Engine blocks production and processing technology
Engine blocks as the core component of the engine, its production and processing technology directly affects the performance and reliability of the engine. Cylinder block manufacturing involves a variety of material selection, complex design and precision machining technology. In this paper, we will introduce the engine blocks materials, production and processing technology and so on.
1.Engine blocks material selection
(1) gray cast iron
Gray cast iron is the traditional cylinder material, which has good casting performance, vibration damping and wear resistance, and relatively low cost. The graphite in gray cast iron can effectively lubricate the internal cylinder block, reducing friction and wear. However, the weight of gray cast iron is large, and it is difficult to meet the needs of modern engine lightweight.
(2) Aluminum alloy
Aluminum alloy cylinder block has been widely used in recent years, and its main advantage lies in its light weight, which helps to improve the overall dynamics and fuel economy of the engine. Aluminum alloy has excellent thermal conductivity, which can effectively reduce the working temperature of the engine, but the strength and abrasion resistance of aluminum alloy are relatively poor, and it needs to be improved through special treatment.
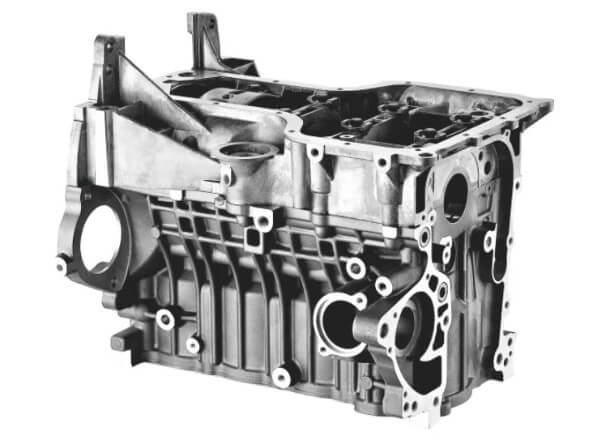
(3) Magnesium Alloy
Magnesium alloy is a lighter material than aluminum alloy, but its cost is higher and more difficult to process. Magnesium alloy cylinder block is used in high-performance engines and racing engines, which can significantly reduce the weight of the engine and improve the acceleration and handling of the vehicle.
(4) Composite materials
Some new composite materials have also begun to try to apply in the engine blocks manufacturing, such as carbon fiber reinforced composite materials. These materials have very high strength and rigidity, but at present the cost is high and the process is complex, has not been applied on a large scale.
2.The main structure and function of the engine blocks
(1) Cylinder block:
As the support structure of the engine, the interior contains cylinder holes for the installation of pistons and connecting rods. The cylinder block needs to withstand the impact and pressure of high temperature and high pressure combustion gases.
(2) Cylinder head:
Used to close off the top of the cylinder and form the combustion chamber together with the top of the piston and the cylinder wall. It is subjected to high temperature and pressure, and also serves as the mounting base for the gas distribution mechanism.
(3) Oil sump:
Located in the lower part of the cylinder block, it is used to store lubricating oil and to close the crankcase to prevent lubricating oil leakage.
(4) Crankcase:
Integrated inside the cylinder block, it accommodates the crankshaft and converts the linear motion of the piston into the rotary motion of the crankshaft, thus outputting power.

(5) Cooling system:
Includes water pumps, radiators, fans, water jackets, etc., which dissipate heat by circulating coolant to ensure that the engine operates within the normal temperature range.
(6) Lubrication system:
Consisting of oil pump, oil filter, etc., it provides lubricating oil to the relative moving parts to reduce friction and wear.
3.Design of the engine blocks
(1) structural design
The structural design of the engine blocks needs to take into account factors such as strength, stiffness and thermal performance. Modern cylinder block design usually adopts a compact structure to reduce weight and volume. The internal structure of the cylinder block, such as the water jacket and oil passages, needs to be reasonably laid out to ensure that the engine can be efficiently cooled and lubricated.
