Metal coatings: a protective tool for industrial manufacturing
In modern industrial manufacturing, metal coating technology plays a vital role. From cars to aerospace vehicles, from medical devices to everyday home appliances, metal coatings are everywhere. So, why are metal coatings so important? What significant advantages can metal coating types and preparation techniques bring?
1.Definition and importance of metal coating technology
Metal coating technology is an engineering technology that changes or enhances the surface properties of the base material by applying one or more layers of metal or alloy films on the surface of the base material. This technology is widely used to improve the wear resistance, corrosion resistance, high temperature oxidation resistance and other specific functional properties of materials.
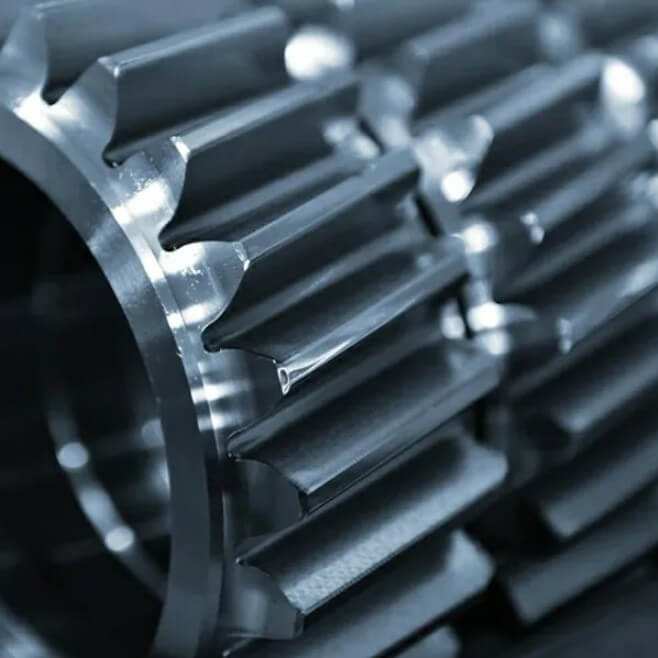
In modern industry, metal coating technology is widely used in aerospace, automobile manufacturing, medical equipment, construction and other fields because it can significantly extend the service life and improve performance of materials. With the advancement of science and technology and the increase in industrial demand, metal coating technology continues to develop, and new materials and new processes are constantly updated, which promotes the continuous expansion of the application scope and efficiency of coating technology.
2.Types and applications of metal coatings
(1) Anti-corrosion coating
1) Function
Anti-corrosion coatings are mainly used to protect base materials from chemical corrosion in the environment and extend the service life of materials. Common anti-corrosion coatings include zinc, aluminum and their alloy coatings, which protect the substrate from corrosion through the mechanism of sacrificial anodes.
2) Application examples
Anti-corrosion coatings are widely used in marine engineering, automobile, construction and other industries, especially in structural parts working in harsh environments, such as offshore platforms, bridges and chemical equipment. For example, zinc coating is often used for the external protection of steel structural parts. It is applied to the surface of the substrate through electroplating or thermal spraying processes to form a dense protective film that can effectively prevent the erosion of oxygen and moisture.
