Analysis of key technologies of rapid quench casting
Rapid quench casting is an advanced metal processing technology that cools molten metal at an extremely fast speed and solidifies it in a very short time. This technology can significantly improve the microstructure of the material, thereby improving the physical and chemical properties of the material. This article will explore in depth the principles, characteristics, classification, key technologies, challenges and corresponding solutions of rapid quench casting.
1.Overview of rapid quench casting
Rapid quench casting is an advanced casting method that changes the microstructure of the material by controlling the cooling rate. Its basic principle is to solidify the molten metal at an extremely high cooling rate (usually in the range of several thousand to tens of thousands of degrees Celsius per second) to inhibit grain growth and form a fine microstructure. This fine microstructure not only improves the mechanical properties of the material, but also improves its physical and chemical properties.
2.Principles and characteristics of rapid quench casting
(1) Principle
The core of rapid quench casting is to control the cooling rate. Traditional casting methods have a slow cooling rate, and the grains have enough time to grow, resulting in a coarse microstructure of the material. By using special cooling media (such as water-cooled copper rollers, atomization cooling, etc.) and process design, the molten metal solidifies in a very short time to form fine equiaxed crystals or even amorphous structures.
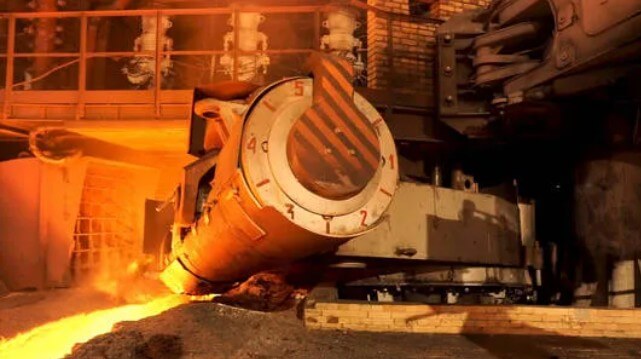
(2) Features
1) High cooling rate:
The cooling rate of rapid casting is much higher than that of traditional casting methods, usually between 103-106K/s, which helps to form a fine microstructure.
2) Microstructure refinement:
Due to the fast cooling rate, the grains do not have time to grow, thus forming a uniform and fine microstructure, which improves the strength and toughness of the material.
3) Composition uniformity:
During the rapid solidification process, the solute atoms do not have time to diffuse, which avoids composition segregation and improves the composition uniformity of the material.
4) Amorphous forming ability:
Under certain conditions, rapid casting can form amorphous alloys, which have unique physical and chemical properties, such as high strength, high hardness, and excellent corrosion resistance.
3.Analysis of the process flow and casting formation mechanism of rapid quench casting
(1) Process flow
The process flow of rapid quench casting mainly includes four steps: material preparation, smelting, pouring and cooling.
First, the raw materials are strictly screened and prepared to ensure the quality and purity of the materials.
Next, the raw materials are smelted at high temperature to obtain uniform molten metal.
Then, the molten metal is quickly poured into a pre-designed mold. The mold is usually made of materials with high thermal conductivity, such as copper or graphite, to ensure that the molten metal can be cooled quickly.
Finally, by controlling the cooling medium and cooling conditions, the molten metal solidifies at an extremely fast speed to obtain castings with excellent properties.
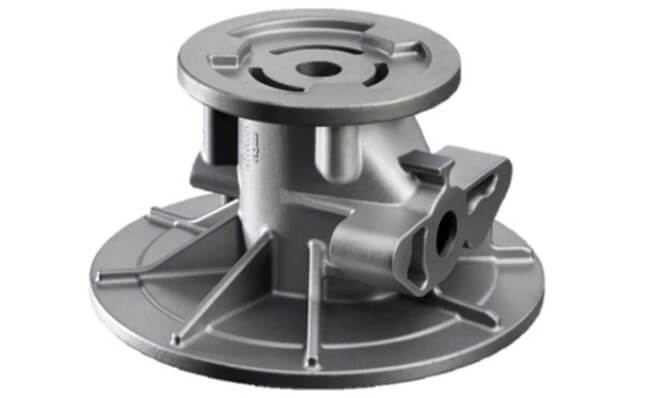
(2) Casting formation mechanism
During the rapid quench casting process, the solidification speed of the molten metal is very fast, usually between a few seconds and a few milliseconds. This extremely fast solidification speed causes the grains to have no time to grow, thus forming a fine grain structure.
In addition, supersaturated solid solution or metastable phase structure may be formed during the rapid quench casting process, which can further improve the performance of the material. The formation of fine grain structure and supersaturated solid solution is the key mechanism for rapid quench casting to improve material performance. By optimizing the cooling rate and cooling conditions, the microstructure of the material can be further controlled, thereby achieving precise regulation of material properties.
4.Classification of rapid quench casting
Rapid quench casting is an advanced casting method that mainly improves the structure and performance of castings by rapid cooling. The following are several main classifications of this technology:
(1) Single-roller rapid quench casting:
This technology uses a rotating cooling roller, and the molten metal quickly solidifies on the roller surface to form a thin strip or sheet. It is suitable for the production of metal strips with excellent surface quality and fine grain structure.
