metallic glass copper mold casting: key technology analysis
Metallic glass copper mold casting is a technology that combines modern technology with traditional craftsmanship. It injects molten metal glass into a copper mold for cooling and molding to obtain products with excellent performance. This technology has been widely used in modern industry. This article will introduce the basic principles, process flow, key technologies, advantages and disadvantages, and application field analysis of metallic glass copper mold casting.
1.Introduction to metallic glass copper mold casting technology
(1) Concept and characteristics of metal glass
Metal glass, also known as amorphous alloy, is a new type of alloy material synthesized by modern rapid solidification metallurgical technology. It is composed of metal elements, but its atomic structure is disordered, similar to glass.
Characteristics:
1) High strength: The strength of metal glass is far superior to that of traditional metals. For example, the strength of iron-based metal glass can reach 3~6GPa.
2) High elasticity: It has excellent elastic recovery ability and can easily rebound to its original shape after deformation.
3) Corrosion resistance: It has high resistance to various corrosive environments.
4) Soft magnetism: Some metallic glasses have excellent soft magnetic properties and are suitable for magnetic material applications.
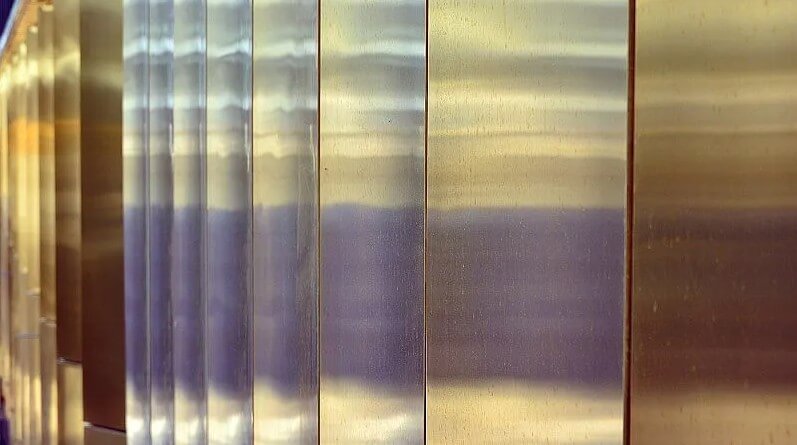
(2) The concept and importance of copper mold casting technology
Copper mold casting technology is a method of casting using copper molds. In the preparation of metallic glass, copper mold casting technology forms an amorphous structure by quickly injecting molten metal into a copper mold and using the high thermal conductivity of copper to achieve rapid cooling.
Importance:
1) Improve molding efficiency: The high thermal conductivity of the copper mold allows the molten metal to solidify quickly, shortening the production cycle.
2) Ensure product quality: Copper mold casting can obtain products with precise dimensions and smooth surfaces, improving product performance.
3) Wide application: In the manufacture of metallic glass, copper mold casting technology is one of the key methods for preparing bulk amorphous alloys and is suitable for the production of high-performance components.
Summary:
In summary, metallic glass has broad application prospects in many fields due to its unique properties, and copper mold casting technology, as one of its key preparation technologies, is of great significance for promoting the industrial application of metallic glass.
2.Basic principles of metallic glass copper mold casting
The basic principle of copper mold casting of metallic glass is to use the high thermal conductivity of the copper mold to cool and solidify the molten metallic glass in a very short time, thereby forming a metallic glass product with an amorphous structure. The rapid thermal conductivity of the copper mold can quickly cool the molten metallic glass, avoiding the occurrence of the crystallization process, thereby obtaining a product with excellent mechanical, physical and chemical properties.
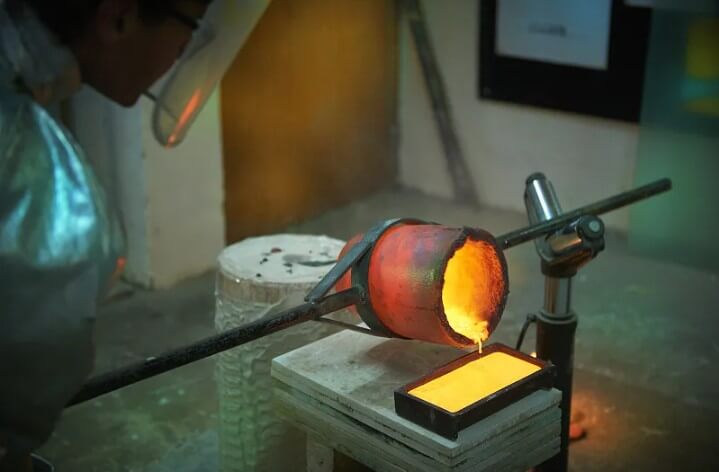
3.Process flow of metallic glass copper mold casting
Metallic glass copper mold casting is a precision manufacturing process that combines the properties of metal and glass to produce high precision parts, the following is a detailed flow of the process:
(1) Mold preparation:
First, a copper mold needs to be prepared. The design of the copper mold must be precise to ensure that the size and shape of the final product meet the requirements. The copper mold is usually processed by CNC machine tools, and the surface is polished to improve the finish.