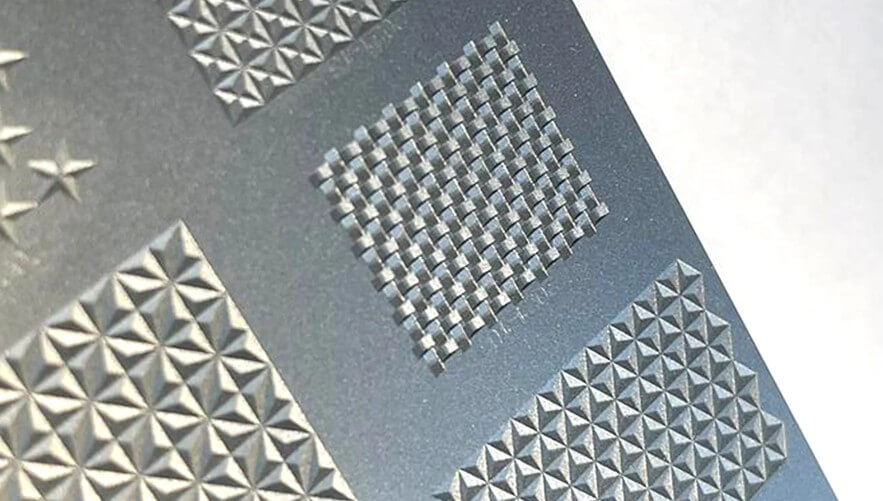
(2) Wear-resistant coating
1) Function
Wear-resistant coatings are used to improve the wear resistance of materials and reduce friction and wear. They are often used in mechanical parts, tools and molds, etc.
2) Application examples
For example, cemented carbide coatings such as tungsten carbide and titanium nitride are widely used in surface treatment of cutting tools and molds due to their high hardness and wear resistance, significantly extending the service life of tools and improving processing efficiency. Wear-resistant coatings are also widely used in automotive engine parts, aerospace components, mining machinery and other fields, and can maintain stable performance in high temperature, high pressure and high friction environments.
(3) Thermal barrier coating
1) Function
Thermal barrier coatings are mainly used in high-temperature environments, such as aerospace engines and gas turbines, to isolate high-temperature gases and protect the substrate from high-temperature oxidation and thermal corrosion. This type of coating is usually composed of ceramic materials, which can effectively reduce the operating temperature of the base material and improve its thermal stability and service life.
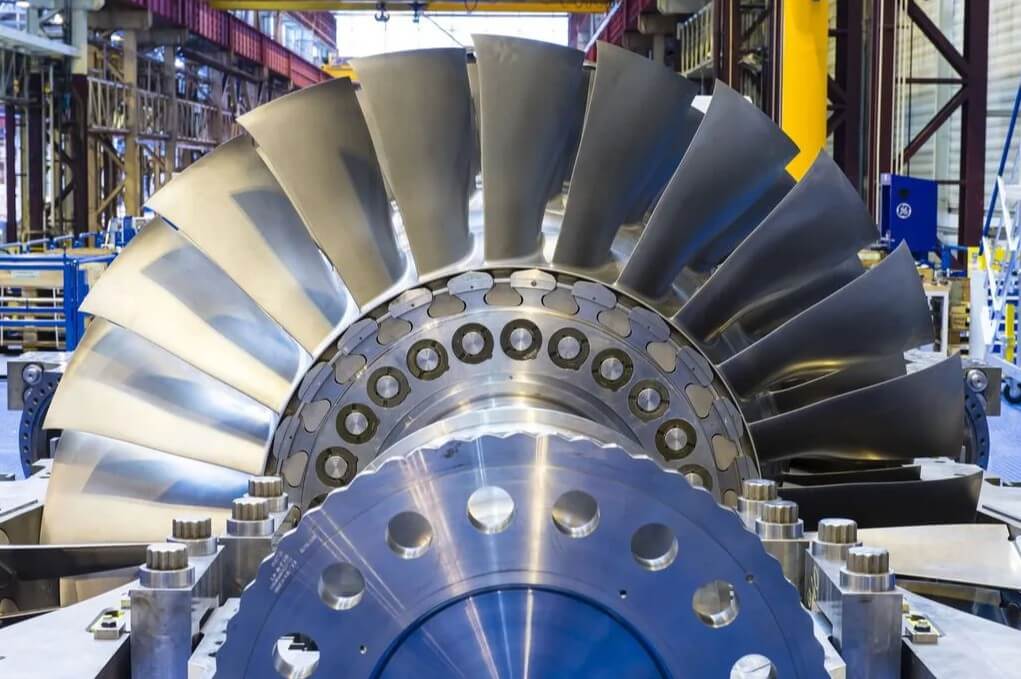
2) Application examples
For example, yttrium oxide partially stabilized zirconia (YSZ) coating is widely used in the hot-end components of aerospace engines due to its excellent thermal stability and insulation properties, which can significantly improve the engine’s operating efficiency and reliability.
