Precision investment casting: high-precision key information you want to know
Precision investment casting is an advanced metal forming technology. With its advantages of high precision, high complexity and low cost, it is widely used in aerospace, automotive, medical and other fields. This article will explore in depth the advantages, key technologies, methods to improve dimensional accuracy, applicable materials and application examples of precision investment casting.
1.Are precision investment casting and investment casting the same?
Precision investment casting and investment casting are essentially the same process. Both use fusible materials (such as wax) to make a model, and then coat the model with refractory materials to form a shell. After melting the model, a hollow refractory shell is obtained, and finally molten metal is poured to obtain the casting. However, precision investment casting emphasizes the precision and surface quality of the casting, so the process control and material selection may be more stringent to ensure the high precision and low surface roughness of the casting.
The following are the differences in process characteristics between precision investment casting and investment casting:
(1) The characteristics of investment casting include:
1) High casting precision and good surface quality, dimensional accuracy is usually between IT11-IT14, and surface roughness is Ra25-3.2 microns.
2) Suitable for casting thin-walled castings with complex shapes.
3) Can be used for various alloy castings.
4) Production batch is not limited.
(2) In addition to the above characteristics, precision investment casting also emphasizes the following points:
1) The casting dimensional accuracy and surface finish are higher, which can reduce the amount of mechanical processing, and some castings can even be used only after grinding and polishing.
2) It can cast complex castings of various alloys, especially high-temperature alloy castings.
3) It is suitable for the production of small parts with complex shapes and high precision requirements, such as turbine engine blades.
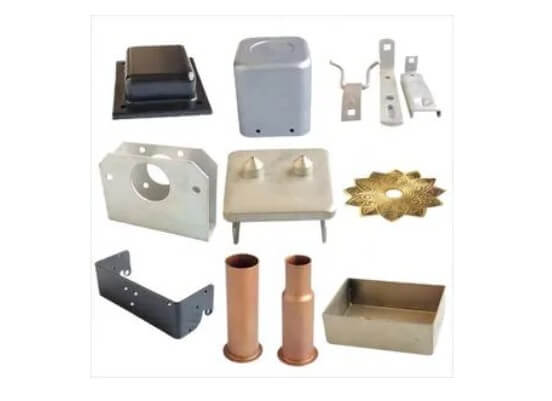
Summary:
From these characteristics, it can be seen that precision investment casting is an advanced form of investment casting. It achieves higher casting accuracy and surface quality through more precise process control and higher quality materials. Therefore, precision investment casting is usually used in occasions with particularly high requirements on casting size and surface finish.
2.Key technologies of precision investment casting
Precision investment casting is an advanced process technology that can produce high-precision, complex-shaped castings. Its key technologies mainly include the following aspects:
(1) Wax pattern manufacturing technology:
The wax pattern is the basis of investment casting, and its dimensional accuracy and surface quality directly affect the quality of the final casting. Modern wax pattern manufacturing technology uses high-precision wax presses and high-quality mold materials to ensure the accuracy and stability of the wax pattern.
(2) Shell preparation technology:
The shell is a complex structure composed of multiple layers of refractory materials and binders. Its preparation process includes multiple steps such as coating, sanding, drying and hardening. The quality of the shell is directly related to the dimensional accuracy and surface roughness of the casting.
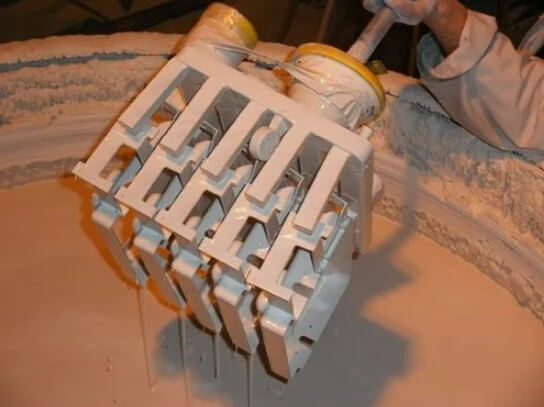
(3) Dewaxing and roasting technology:
Dewaxing is the process of melting the wax pattern from the shell, and roasting is to remove moisture and volatile substances in the shell and improve the strength and permeability of the shell. These two processes are crucial to the quality control of castings.
