Is cast iron or aluminum a better material for an engine blocks?
As the core component of the engine, the material selection of the engine blocks directly affects the performance, durability and economy of the engine. At present, aluminum alloy and cast iron are the two most common engine blocks materials.
This article will conduct a comprehensive comparative analysis of aluminum alloy and cast iron engine blocks from multiple aspects such as weight, strength, heat dissipation, cost, manufacturing process, environmental protection, application scenarios, maintenance and repair, and future development trends to help you understand the advantages and disadvantages of the two.
1.Aluminum alloy and cast iron engine blocks: weight comparison
(1) Aluminum alloy cylinder block
1) Lightweight advantage:
The density of aluminum alloy is about 2.7 g/cm³, which is much lower than the 7.8 g/cm³ of cast iron. Therefore, aluminum alloy engine blocks are lighter.
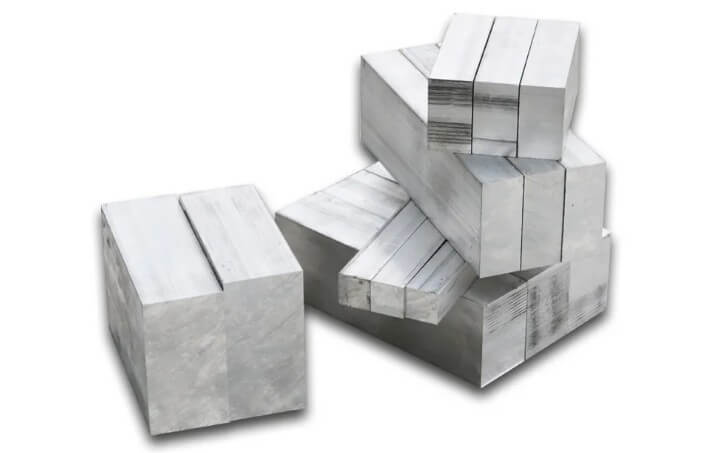
2) Vehicle weight reduction:
Lightweight design helps to reduce vehicle weight, improve fuel economy and handling performance.
3) Energy saving and emission reduction:
Lightweight design helps to reduce exhaust emissions and meet environmental protection requirements.
(2) Cast iron cylinder block
1) Heavy weight:
The high density of cast iron makes the cylinder block heavier, increasing the weight of the vehicle.
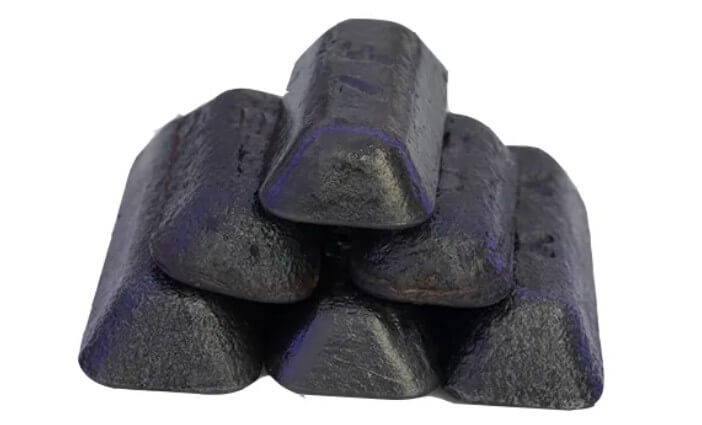
2) Impact on fuel consumption:
A heavier cylinder block may lead to increased fuel consumption, especially in urban driving.
3) Reduced handling:
A heavier cylinder block may affect the vehicle’s handling performance, especially when driving at high speeds and making sharp turns.
2.Aluminum alloy and cast iron engine blocks: strength and durability comparison
(1) Aluminum alloy cylinder block
1) Lower strength:
The strength of aluminum alloys is generally lower than that of cast iron, especially under high temperature and high load conditions.
2) Strengthening design:
The strength of aluminum alloy cylinder blocks can be improved through alloying treatment and strengthening design (such as increasing wall thickness and using reinforcing ribs).