Thermal barrier coatings also have important applications in the energy industry. For example, applying a thermal barrier coating to the surface of the hot-end components of a gas turbine can effectively reduce the component’s operating temperature and improve its thermal stability and service life.
(4) Conductive coating
1) Function
Conductive coatings are mainly used in the electronics industry to provide good electrical conductivity.
2) Application examples
For example, silver and copper coatings are widely used in printed circuit boards, electronic components and connectors due to their excellent conductive properties. In the field of microelectronics, conductive coatings are used to create conductive lines, electrodes and shielding layers, which can improve the performance and reliability of electronic devices.
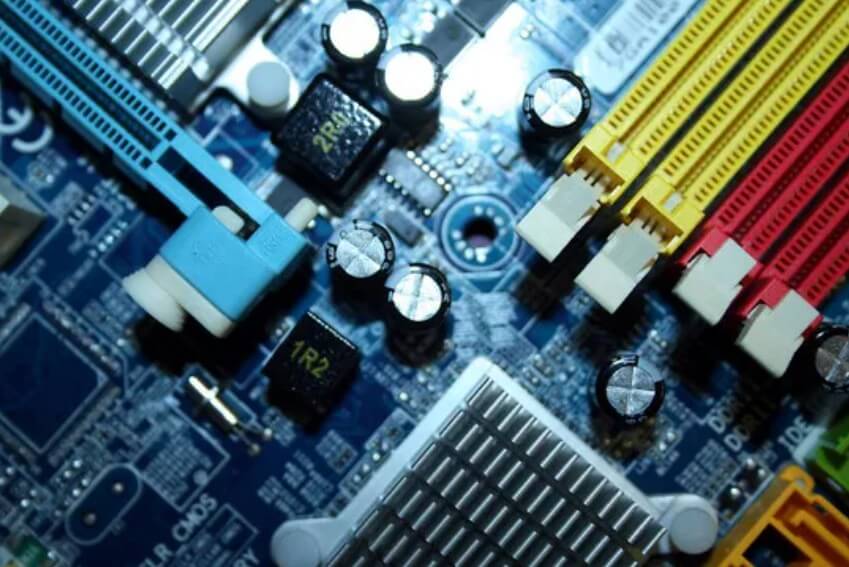
Conductive coatings are also used in other fields, such as electromagnetic shielding and anti-static coatings, which can effectively prevent electromagnetic interference and static electricity accumulation.
3.Preparation technology and application of metal coatings
(1) Electroplating
1) Principles and functions
Electroplating is one of the most common metal coating methods. Its principle is to reduce and deposit metal ions on the surface of the substrate through electrolysis to form a uniform metal coating. Electroplating can not only improve the corrosion resistance of the material, but also give it good conductivity, beautiful appearance and certain special functions. For example, chromium plating can improve hardness and wear resistance and is widely used in automobile parts, decorations, etc.; nickel plating is often used to improve anti-corrosion capabilities and increase surface gloss.
