Plumbing component precision machined parts: a comprehensive analysis of materials, processes and applications
In modern industry, plumbing component precision machined parts play a vital role. Whether in the fields of oil and gas, aerospace, automobile manufacturing, or energy and chemical industry, the performance of the pipeline system directly affects the reliability, safety and efficiency of the equipment.
Precision machining technology is the key to ensuring the high-quality production of pipeline components, while material selection and process optimization are the core links of precision machining. This article will deeply explore the key technologies and development trends of plumbing component precision machined parts from the aspects of material properties, machining technology, and application fields.
1.Common materials and characteristics of plumbing component precision machined parts
The material selection of plumbing component precision machined parts directly affects their performance and service life. The following are several common materials and their characteristics:
(1) Carbon steel
●High strength and good pressure resistance, suitable for general industrial pipelines.
●Mainly used in the fields of oil, natural gas, building water supply, etc.
(2) Stainless steel
●With excellent corrosion resistance, it has become one of the most commonly used materials for plumbing component precision machined parts
●Applicable to chemical, food, pharmaceutical and other industries
●Can be used in high temperature, high pressure, corrosive fluid environments, such as acid and alkali pipelines, steam pipelines, etc.
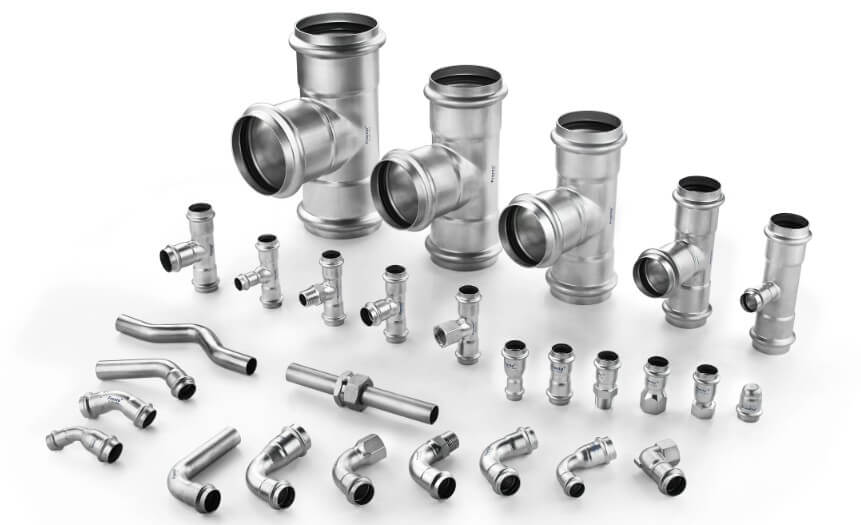
(3) Alloy steel
●By adding elements such as chromium, nickel, and molybdenum, the wear resistance, heat resistance, and corrosion resistance are improved.
●Mainly used for high temperature and high pressure pipelines, such as boiler tubes, power equipment pipelines, etc.
(4) Titanium alloy
●Light weight, high strength, and resistant to strong acid and alkali corrosion.
●Suitable for high-end fields such as marine engineering, chemical industry, aerospace, etc.
(5) Aluminum alloy
●Light weight, with good corrosion resistance and thermal conductivity.
●Mainly used for low-pressure fluid transportation, aerospace, and equipment with lightweight requirements.
(6) Copper and copper alloy materials
●Have excellent thermal conductivity and seawater corrosion resistance.
●Suitable for heat exchange equipment, marine pipelines, refrigeration systems, etc.
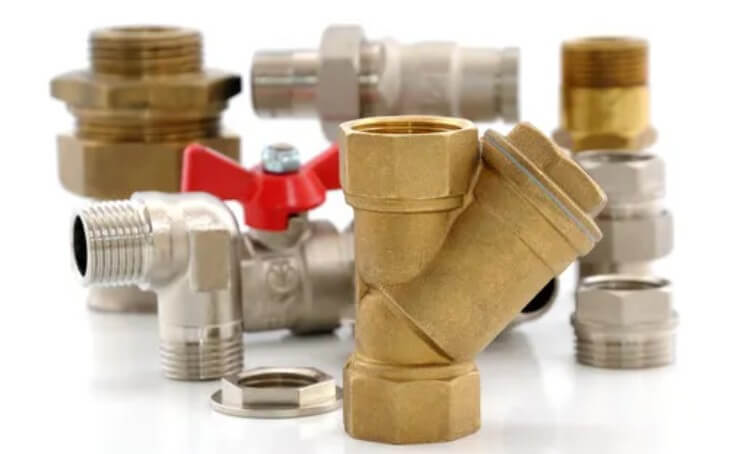
2.Key factors in material selection for plumbing component precision machined parts
In the manufacturing process of plumbing component precision machined parts, the following key factors need to be considered in material selection:
(1) Corrosion resistance
Pipeline systems are often exposed to corrosive media, so the corrosion resistance of materials is the primary consideration. For example, in chemical equipment, stainless steel and titanium alloys are widely used due to their excellent corrosion resistance.
