Precision cast components: the key to shaping the future
Precision cast components play a vital role in modern industry. With the continuous progress of science and technology, the precision and performance requirements for components are becoming higher and higher, and precision casting technology has emerged. It is capable of producing complex parts with precise dimensions and smooth surfaces through accurate mold design and advanced material processing, and is widely used in aviation, automotive, medical and other fields. In this paper, we will introduce in detail the knowledge of precision casting and the advantages of precision cast components, new materials, new processes, factors affecting precision, application areas.
1. Overview of precision casting technology
(1) definition and principle
Precision casting is a casting process that can produce high-precision castings, which includes a variety of different casting methods, such as investment casting, ceramic casting, metal casting, pressure casting and disappearing mold casting. These methods have their own characteristics, but the common goal is to improve the dimensional accuracy and surface finish of castings, reduce the subsequent processing workload, and even realize the near-net shape.
(2) the difference between precision casting and ordinary casting
Compared with the traditional sand casting, precision cast components in the dimensional accuracy and surface finish has been significantly improved. Sand casting, although lower cost, but the casting accuracy and surface quality is poor, usually requires a lot of follow-up processing. In contrast, precision casting, through the use of high-temperature-resistant ceramic shells and precise wax molds, is able to produce complex parts with precise dimensions and smooth surfaces, which are widely used in aerospace, high-end automobiles, medical devices and other fields.
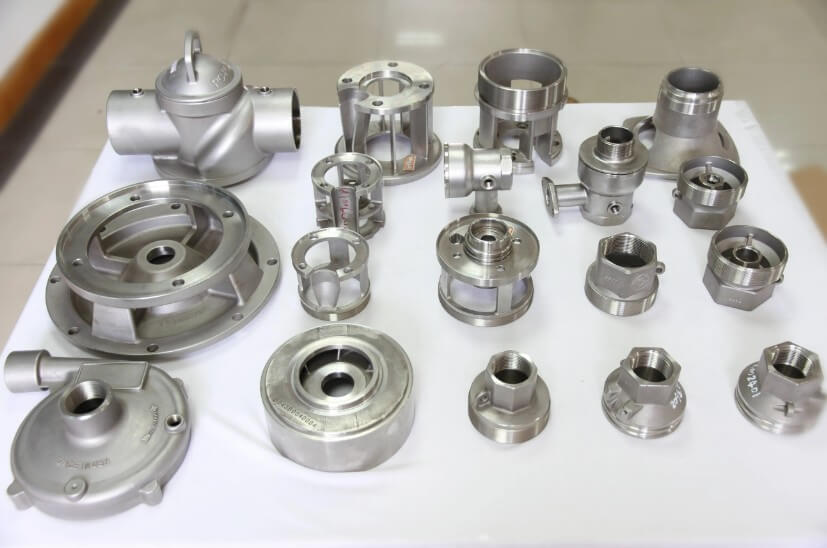
2.Different classifications of investment casting
Precision casting is a kind of metal molding process that can obtain high-precision castings, according to different process characteristics and scope of application, precision casting can be divided into the following main types:
(1) investment casting:
Also known as lost wax casting, it is an ancient method of precision casting. It is made by using wax material to make a model, and then coating the model with multiple layers of refractory material to form a type shell. Afterwards, the wax mold is melted out to form a cavity, and finally the liquid metal is poured in to solidify the casting. Investment casting is suitable for the production of complex shape, high precision requirements of precision cast components.
(2) Ceramic casting:
This method uses ceramic slurry made of casting, usually used in the production of large thick-walled precision castings and molds. Ceramic casting can achieve high dimensional accuracy and surface finish, suitable for single-piece small batch production.
(3) metal casting:
Metal casting using metal molds for casting, compared with sand casting, it has a higher dimensional accuracy and surface quality. Metal casting is suitable for mass production of high-precision requirements of parts.
(4) pressure casting:
Pressure casting is the use of high pressure will be molten metal quickly pressed into the mold cavity, and under pressure solidification molding casting method. The technology has high productivity, high precision, good surface quality and other advantages, suitable for the production of complex shapes, thin-walled, high-strength, high-precision castings.
(5) disappearing mold casting:
This method uses a foam model, the model burns away in the pouring process, forming castings. Vanishing mold casting is suitable for the production of complex shape castings, especially for the production of large castings.