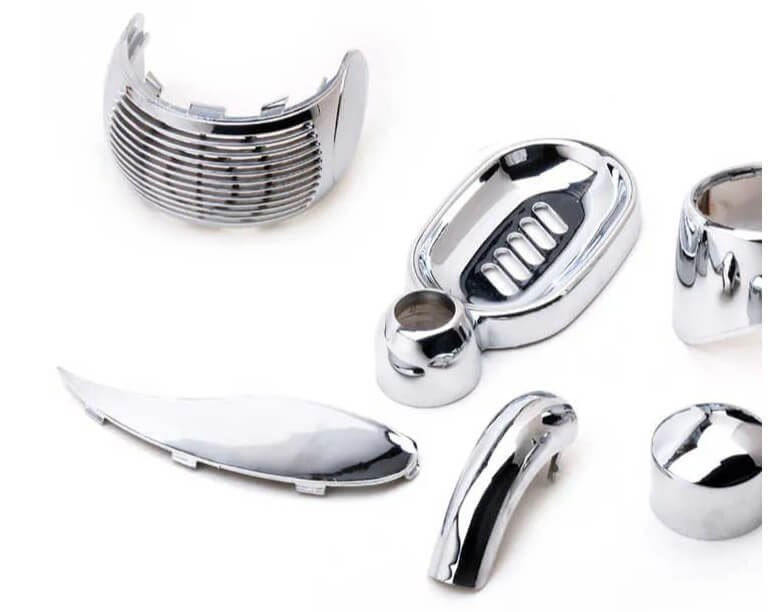
2) Application examples
Some key components in the aerospace field require extremely high corrosion resistance, and their service life can be effectively extended by electroplating nickel or nickel alloys. In the electronics industry, electroplating precious metals such as gold and silver can significantly improve the conductivity and reliability of components.
(2) Thermal spraying
1) Principles and functions
Thermal spraying is a method that uses a heat source to heat metal or alloy powder to a molten or semi-molten state, and then sprays it onto the substrate surface at high speed to form a coating. Thermal spray coating has the characteristics of controllable thickness, strong bonding force, and wide application range. It is especially suitable for large areas and occasions with high wear resistance requirements.
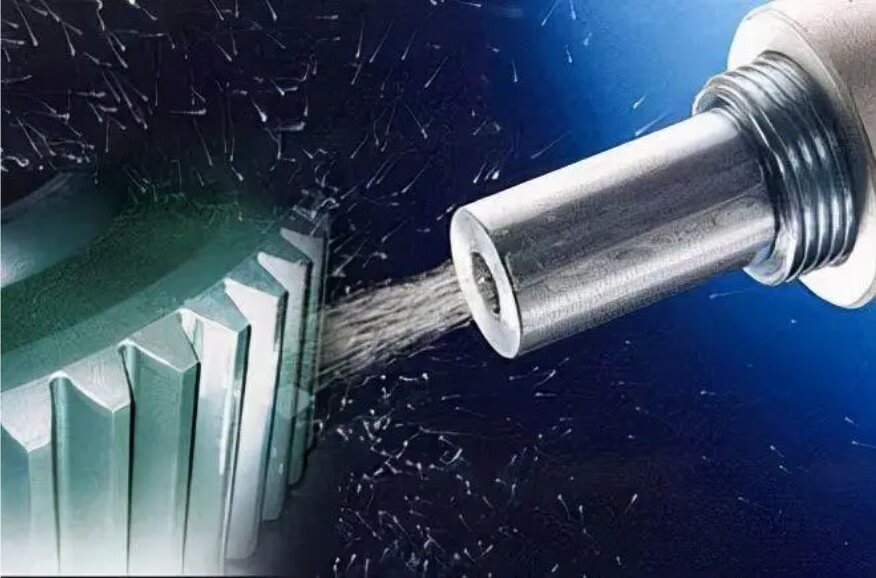
2) Application examples
Thermal spraying technology is widely used in ship manufacturing. By spraying aluminum or zinc coating on the surface of the hull, its seawater corrosion resistance can be significantly improved. Spraying ceramic coatings on the blades of thermal power equipment can effectively improve their resistance to high-temperature oxidation and corrosion.
(3) Physical vapor deposition (PVD)
1) Principles and functions
Physical vapor deposition is a technology that uses physical methods to convert material sources into gas phase atoms, molecules or ions under vacuum conditions, and then deposits them on the surface of a substrate to form a metal coating. PVD coating has the characteristics of thin thickness, high hardness, good wear resistance, and environmental friendliness, and is widely used in cutting tools, molds, decorations and other fields.
