Let you quickly understand gravity casting
1.Definition of Gravity Casting
Gravity casting is an advanced metal casting process that uses reusable molds to produce high-quality, dimensionally accurate metal parts. A significant difference from other casting methods is that gravity casting uses gravity to fill the molten metal into the mold cavity, hence the name.
2.Working Principle of Gravity Casting
(1) Preparation Design
The gravity casting process begins with the production of the mold. The mold consists of two parts: a fixed part and a movable part. By precision machining these two halves, a cavity representing the shape of the desired part can be formed. The design and manufacture of the mold must be very precise to ensure the quality and dimensional accuracy of the final casting.
(2) Mold Coating
The purpose of applying refractory materials or special mold release agents to the mold cavity is to facilitate the demolding of the hardened casting from the mold and to improve the surface quality of the casting. The selection and application of the coating must be optimized according to the specific metal material and casting requirements to ensure the best results.
(3) Preheating
Preheat the mold to a certain temperature. This operation ensures even heat distribution and prevents the molten metal from solidifying prematurely. Controlling the preheat temperature is critical. Temperatures that are too high or too low can affect the quality and performance of the casting.
(4) Metal Casting
Once the mold reaches the desired temperature, the molten metal is poured into the mold cavity. At this point, gravity comes into play, helping to smoothly flow and fill the cavity, ensuring accurate reproduction of complex elements. The injection speed and metal temperature must be strictly controlled to avoid defects and uneven filling.
(5) Cooling and Solidification
After injection, the metal begins to harden and gradually takes the shape of the cavity. The cooling process can be accelerated by circulating coolant in the mold or placing it in a temperature-controlled environment. Controlling the cooling rate is critical to the microstructure and properties of the casting. Cooling too fast or too slow can cause defects.
(6) Opening the mold and removing the casting
Once the metal is completely hardened, the mold is opened and the casting is removed. The casting may require further finishing, such as trimming, deburring, or machining, to obtain the desired final shape and surface quality. The finishing process must be precisely controlled according to the specific requirements of the part to ensure the quality and performance of the final product.
3.Advantages of Gravity Casting
(1) Excellent Dimensional Accuracy
Gravity casting has excellent dimensional accuracy and repeatability, and is very suitable for the production of complex and precise parts. Through precise mold design and manufacturing, as well as strict process control, injection molding can ensure that the dimensional tolerance of parts is controlled within a very small range, meeting the stringent requirements of the high-tech manufacturing field.
(2) Excellent Surface Finish
Precise mold cavities and controlled curing processes can provide smooth, fine surface finishes, usually without much post-processing. This not only improves production efficiency, but also reduces production costs and ensures the appearance quality of parts.
(3) Economic Benefits
Compared with other manufacturing technologies such as CNC machining, gravity casting is an economical and efficient large-scale production method. Casting molds can be reused, reducing mold costs. At the same time, gravity casting has high production efficiency and can produce a large number of parts in a short time, reducing unit costs.
(4) Performance
High production efficiency, a large number of parts can be produced in a short time. By optimizing process parameters and automated production, high-speed and efficient production can be provided to meet the market demand for large quantities of high-quality parts.эффективность и позволяет изготавливать большое количество деталей за относительно короткое время, снижая себестоимость единицы продукции.
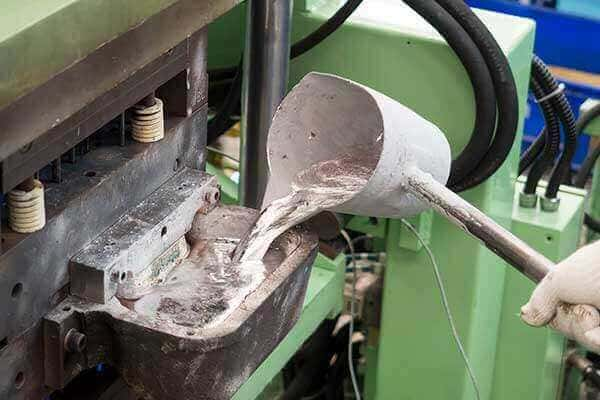
4.Gravity Casting Application Scenarios
Gravity casting is common in many complex engineering fields, such as automotive, defense, shipbuilding, structural and architectural applications, electronics, consumer electronics, and complex mechanical engineering. Its parts have less porosity than many alternatives and are very lightweight and environmentally friendly when cast from aluminum alloys. For industries such as automotive and aerospace, these advantages are often critical to productivity and business growth. In addition, gravity casting is able to create precise shapes that enable components to meet strict specifications. For advanced products, the margin for error is small and reliable performance can be provided in fast, high-volume production runs. This can balance the cost of initial complex tooling and create a favorable long-term return on investment.
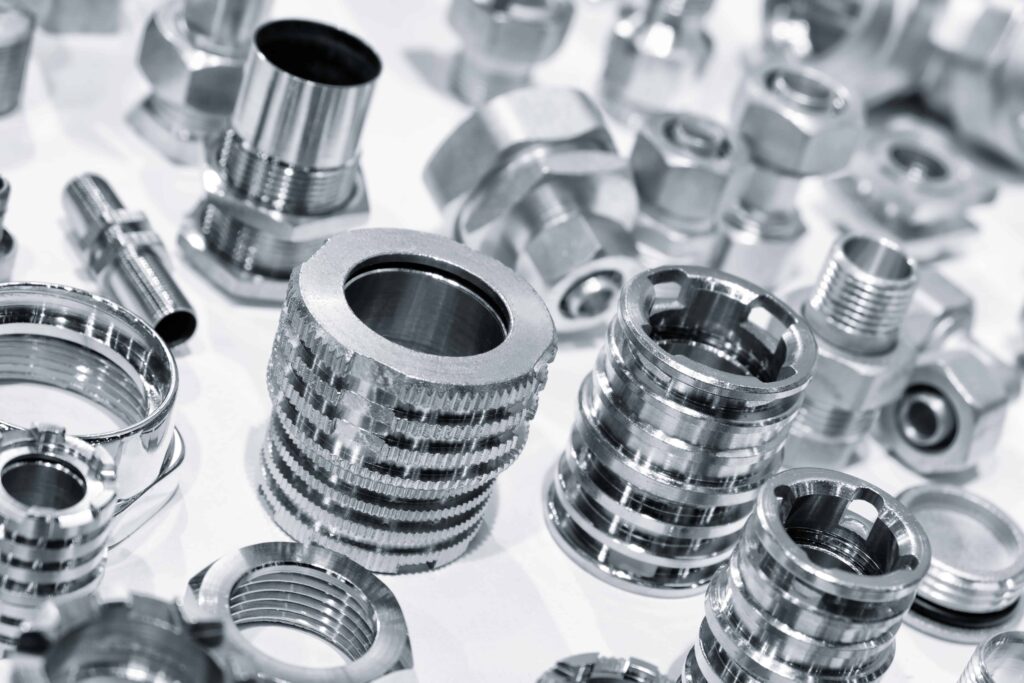
5.Conclusion
Gravity casting is an efficient and precise manufacturing method that offers many advantages for the production of complex metal parts. Using gravity, the method can create complex structures with excellent dimensional accuracy and superior surface finish. Whether in the automotive, aerospace or industrial fields, gravity casting has proven to be a reliable choice for high-quality metal parts.