Metal casting mold materials classification, characteristics and failure investigation
In the metal casting production process, the selection of metal casting mold materials is crucial, and its performance determines the durability of the mold and the precision of the cast products. However, due to the long-term high temperature, high pressure and mechanical impact environment, mold materials are prone to thermal fatigue, wear, corrosion and other failure problems.
Therefore, an in-depth study of metal casting mold materials classification, performance and failure mechanism, to improve productivity and extend the life of the mold is of great significance.
1.The main types of metal casting mold materials
At present, the metal casting mold materials mainly include the following categories:
(1) steel category
1) hot work mold steel (such as H13 steel, SKD61 steel):
Has good high temperature resistance and high thermal fatigue resistance, suitable for die casting and gravity casting and other high temperature casting process.
2) cold mold steel (such as D2 steel, Cr12MoV steel):
Mainly used for low-temperature casting environment, wear resistance is better, but heat resistance is poor.
3) stainless steel:
Apply to special casting process, such as investment casting, can improve the corrosion resistance of the mold and precision.
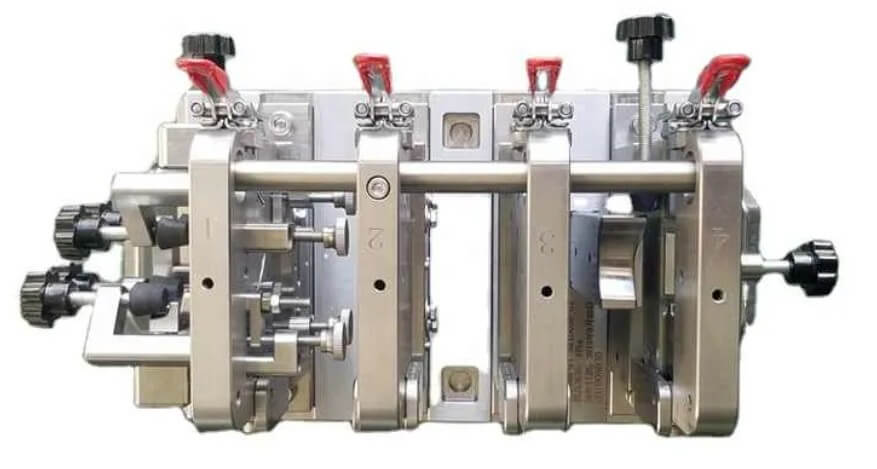
(2) cast iron
1) Gray cast iron:
Good processing performance, low cost, suitable for simple low-pressure casting mold.
2) ductile cast iron:
Compared with gray cast iron has higher toughness and heat resistance, suitable for higher requirements of the casting process.
(3) copper alloy
1) beryllium copper (BeCu):
Has excellent thermal conductivity and wear resistance, commonly used in die casting molds, improve cooling efficiency and mold life.
2) brass:
Good corrosion resistance, but lower mechanical strength, usually used for lower temperature casting molds.
(4) other alloys
1) nickel-based alloy:
Very high heat resistance and oxidation resistance, suitable for extreme high temperature casting process, such as aerospace parts manufacturing.
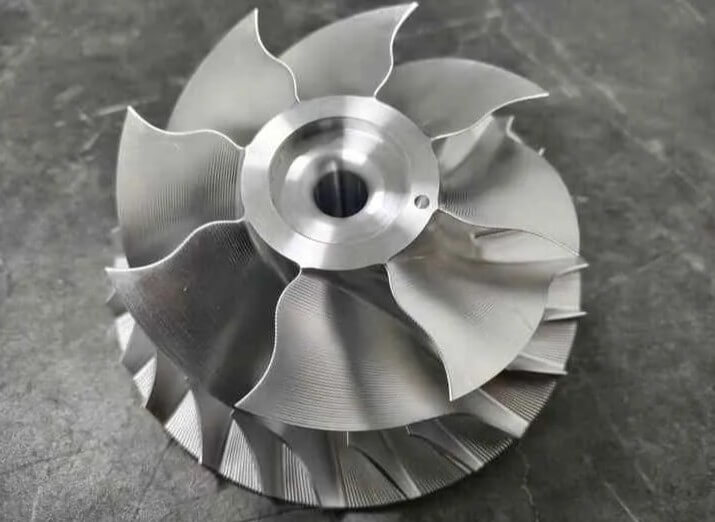
2) Cobalt-based alloys:
With good wear resistance and thermal fatigue resistance, suitable for high strength, high temperature casting environment.
