Lvxun Casting Process Technology
Lvxun has been committed to casting process research and product development for nearly a decade. Lvxun’s process technology department uses its deep process expertise and state-of-the-art laboratory facilities to help customers create the best and highest quality products.
In addition, our experts provide part optimization, technical support and failure analysis to support Lvuxn’s research efforts and operations across the entire business, from casting to finishing processes.
Quality control of lvxun casting
Coordinate measuring machine inspection
High Precision: 3DCMM is a high-precision inspection machine that can measure the dimensions and geometry of a part with high accuracy, ensuring it meets the required tolerances and specifications.
Speed: 3DCMM can measure multiple dimensions of a part simultaneously, making the inspection process faster and more efficient.
Flexibility: Coordinate measuring machines (3DCMM) can measure a wide range of parts, from simple to complex shapes and geometries. This makes it a flexible inspection tool that can be used in a variety of manufacturing applications.
Data-driven analysis: 3DCMM generates a large amount of data during the inspection process, which can be used for data-driven analysis and process improvement.
Consistency: 3DCMM inspection is a consistent and repeatable process, ensuring consistent inspection results across different parts and batches.
Reverse Engineering: 3DCMM can be used for reverse engineering, which is scanning a physical part to create a digital model. This is useful for replicating parts that are no longer in production or creating custom parts.
Optical comparator comparison
High Accuracy: Optical comparators can measure part dimensions and geometry with high accuracy, which is critical to ensuring parts meet required tolerances and specifications.
Speed: Optical comparators can quickly compare inspected parts to reference standards or design specifications, making the inspection process faster and more efficient.
Flexibility: Optical comparators can measure a wide variety of parts, including simple and complex shapes and geometries.
Ease of Use: Optical comparators are easy to use and require minimal training, making them an ideal inspection tool in a manufacturing environment.
Non-Contact Inspection: Optical comparators use a light source and magnifying glass to project an image of the part onto a screen, which means the inspection process does not touch the part being inspected. This is ideal for inspecting delicate parts or parts with sensitive surfaces.
X-ray scanner inspection
Nondestructive Testing: X-ray scanners can perform nondestructive testing on parts and components, allowing manufacturers to identify internal flaws and imperfections without damaging the part.
High Accuracy: X-ray scanners can detect flaws and imperfections with high accuracy, making them an ideal inspection tool for critical parts and components.
Speed: X-ray scanners can quickly scan parts and components, making the inspection process faster and more efficient.
Versatility: X-ray scanners can be used to inspect a wide variety of parts and components, including those with complex shapes and geometries.
Quality Control: X-ray scanners are used to ensure that parts and components meet required standards and specifications, which is important for critical components in industries such as aerospace and medical.
Process Control: X-ray scanners can be used to monitor the manufacturing process and identify any issues that may affect the quality of the produced parts.
Ultrasonic testing machine inspection
Nondestructive Testing: Ultrasonic testing can be used to perform nondestructive testing on parts and components, allowing manufacturers to identify internal defects and flaws without damaging the part.
High Accuracy: Ultrasonic testing machines can detect defects and flaws with high accuracy, making them an ideal testing tool for critical components.
Speed: Ultrasonic testing machines can quickly inspect parts and components, making the inspection process faster and more efficient.
Versatility: Ultrasonic testing machines can be used to inspect a wide variety of parts and components, including those with complex shapes and geometries.
Quality Control: Ultrasonic testing is used to ensure that parts and components meet the required standards and specifications, which is important for critical components in industries such as aerospace and medical.
Process Control: Ultrasonic testing can be used to monitor the manufacturing process and identify any issues that may affect the quality of the produced parts.
Cost-effective: Compared to other testing methods, ultrasonic testing machines are cost-effective, making them an ideal testing tool for manufacturing environments.
Surface roughness tester test
Quality Control: Surface roughness testers are used to ensure that the surface finish of a part meets the required standards and specifications. This is important for parts that come in contact with other surfaces, as surface roughness can affect friction, wear, and corrosion resistance.
Process Control: Surface roughness testers can be used to monitor the surface finish of a part during the manufacturing process, allowing manufacturers to make any necessary adjustments to ensure that the finished part meets the required specifications.
Consistency: Surface roughness testers provide consistent and repeatable measurements, ensuring that the surface finish of parts remains consistent across batches and production runs.
Efficiency: Surface roughness testers are fast and easy to use, making them an ideal inspection tool for manufacturing environments.
Data-driven analysis: The data generated by surface roughness testers can be used for data-driven analysis and process improvement. This can help manufacturers identify areas for improvement in the manufacturing process and make the necessary adjustments to increase efficiency and reduce waste.