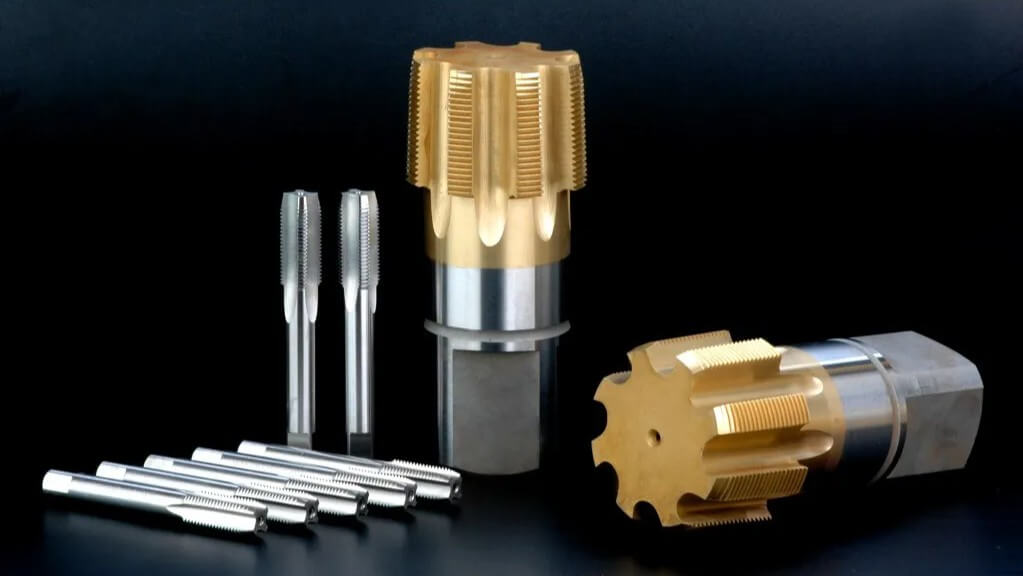
2) Application examples
PVD technology is widely used in high-end watches, eyeglass frames and other decorations. By depositing coatings of different colors and functions, the aesthetics and wear resistance of the product can be significantly improved. Depositing titanium nitride, chromium nitride and other coatings on cutting tools can significantly improve their service life and cutting performance.
(4) Chemical vapor deposition (CVD)
1) Principles and functions
Chemical vapor deposition is a technology that deposits solid substances on the surface of a substrate through chemical reactions. CVD coating has the characteristics of good uniformity, high purity and strong bonding force, and is widely used in semiconductor, aerospace, high-temperature structural materials and other fields.
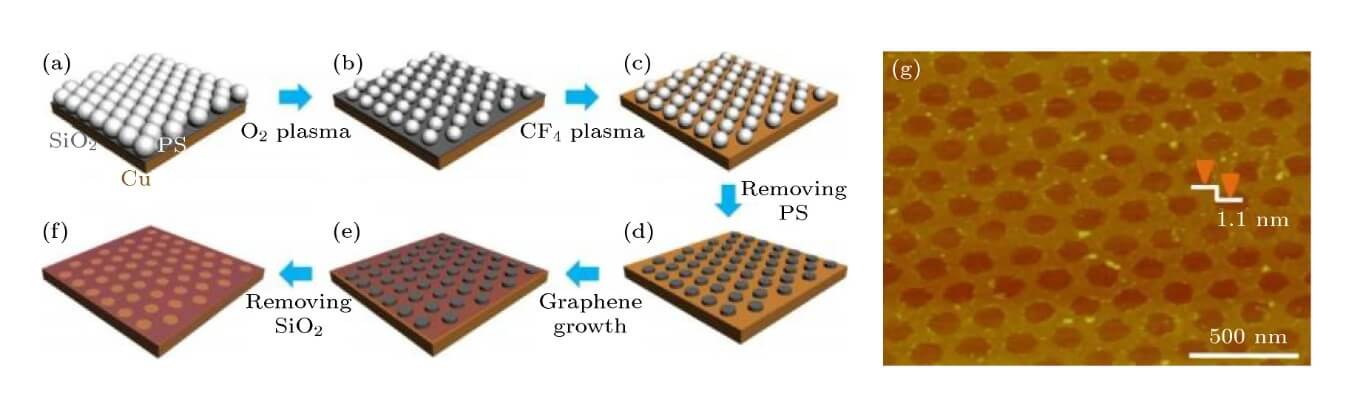
2) Application examples
CVD technology is widely used in semiconductor manufacturing. By depositing thin film materials such as silicon and silicon nitride, various high-performance electronic components can be prepared. Depositing antioxidant coatings on high-temperature structural materials can significantly improve their high-temperature performance and service life.