2.Metal casting mold materials key performance requirements
Different types of casting process on the mold materials put forward different requirements, but in general, the ideal metal casting mold materials need to have the following properties:
(1) high-temperature strength and heat resistance
Moulds in a high-temperature environment for long-term work, must have sufficient strength to prevent softening or deformation in the process of use.
For example, hot work mold steel H13 has good high temperature strength, widely used in high temperature casting process.
(2) wear resistance and corrosion resistance
Wear resistance of the mold material determines the length of its life, especially in the high-pressure, high-speed casting process, the mold and molten metal frequent contact, prone to wear and tear.
At the same time, part of the casting material (such as aluminum alloy) may be corrosive to the mold, so the mold material needs to have a certain corrosion resistance.
(3) thermal stability and thermal fatigue performance
As the mold in the working process constantly undergoes heating and cooling cycles, easy to crack due to thermal fatigue, which in turn affects the service life. Therefore, excellent thermal stability and thermal fatigue resistance is essential to extend the life of the mold.
For example, nickel-based alloys show excellent resistance to thermal fatigue in high-temperature environments.
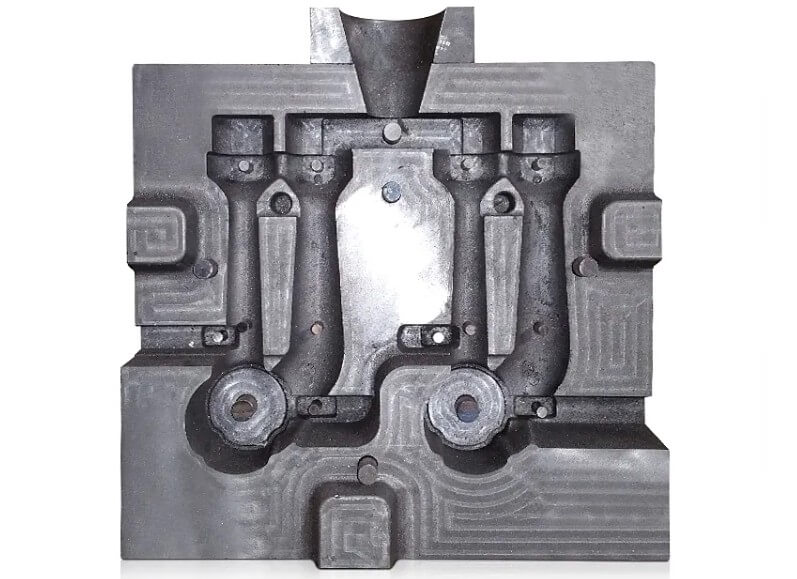
(4) Good thermal conductivity and processability
Good thermal conductivity of the mold material can speed up the cooling rate, improve casting quality and reduce production cycle time. For example, beryllium copper alloy is widely used in die casting molds because of its excellent thermal conductivity.
In addition, the metal casting mold material should also have good processability, in order to reduce manufacturing costs and improve production efficiency.
3.Different types of metal casting process on the mold material requirements
(1) gravity casting
Need mold materials with good heat resistance to withstand high-temperature metal liquid washout and thermal cycling effects.
High thermal fatigue resistance can effectively reduce mold cracks, improve service life.
(2) Investment casting
As the process is mainly used for precision casting, mold materials should have high precision and high corrosion resistance.
The use of nickel-based alloy or stainless steel can improve the corrosion resistance of the mold and surface quality.
(3) die casting
Because the die-casting process involves high pressure, high speed filling, mold materials need to have very high strength and high temperature resistance.
