Liquidmetal coatings amorphous: a new idea for material surface modification
In the face of increasingly harsh usage environments, it is particularly important to improve the performance of materials.
As an emerging material surface modification technology, liquidmetal coatings amorphous forms a layer of amorphous liquid metal film on the surface of the base material, which significantly improves the material’s corrosion resistance, wear resistance and self-propelled properties. Lubricant performance provides new ideas and methods for optimizing material properties.
This article will delve into the basic concepts, characteristics, film formation technology introduction, application fields and specific application case analysis of liquidmetal coatings amorphous.
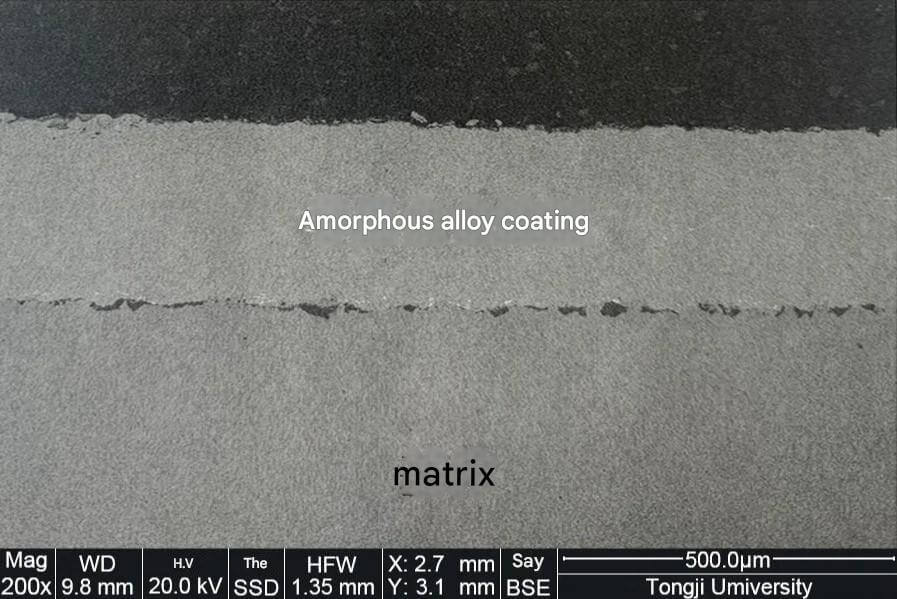
.
Relationship between amorphous alloy coating and substrate
.
1.Basic concepts of liquidmetal coatings amorphous
Liquidmetal coatings amorphous technology is a method that utilizes the characteristics of amorphous alloys to form a liquid metal coating on the surface of the base material. This technology mainly utilizes the characteristics of amorphous alloy to appear liquid within a specific temperature range, and evenly covers it on the surface of the substrate through spraying, electroplating and other processes. Liquidmetal coatings amorphous can not only significantly improve the corrosion resistance and wear resistance of the material, but also improve its mechanical and electrical properties, thereby extending the service life of the material and improving the safety and reliability of the equipment.