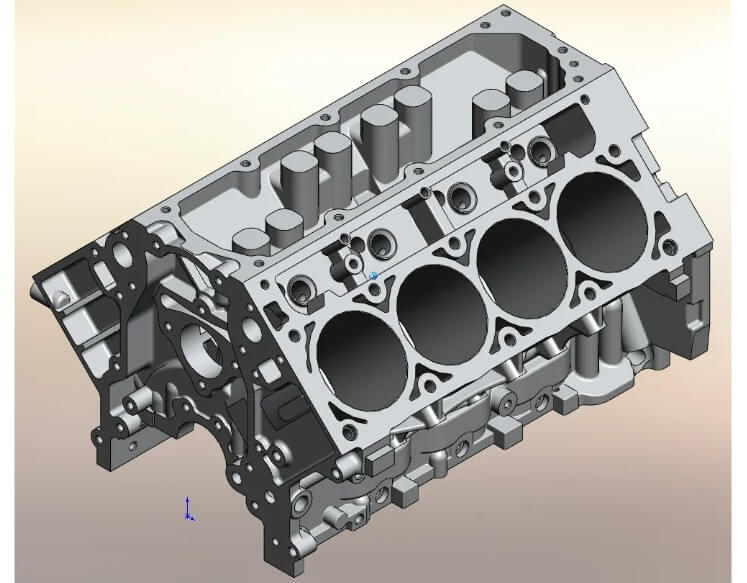
(2) Dimensional accuracy
The dimensional accuracy of the cylinder block directly affects the overall performance of the engine. The design needs to strictly control the diameter of the cylinder hole, cylindricity and the positional accuracy between the holes to ensure that the piston in the cylinder can move smoothly, reduce friction and wear.
(3) Surface treatment
The surface treatment design of the cylinder is also very critical. Common surface treatments include chrome plating, nitriding, etc. These treatments can significantly improve the wear resistance and corrosion resistance of the cylinder block.
4.Production process of engine blocks
The production process of the engine block is mainly casting process, the following are several common methods of cylinder casting:
(1) sand casting:
Sand casting is the traditional engine blocks casting method, the advantages of low cost, adaptability, but the casting of the dimensional accuracy and surface quality is poor.
(2) high-pressure casting:
High-pressure casting can significantly improve the dimensional accuracy and surface quality of castings, suitable for the production of aluminum alloy cylinder block. The principle is that the liquid metal is injected into the mold under high pressure, rapid solidification and shaping.
Die casting high dimensional accuracy, low surface roughness, and high productivity, every 3 minutes to complete the production of a cylinder, greatly saving time and labor costs.
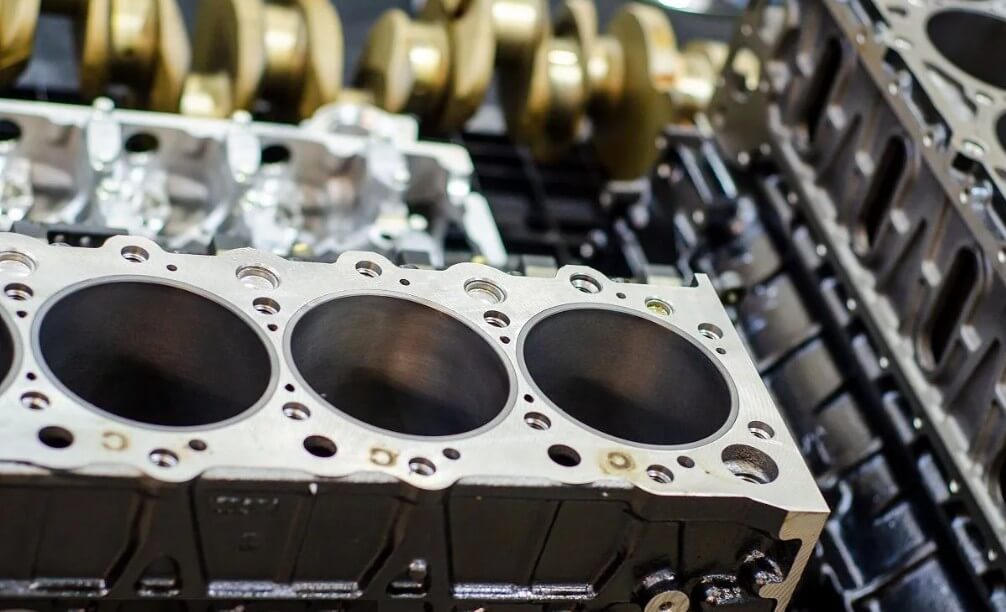
(3) disappearance mold casting:
Vanishing mold casting is an advanced casting process, can produce high precision, complex structure of the castings. The process uses foam models instead of traditional wood or metal molds, reducing the defects of the castings.