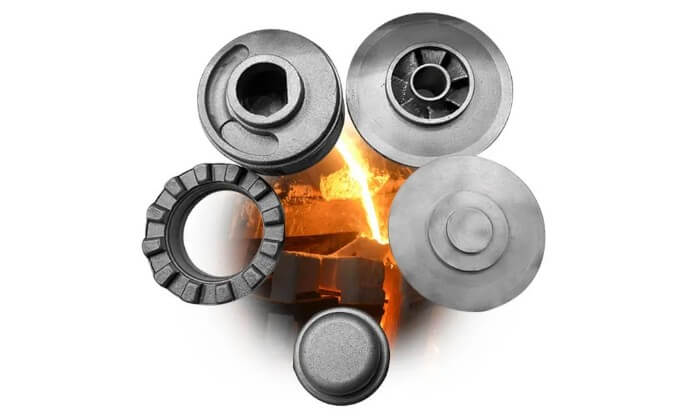
3.Advantages of precision cast components over ordinary castings
Precision cast components compared to ordinary castings have the following advantages:
(1) high dimensional accuracy:
Precision cast components can achieve higher dimensional accuracy, linear tolerance is generally up to 1%, angular tolerance of ± 1/2 degree, surface finish up to Ra 1.6-3.2, which greatly reduces the subsequent machining workload, saving materials and processing costs.
(2) High shape complexity:
Precision casting technology can produce castings with complex shapes, and can even cast multiple parts into one, eliminating the need for combining or welding work and improving production efficiency.
(3) good surface quality:
Precision cast components with higher surface finish, can be cast on the surface of the product fine text or LOGO pattern, improve the product image and added value.
(4) wide range of material properties:
Precision casting of a wide range of material properties, heat-resistant, wear-resistant, corrosion-resistant, hardness up to HRC15-60, to meet the needs of a variety of working conditions.
(5) flexible production batch:
Precision casting technology can be flexibly adapted from small batch to mass production, high efficiency, good repeatability, low cost of molds, less initial investment in product development.
(6) reduce casting defects:
Precision casting process can provide more reliable process control, scrap rate is much lower than sand casting, improve product quality and productivity.
(7) wide range of sizes:
Precision cast components are available in large and small castings, as well as complex micro-parts. Also can cast 30g or smaller parts, can also cast large parts weighing up to 50kg.
(8) Wide range of applications:
Precision cast components can be used in a variety of industries such as aerospace, power generation, firearms, automotive, military, commercial, food service, gas and oil, and energy industries.
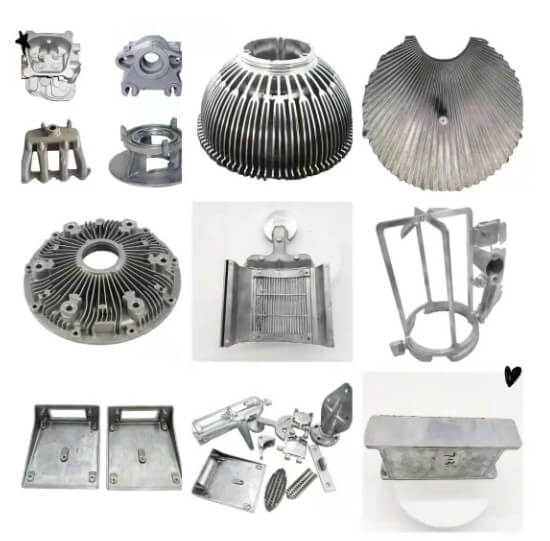
4. The most suitable for the production of precision cast components of the new material
As technology advances, investment casting technology continues to evolve. The application of new materials, such as high-temperature alloys and ceramic matrix composites, enables precision cast components to work in more extreme environments to meet the needs of high-end equipment manufacturing. There are also some common materials that are widely used in the precision casting industry, such as titanium alloys and aluminum alloys. The following are some of the materials used in production:
(1) High temperature alloys:
These materials have excellent high-temperature strength and creep resistance, and are suitable for the manufacture of high-temperature components such as aircraft engines and gas turbines. Commonly, there are nickel-based high-temperature alloys, cobalt-based high-temperature alloys and iron-based high-temperature alloys.
(2) ceramic materials:
Ceramic materials have high hardness, high temperature resistance and good chemical stability, suitable for the manufacture of high temperature and corrosive environment parts, such as crucibles, furnace linings and so on.
(3) Composite materials:
Composite materials combine the advantages of a variety of materials, such as carbon fiber reinforced plastic (CFRP), with high specific strength and high specific modulus, suitable for manufacturing high-performance structural parts.
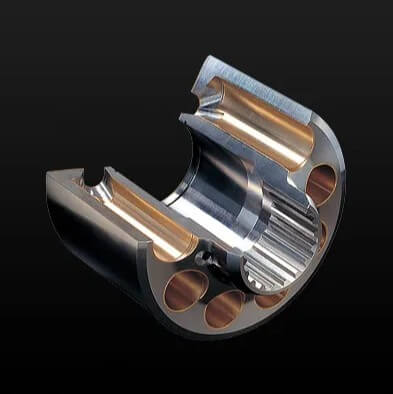
(4) Titanium Alloys:
With high specific strength, good corrosion resistance and biocompatibility, titanium alloys are widely used in aerospace, medical and chemical industries.