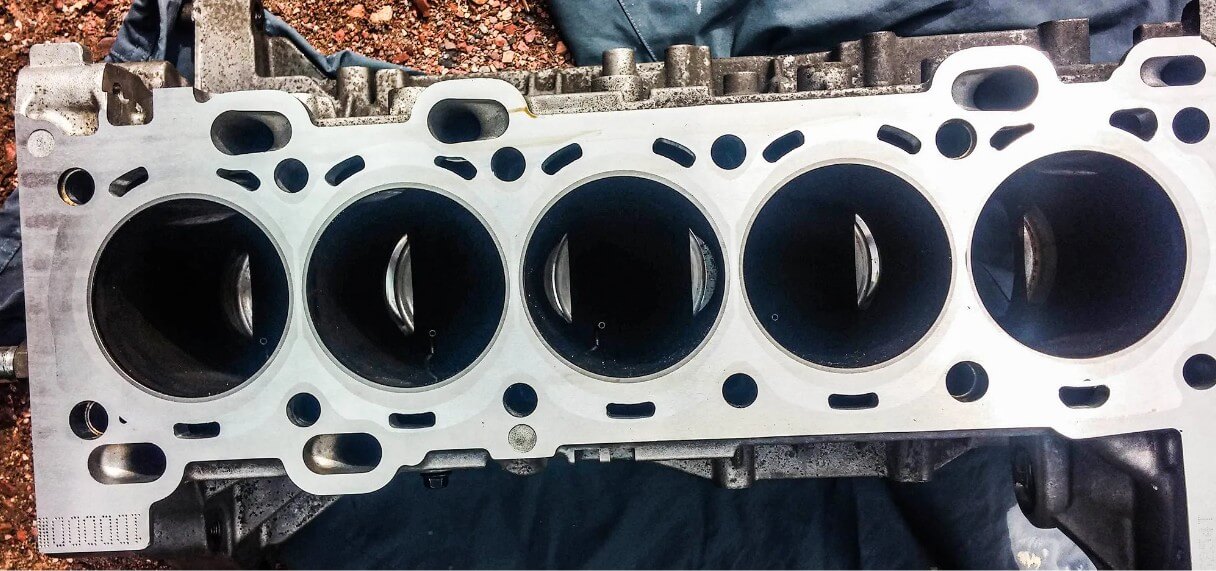
3) Durability:
In high-performance engines, the durability of aluminum alloy cylinder blocks may not be as good as that of cast iron cylinder blocks.
4) Fatigue life:
The fatigue life of aluminum alloys is shorter and requires regular maintenance and inspection.
(2) Cast iron cylinder block
1) High strength:
Cast iron has high strength and hardness and can withstand higher mechanical and thermal stresses.
2) High durability:
Cast iron cylinder blocks perform well under high load and high temperature conditions and are suitable for high-performance and heavy-duty engines.
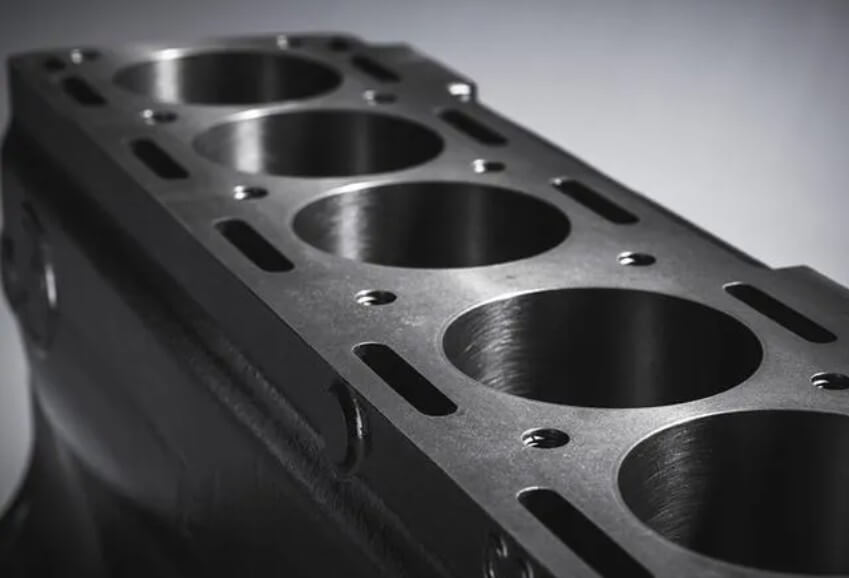
3) Long fatigue life:
Cast iron has a long fatigue life and is suitable for long-term use.
