In-depth analysis of investment casting process: from wax pattern to perfect casting
Investment casting process, also known as precision casting process or lost wax casting process, is a casting method in which metal is melted and injected into a pre-made cavity, and the metal product is taken out after cooling and solidification. This ancient and exquisite technology not only carries the crystallization of human wisdom, but also plays an important role in modern industrial manufacturing.
This article will explore the art and technology of investment casting process in depth, and comprehensively demonstrate the unique charm of this casting technique from its principles, characteristics, processes, materials to applications.
1.Basic principles and characteristics of investment casting process
The basic principle of investment casting process is to make a wax pattern, coat its surface with refractory material to form a shell, then heat the wax pattern to melt and flow out, and then inject molten metal into the shell, and cool it to obtain the desired casting. The main features of this process include:
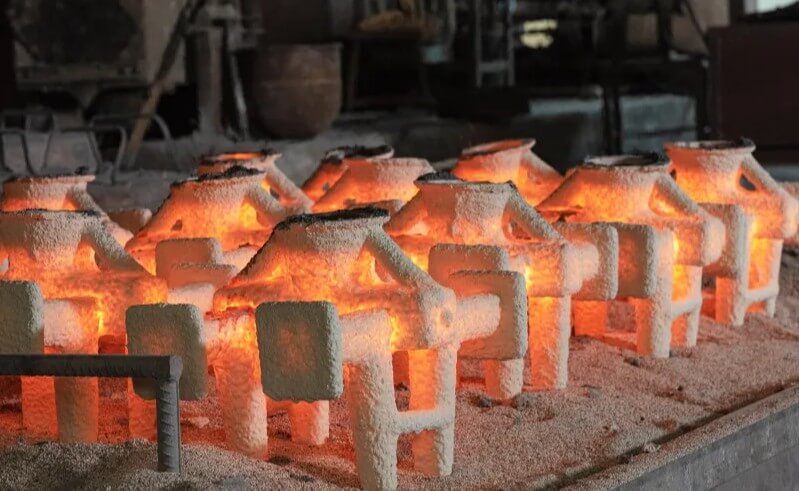
(1) High precision and low surface roughness:
Investment casting can achieve extremely high dimensional accuracy and surface finish, with a general accuracy of 5~7 and a roughness of Ra25-6.3μm, which is suitable for manufacturing parts with complex shapes.
(2) Thin-walled and tiny castings:
Investment casting process can produce thin-walled castings with a wall thickness of only 0.5 mm and a weight of several grams, as well as complex parts with fine patterns, fine grooves and curved fine holes.
(3) Design flexibility:
The investment casting process is almost not limited by the shape of the parts. It can produce complex parts that are difficult to achieve by sand casting, forging, cutting and other methods. It can even directly cast assembled parts and welded parts into integral parts to reduce weight and cost.
(4) Alloy diversity:
Investment casting is suitable for a variety of alloy materials, including alloy steel, carbon steel and heat-resistant alloys.
(5) Flexible production batch:
Investment casting process is suitable for both single-piece production and batch mass production.
