Application of aluminum alloy shell die casting in the electronics industry
As an innovative process, aluminum alloy shell die casting has emerged in the electronics industry and provided key solutions for various electronic devices. This article will explore in depth the important applications of aluminum alloy shell die casting in the electronics industry.
1.Overview of the application premise of aluminum alloy shell die casting in the electronics industry
(1) Definition and development history of die casting process
Die casting is a manufacturing technology that uses high pressure to inject molten metal into a mold and quickly cools and solidifies it to form precision parts. Since this technology was first used in industrial production in the late 19th century, it has undergone many technological innovations and has become an indispensable part of modern manufacturing. Especially in the electronics industry, die casting is widely used because it can produce high-precision and complex structure parts.
(2) Characteristics and selection advantages of aluminum alloy
Aluminum alloy has light weight, high strength, good thermal conductivity and corrosion resistance, which make it an ideal material for electronic equipment housing. Through the die casting process, aluminum alloy can be made into a shell with complex structure and precise size, which can not only meet the requirements of electronic equipment for appearance and performance, but also effectively enhance the market competitiveness of the product.
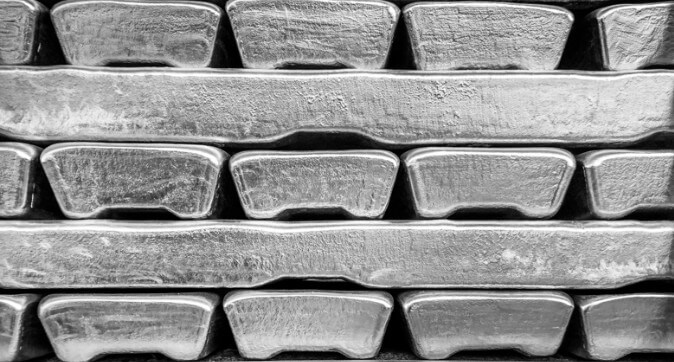
2.Advantages of aluminum alloy shell die casting in the electronics industry
(1) Lightweight design
Lightweight design of electronic equipment is a key trend in the modern electronics industry. Aluminum alloy shell die casting is the first choice for its lightweight characteristics, and it provides higher strength and rigidity than traditional materials such as steel. This allows electronic devices to be more portable without sacrificing protection performance.
(2) Excellent thermal conductivity
Electronic devices usually generate a lot of heat, so heat dissipation is an important issue. Aluminum alloy has excellent thermal conductivity and can quickly conduct and dissipate heat, helping to keep the temperature of the device within a safe range. This is crucial to extending the life and stability of electronic devices.
(3) EMI shielding
In electronic devices, the management of electromagnetic interference (EMI) is crucial. Aluminum alloy housings have excellent electromagnetic shielding properties, which can effectively block external interference and reduce the occurrence of internal interference. This is very important to ensure the normal operation and data integrity of electronic devices.
(4) Durability and corrosion resistance
Aluminum alloy housings have excellent durability and corrosion resistance and can work in various harsh environments, including outdoor and industrial applications. This makes them ideal for outdoor electronic devices and industrial automation equipment.
(5) Customized design
Aluminum alloy shell die casting allows manufacturers to make highly customized designs to meet the needs of specific applications. This flexibility allows aluminum alloy housings to adapt to electronic devices of various shapes and sizes while providing excellent performance and appearance.
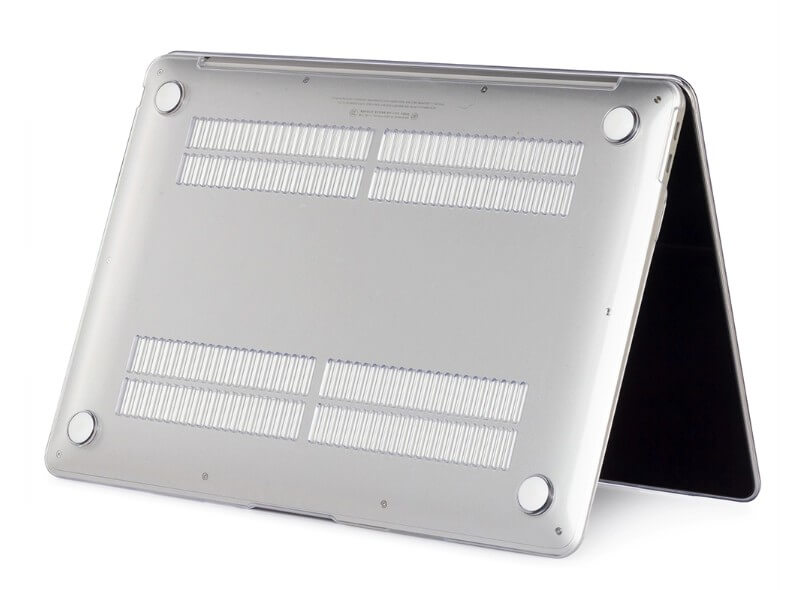
3.Key technologies of aluminum alloy shell die casting in the electronics industry
(1) Type selection and operation process of die casting machines
Die casting machines are mainly divided into two types: cold chamber die casting machines and hot chamber die casting machines. Cold chamber die casting machines are suitable for the production of larger aluminum alloy parts, while hot chamber die casting machines are more suitable for the production of small and precision parts. Therefore, hot chamber die casting should be selected for aluminum alloy shell die casting in the electronics industry.
