Research on low pressure casting process: comprehensive analysis from process to application
Low pressure casting is a metal casting technology that uses a low pressure environment to force molten metal into the mold and solidify it to cast parts.
1.Low pressure casting process flow
(1) Mold design and manufacturing
The mold is made of steel and processed by CNC. The design and manufacturing ensure that there are no errors or defects to ensure the quality and function of the parts. At the same time, the mold is cleaned and preheated to prevent thermal defects caused by temperature differences.
(2) Melting metal
The metal alloy to be processed is heated in a crucible furnace until it is completely melted, and then transferred to an insulated furnace under the mold, which acts as a reservoir for storing molten metal. The positioning and drainage process ensures that no slag is injected into the mold.
(3) Casting
The molten metal is injected into the mold cavity through the riser at a pressure of about 0.08MPa.
(4) Cooling and solidification
The molten metal is cooled and solidified at low pressure to form parts.
(5) Pushing
Once cooled and solidified, the part is ejected by the ejector, the mold cools and releases pressure, and the remaining molten metal flows back to the insulation furnace.
(6) Post-processing
Subsequent processing (such as trimming) is performed to remove excess metal and improve surface quality.
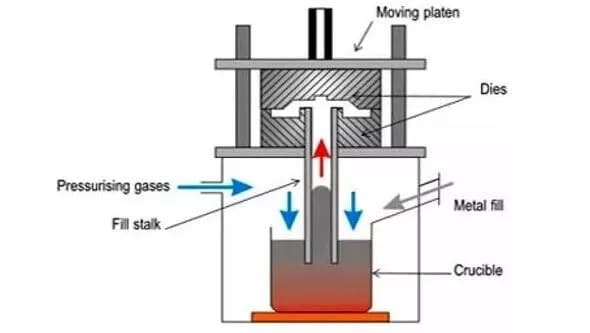
2.Common materials for low pressure casting
(1) Aluminum
When melted, aluminum has low viscosity and flows freely. It is suitable for thin-walled castings with a wall thickness greater than 5mm.
(2) Copper
Copper alloys have high tensile strength and are very suitable for low pressure casting. They do not crack when hardened and cooled rapidly.
(3) Magnesium
Its high fluidity and fluidity make it suitable for low pressure casting and can fill the mold smoothly.
(4) Zinc
Good fluidity, low melting point, and fast solidification make it the preferred material for low pressure casting. It can increase cycle speed and save costs. It has low abrasive load on the mold and good mechanical properties.
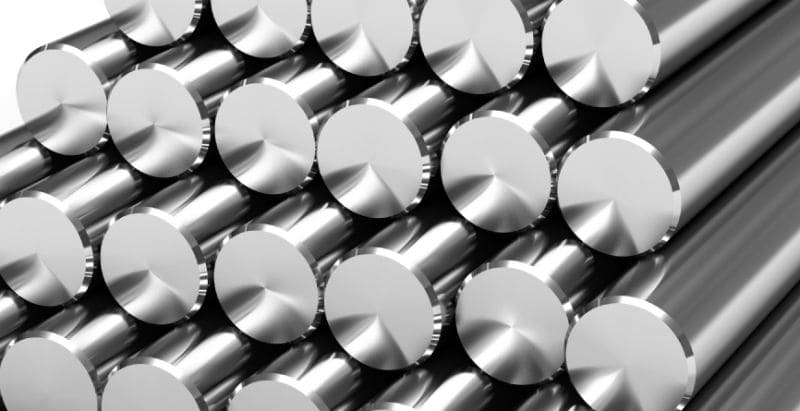
3.Advantages and disadvantages of low pressure casting
(1) Advantages:
1) High precision:
The filling rate is low under constant temperature and pressure, and the parts are very precise, which is important for small castings that need to be assembled after production.
2) Clean castings:
Since the mold is filled slowly under low pressure, no slag is formed, and very clean castings can be produced.
3) Good moldability:
The parts produced do not crack or deform, and are suitable for parts with complex shapes and designs.
4) Good crystallization:
The heat distribution and pressure during solidification are appropriate, and the workpiece after crystallization has finer grains and higher strength. It is suitable for places that require impact resistance and load resistance.
5) Environmental protection:
Energy saving, less waste, and recyclable. This can save operating costs.