(2) Preparation of metallic glass raw materials:
The metallic glass raw materials are mixed in a specific ratio and placed in a high-temperature furnace for melting. Metallic glass is a special alloy with good fluidity and formability.
(3) Melting:
The raw materials are melted at high temperature to completely melt and reach the required temperature. This step is crucial because temperature control directly affects the quality and performance of the final product.
(4) Pouring:
The molten metal glass liquid is poured into the pre-heated copper mold. The temperature control of the copper mold is very critical, which is to ensure the fluidity of the metal glass liquid and prevent it from cooling too quickly.
(5) Cooling and solidification:
The metal glass liquid injected into the copper mold is quickly cooled and solidified in the copper mold. Since the copper mold has excellent thermal conductivity, it can quickly conduct heat away, thereby achieving rapid solidification.
(6) Demolding and post-processing:
After the metal glass is completely solidified, the product is removed from the copper mold. Subsequently, the product is subjected to necessary post-processing, such as grinding and polishing, to remove surface defects and improve surface finish.
(7) Quality inspection:
Quality inspection of the finished product, including dimensional accuracy, surface quality, performance testing, etc., is carried out to ensure that the product meets the design requirements and industry standards.
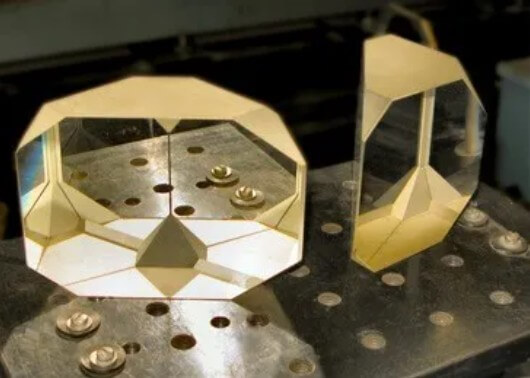
4.Analysis of key technologies for metallic glass copper mold casting
Copper mold casting, as an important method of metal glass preparation, has key technologies that are crucial for obtaining high-performance metal glass products. The key technologies of metallic glass copper mold casting, including mold design, melt preparation, casting process and post-processing.
(1) Mold design
Mold design is the basis of copper mold casting, and its rationality directly affects the formation and quality of metallic glass. Copper molds are usually made of copper alloys with high thermal conductivity, which can quickly cool the melt and promote the formation of amorphous structure. The design of the mold needs to consider the following aspects:
1) Cooling rate:
The formation of metallic glass requires an extremely high cooling rate, usually between 105~106K/s. The thermal conductivity of the mold is the key, and copper alloys with high thermal conductivity are usually selected as mold materials.
2) Mold structure:
The structural design of the mold should ensure that the melt can be filled evenly to avoid defects such as pores and shrinkage holes. At the same time, the opening and runner design of the mold should be conducive to the flow and filling of the melt.
(2) Melt preparation
Melt preparation is one of the key steps in copper mold casting. The composition and temperature of the melt have an important influence on the formation of metallic glass. Melt preparation mainly includes the following links:
1) Composition design:
The composition design of metallic glass needs to consider its glass-forming ability. Usually, a multi-element alloy system is used, such as Zr-based, Cu-based, Fe-based, etc. Reasonable composition design can significantly improve the glass-forming ability and performance of metallic glass.
2) Melting process:
The temperature and composition uniformity of the melt need to be strictly controlled during the melting process. Usually, induction melting, arc melting and other methods are used to avoid oxidation and contamination in the melt.
3) Purification treatment:
Impurities and gases in the melt will affect the quality of metallic glass, so purification treatment is required. Common purification methods include vacuum treatment, inert gas protection, etc.
