Extrusion Die: A Comprehensive Guide to Process Optimization
Extrusion dies, as an important metal forming die, have occupied a pivotal position in modern manufacturing. Through extrusion dies, parts with excellent mechanical properties and surface quality can be produced, while achieving high material utilization. This article is a comprehensive guide to extrusion die technology from multiple dimensions. Here, you can find the relevant important information you want to obtain.
1.Definition of extrusion die
An extrusion die is a tool used for metal plastic forming. It applies huge pressure to the metal blank in the die cavity, forcing the metal to undergo directional plastic deformation, thereby extruding it through the die hole to obtain parts or semi-finished products with the required cross-sectional shape, size and certain mechanical properties. This process is similar to the process of squeezing toothpaste. Aluminum extrusion dies are a common application and are widely used in the manufacture of various aluminum profiles, such as pipes, bars and profiles.
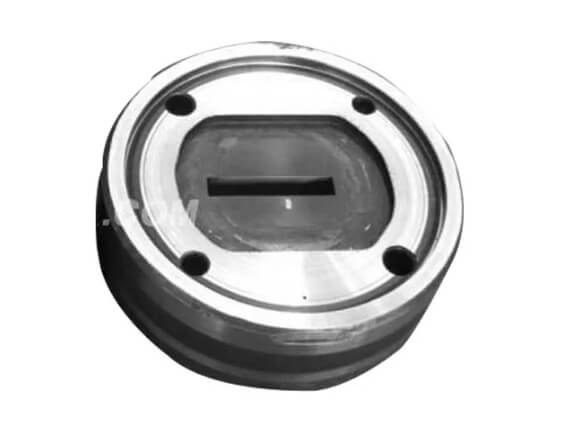
2.Working principle of extrusion die
(1) Die structure and its function
1) Concave die:
The concave die is one of the core components of the extrusion die. Its internal cavity determines the shape of the final extruded part. The concave die usually adopts a combined structure to eliminate stress concentration and improve strength.
2) Punch:
During the extrusion process, the punch applies pressure to the metal blank, causing it to undergo plastic deformation. The design of the punch needs to take into account strength and wear resistance to ensure stable operation under high pressure.
3) Extrusion barrel:
It is used to hold the metal blank and provide necessary support during the extrusion process. The extrusion barrel also needs to have high strength and rigidity to withstand the huge extrusion force.
4) Guide pins and guide sleeves:
Ensure the precise guidance of the mold during the closing and opening process, and improve the stability and life of the mold.
(2) Extrusion process analysis
1) Forward extrusion:
The metal flow direction is consistent with the direction of the punch movement. The metal blank is subjected to the pressure of the punch in the extrusion barrel and is squeezed out of the concave mold cavity to form a part of the desired shape.
2) Reverse extrusion:
The metal flow direction is opposite to the direction of the punch movement. The punch enters the interior of the metal blank, causing it to flow outward and form a cup-shaped or other hollow part.
3) Composite extrusion:
Part of the metal blank flows in the same direction as the punch, while the other part flows in the opposite direction. This method is suitable for manufacturing parts with complex shapes.
4) Reducing extrusion:
A positive extrusion method with a small degree of deformation, mainly used to manufacture stepped shaft parts with similar diameters.
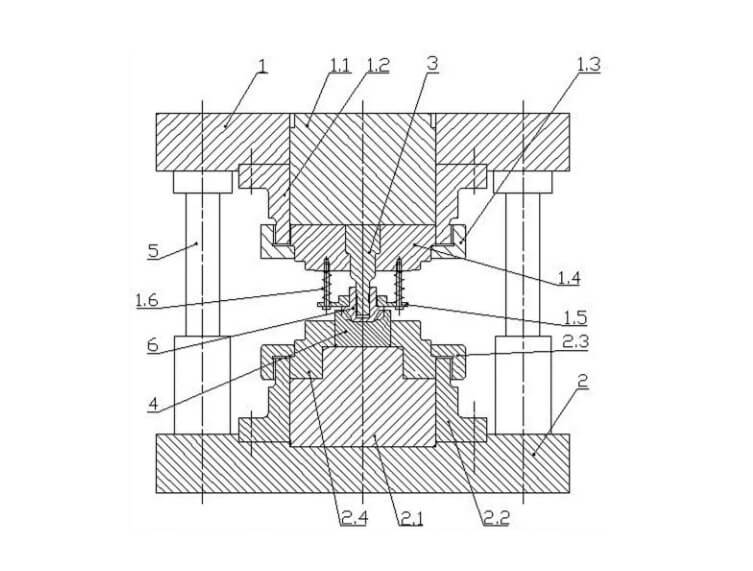
Summary:
The working principle of the extrusion die is to apply pressure to the metal blank through the die structure, causing it to undergo plastic deformation in the cavity, thereby obtaining parts of the desired shape and size. The high efficiency and precision of the extrusion die make it widely used in modern manufacturing.