3.Aluminum alloy and cast iron engine blocks: Comparison of heat dissipation performance
(1) Aluminum alloy cylinder block
1) Good heat dissipation:
Aluminum alloy has high thermal conductivity and can quickly transfer heat to the cooling system, improving heat dissipation efficiency.
2) Reduce thermal stress:
Good heat dissipation performance helps reduce the thermal stress of the engine and extend its service life.
3) Simplified cooling system:
Due to its good heat dissipation performance, the cooling system of the aluminum alloy cylinder block can be relatively simplified, reducing manufacturing costs.
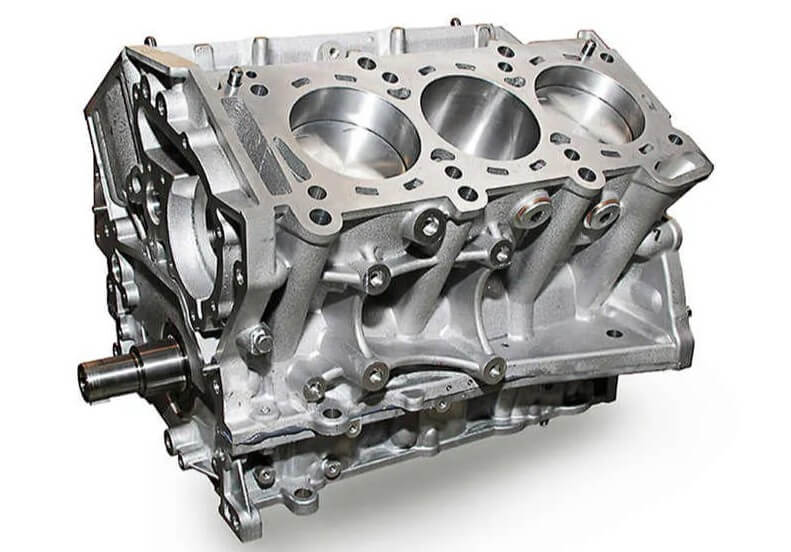
(2) Cast iron cylinder block
1) Poor heat dissipation:
Cast iron has low thermal conductivity and its heat dissipation performance is not as good as that of aluminum alloy.
2) High thermal stress:
Poor heat dissipation may lead to local overheating, increase thermal stress and affect engine life.
3) Complex cooling system:
Due to poor heat dissipation, cast iron cylinder blocks require more complex cooling systems, increasing manufacturing costs.
4.Aluminum alloy and cast iron engine blocks: cost comparison
(1) Aluminum alloy cylinder block
1) High material cost:
The material cost of aluminum alloy is relatively high, which increases the manufacturing cost of the cylinder block.
2) High processing cost:
The processing of aluminum alloy is difficult, requiring more complex processes and equipment, further increasing costs.
3) High maintenance cost:
The maintenance and repair costs of aluminum alloy engine cylinder blocks are high, especially under high temperature and high load conditions.
(2) Cast iron cylinder block
1) Low material cost:
The material cost of cast iron is relatively low, which reduces the manufacturing cost of the cylinder block.
