Investment casting jewelry: a combination of fine craftsmanship and artistic beauty
Investment casting jewelry is a metal processing technique that combines tradition and modernity. It can transform the designer’s creativity into jewelry with complex shapes and details. With the development of modern technology and the application of advanced equipment and materials, the precision and quality of investment casting jewelry have been greatly improved. This article will discuss in depth the specific process, surface treatment technology, advantages, common problems and solutions of investment casting jewelry.
1.Types and characteristics of commonly used jewelry metals
(1) Gold:
Gold has excellent ductility and corrosion resistance and is a traditional choice for jewelry casting. Common gold alloys include 18K gold (75% gold) and 14K gold (58.3% gold). The color and hardness are adjusted by adding elements such as silver and copper.
(2) Silver:
Silver is relatively cheap and has good luster and plasticity. It is often used to make high-end jewelry. 925 silver (92.5% silver content) is a commonly used silver alloy. The hardness is increased by adding elements such as copper.
(3) Platinum:
Platinum is known for its hardness, corrosion resistance and rarity, and is the material of choice for high-end jewelry. Common platinum alloys include 950 platinum and 900 platinum.
(4) Copper alloys:
Such as brass (copper-zinc alloy) and bronze (copper-tin alloy), they are often used to make antique or artistic jewelry because of their low cost and rich colors.

2.Specific process of investment casting jewelry
Investment casting is an ancient metal processing process that is particularly suitable for making jewelry with complex shapes and fine details. The following are the specific process steps of investment casting jewelry:
(1) Design model:
First, make an original model according to the designer’s drawings, usually using wax or plastic. This model needs to accurately reflect the shape and details of the final jewelry.
(2) Make a wax mold:
The wax is injected into the die (mold) and cooled to obtain a wax mold. The dimensional accuracy and surface finish of the wax mold are crucial to the quality of the final casting.
(3) Module assembly:
The wax model is combined with the wax model that forms the pouring and riser system to form a complete module. The pouring and riser system is to ensure that the molten metal can flow smoothly into the mold cavity.
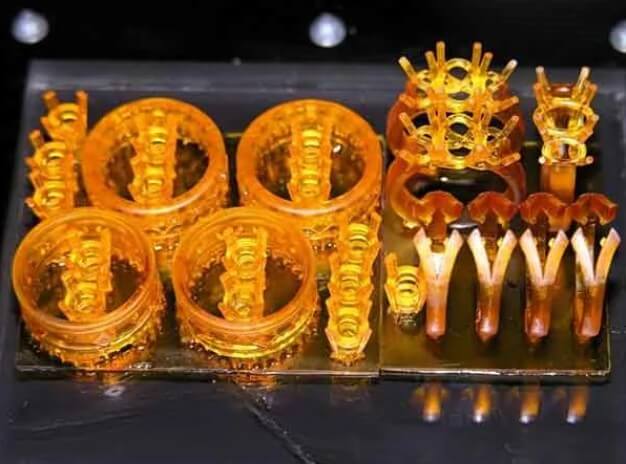
(4) Mold shell production:
The module is immersed in refractory coating and then sprinkled with refractory materials. This process is repeated several times to form a multi-layer mold shell. The materials of the mold shell usually include refractory materials such as quartz and corundum and binders such as silica sol.
(5) Dewaxing and roasting:
The coated module is heated to melt the wax model and flow out, leaving a hollow mold shell. The mold shell is then further heated to a high temperature to remove residual wax and enhance the strength of the mold shell.
(6) Metal pouring:
The molten metal is poured into the preheated mold shell. Commonly used investment casting jewelry metals include gold, silver, copper alloys, etc. Preheating the mold shell helps the molten metal flow better and fill the mold cavity details.
(7) Cooling and cleaning:
After the metal cools and solidifies, the shell is broken and the casting is taken out. Then, post-processing such as cutting, grinding, and polishing is carried out to remove the pouring head and repair surface defects.
(8) Setting gemstones:
If the design includes gemstones, they need to be set in the reserved holes after casting.
(9) Final modification:
The final stage of investment casting jewelry is to modify it, such as electroplating, engraving, etc., to achieve the desired appearance.
3.Surface treatment technology of investment casting jewelry
The investment casting process can create complex and delicate jewelry designs. In order to further enhance the surface finish of the jewelry, it needs to be subjected to final surface treatment. The following are some key technologies for surface treatment of investment casting jewelry:
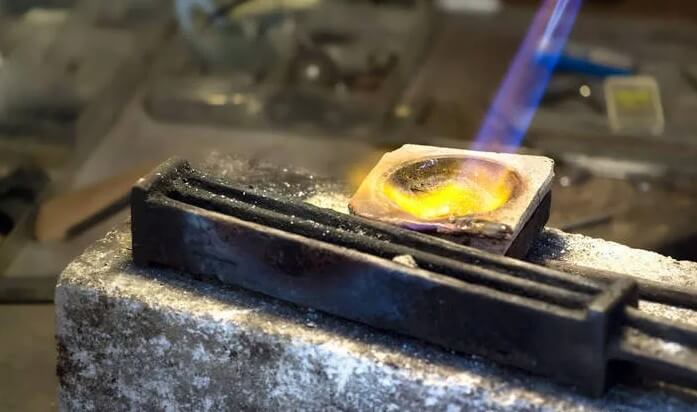
(1) Polishing:
After the investment casting jewelry process is completed, there may be some uneven or rough areas on the surface of the jewelry, which need to be removed by grinding. Grinding can be done using sandpaper or grinding stones of different grits, from coarse to fine, until the surface is smooth.
