Prototype aluminum castings: a key tool from design verification to small batch production
Prototype aluminum castings refer to aluminum samples or models made by casting processes, which are mainly used for design verification, functional testing and small batch production.
In recent years, the application of new technologies such as 3D printing, intelligent manufacturing, and simulation has made the manufacturing process of aluminum castings more efficient and accurate. This article will explore the key technologies, material selection, quality control, and advantages and limitations of prototype aluminum casting manufacturing to help relevant personnel better understand the reasons for making prototypes.
1.Application scenarios of prototype aluminum castings
Prototype aluminum castings are widely used in aerospace, automotive, electronics, machinery and other fields. It plays an important role in all stages of product development in these fields. Its main application scenarios include:
(1) Design verification
In the early stage of product design, prototype aluminum castings are used to verify the feasibility and functionality of the design. Through actual manufacturing and testing, designers can find and correct problems in the design to avoid costly mistakes in large-scale production.
(2) Functional testing
Prototype aluminum castings are also used to test the performance of products in actual environments. For example, in the automotive manufacturing industry, key components such as engine blocks and transmission housings often require functional testing through prototype aluminum castings to ensure their reliability and durability.
(3) Small batch production
For customized products or market testing, prototype aluminum castings provide a cost-effective small batch production solution. Through small batch production, companies can collect user feedback and optimize products before investing in large-scale production.
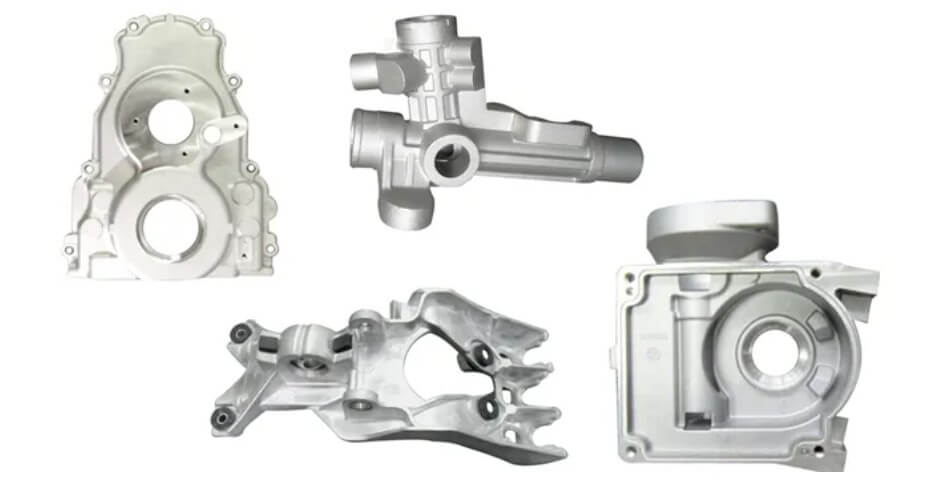
2.What is the most suitable process for casting prototype aluminum castings?
The most suitable process for casting prototype aluminum castings depends on specific needs, including production quantity, part complexity, precision requirements, cost budget, and development cycle. The following are the advantages and disadvantages of several common casting processes and their applicable scenarios to help you choose the most suitable method:
(1) Sand casting
1) Advantages:
Low cost: simple mold making and low material cost.
High flexibility: suitable for single-piece or small batch production, easy to modify the design.
Suitable for large parts: able to cast larger parts.
2) Disadvantages:
Low precision: large casting size tolerance and poor surface finish.
Low production efficiency: suitable for small batch production, not suitable for large-scale manufacturing.
3) Applicable scenarios:
Single-piece or small-batch prototype manufacturing.
Large parts or parts with complex shapes.
Scenarios with low requirements for precision and surface quality.
(2) Investment casting
1) Advantages:
High precision: Able to produce castings with precise dimensions and smooth surfaces.
Complex shapes: Suitable for casting parts with complex geometric shapes.
High material utilization: Almost no waste is generated.
