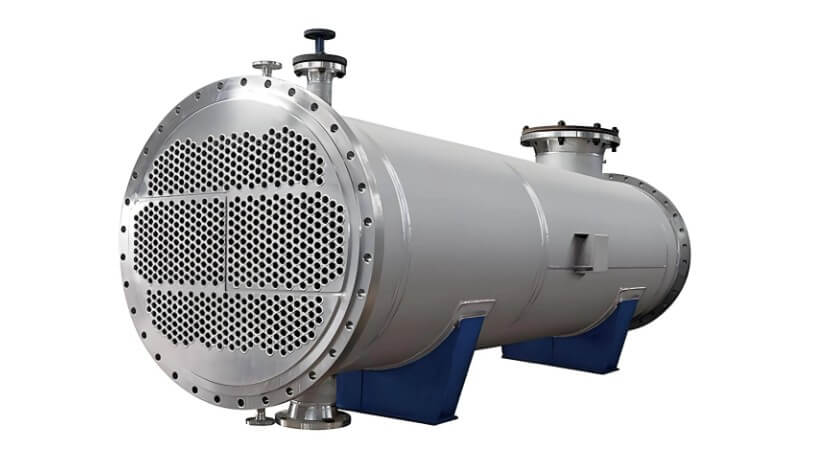
●Крыльчатка химического насоса:
Использование дуплексного литья из нержавеющей стали CD4MCu улучшает коррозионную стойкость к ионам хлора и продлевает срок службы.
(3) Литье под низким давлением
1) Применяемые части:
Корпуса теплообменников, арматура реакторов, соединения нефтехимических трубопроводов и другие коррозионностойкие отливки, требующие высокой герметичности.
2) Характеристики процесса:
●Использование низкого давления (обычно 0,02-0,06 МПа), чтобы жидкий металл медленно заполнял полость для уменьшения пористости и повышения плотности отливки.
●Она позволяет получать отливки с равномерной толщиной стенок и отличной коррозионной стойкостью, которые подходят для работы в условиях высоких температур и высокого давления.
●В основном используется для литья высоколегированной нержавеющей стали, сплавов на основе никеля, титановых сплавов и других специальных коррозионностойких материалов.
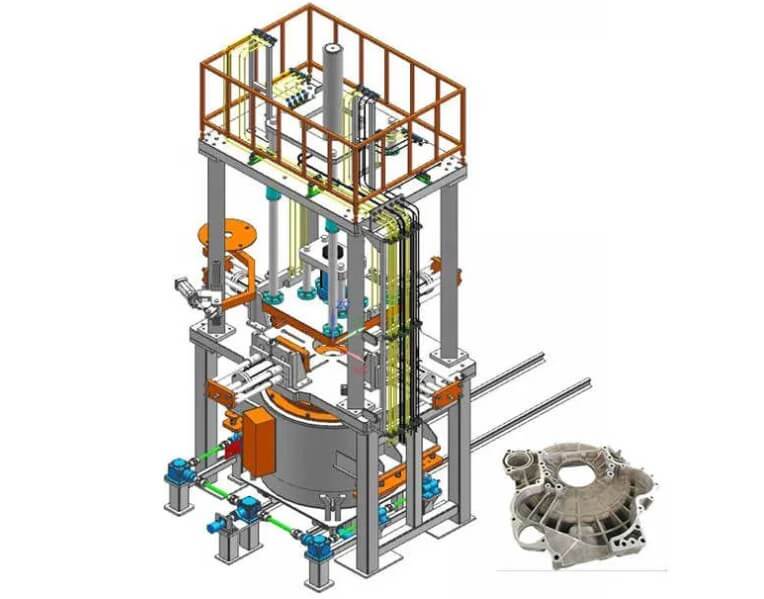
3) Случаи применения:
●Корпус теплообменника:
Теплообменники подвергаются воздействию агрессивных сред в течение длительного времени, и использование литья под низким давлением повышает однородность и коррозионную стойкость материала и снижает риск утечки.
●Мешалка для реактора:
Компоненты мешалок для каталитических реакций требуют высокой коррозионной стойкости, а литье под низким давлением обеспечивает гладкую, бездефектную поверхность и повышенный срок службы.
5. меры по контролю качества коррозионностойкие отливки
Для того чтобы обеспечить длительную стабильную эксплуатацию коррозионностойкие отливки в нефтехимической промышленности, необходимо строго контролировать качество во всем процессе производства.
(1) Контроль сырья
●Сплавы высокой чистоты используются для снижения содержания вредных примесей, таких как сера и фосфор, и повышения коррозионной стойкости.
●Металлографический анализ позволяет убедиться, что коррозионностойкие отливки имеют однородную структуру без дендритных сегрегаций и осажденных фаз.