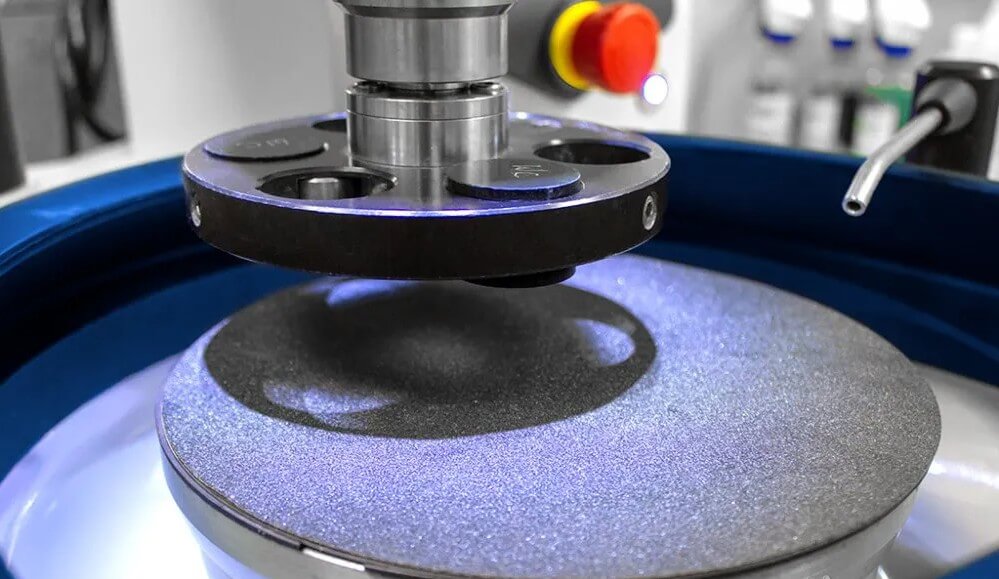
2.Characteristics of liquidmetal coatings amorphous
(1) High strength and hardness
Liquidmetal coatings amorphous exhibit extremely high strength and hardness due to their unique atomic arrangement structure. Research shows that some amorphous alloys can be more than twice as strong as traditional crystalline alloys. This makes liquidmetal coatings amorphous of great application value in applications that require high strength and hardness, such as cutting tools, molds and bearings.
(2) Good wear resistance
The liquidmetal coatings amorphous is far harder and more wear-resistant than traditional materials, making it excellent in high-wear environments. For example, applying this coating to key components such as piston rings and bearings in automobile engines can significantly increase the service life of the components, reduce maintenance frequency, and reduce operating costs.
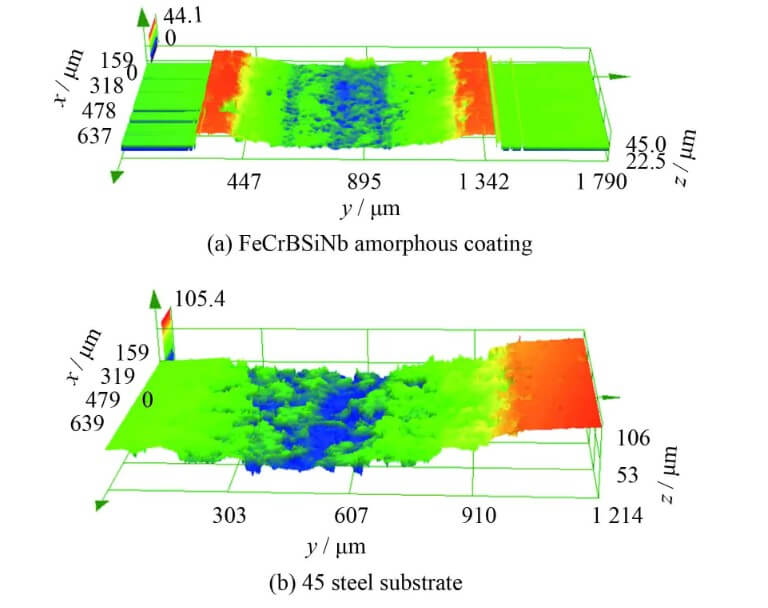
.
Schematic diagram of three-dimensional wear scars between FeCrBSiNb amorphous coating and 45 steel substrate
.
(3) Excellent corrosion resistance
Liquidmetal coatings amorphous have excellent corrosion resistance. Since there are no grain boundaries and defects in amorphous alloys, these structures are generally considered to be fast diffusion channels for corrosive media. Therefore, the amorphous alloy coating can effectively prevent the penetration of corrosive media and improve the corrosion resistance of the base material.