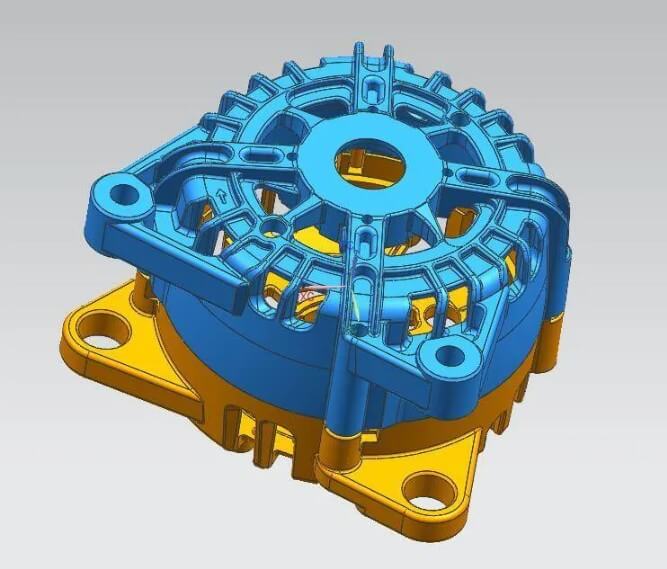
2) Disadvantages:
High cost: The production cost of wax molds and ceramic shells is high.
Long production cycle: There are many process steps and the production cycle is relatively long.
3) Applicable scenarios:
High-precision and complex-shaped parts.
Aerospace, medical devices and other fields with high quality requirements.
Small batch high-precision prototype manufacturing.
(3) Metal mold gravity casting
1) Advantages:
High quality: High casting density and good mechanical properties.
Medium batch production: Suitable for medium-scale production needs.
Good surface quality: The surface finish is higher than that of sand casting.
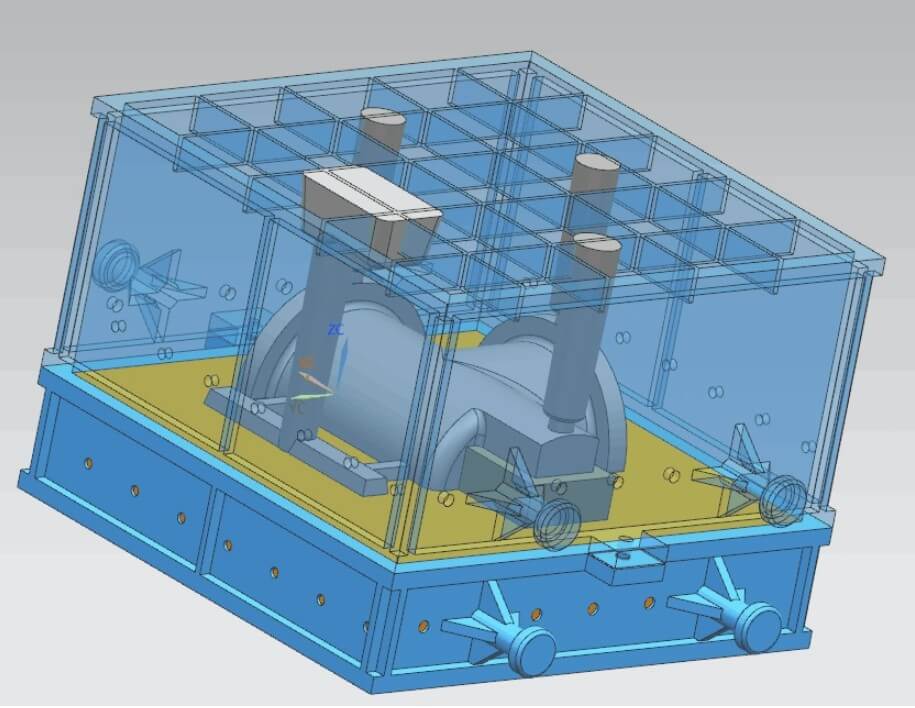
2) Disadvantages:
High mold cost: The production cost of metal molds is high.
