Oil & gas machining components: an in-depth analysis of the performance and processing technology of each component
The oil and gas industry is the backbone of global energy supply, and mechanical components are the core of the efficient operation of this industry.
From deep-sea drilling to land transportation, oil & gas machining components undertake critical tasks in extreme environments.These components must not only withstand high pressure, high temperature, corrosion and wear, but also have high reliability and long life.
This article will comprehensively analyze the design and manufacturing of oil & gas machining components from the aspects of material selection, component classification, performance requirements, production and processing, and industry challenges.
1.Material selection of oil & gas machining components
Material is a key factor in determining the performance of oil & gas machining components. The following are commonly used materials and their characteristics:
(1) Alloy steel
Alloy steel has high strength, high toughness and good processing performance, and is widely used in valves, pipelines and drilling equipment. By adding alloying elements such as chromium, nickel, and molybdenum, its corrosion resistance and wear resistance can be further improved.
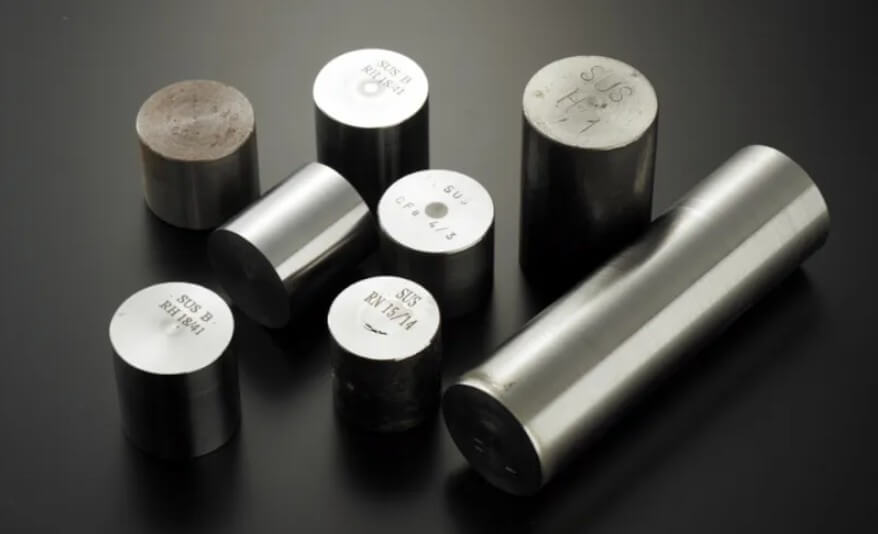
(2) Stainless steel
Stainless steel has good corrosion resistance and is suitable for corrosive media environments. For example, duplex stainless steel performs well in environments containing hydrogen sulfide and is often used in valves and pipelines.
(3) Nickel-based alloys
Nickel-based alloys have excellent high temperature and corrosion resistance and are suitable for extreme environments. For example, Hastelloy alloy performs well in high temperature and high pressure acidic gas environments and is often used in compressor and pump components.
(4) Titanium alloys
Titanium alloys have high strength, low density and excellent corrosion resistance and are suitable for deep-sea equipment. For example, titanium alloy drill pipes perform well in deep-sea drilling.
2.Overview of oil & gas machining components
Oil & gas machining components are an indispensable key component in the extraction, transportation, processing and storage of oil and gas. According to their functions and application scenarios, oil & gas machining components can be roughly divided into the following categories:
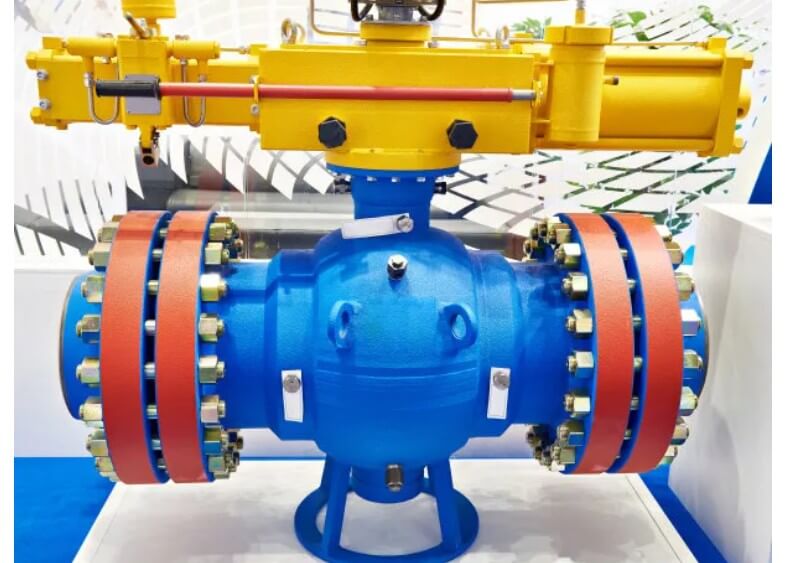
(1) Valve components
Valves are core components in oil and gas transmission systems and are used to control the flow direction, pressure and flow of fluids. There are many types of valves, and the following are common ones:
1) Ball valve:
It controls the flow of fluid by rotating the ball. It has the characteristics of good sealing and flexible operation. It is suitable for high pressure and high flow rate environments.