4.Advantages and challenges of metal coating technology
(1) Advantages
1) Improve material performance:
Metal coatings can significantly improve the corrosion resistance, wear resistance, conductivity and other properties of the base material, extend the service life of the material, and improve its performance.
2) Cost savings:
By applying high-performance metal coatings to inexpensive substrates, the same results as using high-performance materials can be achieved, thereby saving costs.
3) Versatility:
Metal coating technology can prepare coatings with different functions according to different needs, such as wear-resistant coatings, anti-corrosion coatings, conductive coatings, decorative coatings, etc.

4) Environmental protection:
With the advancement of technology, some environmentally friendly metal coating technologies, such as PVD, CVD, etc., have gradually been widely used, reducing environmental pollution.
(2) Challenge
1) Coating quality:
The performance of metal coatings is closely related to its quality. The thickness, uniformity, and bonding strength of the coating will all affect its effectiveness. Therefore, how to control coating quality is an important challenge facing metal coating technology.
2) Process complexity:
Some metal coating technologies, such as CVD, PVD, etc., have relatively complex processes, high equipment requirements, and relatively high costs.
3) Environmental issues:
Some traditional metal coating technologies, such as electroplating, have certain environmental pollution problems. How to develop environmentally friendly metal coating technology and reduce the impact on the environment is an important direction for the development of metal coating technology.
5.Design and optimization of metal coatings
(1) Selection of coating materials
Choosing the right coating material is key to designing metal coatings. The most appropriate coating material needs to be selected based on the properties of the base material, working environment and performance requirements.
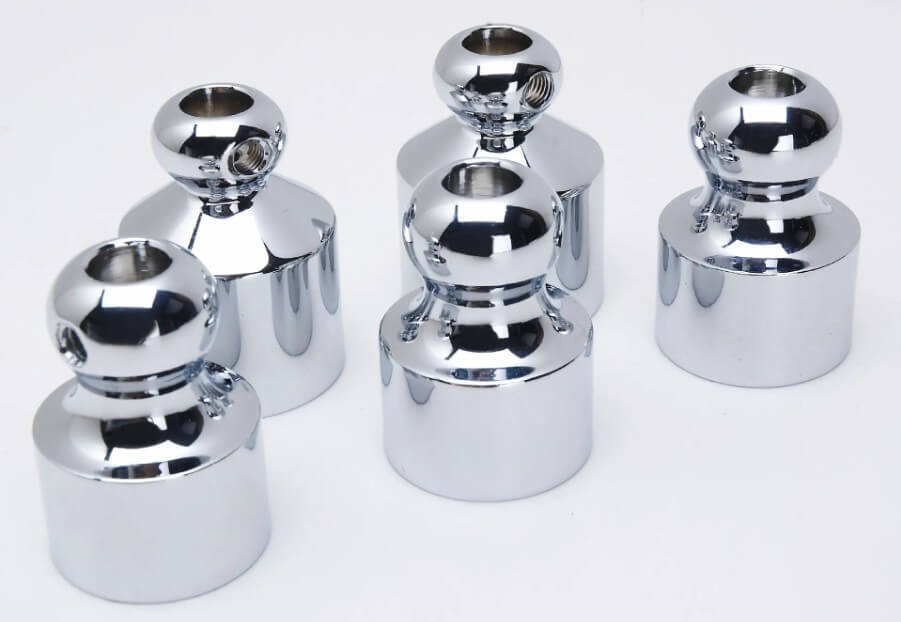
For example, in high-temperature environments, coating materials with high melting points and good oxidation resistance should be selected, such as ceramic coatings or high-temperature alloy coatings. In corrosive environments, coating materials with good corrosion resistance should be selected, such as nickel-based alloy or titanium-based alloy coatings.