The die casting operation process usually includes steps such as metal melting, injection, filling, holding pressure and mold opening. Each step requires precise control to ensure the quality and performance of the final product.
(2) Mold design and manufacturing of aluminum alloy shell die casting
Mold design and manufacturing are key links in the die casting process. The design of the mold should not only consider the structure and dimensional accuracy of the product, but also the fluidity and cooling rate of the aluminum alloy to ensure that the product is defect-free. High-quality molds can significantly improve production efficiency and reduce production costs.
(3) Material selection and processing
Common aluminum alloy types and their characteristics In the electronics industry, commonly used aluminum alloy types include AlSi9Cu3, AlSi12, etc. These alloys have good fluidity and mechanical properties and are very suitable for die casting processes.
AlSi9Cu3 alloy is often used in the production of high-performance electronic equipment casings due to its good heat treatment performance and high strength. AlSi12 alloy is widely used in the production of structural parts of electronic equipment due to its excellent casting performance and good wear resistance.
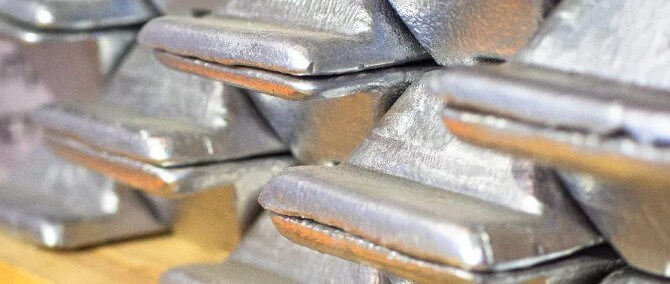
AlSi9Cu3 alloy
(4) Melting and alloying treatment
The melting and alloying treatment of aluminum alloys are important steps to ensure material properties. During the melting process, the temperature and time need to be strictly controlled to ensure the uniformity of the alloy composition. During the alloying process, by adding appropriate amounts of elements such as magnesium and copper, the mechanical properties and corrosion resistance of aluminum alloys can be significantly improved.
4.Main application directions and product cases of aluminum alloy shell die casting in the electronics industry
(1) Smartphones and tablets
1) Lightweight and structural design of shells
Aluminum alloy shell die-casting technology has been widely used in the shell manufacturing of smartphones and tablets. Through sophisticated design and efficient die-casting process, it is possible to produce shells that are both thin and strong. These shells are not only beautiful, but also effectively protect the internal components from external impact and wear. In addition, the excellent heat dissipation performance of aluminum alloys helps to improve the operating efficiency of the equipment and extend the battery life.
2) Heat dissipation and EMI shielding solutions
Aluminum alloy shells not only provide good mechanical protection, but also have excellent heat dissipation performance and electromagnetic interference (EMI) shielding effect. This is crucial for the stable operation of high-performance processors and wireless communication modules. By optimizing alloy composition and surface treatment technology, these properties can be further improved to meet the technical requirements of high-end electronic equipment.
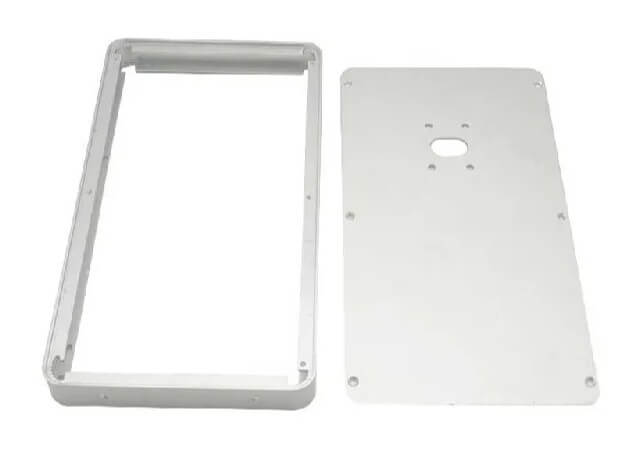
(2) Laptops
1) Applications combining high strength and light weight
Aluminum alloy shell die-casting technology is also widely used in laptop manufacturing. Aluminum alloy shells not only reduce the overall weight of the computer, but also provide sufficient structural strength to protect the fragile internal components. In addition, the aesthetics and processability of aluminum alloys allow laptop shells to be designed into a variety of styles that are both fashionable and functional.