The use of hot work die steel (such as H13) or beryllium copper alloy can improve the impact resistance of the mold and cooling efficiency.
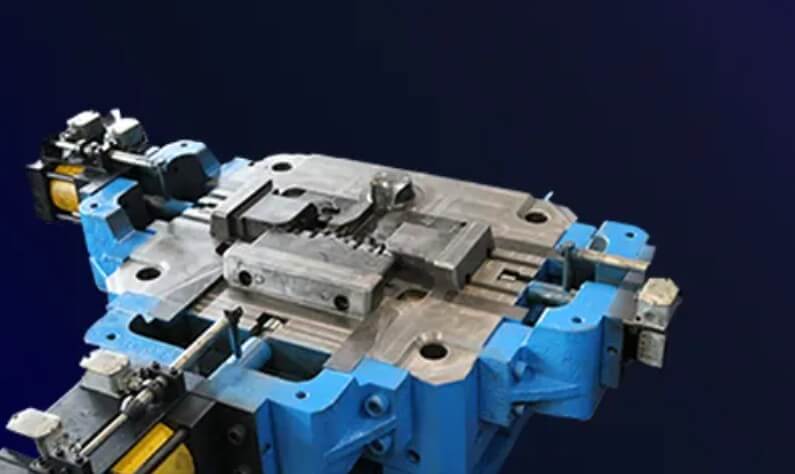
(4) Low pressure casting
The process of the mold thermal shock resistance and toughness requirements are high, in order to prevent the mold in the long term use of cracking.
Selection of ductile iron or high toughness steel can effectively improve the mold life.
The following table form of the main requirements of different casting processes and applicable metal casting mold materials are summarized:
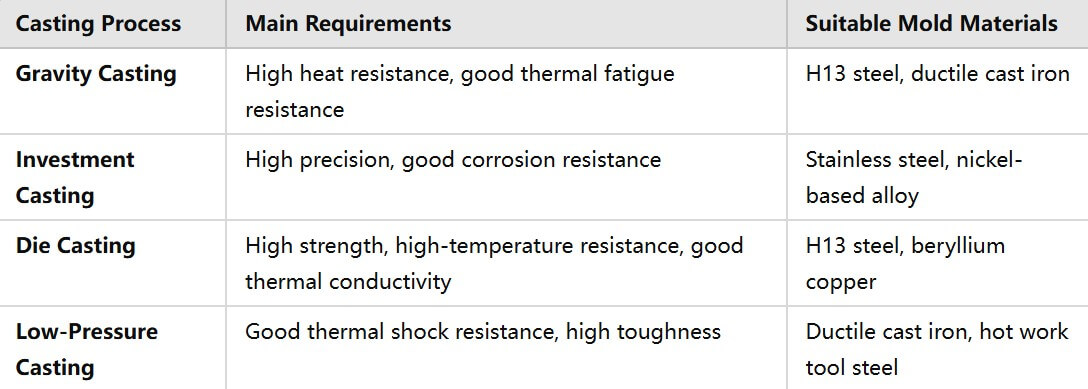
4.Performance comparison and applicable process analysis of different metal casting mold materials
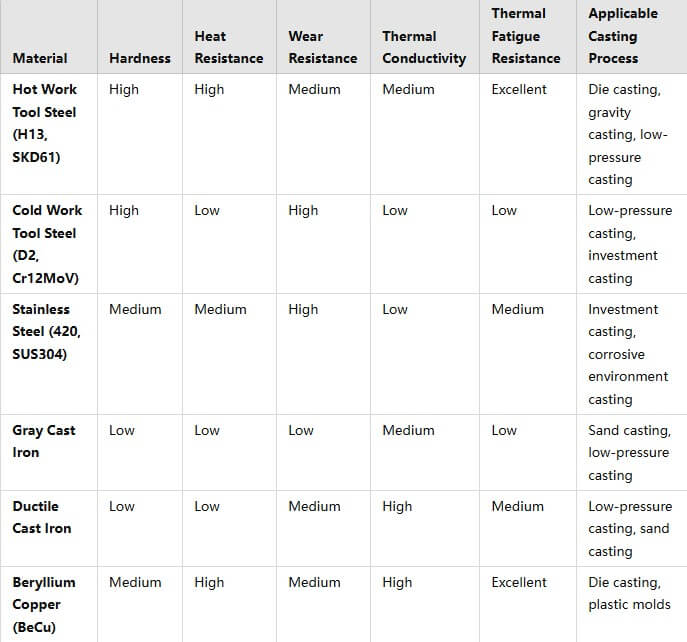
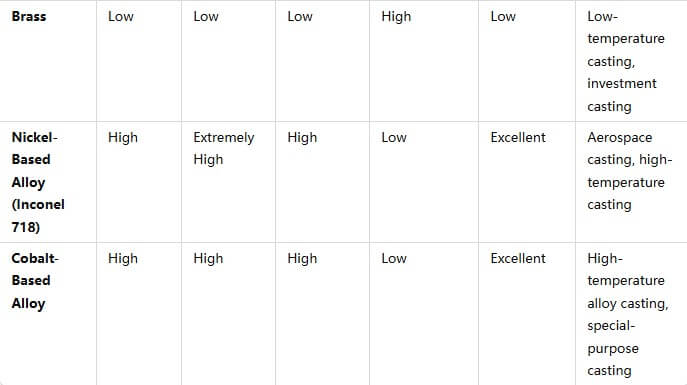
5.Main failure forms of metal casting molds
Metal casting mold in the long-term use of the process, by the scouring of high-temperature molten metal, the role of mechanical loads and chemical corrosion, prone to performance degradation or even failure. The main forms of failure include the following:
(1) thermal fatigue cracks
Mold in a high-temperature environment repeated heating and cooling, will be due to thermal expansion and contraction of stress, the long-term role of thermal fatigue cracks. Cracks usually extend along the mold surface, and ultimately affect the service life of the mold.