Low flexibility: Not suitable for single-piece or small-batch prototype manufacturing.
3) Applicable scenarios:
Medium batch production.
Parts with high mechanical performance requirements.
Parts that require high surface quality.
(4) Die casting (high pressure casting)
1) Advantages:
High precision: Able to produce castings with precise dimensions and smooth surfaces.
High production efficiency: Suitable for large-scale production.
Thin-walled parts: Able to cast thin-walled and complex-shaped parts.
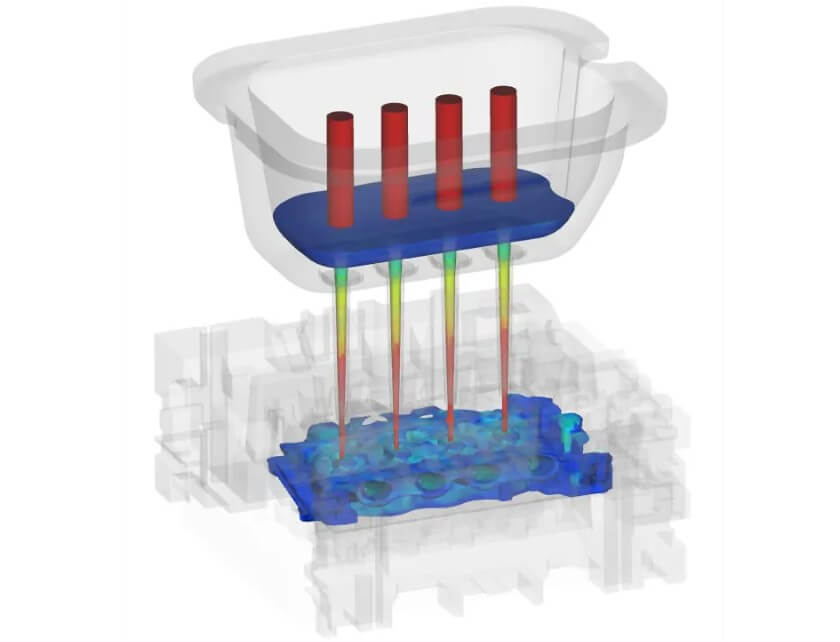
2) Disadvantages:
High mold cost: The production cost of die casting molds is very high.
Not suitable for small batches: Due to the high mold cost, it is not suitable for small-batch prototype manufacturing.
3) Applicable scenarios:
Large-scale production.
Parts with high precision and surface quality requirements.
Thin-walled, complex-shaped parts.
(5) 3D printing + casting process
1) Advantages:
Rapid prototyping: greatly shortens the development cycle and is suitable for rapid prototyping.
High flexibility: can quickly modify the design and is suitable for parts with complex shapes.
Low-cost small batch: suitable for small batch or single-piece production without high mold costs.
2) Disadvantages:
Limited accuracy: 3D printed molds or wax molds may not be as accurate as traditional methods.
Material limitations: The performance of 3D printing materials may affect the quality of the final casting.
3) Applicable scenarios:
Rapid prototyping development.
Small batch or single-piece production.
Parts with complex shapes.
(6) The most suitable process for casting prototype aluminum castings:
If cost, flexibility, accuracy and production cycle are taken into consideration, 3D printing combined with casting process and sand casting are the most suitable processes for prototype aluminum castings:
1) 3D printing combined with casting:
Suitable for rapid prototyping and able to respond quickly to design changes.
No high mold cost is required, suitable for small batch or single piece production.
Capable of processing parts with complex shapes.