3.Classification and characteristics of extrusion die technology
(1) Classification by material:
1) Metal extrusion die:
It is used for extrusion forming of metal materials and can withstand high temperature, high pressure and wear. The design of the metal extrusion die needs to consider the flow characteristics of the material to ensure that the extruded metal product has the desired shape and dimensional accuracy.
2) Non-metallic extrusion die:
It is suitable for non-metallic materials such as plastics, rubber, etc. This type of die usually does not need to withstand extremely high temperatures and pressures, but needs to consider the molten state and fluidity of the material to ensure the quality of the product.
(2) Classification by process:
1) Cold extrusion die:
The material is extruded at room temperature and is suitable for metal materials with good plasticity. The characteristics of cold extrusion dies are high production efficiency and good product surface quality, but the extrusion force is large and the strength and wear resistance of the mold material are high.
2) Hot extrusion die:
The material is extruded at high temperature and is suitable for metal materials with high melting point and high strength. Hot extrusion dies need to consider the thermal expansion and thermal conductivity characteristics of the material, as well as the heat resistance and thermal stability of the mold.
3) Isothermal extrusion die:
The material is extruded at a constant temperature to reduce the internal stress of the material caused by temperature changes and improve the performance of the product. Isothermal extrusion dies usually require precise temperature control to ensure temperature uniformity during the extrusion process.
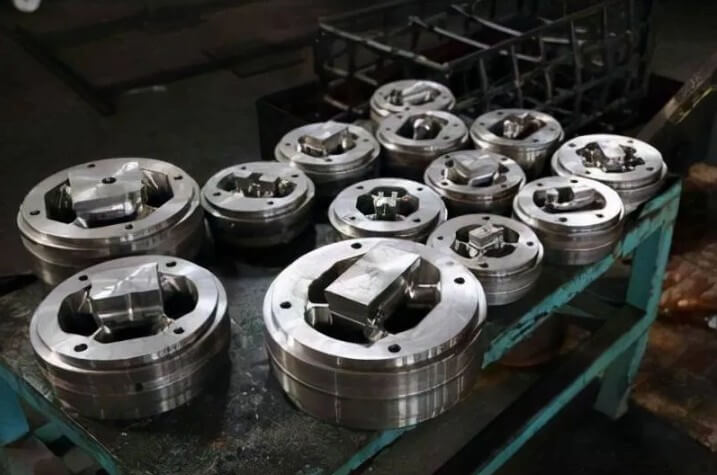
4.Design and manufacturing technology of extrusion dies
(1) Design:
Use CAD software to design the mold, including the size, shape, cooling system and exhaust holes of the mold. The fluidity of the material and the strength of the mold should be considered during the design process.
(2) Material selection:
Select high-strength, high-temperature-resistant and wear-resistant mold steel materials, such as H13 steel, which have good heat treatment performance and mechanical properties.
(3) Blank manufacturing:
According to the design drawings, the mold steel material is cut into the required blank size and subjected to preliminary forging or heat treatment to improve the internal structure and mechanical properties of the material.
(4) Rough machining:
Use lathes, milling machines and other machine tools to perform rough machining on the blank, remove excess material, and initially form the shape and basic dimensions of the mold.
(5) Heat treatment:
Heat treatment is performed on the mold, including quenching and tempering, to improve the hardness and wear resistance of the mold. The hardness of the mold after heat treatment is generally between HRC45-50.
(6) Finishing:
Use CNC machine tools (CNC) for finishing to ensure the dimensional accuracy and surface finish of the mold. Finishing includes turning, milling, drilling, wire cutting and other processes. Pay special attention to the machining accuracy of the cavity and working parts to ensure product quality.