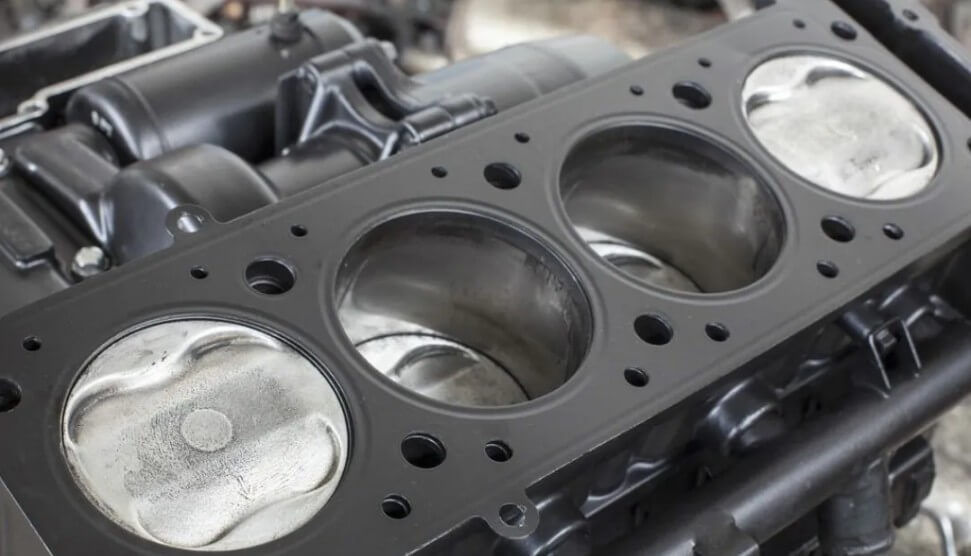
2) Low processing cost:
The processing technology of cast iron is relatively simple and the cost is low.
3) Low maintenance cost:
The maintenance and repair cost of cast iron cylinder block is low, which is suitable for long-term use.
5.Aluminum alloy and cast iron engine blocks: Comparison of manufacturing processes
(1) Aluminum alloy cylinder block
1) Casting process:
Aluminum alloy cylinder block usually adopts high-pressure casting or low-pressure casting process to ensure high precision and high strength.
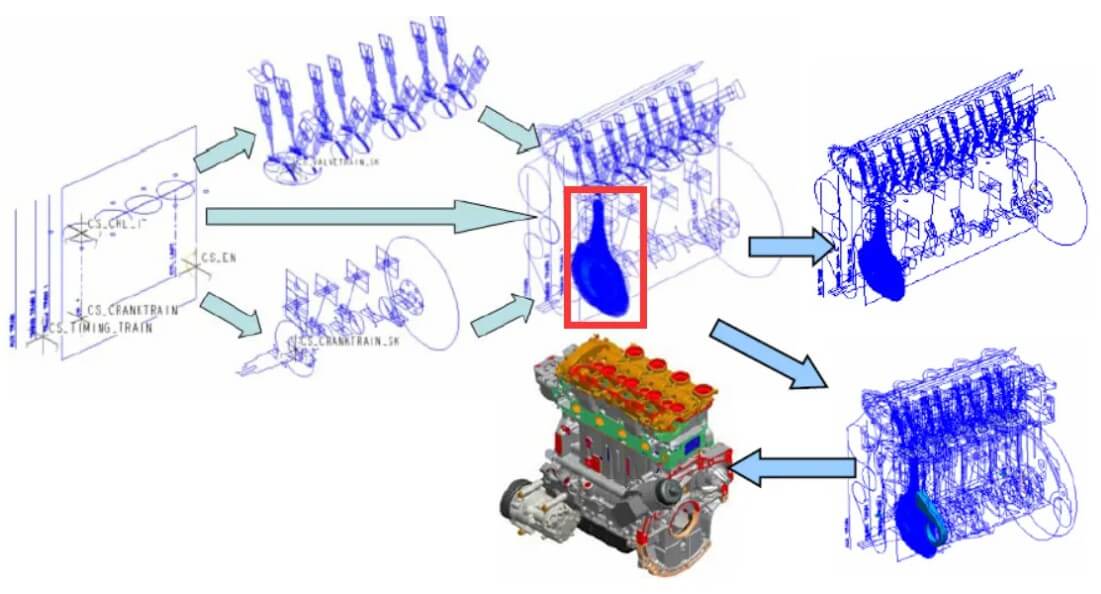
2) Processing difficulty:
Aluminum alloy is difficult to process, requiring high-precision CNC machine tools and advanced processing technology.
