die casting uav parts: Boosting the development of low-altitude economy
UAVs “take off” to escort the low-altitude economy, and die casting uav parts, as an important part of modern aviation technology, also boost the development of the low-altitude economy. Die casting uav parts meet the needs of UAVs to develop in the direction of lightweight and high performance, bringing unprecedented development opportunities to the entire industry. This article will comprehensively introduce the relevant content about die casting uav parts, and give examples to demonstrate the importance of die casting technology in UAV manufacturing.
1.Reasons and advantages of die casting uav parts
Die casting technology is a highly efficient metal forming process that injects molten metal into a mold under high pressure and forms the desired part shape after cooling and solidification. This technology is widely used in the manufacture of UAV components, mainly because it can produce components with high precision, high consistency and complex geometric shapes. The use of die casting technology can greatly improve production efficiency and reduce costs, while meeting the lightweight and high-strength design requirements of UAVs.
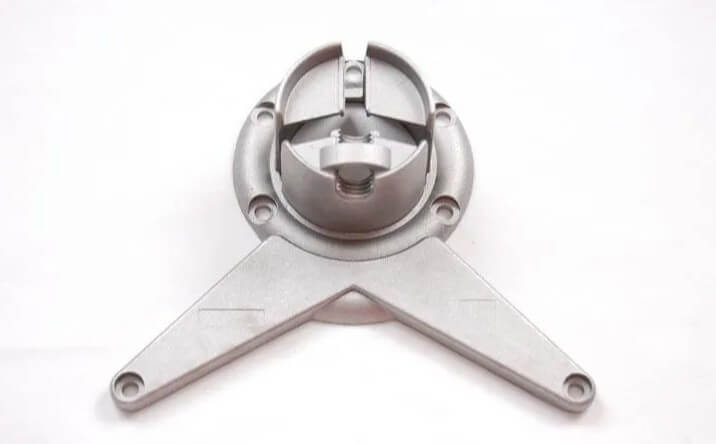
The reasons and advantages of using die casting technology in the manufacturing of UAV parts are mainly reflected in the following aspects:
(1) Lightweight demand:
Drones are sensitive to weight. Die casting technology can produce lightweight and high-strength parts, such as aluminum alloy die castings, which help improve the flight efficiency and endurance of drones.
(2) High precision and complex shapes:
Die casting technology can produce high-precision, complex-shaped parts to meet the requirements of precise size and structure in drone design.
(3) Production efficiency:
Die casting technology has an efficient production speed, is suitable for mass production, and can quickly meet market demand.
(4) High resource utilization:
The die casting process has a high material utilization rate and less waste, which helps to reduce costs and reduce environmental impact.
(5) Superior surface quality:
Die casting uav parts usually have excellent surface quality and require almost no additional surface treatment, which reduces manufacturing costs and ensures the appearance and performance of the final product.
(6) Material diversity:
The die casting process is suitable for a variety of materials, including metals such as aluminum, zinc, and magnesium, providing more options for the manufacturing of drone parts.
(7) Strength and stability:
Die casting uav parts have high static and dynamic strength, making the UAV structure more stable and able to operate stably in various environments.
(8) Cost-effectiveness:
Die casting technology can reduce production processing frequency, reduce production costs and production time, and improve work efficiency.
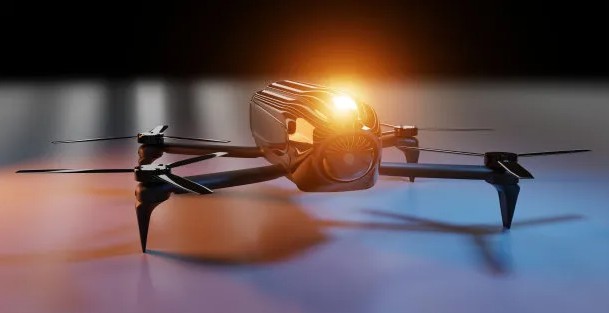
2.Material selection for die casting uav parts
When selecting materials for die casting uav parts, multiple factors need to be considered, including material strength, weight, corrosion resistance, machinability, and cost. The following are some commonly used materials for UAV components and their characteristics:
(1) Aluminum alloy:
Aluminum alloy is one of the most commonly used die casting materials because it is lightweight, high-strength, corrosion-resistant, and has good thermal conductivity. These characteristics make aluminum alloy very suitable for manufacturing UAV components such as frames, motor housings, etc. Common aluminum alloy grades include A380, ADC12, etc.