(7) Electrospark machining:
Electrospark machining (EDM) is performed on complex parts of the mold to further improve the accuracy and surface quality of the mold.
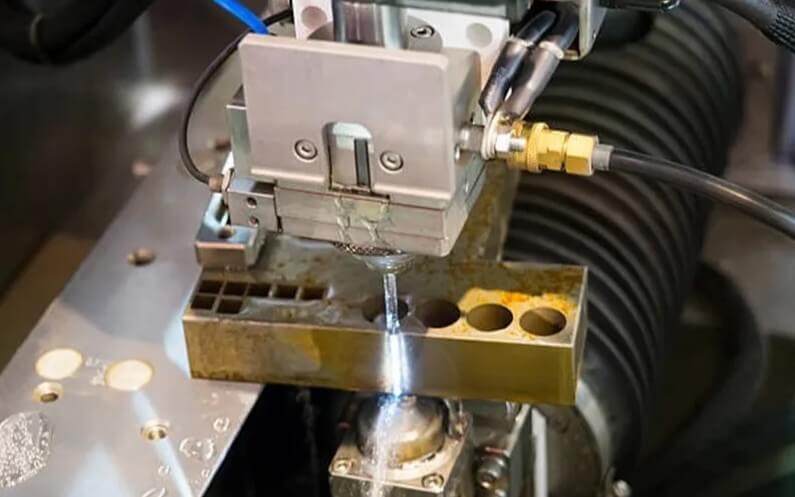
(8) Surface treatment:
Surface treatment of the mold, such as nitriding and chrome plating, is performed to improve the wear resistance and corrosion resistance of the mold.
(9) Assembly and debugging:
Assemble the various parts of the mold to ensure that the overall structure and working state of the mold meet the design requirements. Perform mold trials to verify the working performance and product quality of the mold, and make necessary adjustments and optimizations based on the results of the mold trials.
5.Material selection for extrusion dies
(1) Alloy tool steel:
It has the characteristics of high hardness, high strength and good wear resistance.
(2) H13 mold steel:
It is widely used in the hot forging process of aluminum profile factories. This steel has high cost performance and good durability.
(3) DC53 and LD mold steel:
It is used for cold extrusion dies, but there is a risk of cracking.
(4) LG die steel:
It has excellent toughness and is suitable for cold extrusion dies. There is no need to worry about the punch material breaking.
(5) Cr12MoV steel:
It is suitable for warm extrusion dies of copper. It has high hardness, high strength and good wear resistance.
(6) Metal ceramics:
It has high hardness, good wear resistance, good red hardness, can maintain high hardness at high temperature, low affinity, is not easy to react with materials, does not stick to the mold, has a long life and reduces costs.
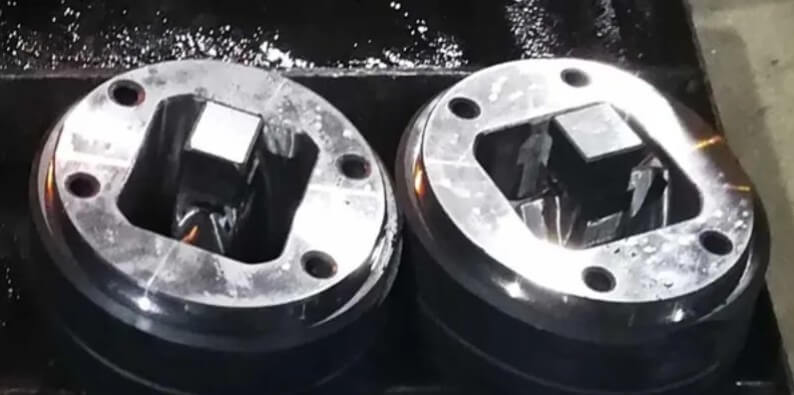
5.Optimization of key process parameters of extrusion dies
(1) Temperature control:
Temperature is a crucial parameter in the extrusion die process. Optimizing the heating temperature can improve the fluidity of the metal, reduce internal stress, and improve the surface quality of the product. Usually, it is necessary to find the optimal heating temperature range through a combination of experiments and simulations to ensure that the material will neither overheat nor underheat during the extrusion process.