2) Gate valve:
Controls fluid flow by lifting and lowering the gate, suitable for fully open or fully closed occasions, and often used in large-diameter pipelines.
3) Stop valve:
Controls fluid flow by moving the valve disc up and down, suitable for occasions where precise flow regulation is required.
4) Safety valve:
Used to prevent system pressure from being too high. When the pressure exceeds the set value, it automatically opens to release excess pressure and ensure system safety.
(2) Pipelines and connectors
Pipelines are the main carrier for the transportation of oil and natural gas, while connectors are used for the connection and diversion of pipelines. Common pipelines and connectors include:
1) Pipelines:
Used to transport oil, natural gas and their derivatives, usually made of high-strength alloy steel or stainless steel to withstand high pressure and corrosive media.
2) Flanges:
Used to connect pipelines and equipment, with high strength and good sealing. Common types include flat welding flanges, butt welding flanges and threaded flanges.
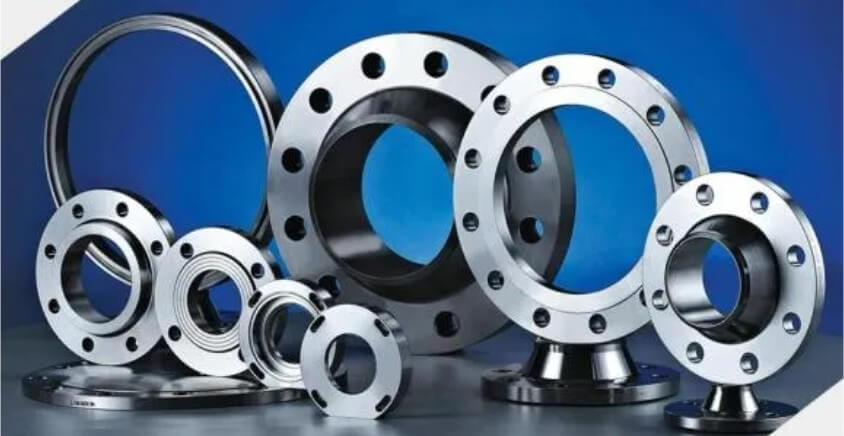
3) Elbow:
Used to change the flow direction of the pipeline. Common angles are 45 degrees, 90 degrees and 180 degrees. They are usually manufactured by forging or casting.
4) Tee:
Used to divert or merge fluids. Common types include equal-diameter tees and reducing tees.
Pipelines and connectors need to have high strength, corrosion resistance and wear resistance to cope with complex geological conditions and fluid media.
(3) Pumps and compressors
Pumps and compressors are key equipment for oil and gas transportation and pressurization. They are widely used in upstream mining, midstream transportation and downstream processing.
1) Pump:
Mainly used to transport liquids such as crude oil, water and chemicals. Common pump types include centrifugal pumps, reciprocating pumps and screw pumps.
Pump components need to have high strength and corrosion resistance to cope with high pressure and corrosive media.
2) Compressor:
Mainly used to pressurize gases such as natural gas and air. Common compressor types include reciprocating compressors, centrifugal compressors and screw compressors.
The components of the compressor need to have high strength and high temperature resistance to cope with high pressure and high temperature environments.