(5) Aluminum Alloy:
Aluminum alloy has light weight, high strength and good thermal conductivity, suitable for the manufacture of automotive and aerospace parts and other precision cast components.
(6) Magnesium alloy:
Magnesium alloy is a lightweight metal with high specific strength and good shock absorption, suitable for the manufacture of automobiles and electronic products such as shells.
(7) Stainless steel:
Stainless steel has excellent corrosion resistance and mechanical properties, suitable for the manufacture of medical equipment, chemical equipment and food processing equipment, etc..
5. What are the new processes belonging to the precision cast components
Precision cast components of the new technology in the continuous promotion of the development of the manufacturing industry, the following are four important new technology:
(1) vacuum dewaxing technology:
By introducing a negative pressure environment in the dewaxing process, the rate of wax or plastic drainage is accelerated, thus improving the dimensional accuracy and surface quality of the precision cast components.
(2) Low temperature solid state dewaxing technology:
At a lower temperature, the wax mold or plastic mold into solid powder, and then through the gas blowing or other ways to discharge it, to avoid the thermal expansion of the high temperature melting process, and further improve the dimensional accuracy of precision cast components.
(3) light-curing rapid prototyping technology:
An emerging precision casting technology, the use of laser or ultraviolet light will be cured layer by layer of liquid resin, the formation of three-dimensional solid model, to achieve rapid and accurate manufacturing.
(4) Vacuum sealing molding:
Mainly used in the production of gasoline engine cylinder block, cylinder head and railroad locomotive parts, etc., is a new physical modeling method, the basic principle is in the special sand box, filled with dry quartz sand without water and binder, with plastic film will be sealed after the sand box into a vacuum, with the help of casting inside and outside of the pressure difference between the sand to tighten and shape.
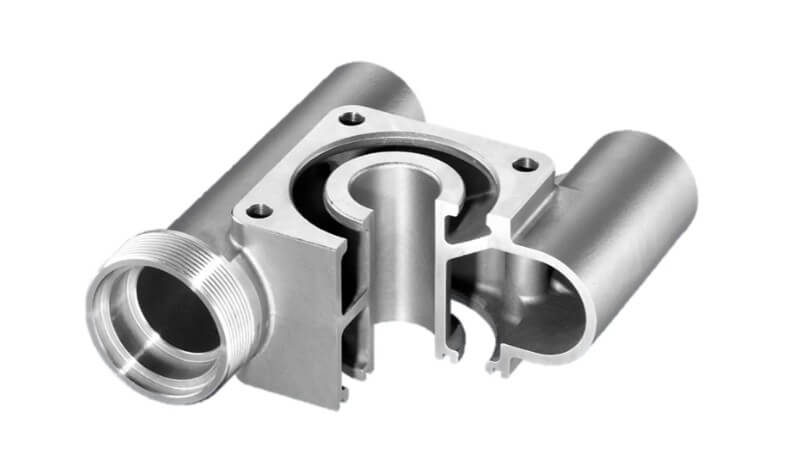
6. Factors affecting the dimensional accuracy of precision cast components
Precision casting is a technology widely used in the manufacture of high-precision metal parts, but in the production process, many factors will affect the dimensional accuracy of the final precision cast components. The following are a few of the main influencing factors:
(1) casting structure:
The wall thickness of the casting will affect its shrinkage. Typically, the greater the wall thickness of the casting shrinkage is also greater, and vice versa.
The geometry and complexity of the casting will also affect its dimensional accuracy, complex shapes may lead to uneven cooling and shrinkage.
(2) casting material:
The level of carbon content in the material will affect the line shrinkage. Generally speaking, the higher the carbon content, the smaller the line shrinkage.
Different alloy materials have different shrinkage rates, which directly affects the final size of the casting.
(3) Mold making process:
The wax injection temperature, wax injection pressure and holding time all affect the size of the wax mold, among which the wax injection temperature has the most significant effect.
Wax molds shrink further during storage and usually stabilize in size after 12 hours of storage.
(4) Roasting and pouring temperature:
The expansion coefficient of the type shell in the roasting process is small, which has little effect on the dimensional accuracy.
The higher the pouring temperature, the greater the shrinkage of the casting, so it is necessary to properly control the pouring temperature to ensure dimensional accuracy.
(5) Mold precision and equipment precision:
The dimensional accuracy of the mold and the degree of wear and tear directly affect the dimensional accuracy of the castings.
Precision casting equipment precision and rigidity is also a key factor in ensuring the dimensional accuracy of castings.