2.Detailed analysis of the manufacturing process of investment casting process
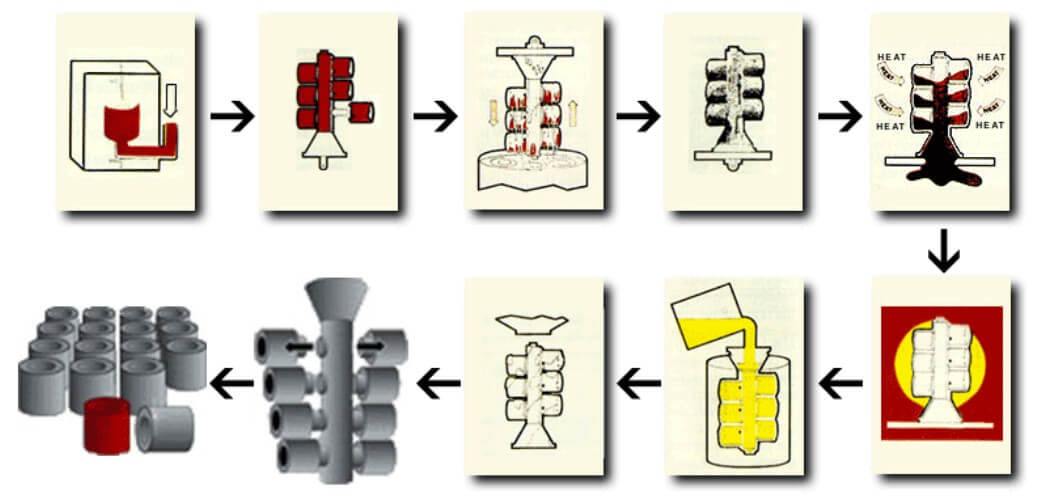
(1) Wax mold molding
1) Wax pressing:
First, the wax material is heated to liquid state, and then the liquid wax material is pressed into the mold cavity by pressure. The mold is usually made of high-hardness steel with a high surface finish to ensure the accuracy and surface quality of the wax model.
2) Cooling:
After the wax material is cooled and solidified in the mold, it is taken out of the mold to form a wax model consistent with the shape of the final casting.
(2) Tree assembly
1) Wax repair:
The wax model is repaired to remove surface defects and burrs to ensure the integrity and accuracy of the wax model.
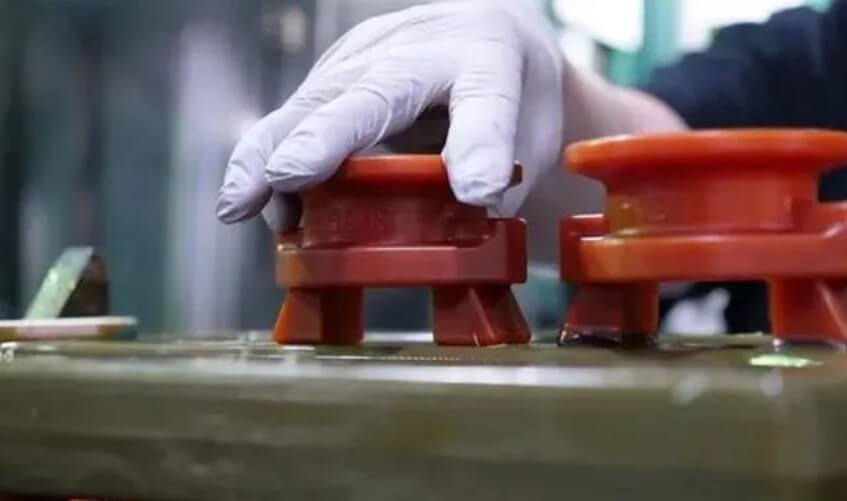
2) Welding:
Multiple wax models are combined on the pouring system by welding to form a mold group. Welding usually uses a thin soldering iron to melt the connecting parts of the wax model and weld the wax models together.
(3) Shell making
1) Coating:
The mold is immersed in a refractory coating such as silica sol, and then a layer of coating is evenly coated on the surface of the wax mold. The main component of the coating is a silica colloidal solution that can remain stable at high temperatures.
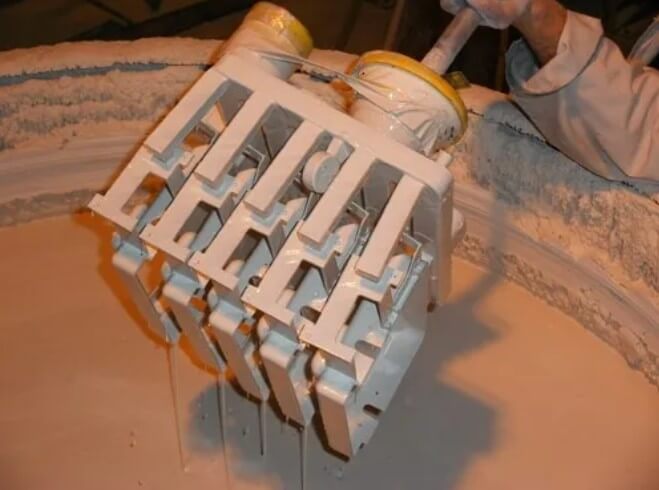
2) Sanding:
After applying the coating, a layer of refractory sand is immediately sprinkled on the surface of the mold. Refractory sand is usually quartz sand or corundum sand, which can improve the strength and refractoriness of the mold shell.