Thermal fatigue crack formation rate and mold material thermal fatigue resistance, cooling mode and process parameters are closely related.
(2) wear and corrosion
1) wear and tear:
Mold surface in the metal liquid high temperature scouring and mechanical friction, there will be material loss, especially in high pressure, high speed die casting process is more serious.
2) Corrosion:
Certain metals (such as aluminum, copper alloy) in high temperature is easy to chemical reaction with the mold material, resulting in the mold surface is oxidized, erosion, weakening the strength and durability of the mold.
(3) plastic deformation and cracking
When the metal casting mold material in the high temperature and high pressure environment, if its strength is insufficient, plastic deformation may occur, resulting in a decrease in dimensional accuracy. In addition, under the action of high stress, the mold may be brittle cracking, affecting the safety of use.
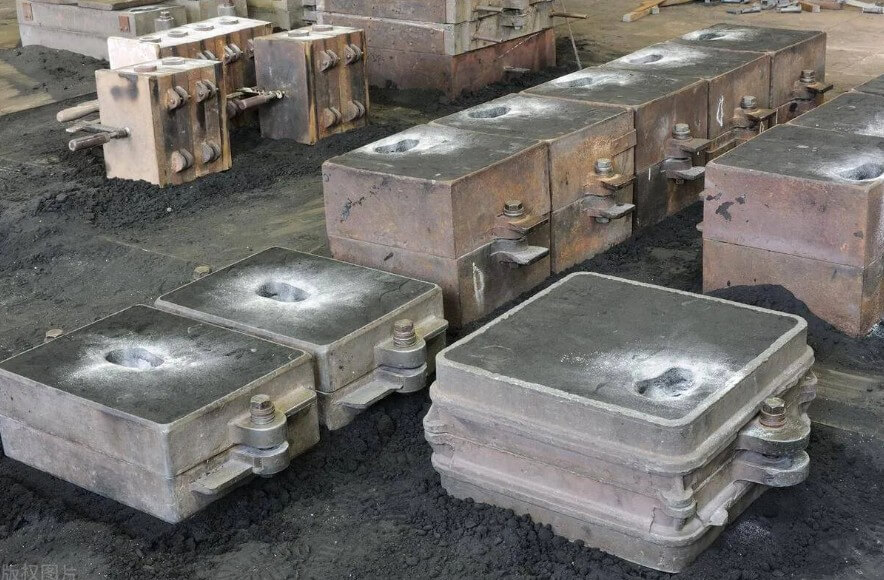
(4) Fracture caused by mechanical shock
In the high-pressure casting or low-pressure casting process, the mold is subjected to strong mechanical impact, such as high-speed filling of alloy liquid or mold opening vibration. These shocks may lead to local stress concentration, and ultimately lead to fracture or local damage to the mold.