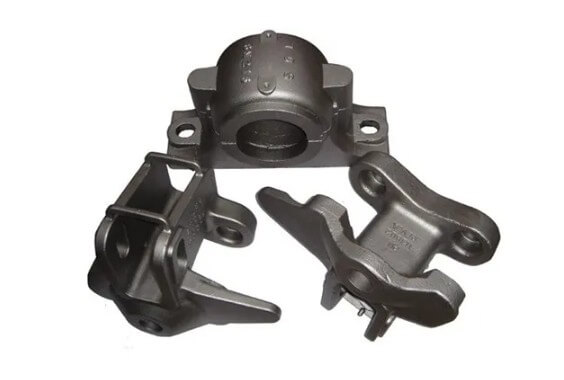
Summary:
Through in-depth understanding and strict control of these influencing factors, manufacturers can significantly improve the dimensional accuracy of precision cast components to meet the needs of high-end manufacturing.
7. Application places of precision cast components
Precision cast components have a wide range of applications in many industries due to their high precision, complex shapes and good surface finish. The following are some of the main application places:
(1) aerospace field:
Precision cast components play an important role in aircraft engines and flight control systems, and can work stably under high temperature, high pressure and severe aerodynamic conditions to ensure the performance and safety of aircraft.
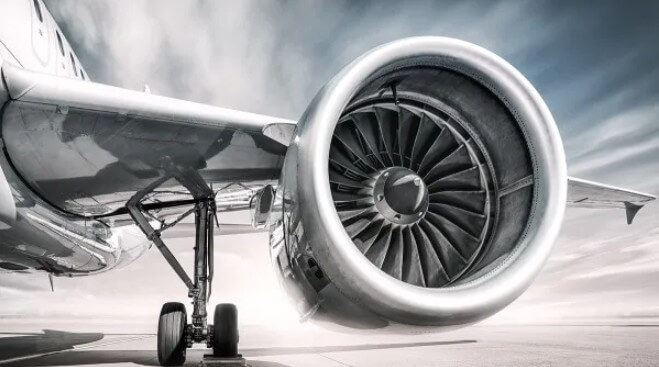
(2) automotive manufacturing:
In automotive engines, transmissions and chassis systems and other key components, precision cast components to provide highly accurate dimensions and complex internal structure, to meet the requirements of automotive performance, while reducing the number of parts and weight, to improve the fuel economy of the vehicle and driving comfort.
(3) Energy field:
Precision cast components are used in the oil and gas industry, nuclear energy industry, solar energy industry and wind energy industry, such as high-pressure valves, pump bodies, flanges, reactor pressure vessels, fuel rod casing, solar cell sheets, key components of wind turbines, etc.
(4) Medical equipment industry:
Precision cast components are used in the manufacture of medical devices such as artificial bones, artificial joints and dental implants, to meet the requirements of these devices for size and material properties, to achieve personalization and provide better treatment results and patient experience.
(5) Heavy Machinery:
The application of precision casting technology in heavy-duty components, such as large cast steel parts, is used to manufacture mining machinery, construction machinery and other key components to meet the requirements of high strength and high durability.
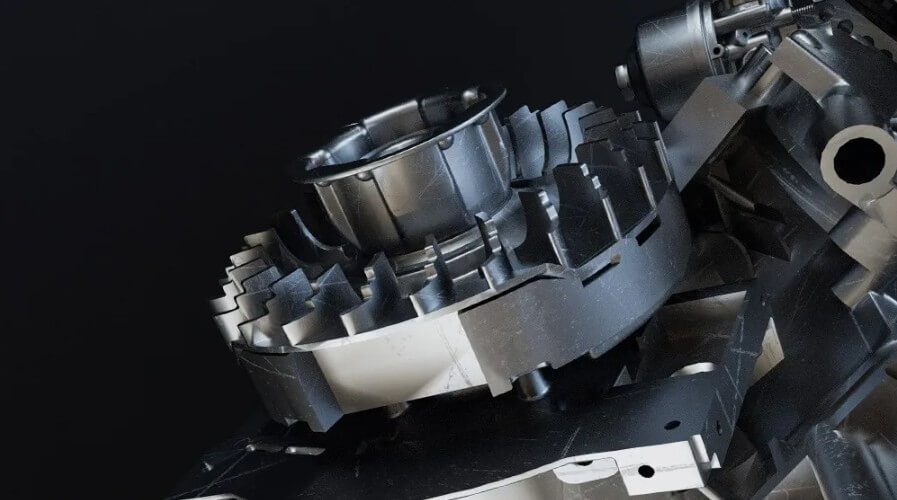
(6) cultural arts:
In the production of bronzes and other cultural artifacts, precision casting technology such as lost wax method and split casting method is used to cast complex and exquisite works of art.
8. Summary
The application of precision cast components is not only limited to the above fields, but also includes textile machinery, locks, ship hardware, high-speed rail hardware, lighting hardware, furniture hardware, etc. With its high precision and quality assurance, it is widely used in various industrial fields.