3) Surface treatment:
Aluminum alloy cylinder block usually requires surface treatment (such as anodizing) to improve corrosion resistance and wear resistance.
(2) Cast iron cylinder block
1) Casting process:
Cast iron cylinder block usually adopts sand casting or metal mold casting process, which is relatively mature.
2) Processing difficulty:
Cast iron is less difficult to process and is suitable for large-scale production.
3) Surface treatment:
Cast iron cylinder block usually requires surface treatment (such as chrome plating) to improve corrosion resistance and wear resistance.
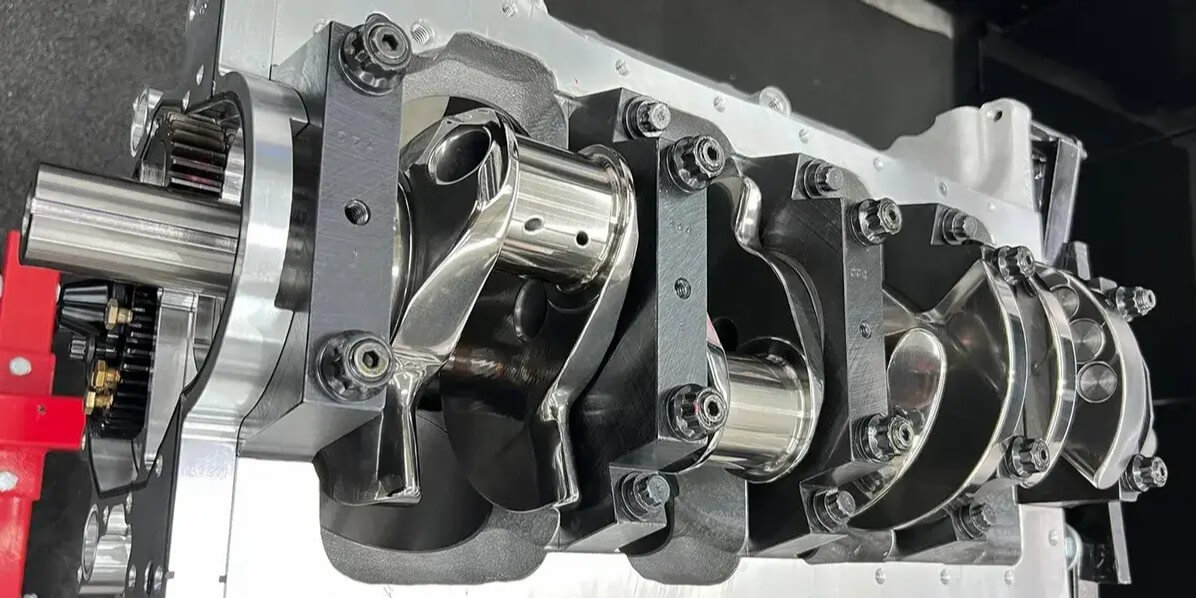
6.Aluminum alloy and cast iron engine blocks: environmental protection comparison
(1) Aluminum alloy cylinder block
1) Strong recyclability:
Aluminum alloy has good recyclability and meets environmental protection requirements.
2) High production energy consumption:
The production energy consumption of aluminum alloy is high, which increases the environmental burden.
3) Recycling:
The recycling efficiency of aluminum alloy is high, which helps to reduce resource waste.