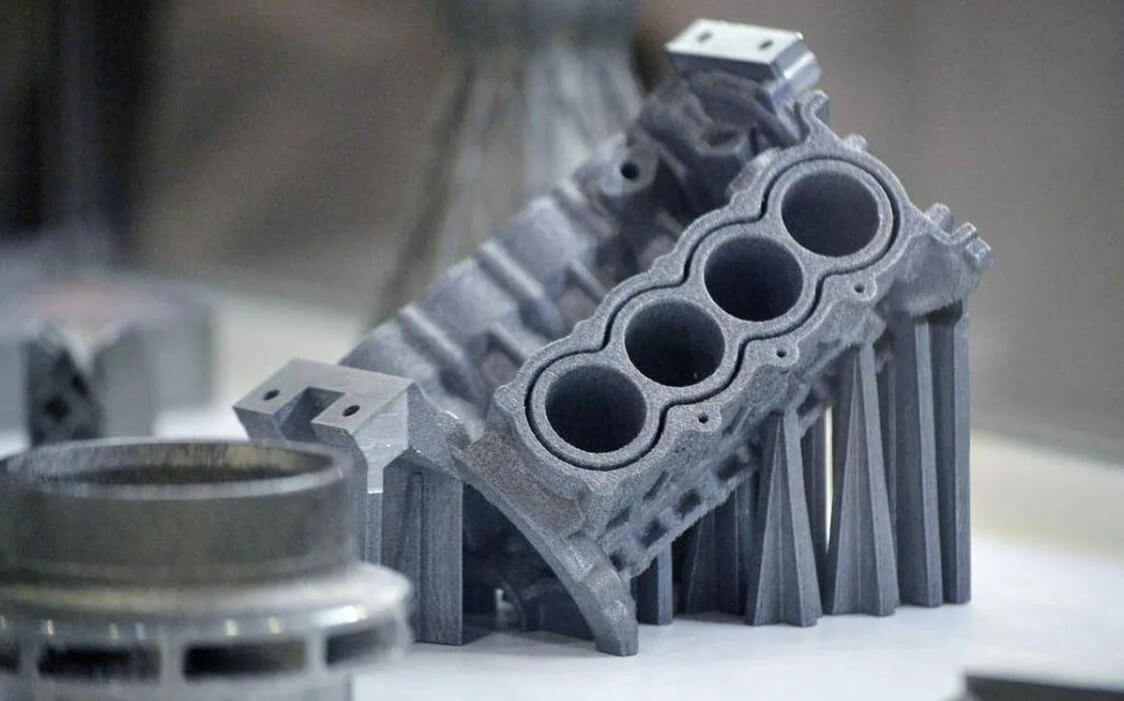
2) Sand casting:
Low cost, suitable for projects with limited budget.
High flexibility, suitable for single piece or small batch production.
Capable of casting large parts.
(7) Summary:
If rapid development and high flexibility are required, choose 3D printing combined with casting.
If the budget is limited and the precision requirements are not high, choose sand casting.
If high precision and complex shapes are required, choose investment casting.
If medium batch production is required and high quality requirements are required, choose metal mold gravity casting.
If large batch production is required and high precision and surface quality requirements are required, choose die casting.
Choosing the most suitable process according to specific needs can maximize the value of prototype aluminum castings and optimize the development process.
3.How to verify whether the prototype aluminum casting meets the requirements?
Verifying whether the prototype aluminum casting meets the requirements is a systematic process that requires comprehensive testing and evaluation from multiple aspects such as design, material, function, and surface quality. The following are detailed verification steps and methods:
(1) Design verification
The purpose of design verification is to ensure that the geometry, size, and structure of the prototype aluminum casting meet the design drawings and functional requirements.
1) Dimension detection
Tools: calipers, micrometers, coordinate measuring machines (CMMs), etc.
Methods: Measure key dimensions (such as wall thickness, hole positions, mounting surfaces, etc.) and compare them with the design drawings.
Focus: Ensure that the dimensions are within the tolerance range, especially for key mating parts.
2) Geometry detection
Tools: 3D scanners or optical measuring equipment.
Methods: Compare the scanned data with the 3D model and analyze the deviation.
Focus: Check whether complex surfaces, angles, and contours meet the design requirements.