(4) Good magnetic properties
Certain liquidmetal coatings amorphous have excellent magnetic properties, such as high magnetic permeability and low magnetic loss. These properties make liquidmetal coatings amorphous have broad application prospects in electronic devices, transformers, sensors and other fields.
(5) High thermal stability
Liquidmetal coatings amorphous have high thermal stability and can maintain the stability of their structure and performance in high temperature environments. This makes liquidmetal coatings amorphous of great application value in high-temperature working environments, such as aerospace and energy fields.
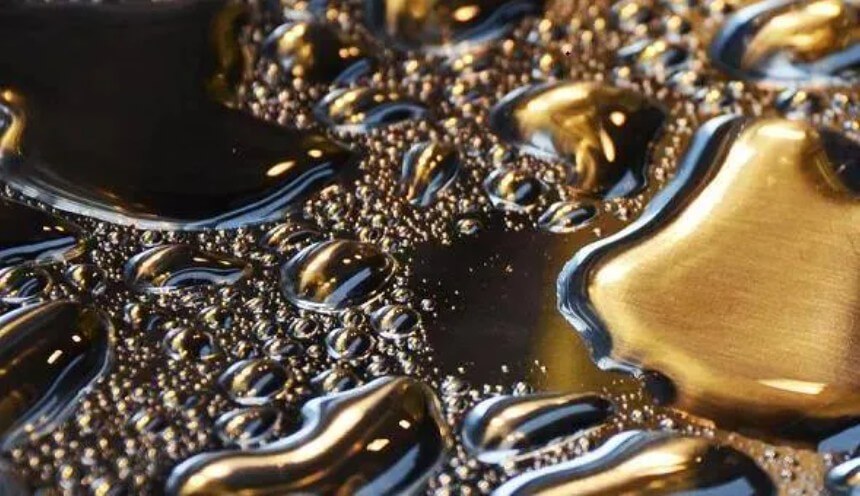
3.How to form a uniform liquidmetal coatings amorphous on the surface of the substrate? Technical introduction
(1) Rapid solidification technology
Rapid solidification technology is one of the core technologies for forming liquidmetal coatings amorphous on the surface of substrates. The molten metal is cooled so quickly that it does not have time to form a crystal structure during the solidification process, thus forming an amorphous state. This technology usually uses methods such as spray deposition and rapid cold rolling, which can accurately control the thickness and structure of the coating to ensure the quality and performance of the coating.
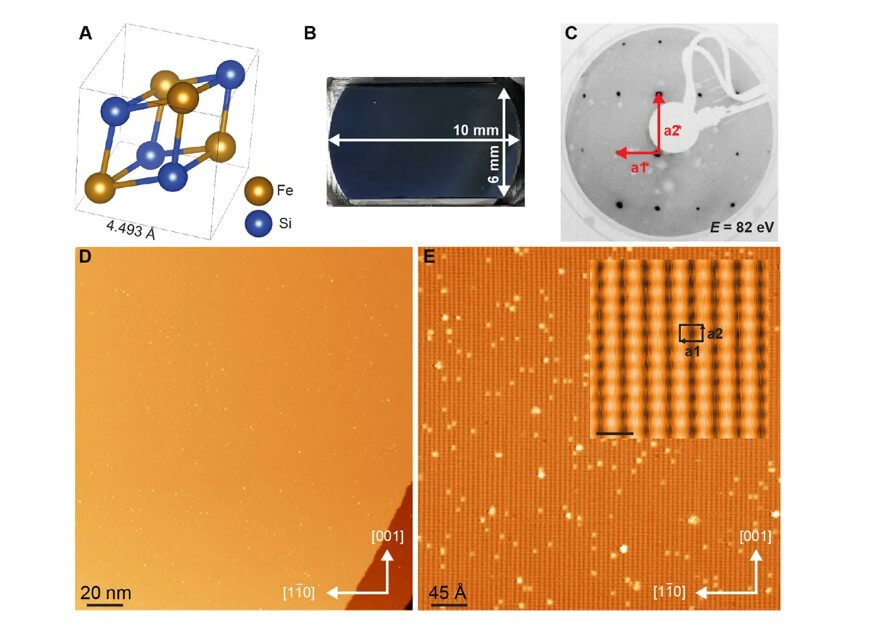
.