(2) Strength and toughness
Pipeline components need to withstand high pressure, high temperature or mechanical impact, so the material must have sufficient strength and toughness. For example, titanium alloys are usually used for pipeline components in the aerospace field to meet performance requirements in extreme environments.
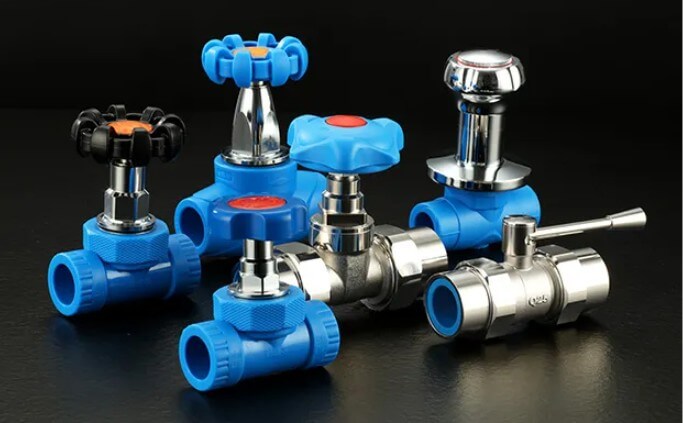
(3) Processing difficulty
The processing properties of different materials vary greatly. Choosing materials that are easy to process can reduce production costs and improve processing efficiency. For example, aluminum alloys are often used for precision machining of complex-shaped pipeline components due to their good cutting performance.
3.Technical overview of plumbing component precision machined parts
(1) CNC turning and milling technology
CNC machine tools are the core equipment for plumbing component precision machined parts, mainly used for machining flanges, elbows, joints, valve bodies and other parts.
1) CNC turning:
Applicable to processing cylindrical or rotationally symmetrical parts, such as pipe joints, threaded connectors, etc. High-precision CNC lathes can achieve multi-axis linkage, reduce errors and improve processing efficiency.
2) CNC milling:
Mainly used for asymmetric or multi-angle pipeline components, such as fluid distribution blocks and special-shaped joints. Five-axis CNC milling machines can complete complex surface processing in one clamping, improving part consistency.
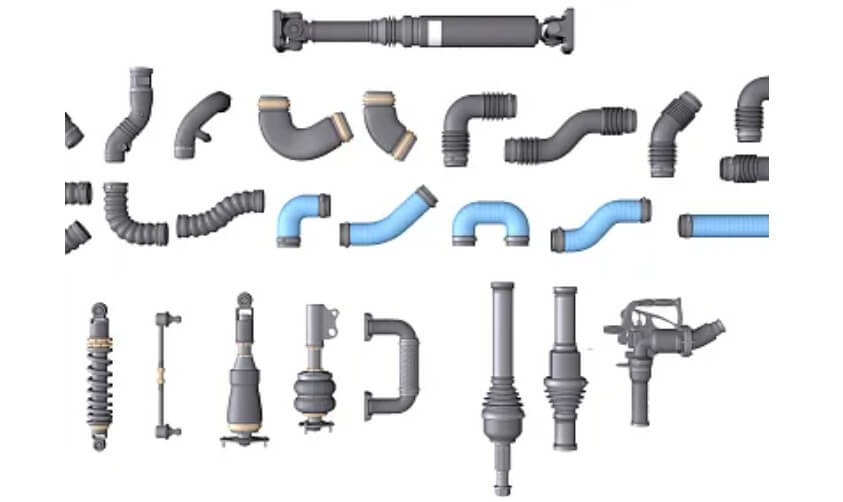
3) Key technical points:
●Tool path optimization, reduce processing vibration, and improve finish.
●Adopt high-precision servo drive system to improve positioning accuracy.
●Combined with CAD/CAM programming to optimize processing strategies and improve processing efficiency and accuracy.
(2) Precision grinding and polishing technology
Precision grinding and polishing are used to improve the surface quality of pipeline components, reduce fluid resistance, and improve sealing performance.
1) Grinding:
Applicable to high-precision sealing surfaces, such as valve sealing surfaces and pipe joint sealing end faces. Ultra-precision grinders can achieve nanometer-level precision.
2) Polishing:
Use mechanical polishing, electrolytic polishing and other technologies to improve the surface finish of parts, reduce corrosion risks, and improve the durability of plumbing component precision machined parts.