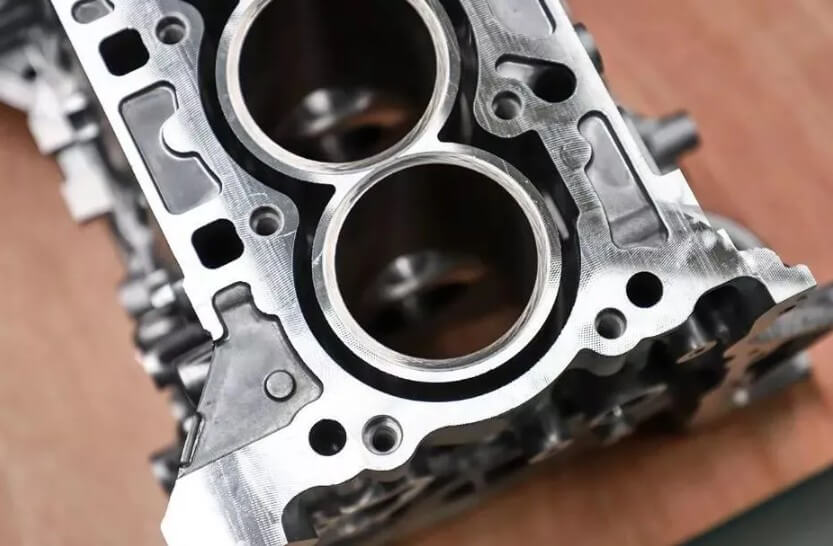
(2) Cast iron cylinder block
1) General recyclability:
The recyclability of cast iron is poor, and the energy consumption during the recycling process is high.
2) Low production energy consumption:
The production energy consumption of cast iron is low, but the environmental impact during the recycling process is large.
3) Resource consumption:
The production of cast iron requires a large amount of iron ore, and the resource consumption is large.
7.Aluminum alloy and cast iron engine blocks: application scenario comparison
(1) Aluminum alloy cylinder block
1) Passenger car:
Aluminum alloy cylinder blocks are widely used in passenger cars, especially small cars and energy-saving cars, to improve fuel economy and handling performance.
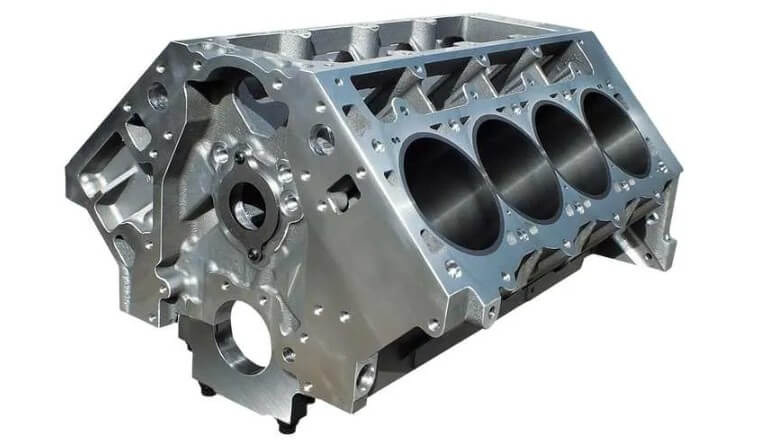
2) High-performance vehicles:
Some high-performance vehicles also use aluminum alloy cylinder blocks, which meet high load requirements through enhanced design.
3) New energy vehicles:
The application of aluminum alloy cylinder blocks in new energy vehicles is gradually increasing to meet the requirements of lightweight and energy saving.
(2) Cast iron cylinder block
1) Commercial vehicles:
Cast iron cylinder blocks are widely used in commercial vehicles and heavy vehicles to meet high strength and durability requirements.
2) High-performance vehicles:
Some high-performance vehicles and racing cars still use cast iron cylinder blocks to withstand extremely high mechanical and thermal stresses.
3) Construction machinery:
Cast iron cylinder blocks are widely used in construction machinery to meet the needs of high loads and harsh working conditions.
8.Aluminum alloy and cast iron engine blocks: maintenance and repair comparison
(1) Aluminum alloy cylinder block
1) High maintenance cost:
The maintenance and repair costs of aluminum alloy cylinder blocks are relatively high, especially under high temperature and high load conditions.