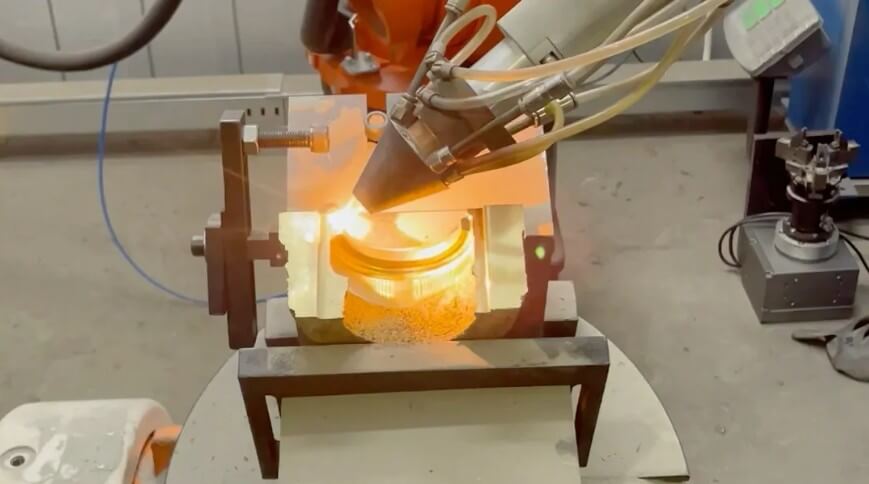
(3) Casting process
The casting process is the core link of copper mold casting, and its parameter control plays a decisive role in the formation and quality of metallic glass. The casting process mainly includes the following steps:
1) Pouring temperature:
The pouring temperature needs to be controlled within an appropriate range. Too high or too low a pouring temperature will affect the formation of metallic glass. Generally, the pouring temperature should be slightly higher than the liquidus temperature of the alloy.
2) Pouring speed:
The pouring speed needs to match the cooling rate of the mold to ensure that the melt can evenly fill the mold. Too fast or too slow a pouring speed may lead to defects.
3) Pressure control:
In some cases, it is necessary to apply a certain pressure to the melt to facilitate its filling of the mold and improve the density of the product.
(4) Post-processing
Post-processing is an important part of improving the performance of metallic glass, mainly including heat treatment, machining and surface treatment.
1) Heat treatment:
Appropriate heat treatment can improve the structure and properties of metallic glass, such as improving its strength and toughness. The heat treatment process needs to be designed according to the specific alloy system and requirements.
2) Machining:
Machining can be used to remove burrs and defects of metallic glass products and improve their dimensional accuracy and surface quality. It should be noted that metallic glass has a high hardness, so it is necessary to select appropriate processing methods and tools.
3) Surface treatment:
Surface treatment can be used to improve the surface properties of metallic glass, such as wear resistance and corrosion resistance. Common surface treatment methods include plating, coating, etc.
5.Analysis of the advantages and disadvantages of metallic glass copper mold casting
Metallic glass copper mold casting is a new material preparation method that combines the characteristics of metallic glass and copper mold casting process. The following is an analysis of the advantages and disadvantages of metallic glass copper mold casting:
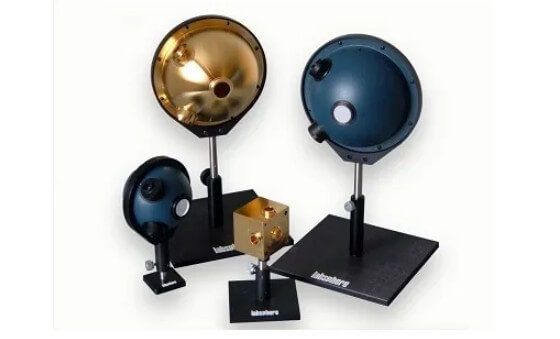
(1) Advantages
1) Reliable quality:
During the metallic glass copper mold casting process, the metal liquid can completely fill the mold, making the internal structure of the part more compact and uniform, thus ensuring a more reliable quality of the part.
2) Compact structure:
The structure of the casting is compact, meets certain mechanical strength requirements, has high rigidity and wear resistance, and can resist external forces such as vibration and impact.
3) High processing accuracy:
The metallic glass copper mold casting process provides castings with high dimensional accuracy and low surface roughness values to meet stringent dimensional and mounting accuracy requirements.
4) Flexible molding:
The metallic glass copper mold casting process can produce complex parts and geometric shapes to meet different design requirements.
5) Strong corrosion resistance:
The casting has strong corrosion resistance and can resist the erosion of corrosive media, extending the service life of the parts.