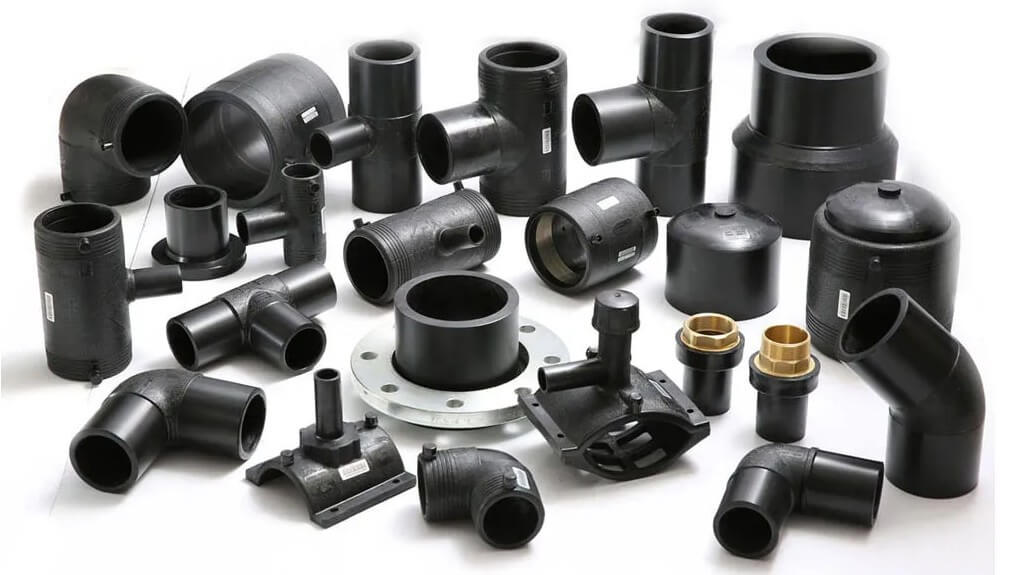
3) Key technical points:
● Use diamond grinding wheels or CBN grinding wheels to ensure grinding accuracy.
● Combine with automated polishing systems to improve surface quality stability.
4.Challenges faced by high-precision processing
(1) Material deformation and processing error control
Pipeline components usually use high-strength materials such as stainless steel, titanium alloy, and high-temperature alloy. These materials are prone to deformation during processing, affecting the dimensional accuracy of parts.
Solution:
● Use prestressed clamping technology to reduce the impact of deformation.
● Select appropriate cutting parameters to reduce the heat-affected area and improve processing stability.
(2) Tool wear and processing efficiency
When processing high-hardness materials, tool wear is severe, affecting processing accuracy and production efficiency.
Solution:
● Use coated tools (such as PCD and CBN coatings) to improve wear resistance.
● Combined with the intelligent tool monitoring system, the tool wear status is detected in real time, and the tool replacement strategy is optimized.
(3) Surface roughness and sealing performance
The sealing surface of the precision machined parts of pipeline components requires extremely high surface quality, and even tiny machining defects will affect the sealing performance.
Solution:
●Use ultra-precision grinding and polishing technology to ensure smoothness.
●Improve wear resistance and corrosion resistance through surface coating or chemical treatment.
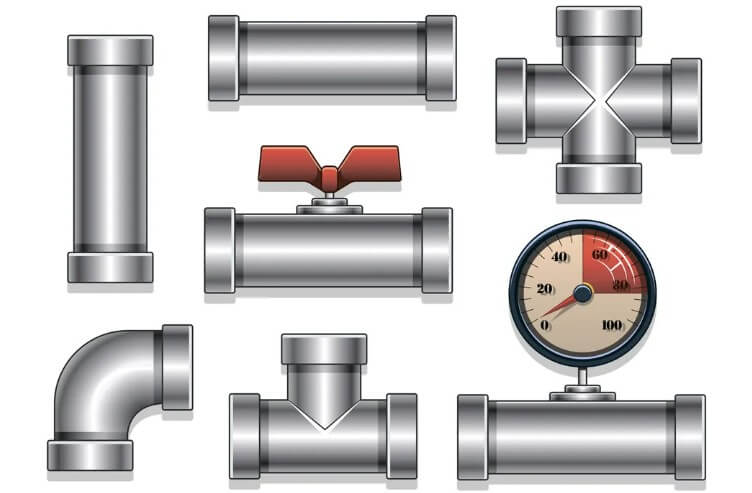
(4) Quality inspection and control
Plumbing component precision machined parts require strict quality inspection to ensure that dimensional tolerances, form and position tolerances meet standards.
Solution:
●Use a three-coordinate measuring machine (CMM) for precision measurement.
●Combined with an optical measurement system, non-destructive testing is achieved to improve detection efficiency.
5.Application areas of plumbing component precision machined parts
Plumbing component precision machined parts are widely used in modern industry. The following are typical cases in several major fields:
(1) Oil and gas industry
●Applicable to oil and gas extraction, transportation, refining and other links.