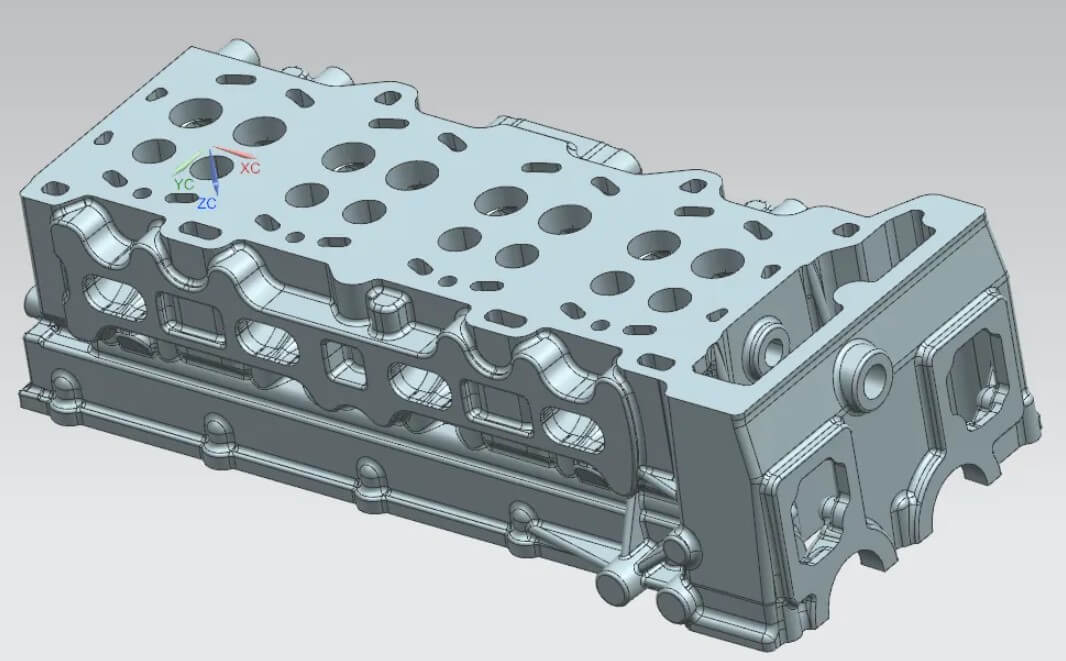
2) Difficult to repair:
The repair of aluminum alloy cylinder blocks is difficult and usually requires professional equipment and technology.
3) Regular inspection:
Aluminum alloy cylinder blocks require regular inspection and maintenance to ensure their performance and life.
(2) Cast iron cylinder blocks
1) Low maintenance cost:
The maintenance and repair costs of cast iron cylinder blocks are low, making them suitable for long-term use.
2) Easy repair:
The repair of cast iron cylinder blocks is relatively easy, making them suitable for use under harsh conditions.
3) Strong durability:
The durability of cast iron cylinder blocks is strong, reducing the frequency of maintenance and repair.