Display of metallic state of FeSi(110) single crystal surface
.
(2) Physical vapor deposition technology
Physical vapor deposition technology (PVD) is a method that converts the material source into a gas phase through a physical process and then deposits it on the surface of the substrate to form a coating. PVD technology includes sputtering deposition, evaporation deposition, etc., which has the advantages of high coating purity and strong bonding force. PVD technology can precisely control the composition and structure of the coating and improve the performance and stability of the coating.
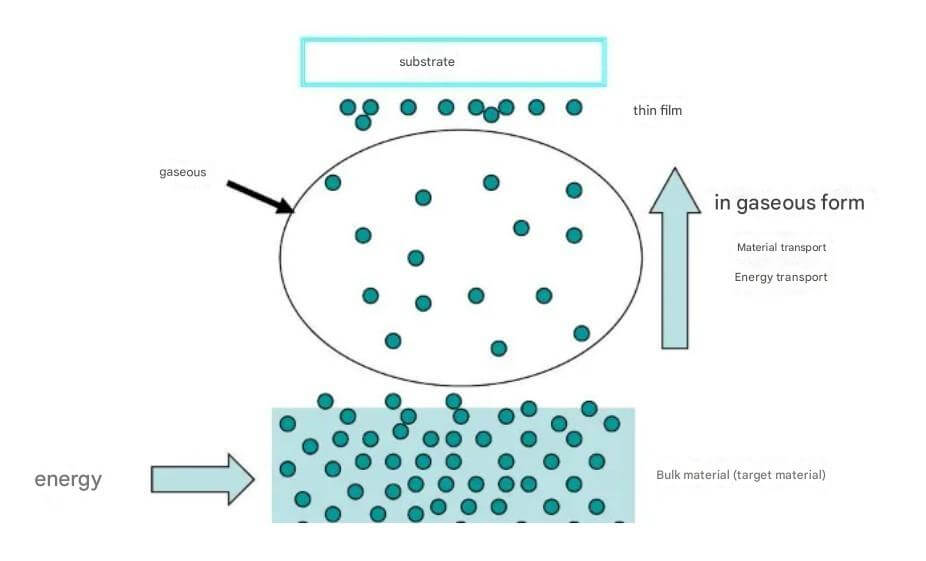
.
Operation principle of physical vapor deposition technology
.
(3) Chemical vapor deposition technology
Chemical vapor deposition technology (CVD) deposits coatings on the surface of a substrate through chemical reactions. This technology can diversify coating materials and improve the performance and functionality of the coating. For example, by regulating chemical reaction conditions and deposition parameters, amorphous coatings with special functions can be prepared, such as high temperature resistance, corrosion resistance, and self-lubrication.
(4) Electroplating and chemical plating technology
Electroplating and chemical plating technologies deposit a metal layer on the surface of a substrate through electrolysis or chemical reaction to form an amorphous coating. These technologies have the advantages of simple equipment and low cost. They can achieve uniform deposition and precise control of the coating and improve the performance and stability of the coating.
Widely used in industrial production.
(5) Thermal spray technology
Thermal spray technology is to heat amorphous liquid metal to a molten state, atomize it into tiny droplets through high-speed airflow, and spray it onto the surface of the substrate to form a coating. Common thermal spraying methods include flame spraying, plasma spraying and high-velocity oxy-fuel spraying. These methods enable rapid deposition of thick coatings and are widely adaptable to substrate materials. By controlling spraying parameters such as spraying distance, spraying angle and spraying speed, a uniform and strong bonding coating can be obtained.