5.Engine blocks casting mold design
(1) Three-dimensional model design
The use of advanced CAD software, according to the structure and size requirements of the engine blocks, to establish an accurate three-dimensional model. The model should fully consider the characteristics of aluminum alloy material to ensure the feasibility and economy of the design.
(2) Design of pouring system and overflow system
Design an efficient pouring system to ensure that the liquid metal can be filled smoothly and quickly to avoid oxidized slag and gas ingress. The overflow system should be able to effectively discharge the gas and impurities in the mold cavity to prevent casting defects.
Referring to the design manual and the analysis results of the simulation software, optimize the structure and size of the inner sprue, cross sprue and overflow channel to ensure good shrinkage effect.
(3) Mold cavity and cooling system design
The design of mold cavity should ensure the surface finish and dimensional accuracy of the cavity to produce high quality castings. The design of the cooling system needs to reasonably arrange the cooling pipes, control the thermal balance of the mold, to prevent casting deformation and cracks.
In the thick parts of the local cooling, to ensure that the casting solidification process of the temperature gradient is reasonable, reduce thermal stress.
(4) Mold structure and parting surface design
Adopting multiple parting surfaces to ensure smooth mold opening process and avoid casting damage. Reasonable design of mold wall thickness to ensure the strength and rigidity of the mold.
Design side core extraction system and ejector system to ensure that the castings can be smoothly removed from the mold.
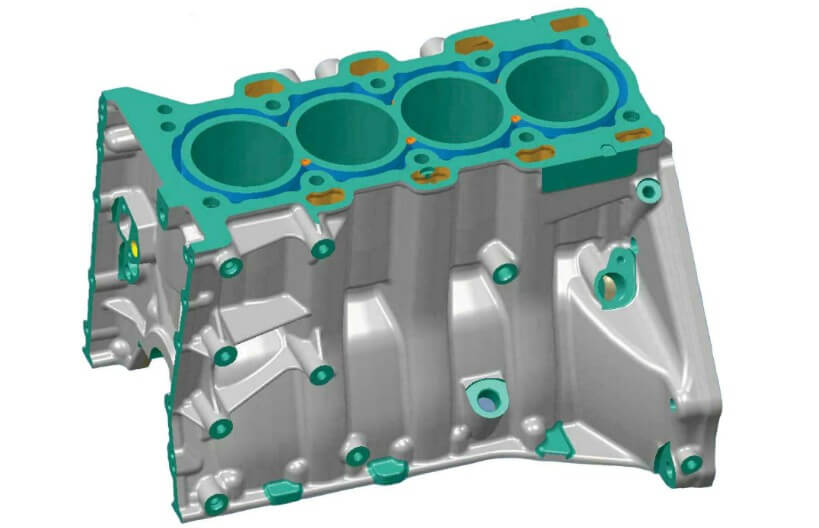
(5) Optimization of process parameters
The use of simulation software on the filling process and solidification process analysis, optimization of die-casting process parameters such as punch fast injection speed, pouring temperature, mold preheating temperature, etc., to reduce casting defects, improve the quality of castings.
(6) mold manufacturing and verification
According to the design drawings and simulation results, the use of CNC machining equipment to manufacture molds. Carry out trial molds and adjustments to ensure that the molds can meet the actual production requirements and produce qualified castings.
6.Engine blocks machining process
(1) Rough machining
1) Milling:
Milling is the main way of rough machining of the engine blocks, which is used to process the plane and hole system of the engine blocks. Commonly used milling machines are vertical milling machines and horizontal milling machines.
2) Boring:
Boring is mainly used for processing the hole system of the cylinder block, especially the cylinder hole and the main bearing hole. The boring machine can ensure the dimensional accuracy and positional accuracy of the hole system.
(2) semi-finishing machining
1) Turning:
Turning is mainly used for processing the external round surface and end face of the engine blocks. Turning can further improve the dimensional accuracy and surface quality of the cylinder block.