(2) Polishing:
Polishing is a key step in improving the surface finish of jewelry. Polishing wheels and polishing paste can be used to remove fine scratches on the surface through mechanical friction, giving the jewelry a mirror-like luster.
(3) Electroplating:
In order to increase the beauty and corrosion resistance of jewelry, electroplating is sometimes performed on the surface of jewelry. Electroplating can give jewelry different colors, such as gold, silver, etc., and can also increase the hardness of the surface.
(4) Sandblasting:
Sandblasting is a technique that changes the surface texture of jewelry by spraying fine abrasive particles. It can create a matte or frosted effect, increasing the texture and design of the jewelry.
(5) Chemical treatment:
Some jewelry materials, such as silver, are prone to oxidation and blackening. Chemical treatment, such as the use of antioxidants, can slow down or prevent this phenomenon.
(6) Laser engraving:
For jewelry that requires fine patterns or text, laser engraving technology can achieve high-precision engraving effects without damaging other parts of the jewelry.
(7) Ultrasonic cleaning:
After completing the above surface treatment, use an ultrasonic cleaner to clean the jewelry to remove dirt and residue on the surface of the jewelry, ensuring the cleanliness and luster of the jewelry.
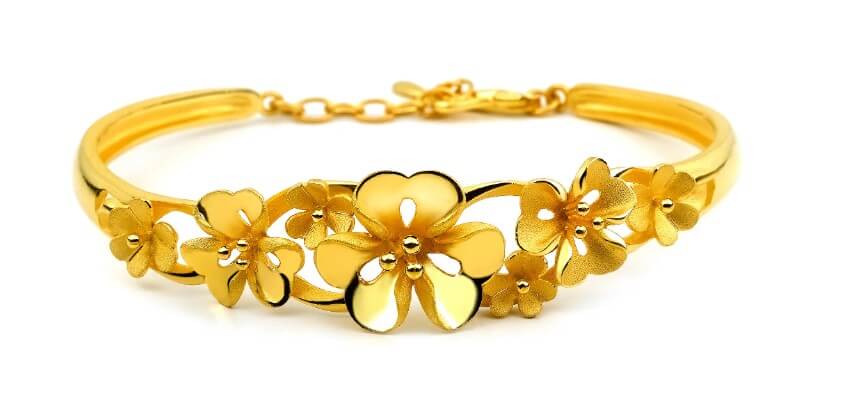
4.Advantages of investment casting in jewelry customization and mass production
(1) High precision and surface finish:
Investment casting can produce castings with high dimensional accuracy and low surface roughness, which makes the jewelry products have better appearance quality and reduces the workload of subsequent machining. Sometimes, they can even be used without machining.
(2) Design freedom:
Investment casting jewelry allows designers to create complex geometric shapes and fine details, which increases design freedom and makes jewelry products more diversified and personalized.
(3) Material diversity:
Investment casting jewelry is suitable for a variety of alloy materials, including precious metals, so it can meet the material requirements of different jewelry products.
(4) Mass production applicability:
Whether it is small-scale customization or mass production, investment casting can adapt. Especially in mass production, metal pressing can be used to improve production efficiency.
(5) Cost-effectiveness:
Although the initial investment of investment casting is high, in the long run, it can save costs due to reduced machining and material waste. In addition, the application of 3D printing technology further reduces the cost and time of mold making and improves production efficiency.
(6) Rapid prototyping:
Combined with 3D printing technology, investment casting can quickly produce jewelry prototypes, accelerate the design iteration process, and meet the market’s demand for rapid updates.
(7) Customized production:
The combination of 3D printing and investment casting makes jewelry customization easier, and personalized design and production can be carried out according to the specific requirements of customers.