3) Drying and hardening:
Place the mold coated with paint and sanded at a specific temperature and humidity for drying and hardening, so that the binder in the paint changes from sol to gel, connecting the refractory materials together. This process needs to be repeated 5-6 times until a mold shell with a certain strength and refractoriness is formed.
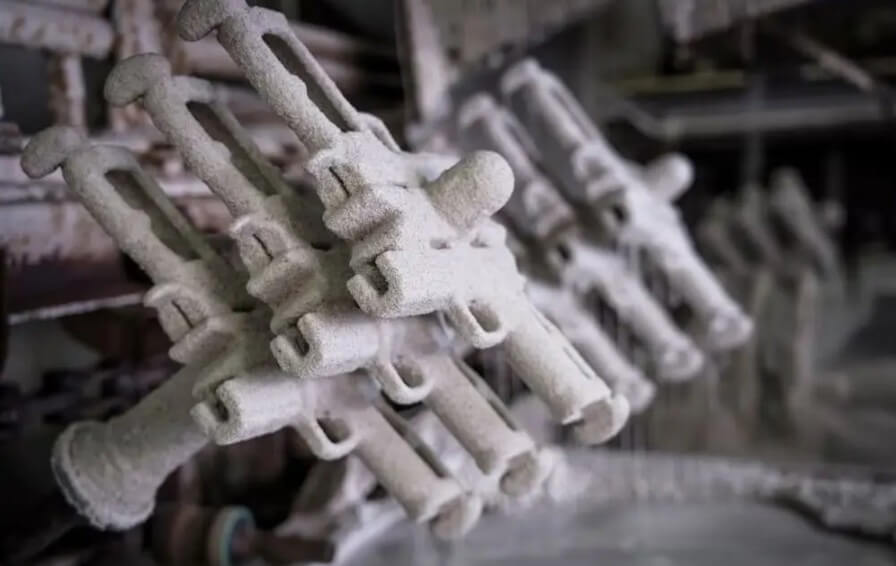
(4) Dewaxing and calcining
1) Dewaxing:
Put the mold shell in high-temperature steam to melt and discharge the wax mold to obtain a hollow mold shell.
2) Calcination:
The dewaxed mold shell is calcined at high temperature, usually at about 1000 degrees for 1-2 hours, to burn off the residual wax and moisture in the mold shell and improve the strength and stability of the mold shell.
(5) Melting and pouring
1) Melting:
Select a suitable metal material and heat it to a molten state. The choice of metal should be determined according to the performance requirements of the casting. Commonly used metal materials include steel, aluminum, copper, etc.
2) Pouring:
Pour the molten metal into the cavity to ensure complete filling. This step requires controlling the injection speed and temperature of the molten metal to avoid defects such as pores and shrinkage holes.
