Motor housing casting: key technologies for design and manufacturing
Motor housing castings are metal shells used to wrap and protect motor rotors, stators and related components. They provide both structural support and heat dissipation management. They are usually produced using aluminum alloy high-pressure die-casting processes to obtain high-precision, thin-walled and complex geometric structures. Its thin walls, ribs and cooling channels bring quality challenges such as pores, shrinkage, deformation and internal stress, which can be avoided by optimizing the pouring system, simulation, vacuum assistance and reasonable design of wall thickness.
1.Definition and core functions of motor housing castings
Motor housing castings are shell parts used to encapsulate the core components of motors (such as stators, rotors, and windings), and are key basic parts of motor structures. Its core functions include:
Mechanical protection: withstand vibration and impact during motor operation, and protect internal precision components from external damage;
Heat management: quickly remove the heat generated by motor operation through the heat dissipation ribs on the shell surface and the inner cavity flow channel design;
Electromagnetic shielding: isolate electromagnetic radiation and prevent external dust and liquid from invading the inside of the motor;
Installation support: provide installation interfaces with the equipment base and transmission components to ensure the stability of the motor during operation.
The performance of motor housing castings directly affects the reliability, life and energy efficiency of the motor. Its quality requirements cover multi-dimensional indicators such as dimensional accuracy (such as mounting hole position accuracy ≤0.1mm), surface quality (such as roughness Ra≤12.5μm), mechanical properties (such as tensile strength ≥180MPa) and heat dissipation efficiency (such as thermal conductivity ≥100W/m・K).
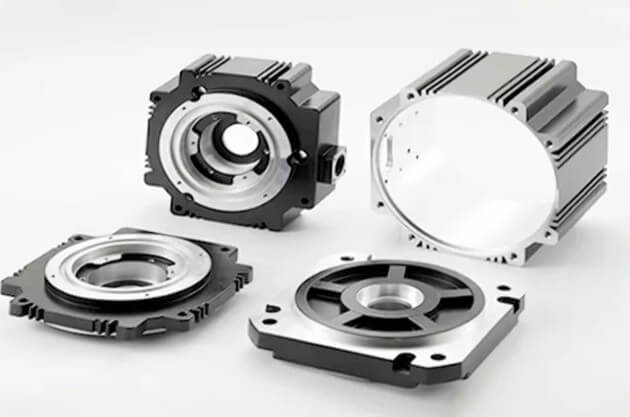
2.Material selection and performance of motor housing casting
(1) Selection principles of casting materials
1) Mechanical properties:
The motor housing needs to withstand a certain mechanical load, so the material is required to have good strength, rigidity and toughness.
2) Thermal conductivity:
The motor will generate heat during operation. Good thermal conductivity helps to dissipate heat and extend the life of the motor.
3) Casting performance:
The die casting process requires the material to have good fluidity, filling and solidification characteristics to ensure the quality of the casting.
4) Economic efficiency:
On the premise of meeting the performance requirements, select lower-cost materials to reduce the production cost of motor housing casting.
(2) Common die casting materials and their properties
1) Aluminum alloy
Advantages: low density, high strength, good thermal conductivity, excellent casting performance, and good corrosion resistance.
Disadvantages: relatively low hardness, poor high temperature strength.
Application: The most commonly used material, widely used in small and medium-sized motor housings, especially for occasions with high requirements for weight and heat dissipation performance.
2) Magnesium alloy
Advantages: lower density, higher specific strength, excellent shock absorption performance, and good casting performance.
Disadvantages: poor corrosion resistance, easy oxidation and combustion, and relatively high cost.
Application: Suitable for high-end motor housings with special requirements for weight and shock absorption performance.
3) Zinc alloy
Advantages: low melting point, good fluidity, easy die casting, high surface finish, and low cost.
Disadvantages: low strength and hardness, poor heat resistance.
Application: Suitable for small motor housings or occasions with low strength requirements.
4) Copper alloy
Advantages: excellent thermal and electrical conductivity, good corrosion resistance, and high strength.
Disadvantages: high density and high cost.
Application: suitable for large motor housings with special requirements for thermal conductivity.
(3) Material selection case analysis
Take a certain model of servo motor housing as an example. The motor requires light weight, good heat dissipation performance and high mechanical strength. After comprehensive comparison, ADC12 aluminum alloy was finally selected as the die casting material. ADC12 aluminum alloy has good strength and toughness, and excellent thermal conductivity, which can meet the heat dissipation requirements of the motor. In addition, the cost of aluminum alloy is relatively low, which conforms to the principle of economy.