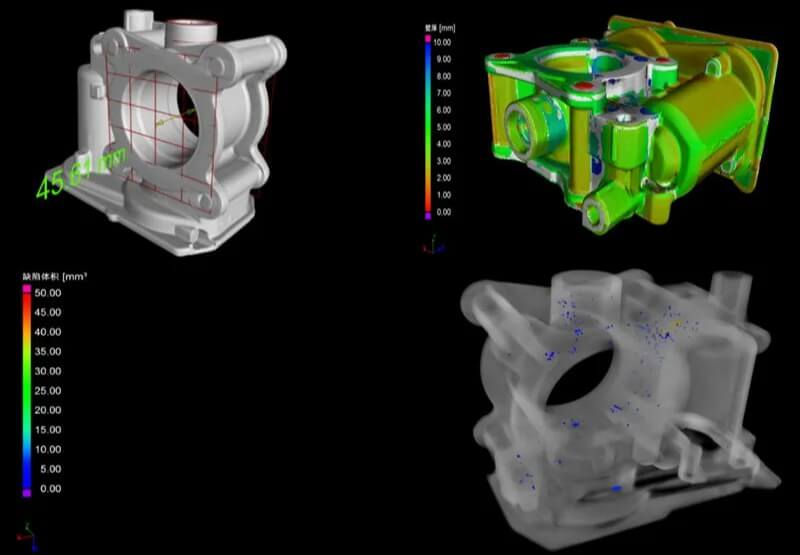
3) Assembly verification
Methods: Assemble the prototype aluminum casting with other components to check whether they match.
Focus: Verify the installation hole position, fit clearance and overall assembly performance.
(2) Material performance test
Material performance test is used to verify whether the material of the prototype aluminum casting meets the design requirements.
1) Chemical composition analysis
Tool: Spectrometer (such as X-ray fluorescence spectrometer).
Method: Detect the chemical composition of the aluminum casting to ensure that the alloy composition meets the standard.
(2) Mechanical property test
Tensile test: Test tensile strength, yield strength and elongation.
Hardness test: Use Brinell hardness tester or Rockwell hardness tester to measure hardness.
Impact test: Test the impact resistance of the material.
3) Metallographic analysis
Tool: Metallographic microscope.
Method: Observe the microstructure of the material and check whether there are defects such as pores, shrinkage, inclusions, etc.
(3) Functional test
Functional test is used to verify the performance of the prototype aluminum casting in the actual use environment.
1) Load test
Method: Apply actual working load to the casting to test its deformation and load-bearing capacity.
Focus: Check for cracks, deformation or failure.
2) Fatigue test
Method: Simulate the cyclic load under actual working conditions to test the fatigue life of the casting.
Focus: Check for fatigue cracks or fractures.
3) Sealing test
Method: Perform air pressure or water pressure test on parts that need to be sealed (such as engine cylinder block).
Focus: Check for leaks.
4) Thermal performance test
Method: Perform thermal cycle test on radiators or parts used in high temperature environments.
Focus: Check thermal deformation and thermal fatigue performance.
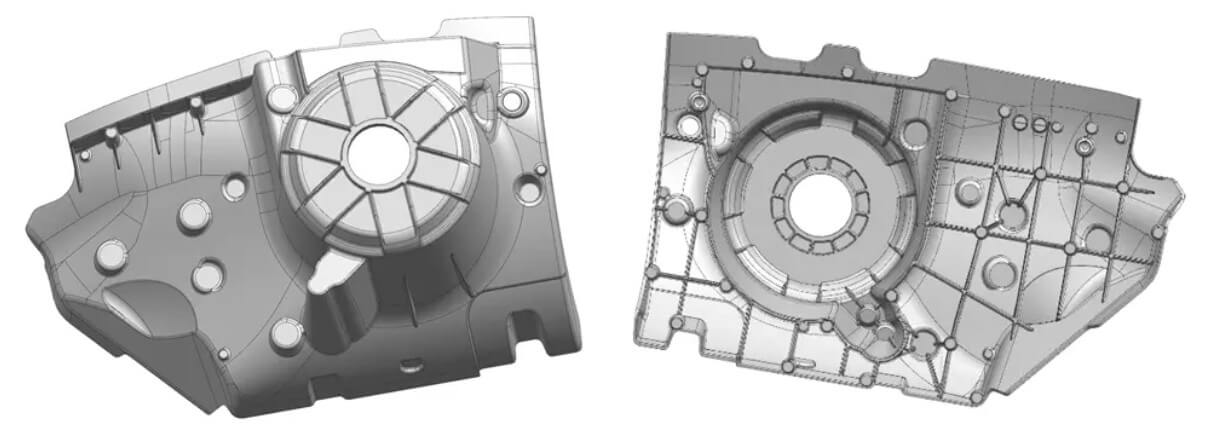
(4) Surface quality inspection
Surface quality inspection is used to verify whether the appearance and surface performance of the casting meet the requirements.