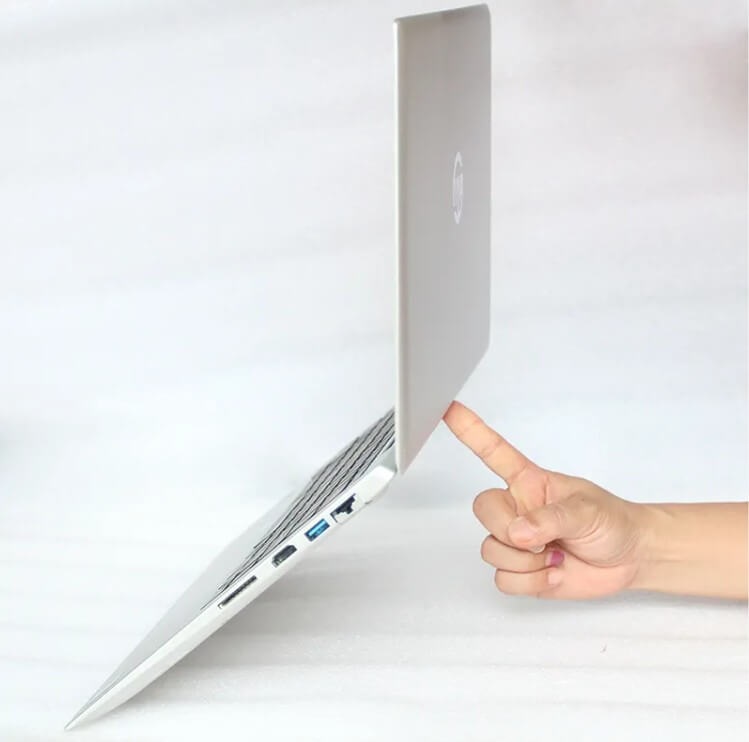
2) Combining aesthetics and functionality of the shell
Through sophisticated surface treatment techniques such as anodizing, sandblasting and coating, aluminum alloy shells can achieve a variety of colors and textures to enhance the visual appeal of the product. At the same time, these treatment techniques can also improve the wear resistance and corrosion resistance of the shell, enhancing the durability of the product.
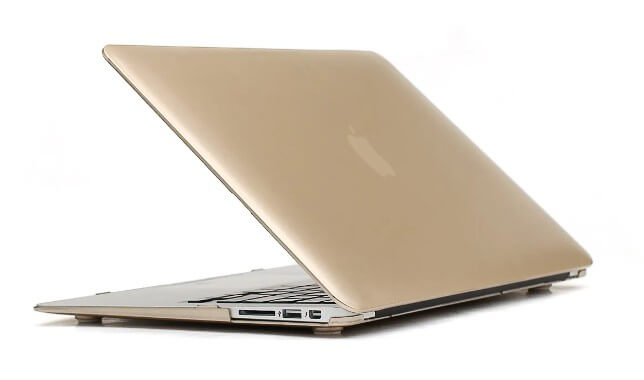
(3) Power supply devices and adapters
1) Heat dissipation advantages of aluminum alloy shells
Power supply devices and adapters generate a lot of heat when working, so heat dissipation performance is an important consideration in material selection. Aluminum alloys are ideal for the shells of these devices due to their efficient thermal conductivity. Aluminum alloy shells can quickly conduct internal heat away, keep the device within a suitable operating temperature range, and improve the stability and safety of the device.
2) Improved safety and protection
Aluminum alloy shells not only have good heat dissipation performance, but also provide excellent electrical insulation and mechanical protection to prevent electric shock and other safety risks. In addition, the corrosion resistance and impact resistance of aluminum alloy also enable power supply equipment to operate stably in various harsh environments, extending the service life of the equipment.
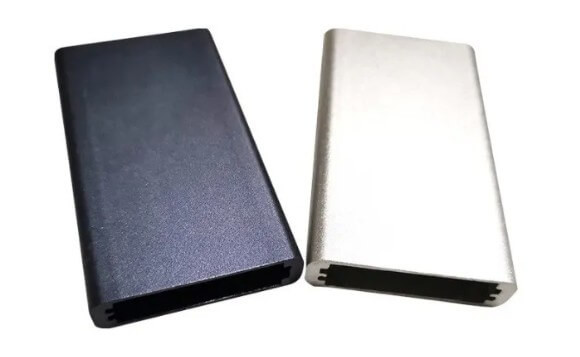
5.Main precautions when aluminum alloy shell die casting:
(1) Demolding problem:
In the early design of aluminum alloy shell die casting, the difficulty of demoulding should be considered, complex structures should be avoided, the number of core pulling should be reduced, and mold damage should be prevented.