6) Improve the environment:
Sand cores are rarely used in the metallic glass copper mold casting process, which reduces the emission of dust and harmful gases and reduces pollution to the environment.
(2) Disadvantages
1) High cost:
The metal mold manufacturing cycle is long and the cost is high, which is suitable for mass production to reduce costs.
2) No air permeability:
The metal mold itself has no air permeability, and certain measures must be taken to guide the air in the mold cavity and the gas generated by the sand core, otherwise it is easy to produce pores.
3) Easy to crack:
The metal mold has no yield, and the casting is prone to cracks and deformation when solidifying.
4) Poor high temperature resistance:
When exposed to high temperature environment, there may be a risk of deformation or cracking.
5) Difficult to repair:
Once damaged or design changes are required, a more complex repair process may be required.
6.Application areas of metallic glass copper mold casting
(1) Electronic devices:
Metallic glass copper mold casting can be used to manufacture high-performance electronic devices, such as transformers, sensors, etc., because of its excellent electromagnetic properties, it can improve the efficiency and stability of the device.
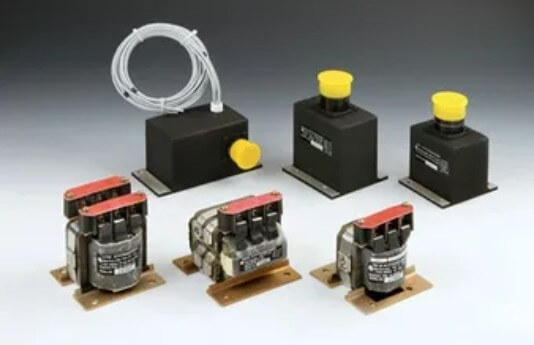
(2) Aerospace:
In the field of aerospace, parts made by metallic glass copper mold casting have high strength, high temperature resistance and corrosion resistance, and are suitable for manufacturing lightweight and high-strength structural parts for aircraft and rockets.
(3) Medical devices:
Because metallic glass copper mold casting can produce parts with high precision and smooth surface, it is widely used in the manufacture of medical devices, such as surgical instruments, prostheses, etc.
(4) Precision instruments:
Metallic glass copper mold casting technology can produce parts with high dimensional accuracy and good surface quality, which is very suitable for manufacturing key components in precision instruments, such as optical instruments, analytical instruments, etc.
(5) Sports equipment:
In the field of sports equipment, metallic glass copper mold casting can be used to manufacture golf clubs, bicycle frames, etc., which have the advantages of light weight, high strength and good feel.
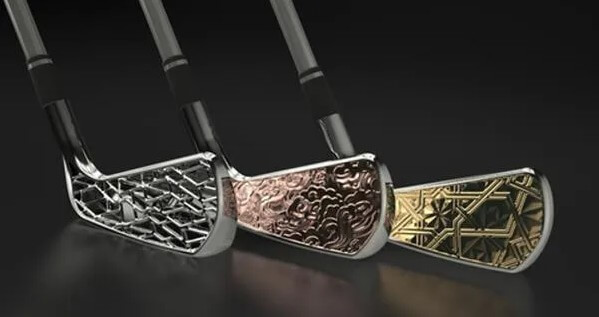
(6) Jewelry:
Metallic glass copper mold casting can produce jewelry with unique texture and luster, so it is used in the jewelry industry to produce exquisite and artistic jewelry.
7.Summary
These applications demonstrate the versatility and breadth of the metallic glass copper mold casting technology, and its unique advantages make it play an important role in many industries.
What do you think?
[…] a new type of material, bulk metallic glass has many unique properties, such as high strength, high hardness, excellent elastic limit and good […]
[…] Bulk metallic glass (BMG), also known as amorphous alloy, is a new type of material with unique structure and excellent properties. Let’s talk about the key technologies and advantages of amorphous alloys mentioned above. […]
[…] article will delve into the definition and importance of glass casting, principles and processes, special glass casting technology, advanced glass casting technology, […]
[…] Copper mold casting is a technology that uses molds made of copper alloys for metal casting. Due to its excellent thermal conductivity, the copper mold can quickly absorb and dissipate the heat of the molten metal during the casting process, thereby achieving rapid cooling. This rapid cooling feature enables the casting to obtain a high surface finish and fine microstructure. The main characteristics of copper mold casting include: […]
[…] manufacturing and processing of aluminum metal casting molds is a complex and delicate process, which requires strict control of the quality of each link. […]