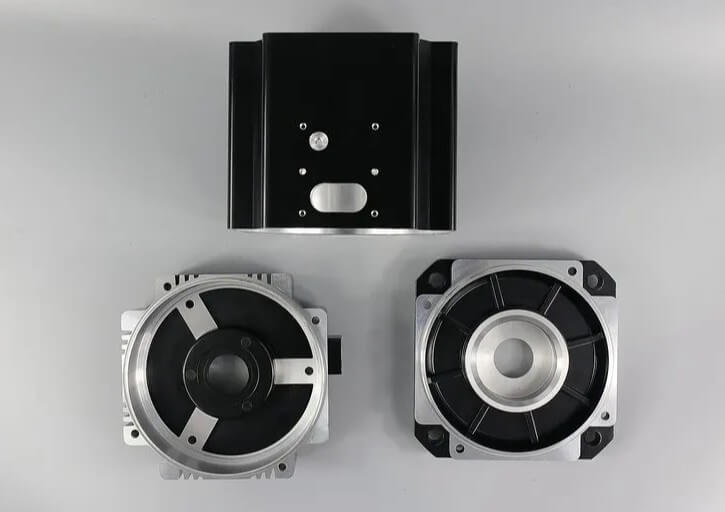
3.Definition and characteristics of die casting process
Die casting process is a metal processing method that uses high pressure to quickly inject molten metal into the mold cavity and then cools and solidifies to form precision castings. This process has the advantages of high production efficiency, high casting dimensional accuracy and good surface quality. It is widely used in many industries such as automobiles, electronics, and home appliances. The core of the die casting process lies in the high pressure and high speed filling process, which enables the molten metal to fill the complex shape mold in a very short time, thereby forming a complex structure and high precision casting.
4.Process optimization and performance improvement of motor housing casting(Taking die casting process as an example)
In order to further improve the quality and performance of motor housing die casting, process optimization can be carried out from the following aspects:
(1) Process parameter control
1) Pouring temperature and speed:
If the pouring temperature is too high, it will cause pores and shrinkage holes in the housing, while if it is too low, it will affect the filling effect. The appropriate pouring temperature is generally 680℃~720℃, and the pouring speed should be adjusted according to the structure and thickness of the housing to ensure smooth flow of the molten metal in the mold.
2) Mold temperature:
The control of mold temperature also has a great impact on the quality of the shell. If the mold temperature is too high, it is easy to cause mold sticking; if it is too low, it will affect the filling effect of the molten metal. Generally, the mold temperature should be controlled at 200℃~250℃.
3) Injection pressure ratio:
The size of the injection pressure ratio directly affects the density and mechanical properties of the shell. The appropriate injection pressure ratio should be selected according to the structure and material properties of the shell to ensure the density of the internal structure of the shell.
(2) Improve mold design and manufacturing
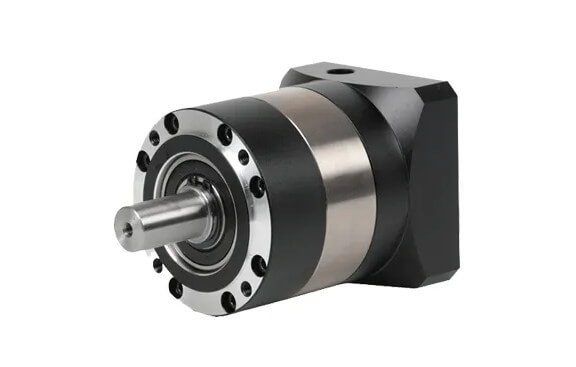
1) Optimize the pouring system:
A reasonable pouring system can ensure the smooth filling of the molten metal and reduce the occurrence of defects such as pores and shrinkage holes. The design of the pouring system should consider factors such as the flow direction, speed and filling time of the molten metal.
2) Strengthen the exhaust design:
When designing the mold, the exhaust problem should be fully considered, and reasonable exhaust grooves and exhaust holes should be set to reduce gas entrapment and improve the density of the shell.
3) Add cooling system:
Adding cooling system to the mold can effectively control the mold temperature, shorten the molding cycle and improve production efficiency. At the same time, uniform cooling can also reduce product deformation and improve dimensional accuracy.
4) Improve mold material performance:
Selecting high-performance mold materials, such as hot-working die steel, can improve the service life of the mold and the molding quality of the shell.
(3) Post-processing process:
1) Heat treatment process:
After die casting, solid solution quenching treatment is carried out to heat the shell to 520-540℃, followed by air quenching to make the Mg2Si strengthening phase supersaturated and retained at room temperature. Then secondary plastic forming is carried out to introduce 2-3% plastic strain and its internal stress. Finally, precipitation heat treatment/overaging treatment is carried out, heating to 170-180℃, keeping warm for 12 hours, eliminating internal stress and stabilizing the size.