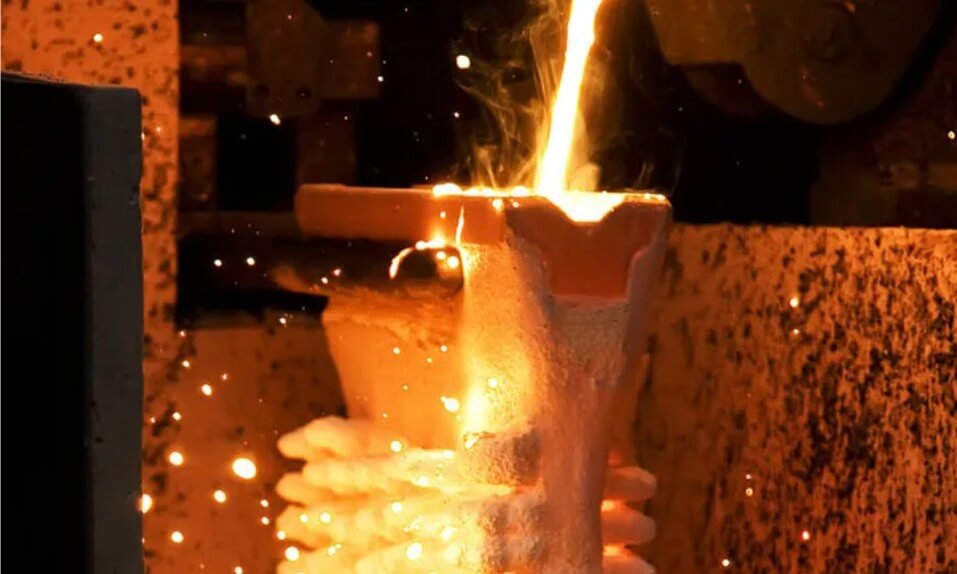
(6) Cooling and cutting to obtain the finished product
1) Cooling:
Cool the cavity to room temperature to solidify the metal. The cooling process needs to control the cooling rate to ensure the structure and performance of the casting.
2) Shelling:
Use a vibrating shelling machine to separate the mold shell from the blank.
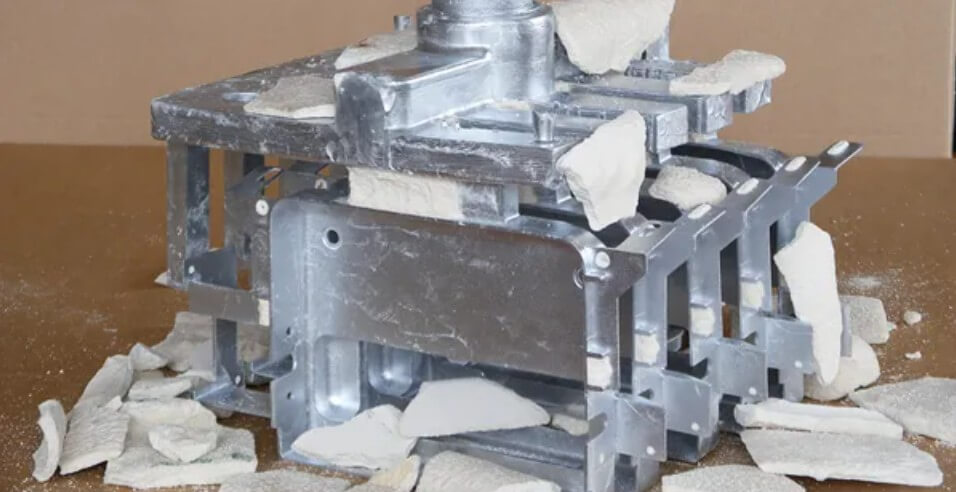
3) Cutting:
Cut and separate the casting from the pouring system to obtain the finished casting.
4) Post-processing:
According to the needs, perform post-processing such as polishing and machining to obtain the final product.
3.Materials that can be used for investment casting process
The investment casting process is almost not limited by alloy materials and can produce castings with complex shapes and high dimensional accuracy to meet the needs of different industries. The following are materials commonly used in investment casting:
(1) Carbon steel and alloy steel:
These materials have good mechanical properties and can produce high-precision, complex-shaped parts through investment casting.
(2) Stainless steel:
Due to its excellent corrosion resistance, it is widely used in the manufacture of parts that require high corrosion resistance.