(2) Extrusion speed:
The extrusion speed directly affects the production efficiency and product quality. A faster extrusion speed can improve production efficiency, but may lead to an increase in internal defects in the product, such as cracks and pores. Although a slower extrusion speed helps improve product quality, it will reduce production efficiency. Therefore, it is necessary to find a balance between the two.
(3) Lubrication conditions:
Good lubrication can reduce friction, increase die life, and improve product surface quality. Selecting the right lubricant and lubrication method is the key. Usually, it is necessary to determine the best lubrication scheme through experiments based on material properties and process requirements.
(4) Die design:
Mold design has an important influence on the optimization of extrusion die process parameters. Reasonable die structure can improve metal flow uniformity and reduce defects. In addition, the design of the die cooling system is also very critical, which directly affects the die life and product quality.
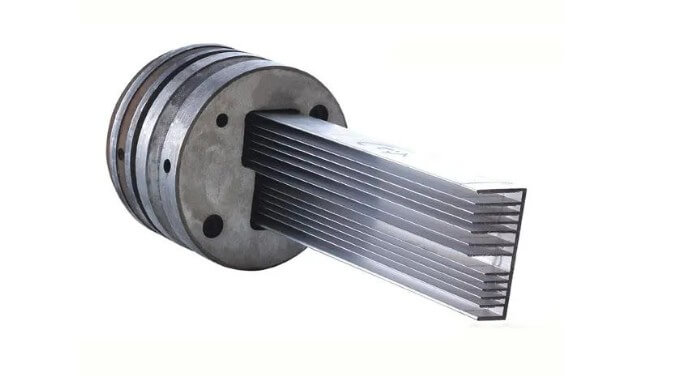
6.Optimization method of extrusion die structure
(1) Optimization of some large-section hollow profile dies
1) Bias bridge design:
The upper die is designed as a bias bridge structure, and the lower die adds convex ribs in the hopper. This can hinder metal flow, keep the weld away from the large surface or decorative surface, and improve the surface quality of the profile.
2) Rib design:
In the welding chamber, a rib of appropriate length is placed in front of the large-surface die hole, similar to a low wall, to hinder the flow of metal and avoid problems such as large-surface ripples and plane gap tolerance.
(2) Optimization of double-die hole hollow profile molds with easy wall deviation
1) Preset offset allowance:
During the mold design process, a cross-sectional dimension offset allowance is reserved in advance to deal with possible wall deviation.
2) Partition-type diverter rib:
Add a partition-type diverter rib in the middle of the two die holes in the silo to ensure that the feeding of the two die holes is relatively stable and reduce wall deviation defects.
(3) Optimization of flat profile molds with small openings and large cantilever areas
1) Bridge feed plate:
Design the direct feed plate as a bridge or cantilever bridge feed plate, so that the cantilever surface under the bridge is placed, reducing the positive pressure on the cantilever and avoiding elastic deformation and fracture.
2) Combination mode:
For profiles with extremely small openings, a combination mode design is used to ensure that the openings fit tightly.
(4) Optimization of long-section flat profile molds with large aspect ratios
The bridge feed plate design is used to effectively adjust the intermediate metal flow rate, so that the material flow rate at each part of the die hole is balanced and deformation defects are reduced.
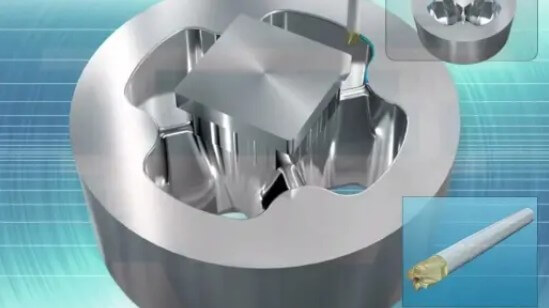
7.Causes and solutions for extrusion die failure
In the manufacturing industry, extrusion die failure is a common but complex problem that not only affects production efficiency but also increases production costs.
(1) Wear failure
Wear failure is one of the most common failure forms of extrusion dies, mainly caused by friction under high temperature and high pressure. The mold cavity surface and the sizing belt surface are worn due to friction, resulting in changes in the mold geometry and inability to continue to be used.
Solutions include selecting mold materials with better wear resistance, such as 4Cr5MoSiV1 steel, and optimizing the mold surface treatment process, such as nitriding, to improve the hardness and wear resistance of the mold surface.