2) Surface treatment process:
Surface treatment can choose electrophoretic coating, anodizing and other processes. Electrophoretic coating uses electrostatic action to evenly adhere the paint to the shell surface to improve corrosion resistance and aesthetics. Anodic oxidation forms a dense oxide film on the surface of the shell, enhancing wear resistance and corrosion resistance.
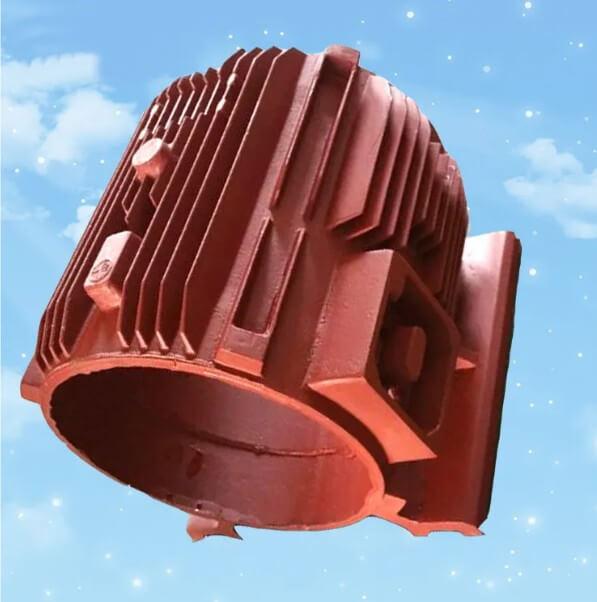
5.Common problems and solutions for motor shell casting
(1) Bubble and pore problems
1) Problem:
During the die casting process, due to the defects of the high-pressure casting process, bubbles and pores are easily generated inside the casting, which will seriously affect the quality and performance of the casting.
2) Measures:
Using semi-solid die casting technology, through vigorous stirring or adding grain refiners, the metal slurry is die-casted in a semi-solid state, thereby obtaining a dense and pore-free casting.
(2) Shrinkage and shrinkage:
1) Problem:
When the molten metal changes from liquid to solid, the volume decreases. Shrinkage cavities are formed without metal liquid replenishment, which usually occur at slower solidification sites.
2) Measures:
Increase the shrinkage pressure, reduce the mold temperature at the shrinkage location, and increase the shrinkage channel, such as increasing the runner volume or redesigning the water inlet location.
(3) Hammer stuck
1) Problem:
Hammer stuck is a common problem in the die casting process. The main reasons are that the temperature of the hammer and the barrel is too high or there are too many impurities in the material.
2) Measures:
Measure and control the temperature regularly, select high-quality alloy materials, and ensure that no impurities are mixed in the return process.
(4) Die casting cracking
1) Problem:
Thin-walled products are prone to cracking when die casting. The main reasons may be material problems, poor mold opening or improper process parameter selection.
2) Measures:
Control the waste ratio to no more than 30%, optimize the layout of mold opening and cooling water, and adjust the mold retention time and ejection delay time.
(5) Metal splashing
1) Problem:
Metal splashing is usually caused by loose mold closing, insufficient clamping force or non-parallel mold installation.
2) Measures:
Reinstall the mold, increase the clamping force, adjust the die casting machine to keep the moving and fixed mold mounting plates parallel, and add support plates to improve the rigidity of the sleeve plate.
6.Application fields of motor housing casting
Due to its advantages of high efficiency, high precision and cost-effectiveness, motor housing casting technology has been widely used in many fields. The following are several major application fields of motor housing casting:
(1) New energy vehicle industry:
With the global emphasis on environmental protection and energy conservation, the new energy vehicle (NEV) market has grown rapidly. As one of the core components of new energy vehicles, the motor housing casting technology is crucial to improving vehicle performance and reducing costs. Motor housing casting can achieve lightweight and improve energy efficiency while meeting the requirements of new energy vehicles for endurance and power performance.