(4) Pouring and cooling technology:
Pouring is the process of injecting molten metal into the mold shell, while cooling is the process of solidification and solidification of the casting. Reasonable pouring temperature and speed, as well as optimized cooling conditions, can reduce defects in castings and improve their mechanical properties and dimensional stability.
(5) Computer-aided design and manufacturing (CAD/CAM) technology:
Modern precision investment casting widely uses CAD/CAM technology for casting design and mold manufacturing, which improves design efficiency and manufacturing accuracy.
(6) Numerical simulation technology:
By computer simulation of metal flow and solidification behavior during the pouring process, possible defects can be predicted, process parameters can be optimized, and casting quality can be improved.
(7) Rapid prototyping technology:
For example, 3D printing technology can quickly produce wax molds or mold shell prototypes, shortening the product development cycle.
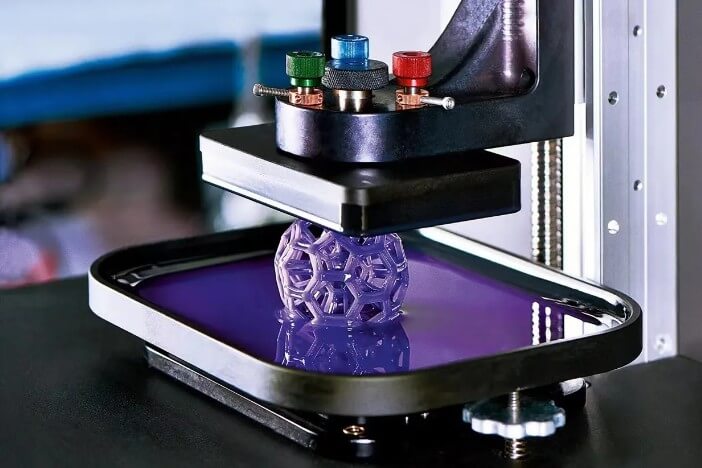
(8) Green intelligent production line technology:
Integrate green manufacturing technologies such as flue gas waste heat recovery refrigeration and sewage deep purification treatment to realize the intelligent and green production process and improve production efficiency and product quality.
3.How to control and improve the dimensional accuracy of castings in precision investment casting?
Precision investment casting is a high-precision metal forming process. By accurately controlling each link, the dimensional accuracy of castings can be significantly improved. The following are some key methods to control and improve the dimensional accuracy of castings:
(1) Control the pouring temperature
The pouring temperature has a significant impact on the dimensional accuracy of castings. Too high a pouring temperature will increase the shrinkage of the molten metal, thereby affecting the dimensional accuracy of the casting. Therefore, the appropriate pouring temperature range should be selected according to the characteristics of different alloys and strictly controlled during the production process.
(2) Optimize the design of casting structure
Factors such as the wall thickness and shape complexity of the casting will affect its dimensional accuracy. In the design stage, the characteristics of the casting process should be fully considered, and the casting structure should be reasonably designed to avoid structures with large wall thickness differences and sharp corners that are prone to stress concentration. At the same time, the deformation of the casting is predicted through simulation analysis software to optimize the design scheme.
(3) Select high-performance materials
The selection of shell materials and mold materials is crucial to the dimensional accuracy of castings. High-performance shell materials have low thermal expansion coefficients and high strength, which can reduce the deformation of the shell during heating and cooling. In addition, selecting mold materials with stable linear shrinkage and strictly controlling the mold material ratio and process parameters can help improve the dimensional stability of the wax mold.
(4) Improving mold and shell making processes
Mold and shell making processes have a direct impact on the dimensional accuracy of castings. Use high-precision press molds to ensure the surface finish and dimensional accuracy of the wax mold. During the shell making process, strictly control the coating ratio, coating times and drying conditions to improve the quality and dimensional stability of the shell.