●Key parts include flanges, valve bodies, high-pressure joints, sealing gaskets, etc.
●Need to meet high pressure, high temperature, corrosion resistance and fatigue resistance requirements.
(2) Chemical and pharmaceutical industries
●Applied to chemical production, pharmaceutical synthesis, precision filtration systems, etc.
●Mainly include corrosion-resistant pipe fittings, precision valves, reactor connectors, etc.
●Need to have excellent chemical corrosion resistance and high cleanliness.
(3) Aerospace industry
●Applicable to fuel delivery systems, hydraulic systems, engine cooling pipelines, etc.
●Main parts include precision pipe joints, pressure seals, high-temperature pipelines, etc.
●Need to meet lightweight, high strength, high temperature tolerance and fatigue resistance.
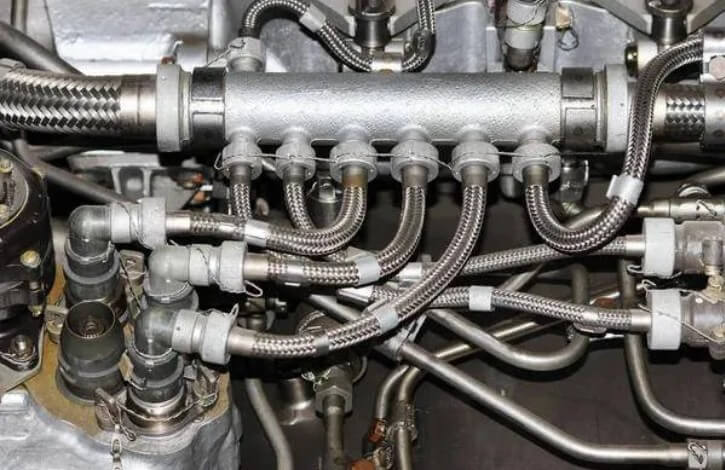
(4) Energy and power industry
●Applied to nuclear energy, thermal power generation, wind power and other energy systems.
●Key components include steam pipes, cooling water systems, high-temperature and high-pressure connectors.
●Need to have high temperature resistance, high pressure, oxidation resistance and radiation resistance.
(5) Marine Engineering
●Applicable to submarine oil and gas extraction, seawater desalination, ship pipeline systems, etc.
●Main components include submarine oil pipelines, corrosion-resistant joints, and deep-sea drilling equipment accessories.
●Must meet the requirements of seawater corrosion resistance, pressure resistance, and fatigue resistance to ensure long-term stable operation.
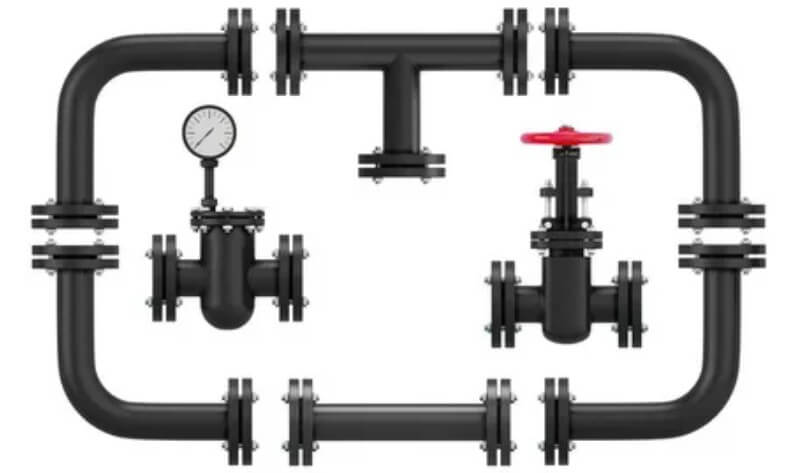
(6) Food and Medical Industry
●Used for food-grade fluid transportation, medical gas transportation, and pharmaceutical production equipment.
●Key parts include food-grade pipe joints, precision filtration systems, and medical valves.
●Must meet hygiene standards and have corrosion resistance, easy cleaning, non-toxic and pollution-free characteristics.
(7) Intelligent Manufacturing and Automation
●Applicable to industrial automation, robot hydraulic systems, and intelligent fluid control.
●Main components include automated transportation pipelines, intelligent valves, and high-precision seals.
●Must have high precision, wear resistance, and high-pressure impact resistance to improve automated production efficiency.
Plumbing component precision machined parts play a vital role in many industries. Different application fields have different performance requirements for parts, and appropriate processing technology and quality control methods need to be selected according to specific working conditions.
7.Summary
The manufacturing of plumbing component precision machined parts is a complex and precise process involving multiple links such as material selection, process optimization and practical application. By rationally selecting materials, optimizing processing technology, and combining actual application needs, the performance and quality of plumbing component precision machined parts can be significantly improved.