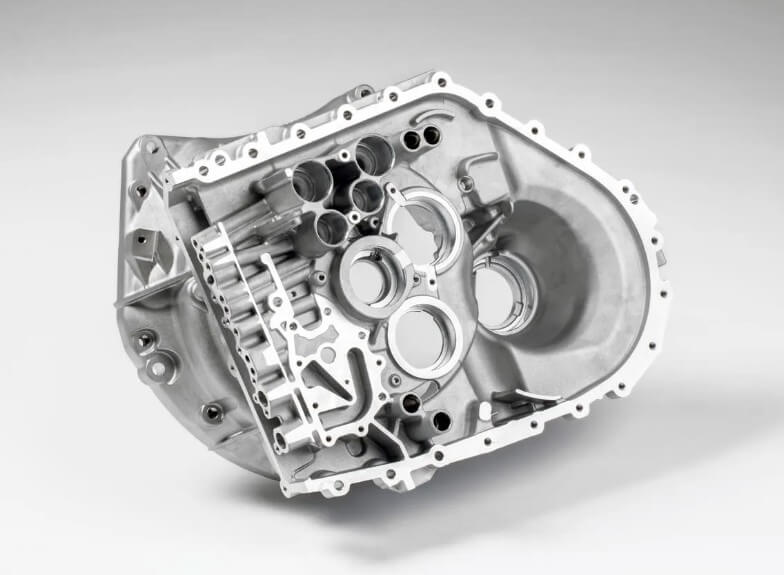
(2) Traditional automobile industry:
In traditional fuel vehicles, motor housing casting technology also plays an important role. Die casting parts can be used in key components such as engines and gearboxes. By optimizing the design and manufacturing process, fuel efficiency can be improved and emissions can be reduced.
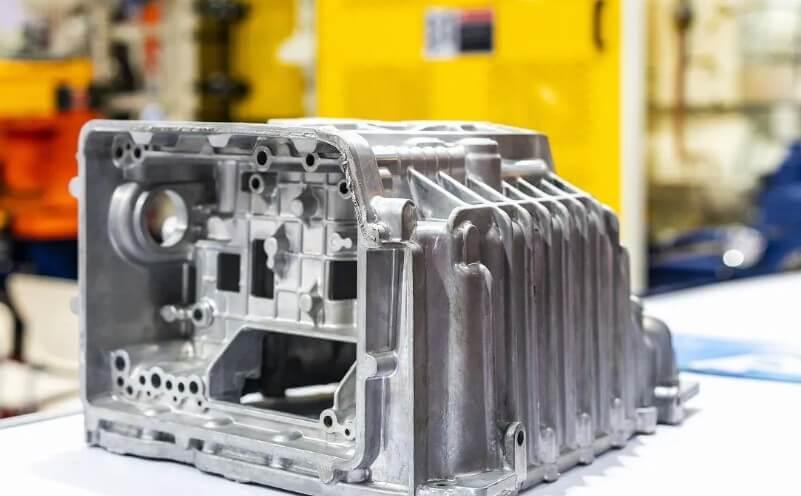
(3) Home appliance industry:
Motor housing casting technology is also widely used in the home appliance field, such as motor housings of home appliances such as air conditioners, refrigerators, and washing machines. Through die casting technology, motor housings with complex structures and high precision can be produced to meet the requirements of household appliances for quietness, efficiency and durability.
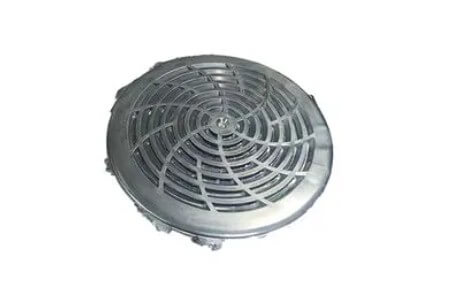
(4) 5G communication and smart terminals:
With the popularization of 5G technology and the development of smart terminal equipment, motor housing casting technology has also found applications in these fields. For example, the housings of 5G base stations and smart terminal equipment need to have high strength and light weight, and die casting technology can meet these requirements.
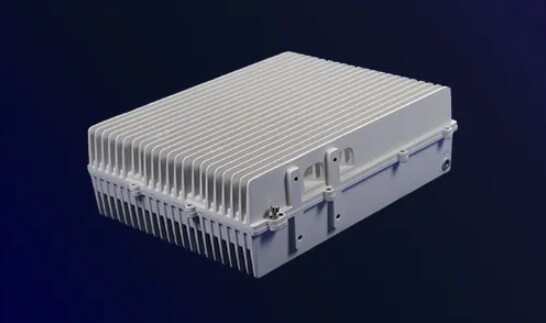
(5) Energy storage equipment:
With the rise of renewable energy, the demand for energy storage equipment is also growing. Motor housing casting technology can be used to manufacture the housings of energy storage equipment to improve the overall performance and safety of the equipment.
7.Summary
In summary, motor housing casting technology has a wide range of applications in new energy vehicles, traditional vehicles, household appliances, 5G communications and smart terminals, and energy storage equipment. With the continuous advancement of technology and the expansion of application fields, motor housing casting technology will continue to play an important role in modern manufacturing.