(2) Control of coating thickness
Coating thickness has a significant impact on coating performance. A coating that is too thin may not provide adequate protection, while a coating that is too thick may result in increased costs and reduced performance. Therefore, the coating thickness needs to be reasonably controlled according to specific application scenarios.
For example, in wear-resistant coatings, the coating thickness should be sufficient to resist wear, but in thermal barrier coatings, the coating thickness should be appropriate to avoid coating failure due to thermal stress.
During the manufacturing process, precise control technology and detection methods are required to ensure the uniformity and consistency of the coating thickness. For example, the thickness of the coating can be precisely controlled through electroplating technology, thin film coatings with uniform thickness can be prepared through CVD and PVD technology, and spraying parameters can be adjusted through thermal spraying technology to control the thickness and structure of the coating.
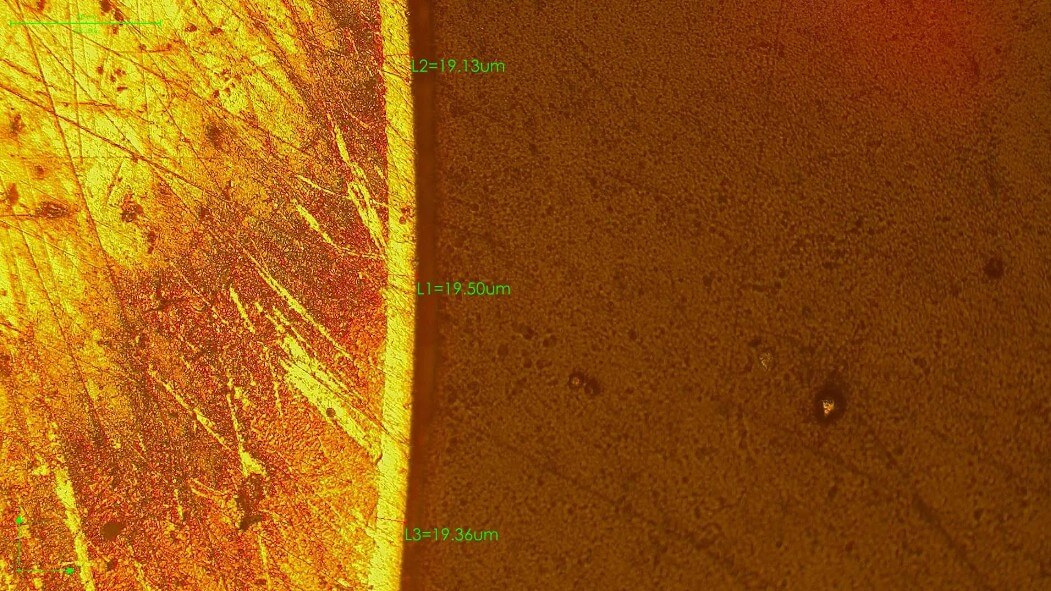
(3) Optimization of coating structure
Coating structure also has an important influence on coating performance. By optimizing the coating structure, the overall performance of the coating can be improved. For example, the use of a multi-layer coating structure can improve the wear resistance and corrosion resistance of the coating, and the use of a gradient coating structure can improve the thermal stability and bonding strength of the coating.