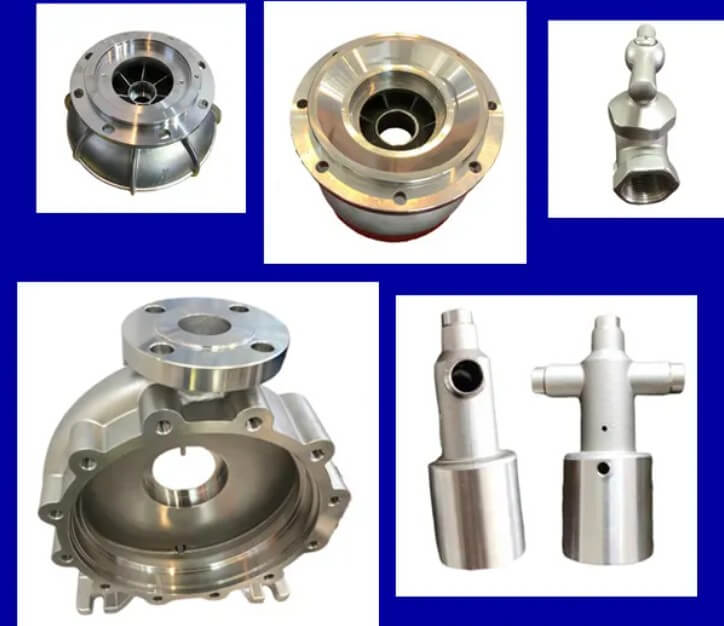
(3) Heat-resistant alloys:
Suitable for the manufacture of parts in high-temperature environments, such as blades of steam turbines and gas turbines.
(4) Copper alloys:
Have good electrical and thermal conductivity and are often used in the manufacture of electrical and mechanical parts.
(5) Aluminum alloys:
Lightweight and high strength, suitable for the aerospace and automotive industries.
(6) Titanium alloys:
Have extremely high strength-to-weight ratio and excellent corrosion resistance, commonly used in the aerospace and medical device fields.
(7) Precision alloys and permanent magnet alloys:
These materials have special physical properties, such as high magnetic permeability or low expansion coefficient, and are suitable for the manufacture of precision instruments and electronic equipment.
(8) Ductile iron:
It has good toughness and strength and is suitable for manufacturing complex mechanical parts.
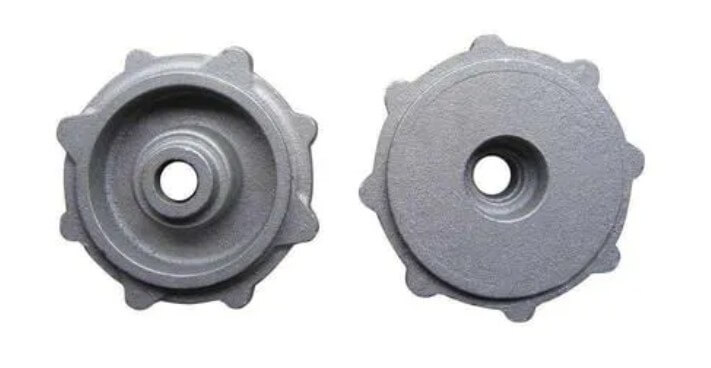
(9) Bearing alloy:
It is used to manufacture bearings and other parts that require high wear resistance.
4.Application of investment casting process
Due to its high precision and complex shape forming capabilities, the investment casting process has been widely used in many fields. The following are its main application areas and specific parts:
(1) Aerospace field
1) Turbine blades:
Investment casting can produce complex-shaped blades that can withstand high temperatures and high pressures.
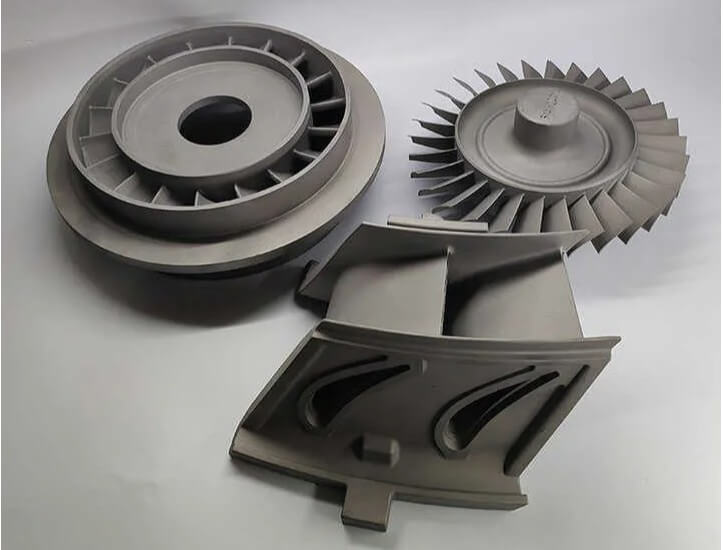
2) Integral blade disk:
Reduce the number of parts and improve engine performance and reliability.