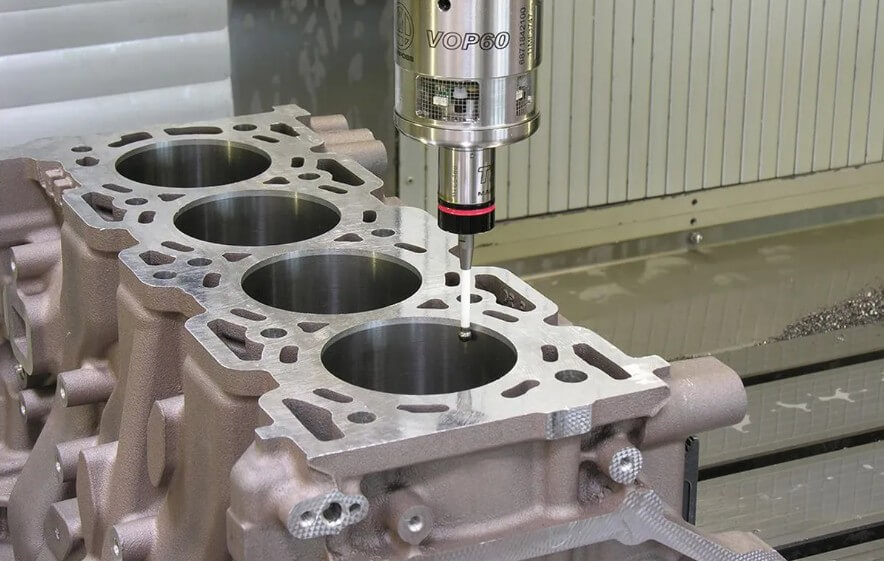
2) Drilling:
Drilling is used to process small holes and threaded holes on the cylinder block. The drilling machine can ensure the dimensional accuracy and positional accuracy of the holes.
(3) Finishing
1) Honing:
Honing is an important process of cylinder block finishing and is used to process the cylinder bore. Honing can significantly improve the dimensional accuracy, cylindricity and surface quality of the cylinder bore.
2) Grinding:
Grinding is used to process the precision holes and planes on the cylinder block. Grinding can further improve the dimensional accuracy and surface quality of the cylinder.
3) Polishing:
Polishing is used to improve the roughness of the surface of the cylinder block and improve the appearance of the cylinder block.
7.Quality Inspection of Engine Blocks
(1) Dimensional inspection
Dimensional testing is an important part of the engine blocks quality inspection, mainly using three coordinate measuring machine, micrometer, inside diameter micrometer and other testing tools for testing. The inspection items include the diameter, cylindricity and position of the cylinder bore.
(2) Surface Inspection
Surface inspection is mainly used to detect roughness, cracks, pores and other defects on the cylinder surface. Commonly used surface inspection methods include magnetic particle testing, ultrasonic testing and penetration testing.
(3) Performance testing
Performance testing mainly includes sealing testing, pressure resistance testing and fatigue strength testing. These tests can ensure the reliability and safety of the cylinder block under actual working conditions.
8.Summary
The production and processing of engine block is a complex and systematic process, involving material selection, design, production technology and processing technology and other aspects. With the continuous development of the automotive industry, the production and processing technology of the engine block is also constantly innovating and improving, and in the future, its performance and quality will be further improved to provide strong support for the development of the automotive industry.
What do you think?
[…] can imagine. As the core components of an engine, although the names of engine cylinder block and engine block are only one letter different, there are many differences in production and […]
[…] the core components of an engine, although the names of engine cylinder block and engine block are only one letter different, there are many differences in production and […]
[…] of the engine. The following are the principles and advantages of three commonly used aluminum engine block manufacturing processes, including low-pressure casting technology, metal mold gravity casting and die casting […]
[…] parts (such as engine block, oil pan, etc.), transmission system (such as transmission housing, clutch housing, etc.), […]
[…] parts (such as engine block, oil pan, etc.), transmission system (such as transmission housing, clutch housing, etc.), […]
[…] manufacturing parts with complex structure, light weight and high strength requirements, such as automobile engine block, cylinder head, wheel hub, aerospace structural parts, electronic product housing, […]
[…] iron engine blocks are widely used in many fields due to their high strength, durability and cost advantages. The […]
[…] and economy of the engine. At present, aluminum alloy and cast iron are the two most common engine blocks […]
[…] and economy of the engine. At present, aluminum alloy and cast iron are the two most common engine blocks […]