(2) Double-roller rapid quench casting:
Two relatively rotating cooling rollers are used, and the molten metal solidifies between the two rollers to form a thin strip. This technology is suitable for the efficient production of metal strips and is widely used in the production of aluminum alloys and copper alloys.
(3) Atomization quench casting:
The molten metal is atomized into tiny droplets by high-pressure gas, and then rapidly solidified on the collector. This method can produce fine powders or particles with extremely high cooling rates, which are suitable for the preparation of high-performance alloy materials.
(4) Immersion quench casting:
The prefabricated model is immersed in the molten alloy, then quickly removed and cooled. This technology is suitable for the production of castings with complex shapes and can obtain fine microstructures and excellent mechanical properties.
(5) Directional solidification quench casting:
By controlling the solidification direction, the casting solidifies in a specific direction, thereby eliminating transverse grain boundaries and improving the performance of the material. It is often used in the production of high-performance components such as aircraft engine blades.
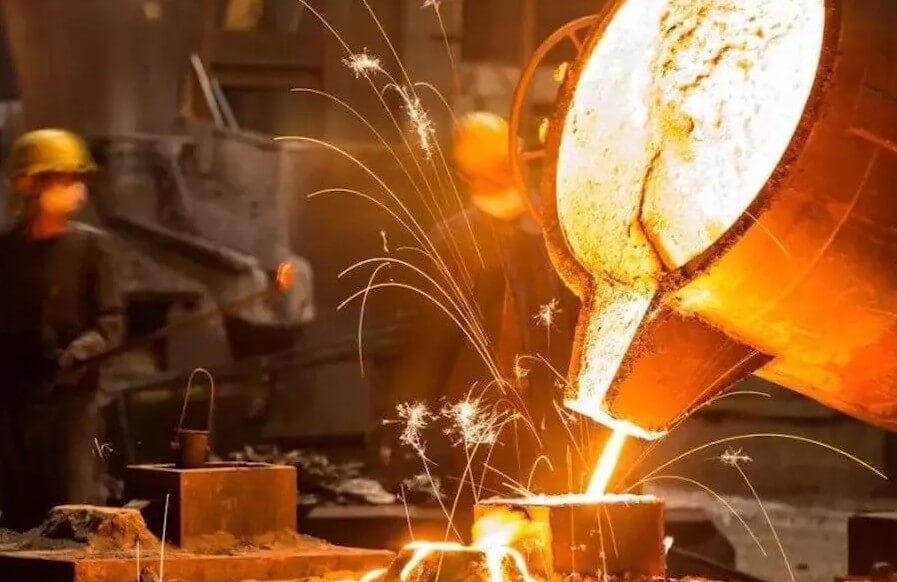
5.Key technologies of rapid quench casting
(1) Selection and control of cooling medium
In rapid quench casting, the selection of cooling medium has a decisive influence on the cooling rate and casting quality. Commonly used cooling media include water, oil, gas and certain special liquids such as liquid nitrogen.
Water has the fastest cooling rate and is suitable for quench casting of most metals, but it may cause increased thermal stress in the casting. Oil and gas have a slower cooling rate and are suitable for occasions where the cooling rate is not high. Special liquid cooling media such as liquid nitrogen have extremely low temperatures and can achieve faster cooling rates. They are suitable for special materials with extremely high performance requirements.
(2) Mold design and material selection
Mold design is another key technology in quench casting. The mold needs to have good thermal conductivity and high temperature resistance to ensure that the molten metal can be cooled quickly and evenly. Commonly used mold materials include copper, graphite and some special alloy materials.
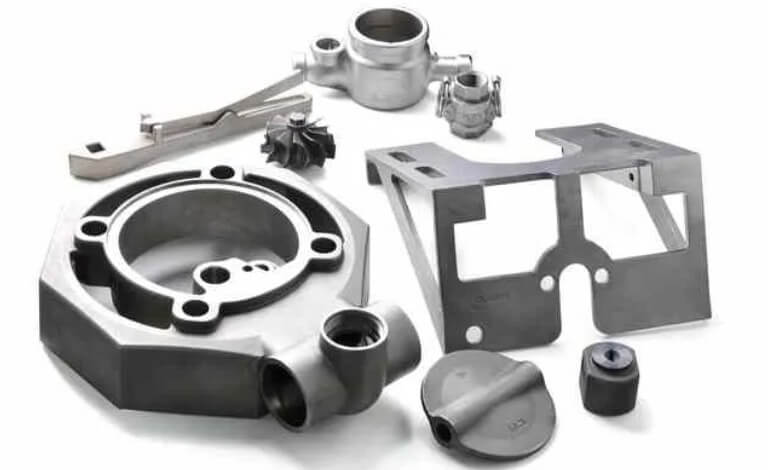
Copper has extremely high thermal conductivity and is suitable for occasions where the cooling rate is extremely high. Graphite has good self-lubricity and corrosion resistance and is suitable for occasions where the surface quality of the casting is high.