(4) Drilling equipment
Drilling equipment is the core tool for oil and gas extraction and is widely used in land drilling and offshore drilling. Common drilling equipment includes:
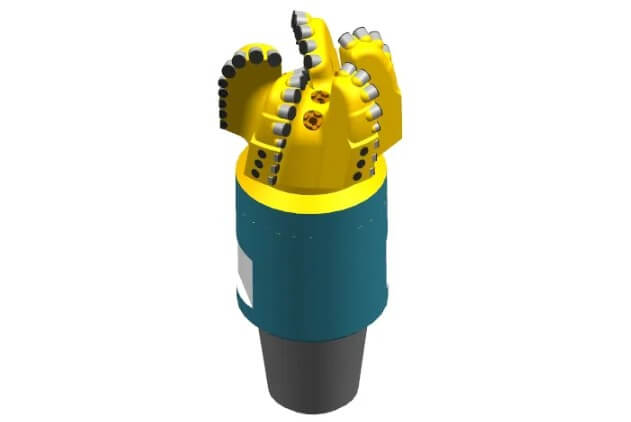
1) Drill bit:
Used to break rocks. Common drill bit types include roller drill bits, PDC drill bits and diamond drill bits.
The drill bit needs to have high hardness and wear resistance to cope with complex geological conditions.
2) Drill rod:
Used to transmit torque and drilling fluid. It is usually made of high-strength alloy steel and needs to have high strength and fatigue resistance.
3) Drill collar:
Used to increase drilling pressure and stabilize drilling tools. It is usually made of high-strength alloy steel and needs to have high strength and wear resistance.
3.Specific application of CNC machining in the manufacturing of oil & gas machining components
The complexity and high performance requirements of oil & gas machining components make CNC machining a core link in their manufacturing process. The following are the applications of CNC machining in the manufacturing of several typical components:
(1) CNC machining of valve components
Valve components (such as valve body, valve seat, valve stem) usually have complex internal flow channels and sealing surfaces, and have extremely high requirements for machining accuracy and surface quality.
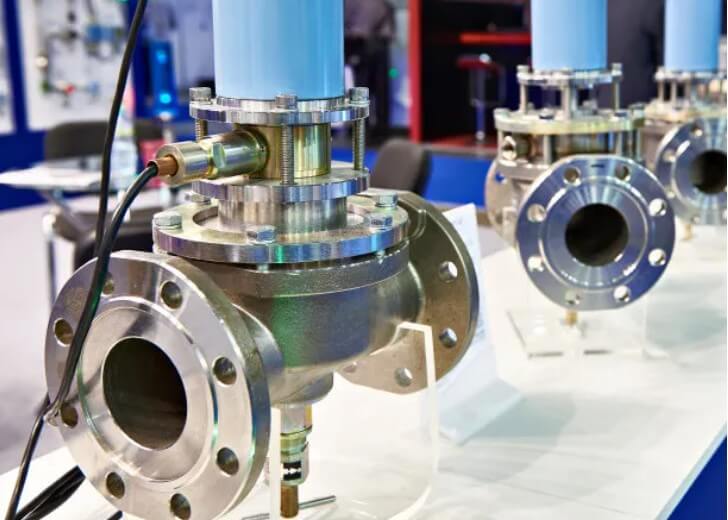
1) Valve body machining:
The valve body is usually made of stainless steel or alloy steel, and the internal flow channel shape is complex. CNC milling machines and milling machines can efficiently complete the rough machining and fine machining of the flow channel to ensure the smoothness and dimensional accuracy of the flow channel.
2) Valve seat machining:
The sealing surface of the valve seat requires extremely high surface finish and shape accuracy. CNC grinders and precision lathes can complete the precision machining of the sealing surface to ensure the sealing performance of the valve.
3) Valve stem machining:
The valve stem usually has a slender structure and high-precision threads. CNC lathes can efficiently complete the outer circle machining and thread machining of the valve stem to ensure its matching accuracy with the valve body.
(2) CNC machining of pipes and fittings
Pipes and fittings (such as flanges, elbows, and tees) need to have high strength and good sealing performance, and their machining process involves a large amount of hole machining, end face machining, and complex surface machining.
1) Flange machining:
The end face and bolt holes of the flange require high-precision machining. CNC milling machines can efficiently complete the plane machining of the flange end face and the drilling and tapping of the bolt holes.
2) Elbow machining:
The inner and outer walls of the elbow need a smooth transition to ensure smooth flow of the fluid. CNC lathes and five-axis machining centers can complete the precision machining of the inner and outer walls of the elbow.
3) Tee machining:
The branch interface of the tee requires high-precision position control and shape machining. CNC milling machines and milling machines can complete the complex surface machining of the tee.