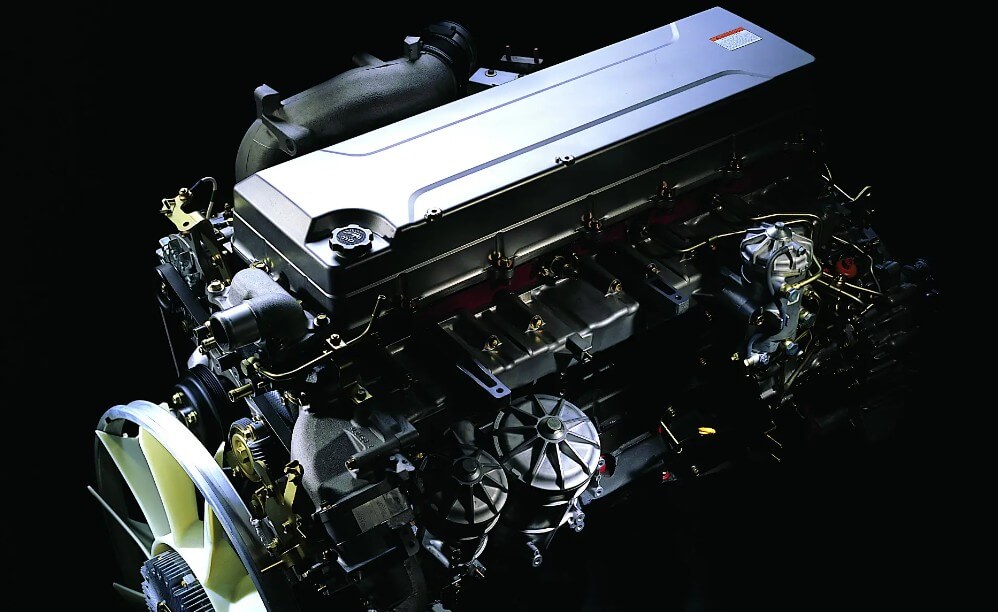
9.Aluminum alloy and cast iron engine blocks: future development trends
(1) Aluminum alloy cylinder blocks
1) Lightweight trend:
With the improvement of environmental protection requirements, the lightweight advantages of aluminum alloy cylinder blocks will become more prominent.

2) Technological progress:
The application of new materials and new processes will further improve the strength and durability of aluminum alloy cylinder blocks.
3) New energy vehicles:
The application of aluminum alloy cylinder blocks in new energy vehicles will gradually increase to meet lightweight and energy-saving requirements.
(2) Cast iron cylinder block
1) High performance requirements:
In the field of high-performance and heavy-duty engines, cast iron cylinder blocks will continue to occupy an important position.
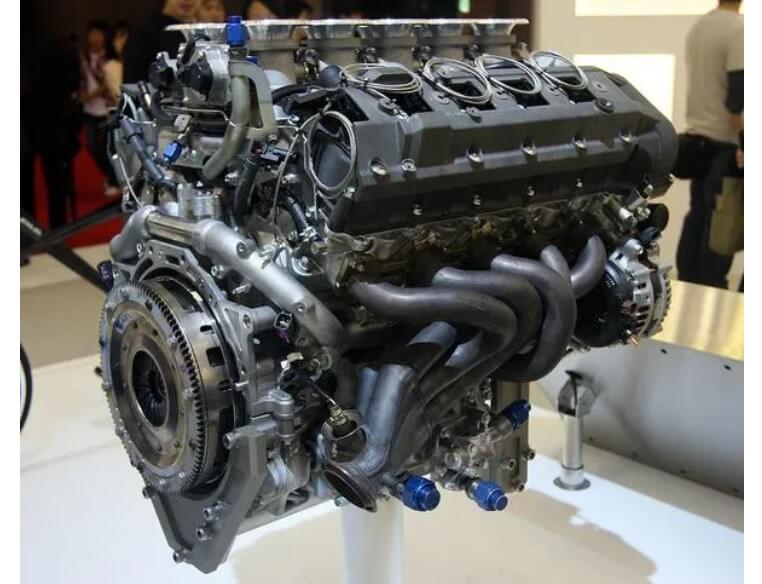
2) Environmental pressure:
With the improvement of environmental protection requirements, the environmental performance of cast iron cylinder blocks will face challenges.
3) Material improvement:
By improving cast iron materials (such as ductile iron), its performance and environmental protection can be improved.
10.Conclusion
Aluminum alloy and cast iron engine blocks have their own advantages and disadvantages and are suitable for different application scenarios. Aluminum alloy cylinder blocks have advantages in lightweight, heat dissipation and environmental protection, and are suitable for passenger cars and energy-saving vehicles; while cast iron cylinder blocks have excellent performance in high strength, durability and cost, and are suitable for commercial vehicles and heavy vehicles.
The choice of which material to use for the engine blocks should be comprehensively considered based on specific needs and budget.