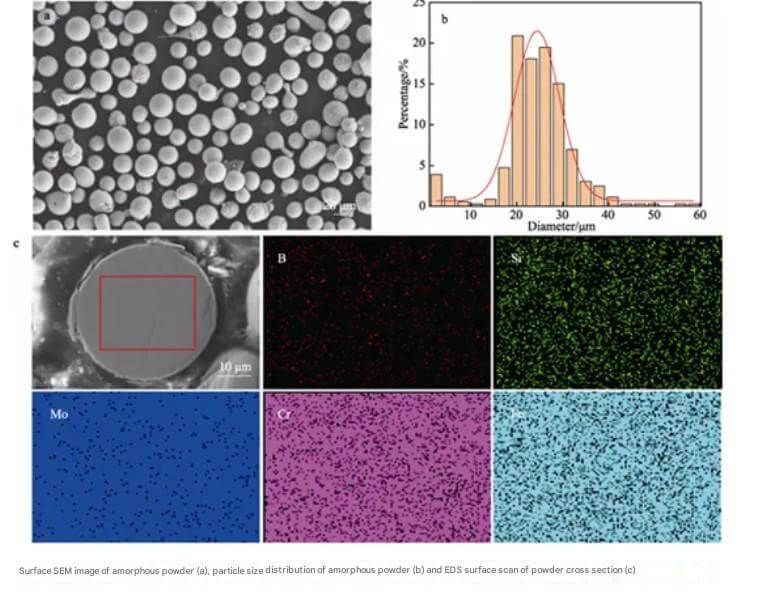
.
Effect of substrate temperature on wear and corrosion resistance of plasma sprayed Fe-based amorphous alloy coating
.
4.Application fields of liquidmetal coatings amorphous
(1) Application in aerospace field
In the aerospace industry, liquidmetal coatings amorphous are widely used to improve the performance of engines and structural components. For example, amorphous coatings can significantly improve the high temperature resistance and corrosion resistance of engine blades and extend their service life. In addition, amorphous coatings are also applied to aircraft frames and connectors to improve their strength and durability and ensure flight safety.
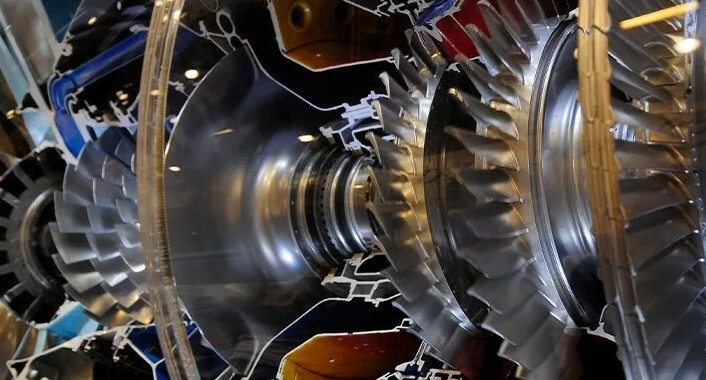
(2) Application in automobile industry
In the automotive industry, liquidmetal coatings amorphous are primarily used to improve the efficiency and durability of engines and transmission systems. For example, amorphous coatings can be applied to engine cylinders and piston rings to reduce friction and wear and improve engine efficiency. In addition, amorphous coatings are also applied to transmission gears and bearings to improve their wear resistance and service life and reduce maintenance costs.
(3) Application in the field of medical devices
In the field of medical devices, liquidmetal coatings amorphous are widely used to manufacture high-performance medical implants and surgical instruments due to their excellent biocompatibility and corrosion resistance. For example, amorphous coatings could be applied to artificial joints and dental implants to improve their biocompatibility and durability. In addition, amorphous coatings are also used in instruments such as scalpels and scissors to improve their wear resistance and corrosion resistance and ensure the hygiene and safety of the instruments.