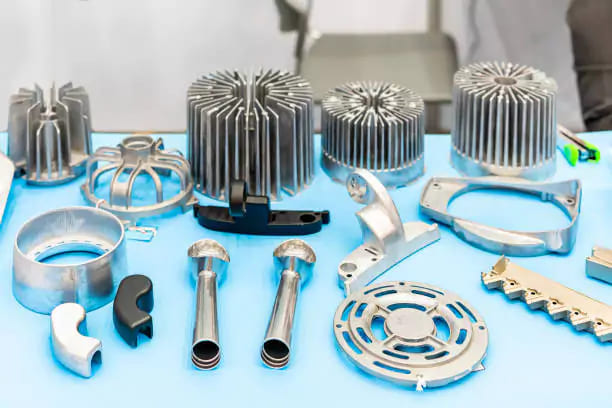
(2) Disadvantages:
1) Slow cycle:
Low pressure will lead to slow casting cycle and longer delivery time.
2) Not durable mold:
The mold is easily damaged by constant contact with molten metal.
3) Not suitable for thin-walled parts:
Low pressure casting is not suitable for thin-walled parts, and the wall thickness should be greater than 5mm.
4) High initial investment:
The die-casting machine, mold design, and manufacturing costs are high.
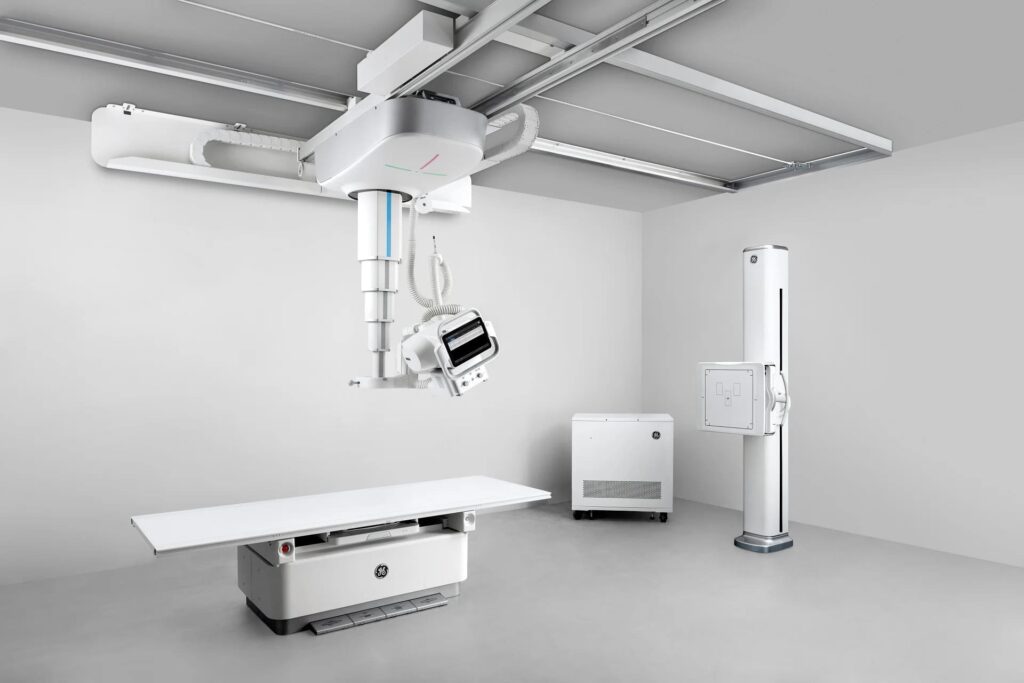
4.Application areas of low pressure casting
(1) Automobile industry
Small and medium-sized automobile parts such as wheels and cylinder heads.
(2) Medical equipment
Surgical instruments, X-ray machines. Castings are non-porous and can withstand heat sterilization and chemical sterilization.
(3) Aerospace industry
High-quality parts that meet strict tolerances. Precise and neat details.
(4) Household appliances
Cooking tools and other parts, manufacturing complex household parts.
(5) Electrical industry
Very thin and homogeneous electrical parts, such as motor housings.
(6) Marine shipbuilding
Pumps, motors and other marine parts, durable and corrosion-resistant.