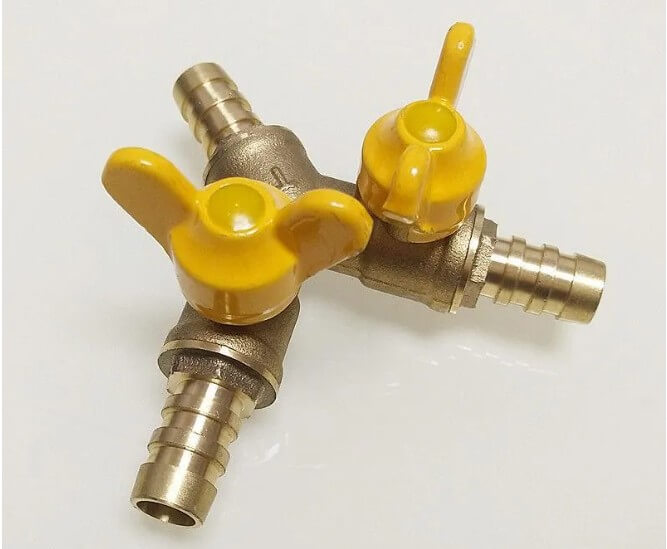
(3) CNC machining of pump and compressor components
The core parts of pumps and compressors (such as impellers, housings, and shafts) usually have complex geometric shapes and high-precision matching requirements.
1) Impeller processing:
The impeller is the core component of the pump and compressor. Its blades have complex shapes and require extremely high processing accuracy. The five-axis CNC milling machine can efficiently complete the rough processing and fine processing of the blades to ensure the fluid dynamics performance of the impeller.
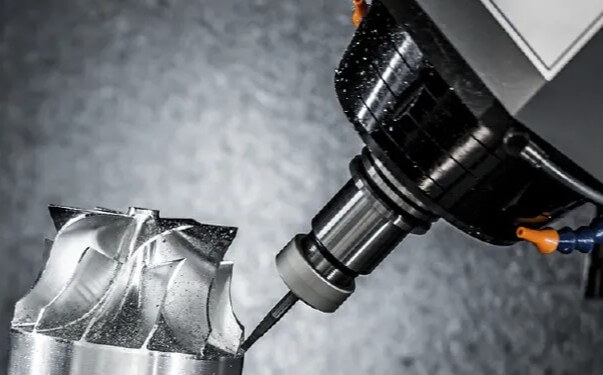
2) Shell processing:
The inner cavity of the shell has a complex shape and requires high-precision processing. CNC milling machines and milling machines can complete the inner cavity processing and end surface processing of the shell.
3) Shaft processing:
The shaft usually has a slender structure and a high-precision bearing mating surface. CNC lathes can efficiently complete the outer circle processing of the shaft and the precision processing of the bearing mating surface.
(4) CNC processing of drilling equipment
Drilling equipment (such as drill bits, drill rods, and drill collars) needs to work under extreme geological conditions and has extremely high requirements for the hardness and wear resistance of the material.
1) Drill bit processing:
The cutting teeth of the drill bit require high-precision shape processing and surface treatment. CNC grinders and EDM machines can complete the precision processing of cemented carbide cutting teeth.
2) Drill pipe processing:
The outer circle and thread of the drill pipe need high-precision processing. CNC lathes can efficiently complete the outer circle processing and thread processing of the drill pipe.
3) Drill collar processing:
The outer wall and inner wall of the drill collar need a smooth transition to ensure the smooth flow of drilling fluid. CNC lathes and milling machines can complete the complex surface processing of drill collars.