1) Visual inspection
Method: Check the surface for defects such as cracks, pores, shrinkage, etc. with the naked eye or a magnifying glass.
2) Surface roughness inspection
Tool: Surface roughness meter.
Method: Measure the roughness of key surfaces to ensure that they meet the design requirements.
3) Coating or surface treatment inspection
Method: Adhesion and corrosion resistance tests are performed on castings that have been surface treated by anodizing, sandblasting, etc.
(5) Nondestructive testing
Nondestructive testing is used to detect defects inside castings without destroying the parts.
1) X-ray testing
Inspect internal defects such as pores, shrinkage, and cracks through X-ray fluoroscopy.
2) Ultrasonic testing
Use ultrasound to detect internal defects, suitable for thick-walled parts.
3) Penetrant testing
Use penetrant fluid to check surface and near-surface cracks.
4) Magnetic particle testing
Test ferromagnetic materials to detect surface and near-surface defects.
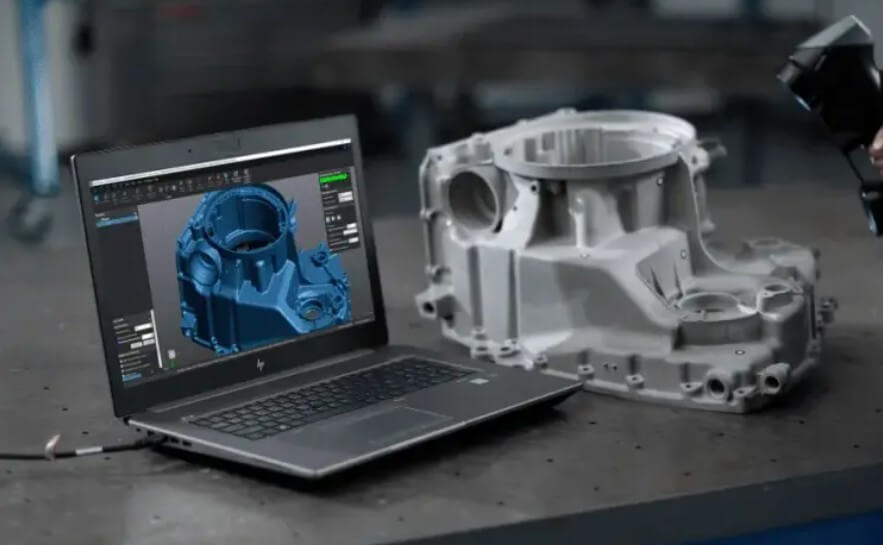
(6) Environmental testing
Environmental testing is used to verify the performance of prototype aluminum castings under specific environmental conditions.
1) Corrosion resistance test
The casting is exposed to corrosive environments such as salt spray and wet heat to test its corrosion resistance.
2) High and low temperature testing
The casting is placed in a high or low temperature environment to test its performance changes.
(7) Data analysis and improvement
Data analysis: Compare the test results with the design standards and analyze the causes of deviations.
Improvement measures: Optimize the design, adjust the process parameters or improve the material selection according to the test results.
4.Summary
Through a series of steps such as design verification, material performance testing, functional testing, surface quality testing, non-destructive testing and environmental testing, it is possible to fully verify whether the prototype aluminum casting meets the requirements. These tests can not only identify potential problems, but also provide data support for subsequent optimization to ensure that the quality and performance of the final product meet the expected goals.