Surface finish of investment casting: influencing factors and improvement strategies
Investment casting surface finish is one of the important indicators to measure the quality of castings. It not only affects the appearance quality of the casting, but also has a direct relationship with the performance and life of the casting. This article will explore in depth the importance of investment casting surface finish, why investment casting can produce castings with good surface quality, the factors affecting investment casting surface finish, and how to improve the finish.
1.Definition and importance of investment casting
(1) Definition:
Investment casting, also known as lost wax casting, is a precision metal casting process. The process first uses a fusible material (such as wax) to make a model, and then coats the surface of the model with multiple layers of refractory material to form a shell. After heating, the wax model melts and flows out to obtain a hollow shell, which is then filled with molten metal. After cooling, the refractory material is broken to obtain the final metal part.
(2) Importance:
1) High precision:
Investment casting can produce castings with high dimensional accuracy and good surface finish, reducing the amount of subsequent processing.
2) Complex structure:
Applicable to the manufacture of parts with complex shapes that are difficult to form by other methods, such as aircraft engine blades.
3) Wide range of materials:
Can be used for a variety of alloys, including carbon steel, stainless steel, high-temperature alloys, etc.
4) Economic efficiency:
Through integral casting, the combination of parts can be reduced, production costs can be reduced, and production efficiency can be improved.
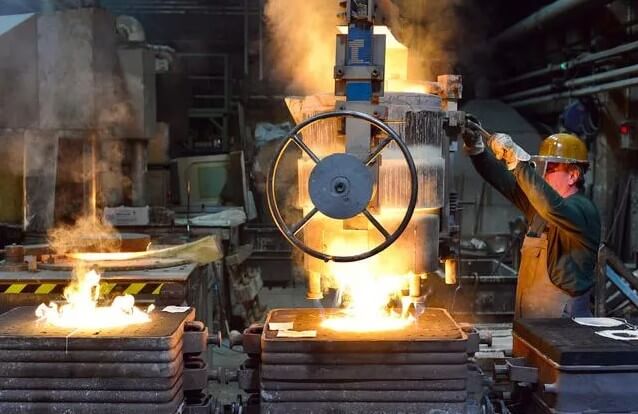
2.The role of surface finish in investment casting
(1) Improving product quality:
Surface finish directly affects the appearance and performance of castings. Castings with high finish have better corrosion resistance and mechanical properties.
(2) Reducing subsequent processing:
High surface finish can reduce or eliminate secondary processing, reduce production costs and processing time.
(3) Improving service life:
Good surface finish can reduce friction and wear during operation of parts and extend service life.
(4) Enhancing market competitiveness:
Castings with excellent surface quality can meet higher-end market demands and improve product competitiveness.
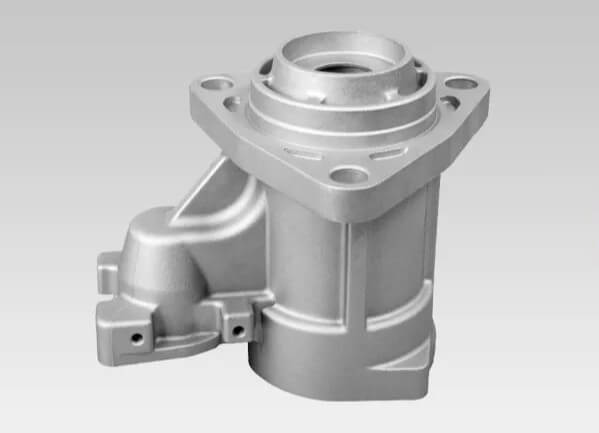
3.Why does investment casting produce a better surface finish?
(1) High precision of wax pattern:
During the investment casting process, a wax pattern needs to be made first. The wax pattern is usually pressed using a high-precision mold, which ensures the dimensional accuracy and surface finish of the wax pattern itself. Since the wax pattern is replicated in the subsequent process, the high precision of the wax pattern is directly transferred to the final casting.
(2) Uniform coating of refractory materials:
Multiple layers of refractory materials are coated on the surface of the wax pattern, which form a mold shell after hardening and drying. The uniform coating and fine particle structure of the refractory material help to form a smooth cavity surface, thereby improving the surface finish of the casting.
(3) High temperature roasting:
The mold shell is roasted at high temperature before pouring. This process not only removes the wax pattern, but also makes the mold shell material further densified, reduces surface defects, and thus optimizes the investment casting surface finish.
(4) No parting surface:
Unlike traditional sand casting, investment casting has no parting surface. This means that during the pouring process, the liquid metal will not be affected by the parting surface, thereby reducing the defects and unevenness of the casting surface.
(5) High temperature stability of the mold shell:
The mold shell used in investment casting usually has excellent high temperature stability, which can maintain the stability of shape and size at high temperatures, avoiding surface defects of the casting caused by deformation of the mold shell during the pouring process.
(6) Fine pouring process:
Investment casting usually adopts fine pouring processes such as gravity pouring, vacuum suction pouring, and crystallization under pressure. These processes can ensure that the liquid metal is smoothly filled in the mold shell, reduce defects such as pores and inclusions, and improve the surface finish of the casting.