(5) Applying mathematical statistics methods
By collecting the dimensional data of the wax mold and casting, mathematical statistics methods (such as CPK analysis) are used to evaluate the stability of the process and the dimensional accuracy of the casting. According to the analysis results, adjust the mold and process parameters to achieve purposeful control of the casting size and improve dimensional accuracy and consistency.
(6) Strengthen process control
During the production process, strengthen the detection and control of key process parameters, such as wax injection temperature, pressure, and roasting temperature. Establish a strict quality control system, implement full-process quality monitoring, timely detect and correct deviations, and ensure the stable improvement of casting dimensional accuracy.
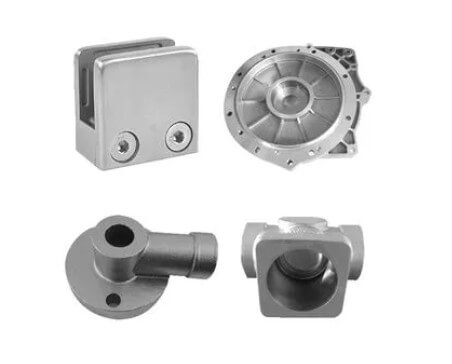
4.Which materials are most suitable for precision investment casting?
Materials suitable for precision investment casting include but are not limited to the following:
(1) Carbon steel:
It has good strength and toughness and is suitable for manufacturing various mechanical parts.
(2) Alloy steel:
By adding alloying elements to improve the performance of steel, such as improving strength and heat resistance, it is suitable for applications in special environments.
(3) Heat-resistant alloy:
It can maintain performance in high temperature environments and is suitable for the manufacture of high-temperature components such as aircraft engines.
(4) Stainless steel:
It has excellent corrosion resistance and is suitable for applications in corrosive environments such as chemical and marine environments.
(5) Precision alloy:
It has specific physical properties, such as high magnetism and high elasticity, and is suitable for precision instruments and electronic equipment.
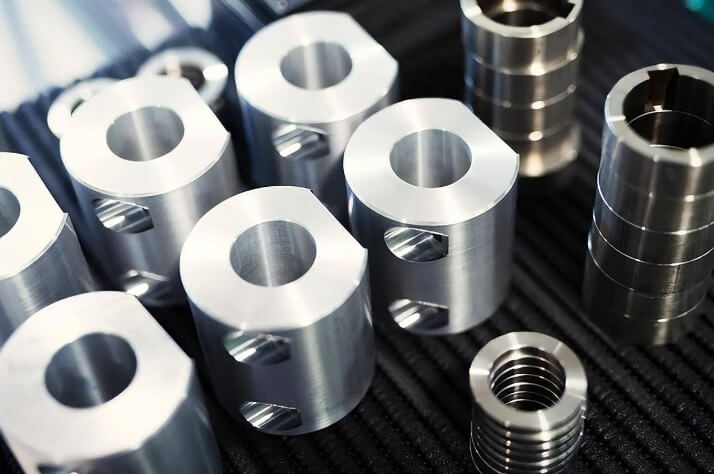
(6) Permanent magnet alloy:
It has high magnetic properties and is suitable for manufacturing permanent magnets.
(7) Bearing alloy:
It has high wear resistance and good lubrication properties and is suitable for manufacturing friction parts such as bearings.
(8) Copper alloy:
Good thermal conductivity and corrosion resistance, suitable for manufacturing heat exchangers and conductive parts.
(9) Aluminum alloy:
Low density, good thermal conductivity, suitable for weight reduction and applications requiring good heat dissipation.
(10) Titanium alloy:
High strength-to-weight ratio and excellent corrosion resistance, suitable for aerospace and high-performance automotive applications.
(11) Magnesium alloy:
Extremely light, good shock absorption, suitable for automobiles and other vehicles.
(12) Cobalt-based alloy:
Extremely high heat resistance and wear resistance, suitable for applications in high temperature and high wear environments.
Summary:
When selecting materials for precision investment casting, it is necessary to consider the performance requirements of the casting, the application environment, the cost, and the adaptability of the casting process. For example, for applications requiring high strength and high temperature resistance, heat-resistant alloys or cobalt-based alloys may be selected; while for applications requiring weight reduction, aluminum alloys or magnesium alloys may be selected. At the same time, the casting properties of the material, such as fluidity and shrinkage, are also important factors to consider when selecting materials.