(2) Wall thickness problem:
Control the wall thickness of the aluminum alloy shell die casting parts to avoid excessive thickness difference, which will affect the filling effect and casting quality.
(3) Mold design:
Optimize mold design to ensure that the pouring system is reasonable, the exhaust groove and overflow groove are correctly positioned, and the size is appropriate to ensure smooth flow of molten metal and effective gas discharge.
(4) Die-casting process parameters:
Reasonably select the process parameters of aluminum alloy shell die casting, such as injection speed, filling time, mold opening time, etc., to ensure the quality of castings.
(5) Mold temperature control:
Use the mold cooling system to control the mold temperature, extend the mold life, improve production efficiency, and prevent cracks and deformation caused by mold overheating.
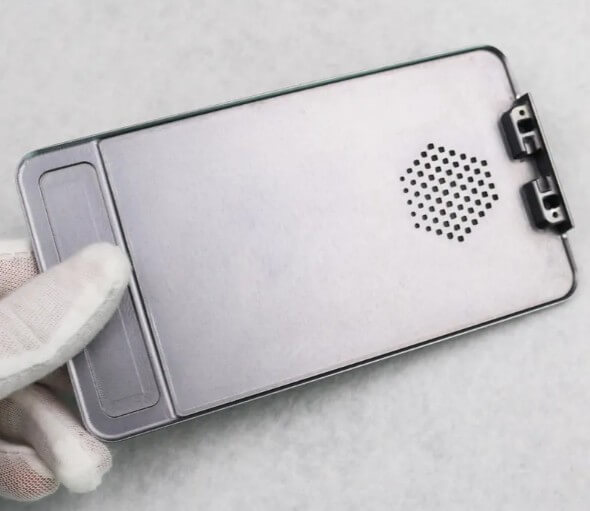
6.How to set the process parameters for aluminum alloy shell die casting
(1) Metal temperature:
Controlling the temperature of molten metal is the key to ensuring the stability of the aluminum alloy shell die casting process. Generally, the melting temperature of aluminum alloy is 650℃-710℃. Maintain the temperature of the metal through appropriate furnace temperature control and melting time.
(2) Mold temperature:
The temperature of the mold directly affects the molding quality and surface finish of the part. The temperature of the mold is usually between 150℃-250℃. Control the temperature of the mold through the heating and cooling system to ensure the molding quality of the part.
(3) Pressure control:
The pressure in the die casting process is generated by the pressure pump. The pressure acting on the metal liquid is the main factor in obtaining a dense structure and a clear contour casting. The pressure of aluminum alloy shell die casting is usually between 3500Psi~4500Psi.
(4) Injection speed:
Injection speed affects the speed at which the metal liquid enters the mold cavity and the filling situation. The slow speed is generally 0.10.5M/S, while the fast speed is generally 0.11.1M/S. The thinner the wall thickness of the casting, the faster the injection speed.
(5) Filling time:
Filling time is the time required for the aluminum alloy metal liquid to start filling the mold cavity. The selection principle of filling time is: the higher the alloy pouring temperature, the longer the filling time should be; the higher the mold temperature, the longer the filling time; the farther the thick wall part is from the inner door, the longer the filling time should be; the alloy with high melting heat, the longer the filling time should be; when the exhaust effect is poor, the filling time should be longer.
(6) Holding time:
The holding time is also called the holding time, which is the time required for the metal liquid to solidify under the action of the pressure ratio after filling the mold cavity. When the wall thickness of the casting is less than 1.2MM, the holding time of die-cast aluminum is 2 to 5 seconds, and when the wall thickness of the casting is 3 to 8MM, the holding time is 2.5 to 6 seconds.
(7) Retention time:
This is the time the casting stays in the mold. That is, the time required from the start of pressure holding to the time the casting is ejected from the mold. Adequate retention time ensures that the casting is completely solidified, cooled and has a certain strength in the mold. It is usually advisable to keep the casting from deformation and cracking in the shortest time.

7.Summary
The application of aluminum alloy shell die casting technology in the electronics industry is important and extensive. By adopting aluminum alloy die-casting technology, high-precision and complex structure electronic equipment housings can be produced to meet the market’s demand for lightweight, high strength, good heat dissipation and EMI shielding performance. In the future, aluminum alloy shell die casting technology will continue to develop in the direction of high precision, high efficiency and environmental protection.