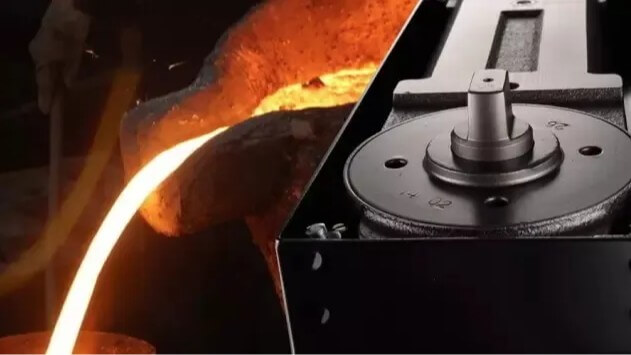
4.Investment Casting Surface Finish: Factors Influencing
The surface finish of investment casting is affected by many factors. The following is a detailed explanation of the impact of investment casting process on surface finish:
(1) The impact of material selection on the surface finish of investment casting:
1) Mold shell material:
The choice of mold shell material has a direct impact on the surface finish of the casting. The use of high-quality die castings can replicate the surface of the investment pattern, thereby improving the surface finish of the casting. In addition, the mold shell is made of a refractory coating made of a special high-temperature resistant binder and refractory materials, which is applied to the investment pattern. The surface finish of the cavity in direct contact with the molten metal is high.
2) Properties of molten metal:
The properties of molten metal will also affect the surface finish of the casting. The fluidity, solidification characteristics and interaction of the metal with the shell material will affect the surface quality of the casting. For example, metal with good fluidity can better fill the cavity and reduce surface defects.
(2) The effect of process parameters on the surface finish of investment casting:
1) Pouring temperature:
Pouring temperature is an important factor affecting the investment casting surface finish. Appropriate pouring temperature can ensure that the molten metal has good fluidity, which helps to fill every corner of the cavity, reduce defects such as pores and shrinkage holes, and thus improve the surface finish.
2) Cooling rate:
The cooling rate has a significant effect on the microstructure and surface finish of the casting. Slow cooling can reduce the internal stress of the casting, which helps to obtain uniform structure and good surface quality. On the contrary, rapid cooling may cause cracks or roughness on the surface of the casting.
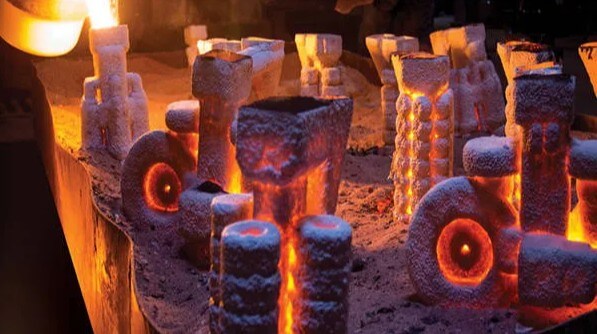
5.Investment Casting Surface Finish: Analysis of Strategies for Improvement
Investment casting is a precision casting process, and its surface finish directly affects the quality and performance of the casting. In order to improve the surface finish of investment casting, strategies can be analyzed from the following aspects:
(1) Optimize the investment material:
1) Use liquid mold material:
Liquid mold material has a lower viscosity and can better fill the details of the die, thereby producing a bright investment mold with the same finish as the die. The fluidity of the liquid mold material helps to reduce the surface depression of the casting.
2) Improve the finish of the mold material:
The finish of the investment mold surface is the basis for the smoothness of the casting surface. Using mold materials with high finish can significantly improve the surface quality of the casting.
(2) Improve the mold shell preparation process:
1) Powder particle size control:
Reasonably grading the particle size of refractory powder to make it have better embedding density and lower viscosity, which helps to improve the smoothness of the mold shell.
2) Slurry performance optimization:
Adjust the powder-liquid ratio of the slurry to make it have better process performance. The wetting ability, evaporation and gelling shrinkage characteristics of the slurry will affect the smoothness of the mold shell.
(3) Accurate control of the pouring process:
1) Pouring temperature and speed:
Control the pouring temperature and speed to avoid surface defects such as pores and cracks caused by excessive temperature or excessive speed.
2) Pouring system design:
Reasonably design the pouring system to ensure smooth flow of molten metal and reduce the impact on the mold shell, so as to obtain a smooth casting surface.
(4) Post-processing process:
1) Surface cleaning:
After the casting is cooled, appropriate surface cleaning is carried out, such as sandblasting, grinding, etc., to remove surface residues and oxide scale to improve the smoothness.
2) Surface treatment:
According to the needs, polishing, electroplating and other surface treatment processes are used to further improve the surface finish of investment casting.
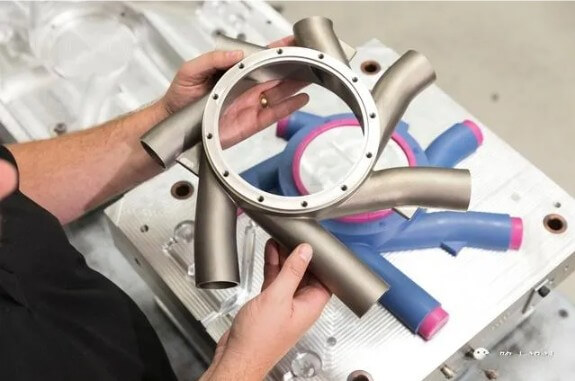
6.Summary
In summary, improving the surface finish of investment casting needs to start from multiple aspects. By optimizing the quality of wax molds, selecting appropriate shell materials and process parameters, and improving casting processes, the surface finish of castings can be effectively improved. Improving the surface finish of investment casting can not only improve the quality and market competitiveness of castings, but also win more development opportunities for enterprises in the fierce market competition.