(2) Cracking failure
During the use of the mold, cracks may appear and gradually expand due to unreasonable design, material defects or improper heat treatment, eventually leading to mold breakage.
Preventive measures include optimizing the mold design, ensuring that the radius of the corners at the transition is reasonable, and strictly controlling the heat treatment process to avoid microcracks. During use, pay attention to the control of mold preheating and extrusion parameters to reduce thermal stress.
(3) Deformation failure
Deformation failure is usually caused by insufficient mold material strength or improper heat treatment process. The mold may have problems such as cantilever eccentricity and sinking during use, resulting in the mold being unable to work properly.
To prevent deformation failure, a mold material with higher strength should be selected, and the heat treatment process should be correct to give full play to the strength and toughness of the mold steel. In addition, the design should ensure that the mold structure is reasonable to avoid stress concentration.
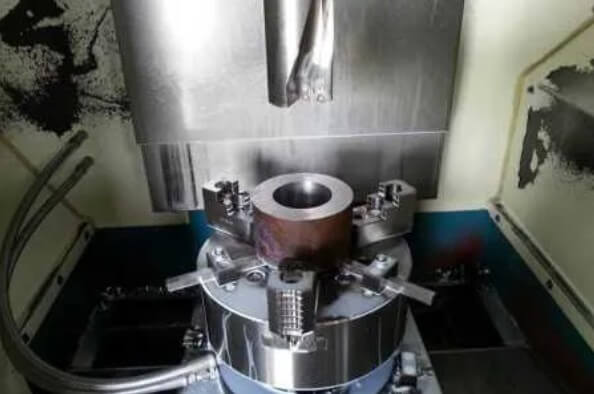
8.Maintenance and life extension plan for extrusion dies
(1) Selection of high-quality materials:
The selection of mold materials is crucial. Materials with high thermal stability, high hardness and good toughness should be selected, such as 4Cr5MoSiV1 steel (H13 steel). This material can withstand high temperature and high pressure environments, reducing the possibility of early failure.
(2) Optimize heat treatment process:
Reasonable heat treatment process can significantly improve the performance and life of the mold. Preheating, quenching and tempering processes require strict control of temperature and time to reduce internal stress and improve the mechanical properties of the mold.
(3) Reasonable design of mold structure:
Mold design should consider the uniformity of metal flow and avoid stress concentration. For example, for aluminum profiles with different wall thicknesses, unequal length working belt design can be adopted to ensure the uniformity of metal flow.
(4) Regular maintenance:
Clean, lubricate and inspect the mold regularly, and replace damaged parts in time. The mold should be polished and nitrided before and after use to improve surface hardness and wear resistance.
(5) Scientific use of mold:
Control the extrusion speed to avoid local overheating of the mold due to excessive speed. In the early and late stages of mold use, a lower use intensity should be used to extend its service life.
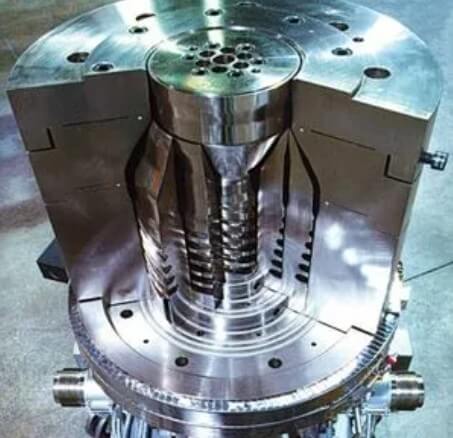
(6) Strictly manage the mold use environment:
Keep the mold storage environment dry and clean to prevent the mold from being corroded by corrosive media. Use special tools for loading and unloading to prevent collision damage.
(7) Establish mold files:
Record the use and maintenance of the mold, including the number of extrusions, nitriding treatment records, etc., so as to adjust the use strategy and perform necessary maintenance in a timely manner.
9.Summary
In summary, in order to maintain and extend the service life of the extrusion die, it is necessary to consider multiple aspects such as material selection, heat treatment process, reasonable mold design and scientific use. By taking effective measures, the service life of the extrusion die can be significantly improved, production costs can be reduced, and production efficiency can be improved.
What do you think?
[…] the design and manufacturing process of aluminum extrusion dies, there are several key factors that cannot be ignored. The selection of materials, the design of […]