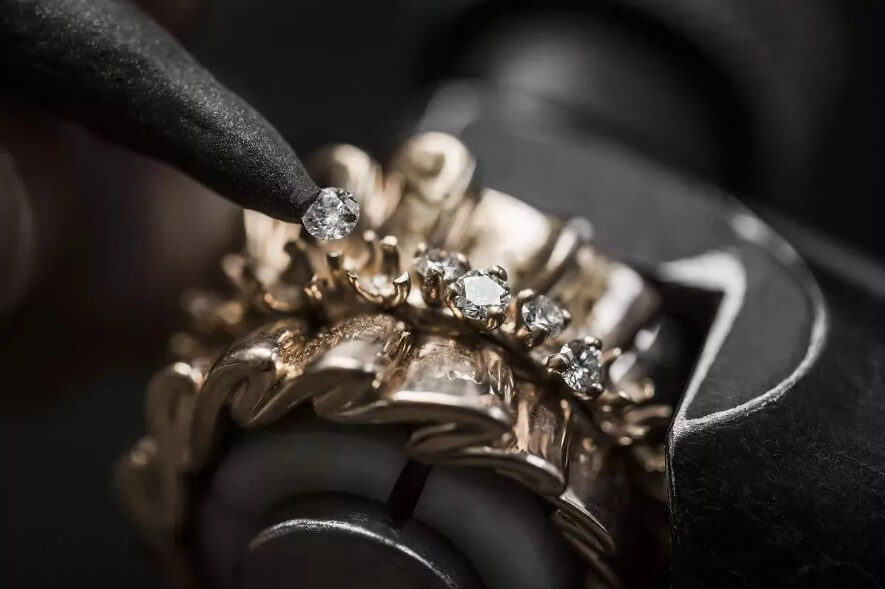
5.Common problems and solutions for investment casting jewelry
Investment casting is a precision casting technology commonly used in jewelry making. This process can produce complex and delicate jewelry works, but some problems may also be encountered in the process. The following are common problems and solutions for investment casting jewelry.
(1) Wax mold deformation
1) Problem: When pressing the wax mold, the wax mold may be deformed due to improper pressure, temperature or mold material selection.
2) Solution: Select a mold material with a small shrinkage rate and ensure that the temperature and pressure are moderate when pressing the wax mold. After the wax model is removed, it should be cooled immediately and the cooling time should be controlled to avoid deformation caused by uneven cooling.
(2) Surface defects
1) Problem: The surface of the casting may have defects such as wrinkles, pits or orange peel, which is usually caused by paint accumulation, uneven hardening or insufficient drying time.
2) Solution: Ensure that the surface of the wax model is clean and grease-free before painting. Avoid accumulation and ensure uniformity during painting. Increase the natural drying time to ensure that the paint is fully hardened. In addition, control the concentration and temperature of the hardener and set the hardening time reasonably.
(3) Porosity and inclusions
1) Problem: Porosity and inclusions often appear inside the casting, affecting the beauty and strength of the jewelry.
2) Solution: Rationally design the pouring and riser system so that the molten metal can flow smoothly and fully compensate for shrinkage. Preheat and clean the mold shell before pouring to remove impurities and moisture. In addition, control the temperature of the molten metal and the pouring speed to avoid inclusions.
(4) Cracks
1) Problem: Cracks may occur in castings due to unreasonable design or too fast cooling speed.
2) Solution: Optimize casting design to avoid large differences in wall thickness and transition mutations. Reasonably set up the pouring system and cooling system so that the casting can be cooled evenly. During the casting process, control the pouring temperature and speed of the molten metal to reduce thermal stress.
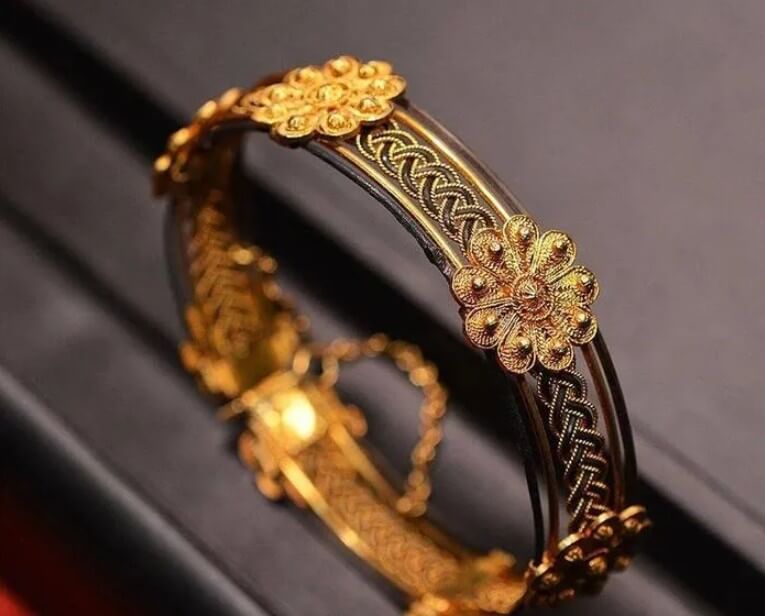
(5) Rough surface
1) Problem: The surface of the casting is rough, with sand sticking or burrs.
2) Solution: Improve the shell manufacturing process to ensure uniform coating and sand spreading. Increase the temperature of the dewaxing water, shorten the dewaxing time, and fully harden the shell. Carefully clean the shell before roasting to remove impurities and floating sand.
(6) Uneven color
1) Problem: Uneven color or black spots appear on the surface of the jewelry.
2) Solution: Control the composition of the molten metal and the pouring temperature to ensure uniform alloy composition. Improve the polishing process and use appropriate polishing materials and parameters. For the problem of black spots on the surface, the concentration of the spraying agent and the blowing time after spraying can be adjusted.
6.Conclusion
In today’s era, investment casting jewelry has been favored by more and more consumers for its unique artistic charm and cultural connotation. Whether as a daily wear ornament or as a collection, investment casting jewelry can bring endless beauty and surprises to people.