(4) Application in electronics industry
In the electronics industry, liquidmetal coatings amorphous are mainly used to manufacture high-performance electronic components and devices. For example, amorphous coatings can be used to make transformers and inductors to improve their electromagnetic performance and efficiency. In addition, amorphous coatings are also used to manufacture devices such as sensors and memories to improve their stability and reliability and meet the needs of high-end electronic equipment.
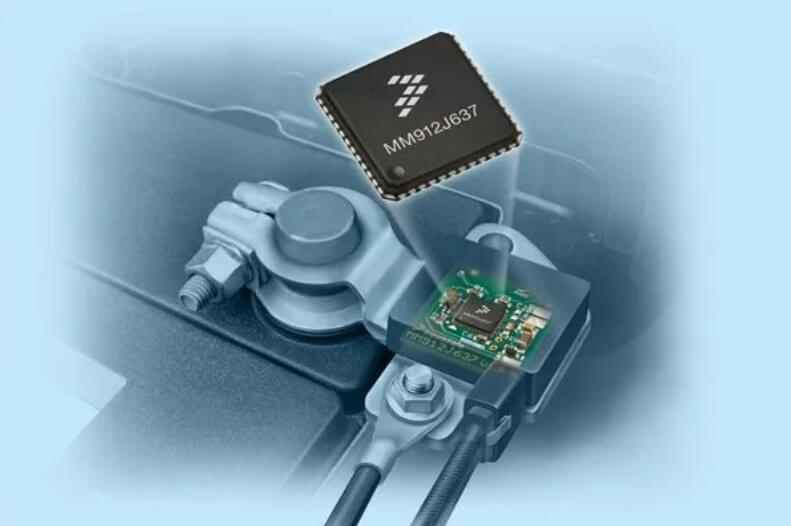
(5) Tool and mold field
Liquidmetal coatings amorphous have important application prospects in the field of tools and molds due to their high strength and hardness. By coating the surfaces of cutting tools and molds with liquidmetal coatings amorphous, their service life and processing efficiency can be significantly improved. For example, amorphous alloy-coated tools show excellent performance when cutting high-strength materials, which can effectively reduce tool wear and increase cutting speed.
(6) Corrosion protection field
Liquidmetal coatings amorphous have broad application prospects in the field of corrosion protection due to their excellent corrosion resistance. By coating an liquidmetal coatings amorphous on the surface of a base material, the corrosion resistance of the material can be effectively improved and its service life extended. For example, in fields such as marine engineering, chemical equipment, and oil pipelines, liquidmetal coatings amorphous can significantly improve the corrosion resistance of equipment and reduce maintenance costs.
5.Analysis of specific application cases of liquidmetal coatings amorphous
(1) Application of Ti-based amorphous alloy coating in corrosion resistance
Ti-based amorphous alloy coatings are widely used in chemical equipment and marine engineering due to their excellent corrosion resistance. For example, in chemical equipment, Ti-based amorphous alloy coatings can effectively resist corrosion by strong acids and alkalis and extend the service life of the equipment. In marine engineering, Ti-based amorphous alloy coatings can resist corrosion in seawater and marine atmosphere, ensuring the long-term stable operation of marine structures.