Airtightness control of aluminum castings
Tools and processes to ensure pressure tightness
Pressure tightness refers to the ability of a casting to maintain a specified internal pressure for a specified time. Here are some of the tools and processes Lvxun uses to ensure the supply of high integrity castings:
Slurry Simulation: Each new part is simulated before the mold is made. This ensures that potential leak areas are discovered and remedied early in the casting development process, and that the mold is developed using best design practices.
Projection X-ray: Digital/Real-time Radiography (DR), Computed Radiography (CR), and Film Radiography.
Leak Testing: Lvxun offers air decay (also known as pressure decay), mass flow, and underwater testing to ensure that the supplied castings meet the pressure test requirements expected of the casting.
Metal Spectrometers: Lvxun uses optical emission spectrometers (OES) to verify the chemical composition of the alloys we purchase and to verify individual furnaces throughout the manufacturing facility.
In-house Heat Treatment: Improves the mechanical properties of our sand and permanent mold castings.
In-house Machining: Includes part assembly and custom testing.
Liquid Penetrant Testing: For crack detection (also known as dye penetrant testing)
- Surface treatment test
Our quality control team is proficient in a range of specialized testing methods to ensure that the product meets your requirements.
Adhesion tests include cross-cut testing, scratch adhesion testing, pull-off testing, etc.
We use a UV weathering tester to evaluate the weathering resistance of products.
Salt spray testing is a corrosion test used to check the corrosion resistance of materials and surface coatings and to detect coating pretreatment or paint quality issues.
We provide color comparison testing that follows the Pantone color matching system.
We use an alcohol rubber wear tester to help us identify coating problems related to certain chemicals.
We also utilize a range of specialized coating thickness gauges to measure the thickness of anodizing, electroplating, painting and powder coating.
We also use digital ultrasonic flaw detectors to identify casting porosity or other quality issues in various substrates.
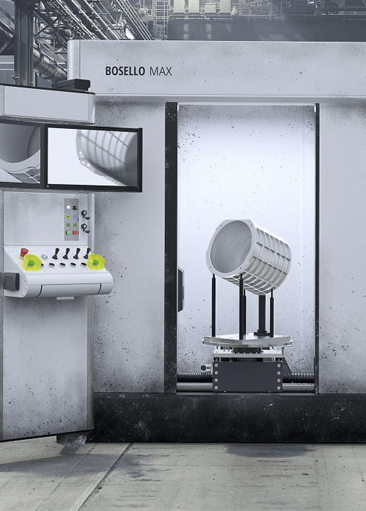
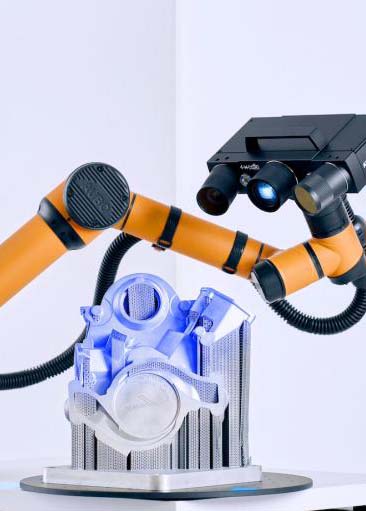
- Research & Technology Center
Lvxun’s product technology department provides engineers and professionals with a wide range of cutting-edge resources, including advanced testing, metallographic analysis, mold flow analysis, metal fatigue testing, blue light scanning, fluorescent penetration, salt spray testing, comprehensive failure analysis and risk control, etc.
Mechanical Testing Facilities
At our Mechanical Testing facilities, we leverage automated equipment for conducting essential tests such as tensile and hardness measurements. These tests play a pivotal role in establishing the mechanical attributes of materials, bolstering product development and aiding customer projects. Our array of testing frames spans from 5 to 220 kip, encompassing both tensile testing and stress- or strain-controlled fatigue testing.
Metallographic analysis
We all know that material composition is critical for cast parts. Our quality control team uses a range of specialized analyses to ensure all materials meet specifications.
We use digital CCD spectrometers to monitor metal composition and ensure material quality.
We also test samples of our products through a battery of chemical tests to verify material composition and identify impurities or contaminants.
Visual Inspection
All cast parts are visually inspected to ensure true quality from start to finish. When it comes to casting quality control, our quality control experts carefully inspect each component to ensure they are fully filled (no cracks, tears, holes, unfilled, etc.), free of twists, bends, or surface defects. Products are also cross-checked against the quality control plan and written process instructions before entering other processes.