(3) Optimization of pouring temperature and speed
Pouring temperature and speed are also crucial to the quench casting process. A higher pouring temperature can ensure the fluidity of the molten metal, but too high a temperature may result in coarse grains. Although lower pouring temperature helps to form a fine grain structure, it may increase the difficulty of pouring. Therefore, it is necessary to optimize the pouring temperature and speed according to the specific materials and requirements to obtain the best casting performance.
6.Related application places of rapid quench casting
(1) Aerospace field
In the aerospace field, this technology is used to manufacture high-performance engine components and structural parts, which need to work in extreme environments and have excellent mechanical properties and corrosion resistance.
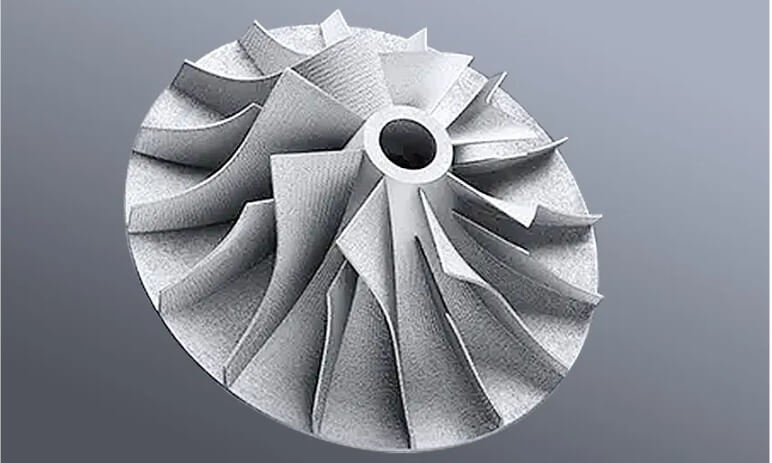
(2) Automobile manufacturing field
In the automobile manufacturing field, this technology is used to manufacture lightweight high-strength parts such as engine cylinders, pistons and connecting rods to improve fuel efficiency and vehicle performance.
(3) Electronic industry field
In the electronics industry, this technology is used to manufacture high-precision and high-reliability electronic components and semiconductor materials.
(4) Medical device field
In the medical device field, this technology is used to manufacture medical devices with high biocompatibility and high wear resistance, such as artificial joints and dental implants.
7.Challenges and solutions
(1) Technical challenges
The main challenges faced by this technology include controlling the cooling rate, preventing cracks in castings, and ensuring the uniformity of castings. Too fast a cooling rate may increase the internal stress of the castings, resulting in cracks. Too slow a cooling rate may lead to coarse grains, affecting the performance of the castings.
In addition, the problem of uneven cooling of the castings may occur during the rapid quench casting process, resulting in large differences in the performance of different parts of the castings.
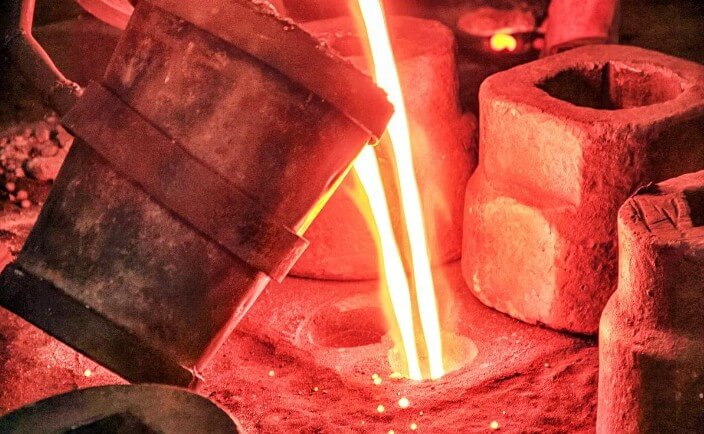
(2) Improvement measures
In order to solve these technical problems, the following improvement measures can be taken:
1) Optimizing cooling medium and casting design:
By selecting appropriate cooling medium and optimizing casting design, the cooling rate can be controlled, the internal stress of the casting can be reduced, and the generation of cracks can be avoided. For example, when using water as the cooling medium, the cooling characteristics of water can be changed by adding certain chemical reagents to improve the cooling effect.
2) Controlling casting process parameters:
By accurately controlling process parameters such as casting temperature, speed and pressure, the uniformity and performance of the castings can be improved. For example, during the pouring process, the pouring speed can be monitored and adjusted in real time to ensure uniform filling and cooling of the molten metal.
3) Use computer simulation technology:
Through computer simulation technology, the flow path and pouring speed of the cooling medium can be optimized to improve the cooling uniformity and performance stability of the casting. For example, by simulating the flow path of different cooling media, the optimal cooling scheme can be selected to improve the cooling effect.
7.Summary
Through the precise control of the above key technologies, rapid quench casting can achieve the regulation of the microstructure of the casting, improve the comprehensive performance of the casting, and meet the needs of different industrial fields.