6.The main factors leading to the failure of metal casting mold materials
The failure of the mold is not only related to the material properties, but also by the use of the environment and process parameters. The following are the main factors leading to mold failure:
(1) high temperature environmental impact
● Molds are exposed to high temperatures for a long period of time, which can easily lead to softening of the material and decrease in strength, thus accelerating wear and deformation.
●Frequent high temperature – low temperature alternation makes the mold material repeatedly expansion and contraction, easy to produce thermal stress, resulting in the formation and expansion of thermal fatigue cracks.
● If the cooling system is not properly designed, some areas of the mold may have uneven temperatures, further increasing the risk of thermal stress concentration.
(2) Overload and stress concentration
●Molds that are subjected to mechanical loads in excess of their designed capacity during use may result in plastic deformation or fracture.
● Due to the non-uniformity of the mold structure, there may be stress concentration in certain parts, which may easily become the starting point of fatigue cracks and accelerate the failure of the mold.
● Improper assembly or overuse may increase the load-bearing burden of the mold, causing it to be damaged prematurely.
(3) Irrational production process parameters
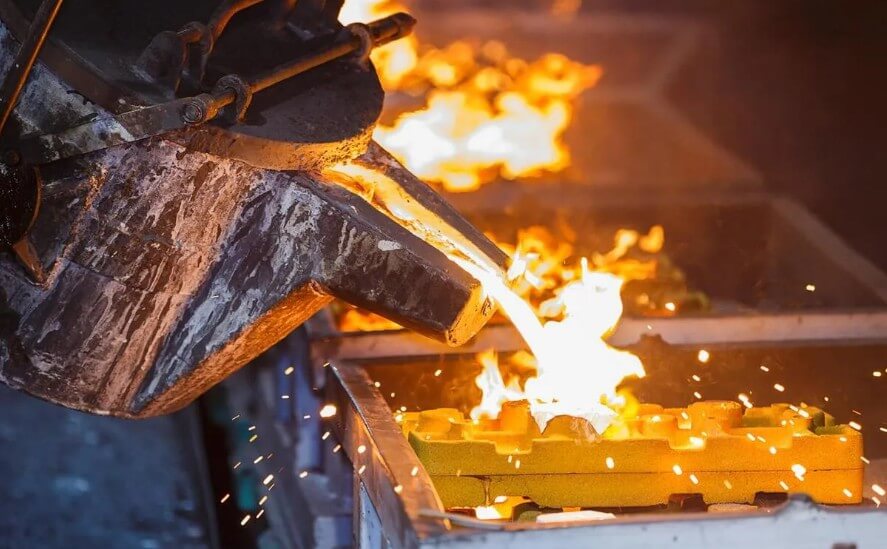
● Too high a temperature of the metal liquid may increase the thermal shock on the surface of the mold, accelerating the formation of thermal fatigue cracks.
●The filling speed is too fast may lead to strong impact on the mold, increasing wear and mechanical damage.
●Unreasonable cooling rate may trigger thermal stress concentration, leading to mold cracking.
●Irregular lubrication and maintenance will accelerate the wear of the mold surface and shorten the service life.