4.Key technologies and challenges of CNC machining in the manufacturing of oil & gas machining components
Although CNC machining has significant advantages in the manufacturing of oil & gas machining components, its application still faces some key technologies and challenges:
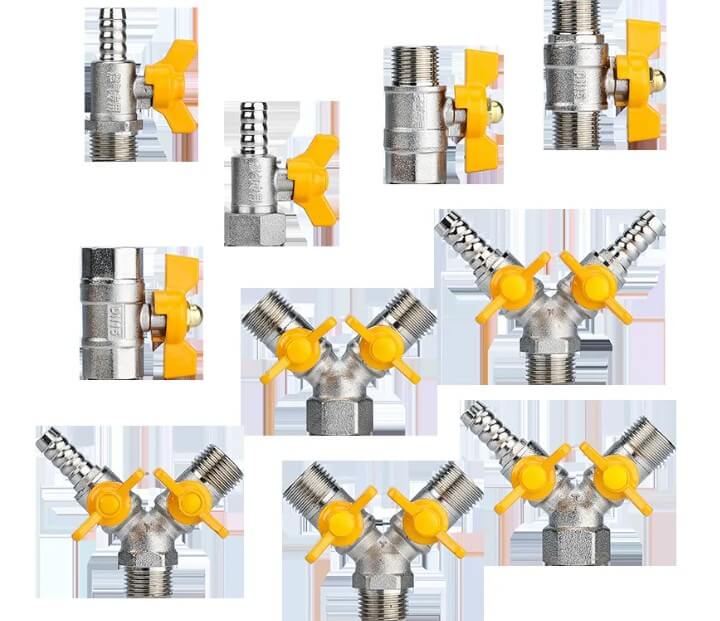
(1) Processing of high-hardness materials
Oil & gas machining components are usually made of high-strength alloy steel, stainless steel, nickel-based alloys and other high-hardness materials. These materials are difficult to process and put forward higher requirements on the performance of cutting tools and machine tools.
1) Tool selection:
Use carbide tools, ceramic tools or cubic boron nitride (CBN) tools to improve cutting efficiency and tool life.
2) Cutting parameter optimization:
Reduce tool wear and machining deformation by optimizing cutting speed, feed rate and cutting depth.
(2) Machining of complex shapes
Oil and gas machining components usually have complex geometric shapes, such as curved surfaces, inner cavities and flow channels, which puts higher requirements on the multi-axis linkage capability and programming technology of CNC machining.
1) Multi-axis machining technology:
Use five-axis CNC machine tools to achieve high-precision machining of complex curved surfaces.
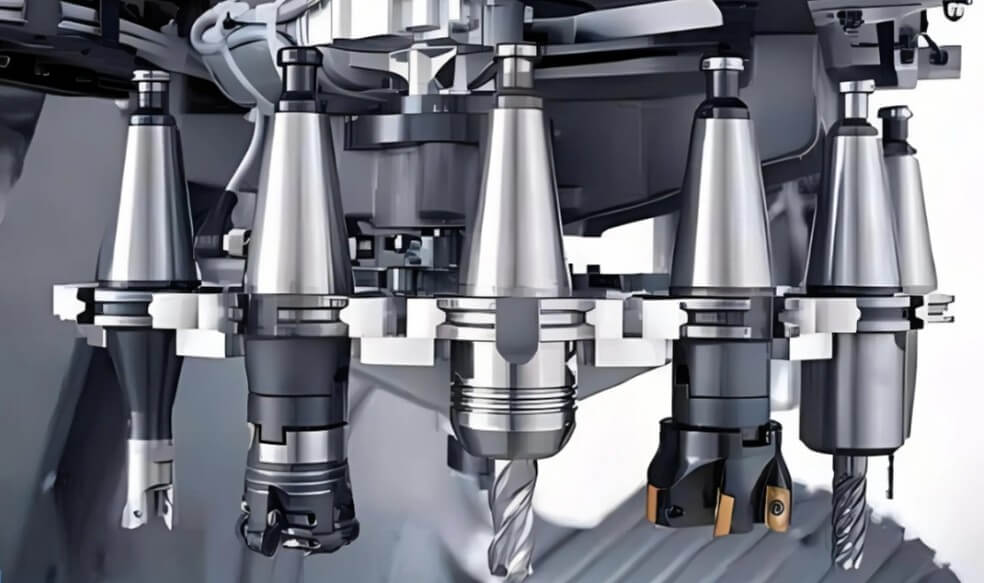
2) CAM software application:
Use advanced CAM software to generate efficient tool paths to reduce machining time and tool wear.
(3) Machining accuracy and surface quality
Oil and gas machining components have extremely high requirements for machining accuracy and surface quality, especially in the machining of sealing surfaces and mating surfaces.
1) Precision machining technology:
Use CNC grinders and precision lathes to ensure the dimensional accuracy and surface finish of key surfaces.
2) Online detection technology:
Real-time monitoring of workpiece size and surface quality during machining to ensure machining accuracy.
5.Summary
Oil & gas machining components are of various types and have different functions, but their common feature is that they need to operate in extreme environments, which places extremely high demands on performance, materials and manufacturing processes. By deeply understanding the classification and functions of these components, it can provide an important basis for material selection, processing technology design and quality control, thereby improving the performance and reliability of components and meeting the needs of the oil and gas industry.