5.Examples of industry applications of precision investment casting
(1) Aviation industry:
Precision investment casting is widely used in the aviation industry, mainly for manufacturing complex parts such as engine blades, impellers, and nozzles. These parts are usually made of high-temperature resistant alloys, have complex shapes, high dimensional accuracy requirements, and are difficult to machine. Through precision investment casting, high-precision and high-surface quality production can be achieved to meet the high performance requirements of aircraft engines.
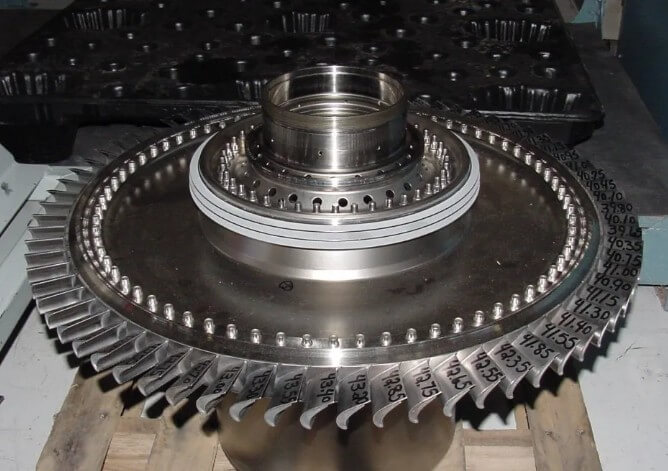
(2) Automobile industry:
In the automobile industry, precision investment casting is used to produce key components such as engine exhaust manifolds and turbocharger impellers. These components require good air tightness and high temperature resistance. Precision investment casting can meet these requirements while reducing the amount of machining and improving production efficiency.
(3) Medical devices:
In the field of medical devices, precision investment casting is used to manufacture precision parts such as surgical instruments, prostheses, and joint replacements. These parts have extremely high requirements for dimensional accuracy and surface finish. Precision investment casting can achieve high-precision replication of complex shapes to meet the strict requirements of medical devices.
(4) Tool manufacturing:
Precision investment casting is used to manufacture various cutting tools, such as drills, milling cutters, etc. These tools require high hardness, high wear resistance and complex geometric shapes. Precision investment casting can meet these requirements and improve the service life and cutting performance of the tools.
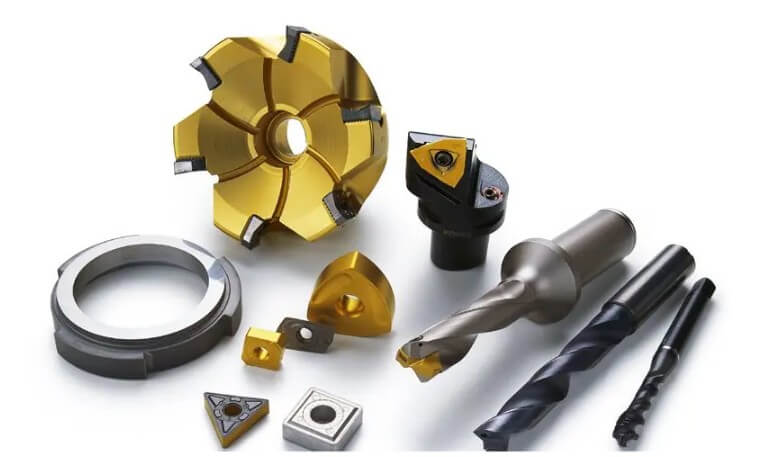
(5) Arts and crafts:
In the field of art, precision investment casting is used to make various metal artworks, sculptures, etc. Taking advantage of the easy engraving characteristics of wax materials, artworks with complex patterns and fine structures can be produced, and then replicated into metal products through precision investment casting.
6.Summary
Precision investment casting is a metal forming process that can achieve high precision. The dimensional accuracy of this process is controlled at a high level and can meet the manufacturing requirements of most precision parts.