7.Optimization strategy to extend mold life
Extending the life of the mold helps to improve productivity and reduce costs, which can be optimized from the following aspects:
(1) material optimization
Selection of high-performance metal casting mold materials, such as H13 steel (heat-resistant and wear-resistant), nickel-based alloys (corrosion-resistant and heat-resistant) and beryllium copper (high thermal conductivity), in order to improve the durability of the mold.
According to the needs of different casting process to choose the appropriate material, to reduce the risk of failure.
(2) Heat treatment process optimization
● Quenching + tempering can improve mold hardness and wear resistance.
●Deep cold treatment (-196℃) can enhance fatigue resistance and prolong service life.
●High-temperature tempering can reduce residual stress and reduce the risk of high-temperature cracking.
(3) Surface Strengthening Technology
●Nitriding treatment (e.g. gas nitriding, ion nitriding) can enhance surface hardness and improve wear resistance.
PVD coating (e.g. TiN, CrN) can improve corrosion resistance and high temperature resistance.
● Laser surface strengthening can increase the wear resistance and thermal fatigue resistance of the mold.
(4) Design and cooling system optimization
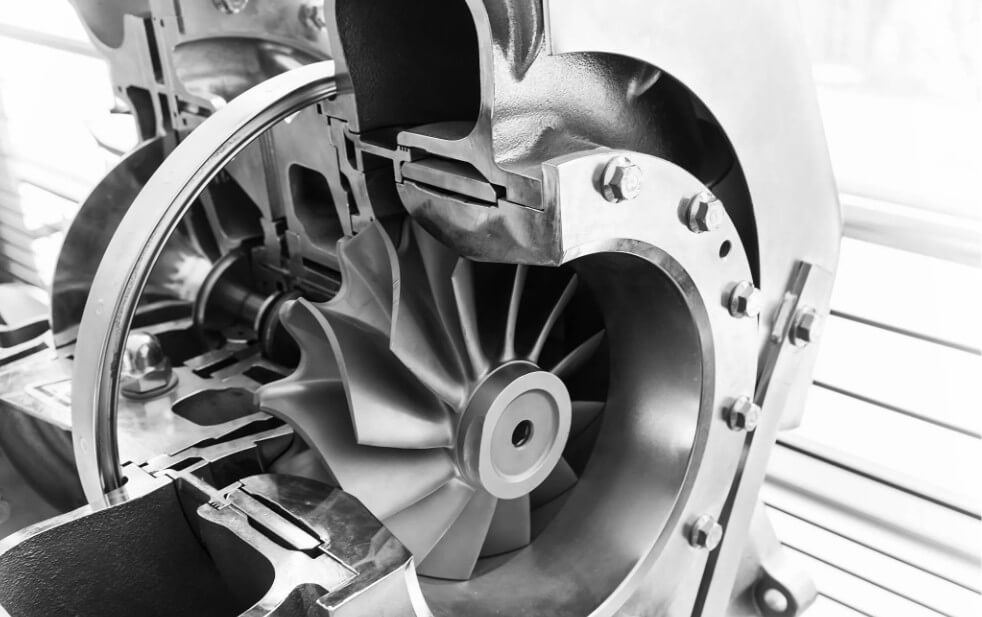
●Optimize the layout of cooling channels to improve heat dissipation efficiency and reduce thermal stress.
●Uniform wall thickness design to avoid cracks caused by localized overheating.
●Use high thermal conductivity materials (such as beryllium copper) to manufacture cooling components to improve cooling effect.
(5) Reasonable use and maintenance
●Control production parameters, avoid overload operation, reduce thermal shock.
●Regular cleaning and maintenance to remove carbon and residue and prevent corrosion and oxidation.
8.Summary
In summary, the selection of metal casting mold materials needs to take into account its heat resistance, wear resistance, thermal fatigue resistance and other key properties, and different casting processes have different requirements for mold materials.
At the same time, the mold in the long-term use of the process, by thermal stress, mechanical shock, chemical corrosion and other factors, fatigue cracks, plastic deformation, wear and other failure phenomena may occur. Therefore, optimizing material selection, improving heat treatment process and strengthening maintenance are the keys to prolonging the life of the mold and improving production efficiency.