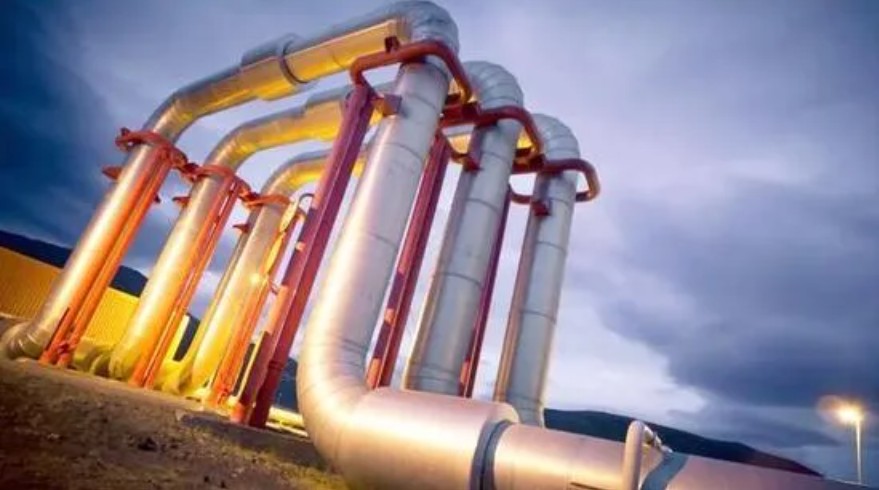
(2) Application of Fe-based amorphous alloy coating in wear resistance
Fe-based amorphous alloy coatings are widely used in the manufacture of high-performance cutting tools and wear-resistant parts due to their high hardness and excellent wear resistance. For example, in cutting tools, Fe-based amorphous alloy coatings can significantly improve the wear resistance and service life of the tools and improve cutting efficiency. In wear-resistant parts, Fe-based amorphous alloy coatings can effectively reduce friction and wear and improve the durability and reliability of parts.
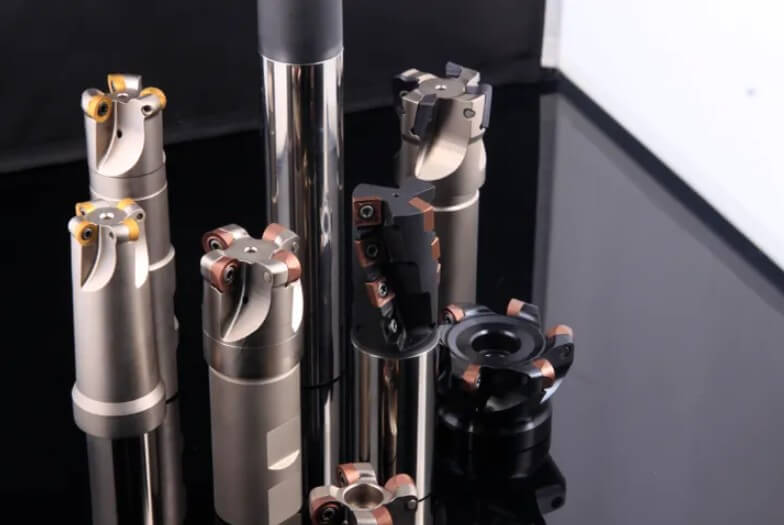
(3) Application of Zr-based amorphous alloy coating in biocompatibility
Zr-based amorphous alloy coatings are widely used in the manufacture of medical implants due to their excellent biocompatibility and corrosion resistance. For example, in medical implants, Zr-based amorphous alloy coatings can improve the biocompatibility of implants, reduce human body rejection, and ensure long-term stable operation of implants. In addition, the Zr-based amorphous alloy coating also has good corrosion resistance and can effectively resist corrosion from human body fluids and extend the service life of implants.
(4) Application of amorphous alloy coating in nuclear waste regeneration treatment
Amorphous alloy coatings are widely used in nuclear waste regeneration processing equipment due to their excellent corrosion resistance and stability. For example, in nuclear waste regeneration processing equipment, amorphous alloy coatings can effectively resist the erosion of highly corrosive nitric acid, ensuring long-term stable operation of the equipment. In addition, the amorphous alloy coating also has good high temperature resistance and radiation resistance, can remain stable in extreme environments, and improves the safety and reliability of equipment.
6.Summary
Liquidmetal coatings amorphous, with their unique performance advantages, have opened up new application prospects in the field of material surface modification and protection. From aerospace to biomedicine, from the automotive industry to electronic devices, its application not only improves the durability and reliability of materials, but also brings significant economic benefits and technological progress to related industries.
What do you think?
[…] modern industry, metal coating technology is widely used in aerospace, automobile manufacturing, medical equipment, construction […]