(2) Оптимизация процесса литья
●Продуманная конструкция системы заливки, оптимизация конструкции бегунов и стояков, уменьшение количества включений и усадочных отверстий, повышение плотности отливки.
●Строго контролируйте температуру и скорость заливки, чтобы предотвратить холодную сегрегацию металлической жидкости и улучшить качество формовки.
●Защитная газовая или вакуумная среда используется для уменьшения окислительных включений и повышения коррозионной стойкости отливок.
(3) Неразрушающий контроль и проверка механических свойств
●Рентгеновский контроль (RT): проверка на наличие внутренних дефектов, таких как воздушные отверстия и усадка.
●Ультразвуковой контроль (UT): обнаруживает включения и трещины в отливке.
●Испытание на проникновение (PT): выявляет мелкие трещины и отверстия на поверхности отливки.
●Испытания на механические характеристики: проводятся испытания на растяжение, удар и твердость, чтобы убедиться, что отливки соответствуют требованиям для использования.
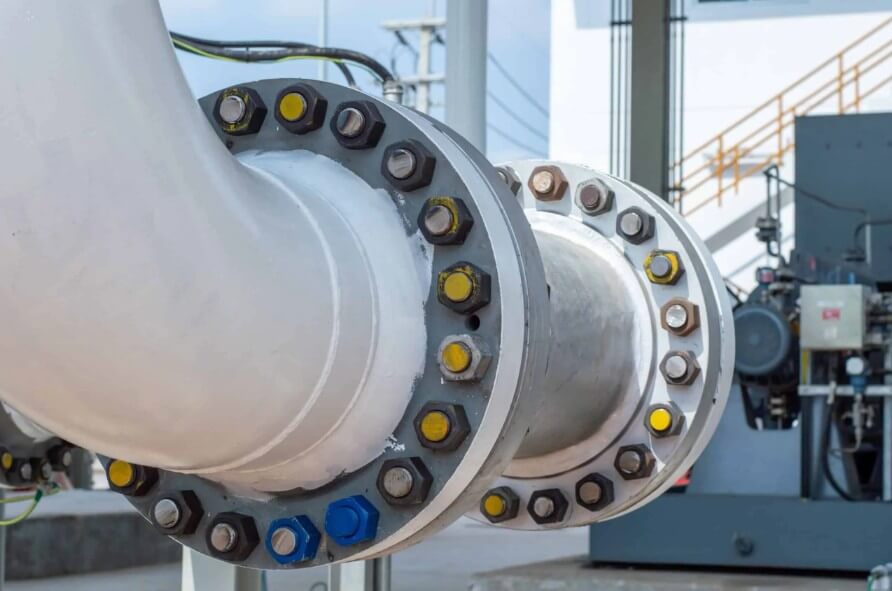
(4) Испытание на коррозионную стойкость
●Испытание соляным туманом: оценивает скорость коррозии отливок в хлоридной среде.
●Испытание на электрохимическую коррозию: проверяет питтинговый потенциал и коррозионную стойкость отливок.
●Эксперимент по высокотемпературной коррозии: моделирование реальных условий работы, проверка коррозионной стойкости отливок в условиях высокой температуры и высокого давления.
6. Резюме
Нельзя игнорировать ключевую роль коррозионностойкие отливки в нефтехимической промышленности. Разумный выбор материала, передовой производственный процесс и эффективные меры защиты являются основой для обеспечения долгосрочной стабильной работы оборудования.
What do you think?
[…] (2) Бронированные машины и защитное снаряжение […]
[…] не только мощной огневой системой и мобильностью, но и отличной защитой, чтобы противостоять угрозе различных […]
[…] баллистических материалов играют жизненно важную роль в современном обществе, причем не только в защите военнослужащих от пуль, но и в правоохранительной деятельности, обеспечении безопасности и защите гражданского населения. баллистических материалов — это материалы, способные противостоять пулям или осколкам, такие как стекловолокнистые композиты, арамид и сверхвысокомолекулярный полиэтилен. Их преимуществами являются хорошая эластичность, малый вес, простота изготовления и т. д. […]
[…] Защитный принцип брони основан в первую очередь на физических свойствах материала рассеивать и поглощать энергию удара. Благодаря высокой твердости и прочности твердые баллистические материалы рассеивают кинетическую энергию пули на большой площади и поглощают часть энергии. Мягкие баллистические материалы дополнительно рассеивают и поглощают энергию удара, преобразуя кинетическую энергию пули во внутреннюю энергию волокон за счет растяжения и деформации волокон. […]
[…] аморфных материалов для более эффективного пробития современной брони. По сравнению с традиционными боеприпасами с […]
[…] собственными характеристиками, и их применение в области баллистической защиты становится все более широким. Так кто же из них […]