3) Combustion chamber:
Combustion chambers with complex structures can be formed in one step through investment casting.
(2) Automobile field
1) Engine parts:
Such as exhaust manifolds, turbochargers, etc., to improve engine efficiency.
2) Suspension system parts:
Precision parts such as control arms improve vehicle handling.
3) Brake system parts:
Such as brake calipers, to ensure safety performance.
(3) Medical device field
1) Surgical instruments:
Such as scissors and pliers used in surgical operations, which require high precision and surface finish.
2) Orthopedic implants:
Artificial joints, etc., which need to be precisely matched with human bones.
(4) Energy field
1) Gas turbine blades:
Used in power generation equipment, resistant to high temperature and high pressure.
2) Nuclear power equipment parts:
Such as valves, pump bodies, etc., which require stable material properties.
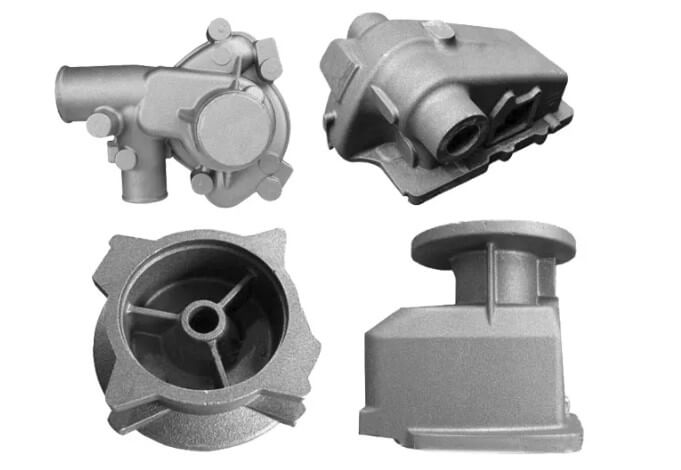
(5) Jewelry field
1) Jewelry:
Such as rings, necklaces, etc., which can be made into complex and exquisite shapes.
2) Watch parts:
Precision watch cases and internal structural parts.
Due to its high flexibility and precision, the investment casting process can meet the production needs of complex and precision parts in different fields.
5.Summary
In short, as an art and technology for manufacturing precision castings,investment casting process has exquisite process flow, diverse applicable materials, and diverse application fields, all of which show that investment casting process plays an important role in modern industrial manufacturing.
What do you think?
[…] defects and taking effective preventive measures can weContinuously improve the technical level of investment casting process, thereby improving casting quality, reducing production costs, and improving the competitiveness of […]
[…] 2.Specific applications of aerospace investment castings […]
[…] что позволяет избежать ошибок в размерах и дефектов поверхности, возникающих из-за разделительных […]
[…] что позволяет избежать ошибок в размерах и дефектов поверхности, возникающих из-за разделительных […]
[…] basic process flow of investment casting includes: making wax molds, wax mold combination, coating refractory materials, hardening and […]
[…] Investment casting, also known as lost wax casting, mainly includes the following steps: […]
[…] been selected according to the needs, and the next step is specific production and manufacturing. The process of steel investment casting includes wax pattern manufacturing, shell manufacturing, dewaxing, roasting and pouring, and each […]
[…] Investment casting first makes a wax mold and then covers it with refractory material. The process is […]
[…] In short, how to make a mold? This is a complex and systematic process involving multiple links such as material selection, design and processing. Only by comprehensively considering the factors of each link can high-quality casting molds be manufactured to provide strong support for the metal forming process. […]