In multi-layer coatings, the selection of materials and control of thickness of each layer need to be carefully designed to ensure compatibility and synergy between the layers. In gradient coating, the composition and structure of the coating gradually change along the thickness direction, which can effectively reduce the stress inside the coating and improve the stability and service life of the coating.
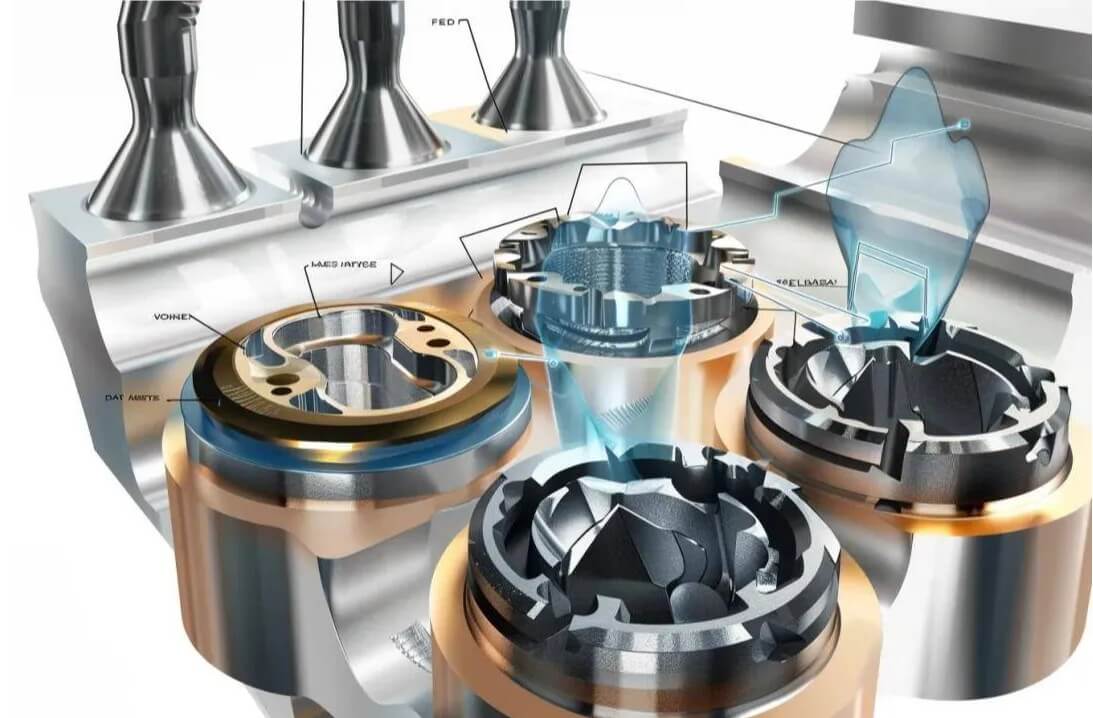
For example, in thermal barrier coatings, the use of gradient structures can reduce thermal stress and improve the thermal stability and thermal shock resistance of the coating. In wear-resistant coatings, the use of multi-layer structures can improve the hardness and toughness of the coating, and improve its wear resistance and service life.
(4) Post-processing process
Post-treatment processes also play an important role in improving coating properties. For example, heat treatment can improve the microstructure of metal coatings and increase the hardness and wear resistance of the coating; surface modification can improve the surface properties of metal coatings and improve their corrosion resistance and fatigue resistance.
The selection of post-treatment process should be reasonably designed based on the properties of the coating material and application requirements to ensure the best performance of the coating.
6.Summary
The application of metal coatings not only improves the quality and performance of products, but also extends their service life, bringing huge economic benefits to all walks of life. With the continuous advancement of science and technology, metal coating technology is also constantly innovating, and its application prospects will be broader.