(2) Magnesium alloy:
Magnesium alloy has a lighter weight and good mechanical properties than aluminum alloy, making it another choice for die casting uav parts. However, magnesium alloy is more expensive and prone to corrosion at high temperatures. Common magnesium alloy grades include AZ91D, AM60B, etc.
(3) Zinc alloy:
Zinc alloy has good fluidity and mechanical properties and is suitable for manufacturing small and complex drone parts. However, the strength and heat resistance of zinc alloy are not as good as aluminum alloy and magnesium alloy. Common zinc alloy grades include Zamak 3, Zamak 5, etc.
(4) Copper alloy:
Copper alloy has good thermal conductivity and wear resistance and is suitable for manufacturing certain specific parts in drones, such as motor rotors and bearings. However, copper alloy is heavy and expensive. Common copper alloy grades include brass, bronze, etc.
(5) Titanium alloy:
Titanium alloy has extremely high strength and corrosion resistance, but it is expensive and difficult to process. Therefore, titanium alloy is usually only used to manufacture drone parts that require extremely high strength and corrosion resistance.
(6) High-strength plastic:
High-strength plastic may be used in some parts, such as drone propellers and certain internal structures. These plastics are lightweight, durable and corrosion-resistant, which helps reduce the overall weight of drones and improve performance.
(7) Carbon fiber:
Carbon fiber is a very strong and lightweight material that is widely used in some high-end drones. The strength and rigidity of carbon fiber are very high, allowing drones to withstand more complex flight missions. In addition, carbon fiber also has good corrosion resistance and can adapt to various harsh environments.
(8) Composite materials:
Composites are made of a combination of multiple materials, such as carbon fiber, glass fiber and resin. These materials have good strength and rigidity while being lightweight. Therefore, they not only ensure the structural strength of the drone, but also help improve the flight performance of the drone.
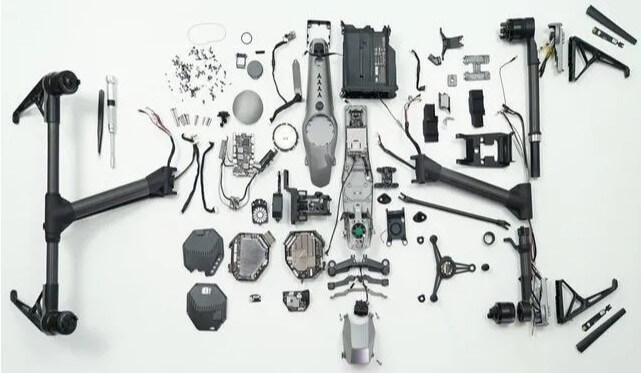
3.Key production processes of Die casting uav parts
Die casting technology is widely used in modern manufacturing, especially in the production of high-precision and complex structure drone parts. Die casting technology can produce parts with excellent mechanical properties and surface quality. The following are the key production processes of die casting uav parts:
(1) Mold design and manufacturing
The mold is the basis of die casting production, and its design directly affects the quality and production efficiency of the final product. The mold design of drone parts needs to consider the structural complexity, dimensional accuracy and material properties of the parts. The mold is usually made of high-strength steel and is precision machined to ensure the dimensional accuracy and surface finish of the mold.
(2) Raw material preparation
Selecting the right die casting material is the key to ensuring the performance of die casting uav parts. Commonly used die casting materials include aluminum alloy, zinc alloy and magnesium alloy. Aluminum alloy is widely used in the production of drone parts due to its light weight, high strength and good corrosion resistance. The raw materials need to be preheated before die casting to remove impurities and gases and improve their fluidity.
(3) Melting and pouring
Put the prepared raw materials into a furnace and heat them to a molten state. The melting temperature needs to be strictly controlled to ensure the fluidity and filling performance of the molten metal. During the melting process, the molten metal also needs to be degassed to reduce pores and defects in the casting. The molten metal is injected into the mold through the pouring system. The pouring speed, pressure and temperature are the key parameters for controlling the quality of the casting.
(4) Die casting
Die casting is the core link of the entire production process. Under high pressure, the molten metal quickly fills the mold cavity and cools and solidifies in a short time. The selection and parameter setting of the die casting machine have an important impact on the quality and production efficiency of the casting. Common die casting machines include cold chamber die casting machines and hot chamber die casting machines. Choose the appropriate type of die casting machine according to different production needs.
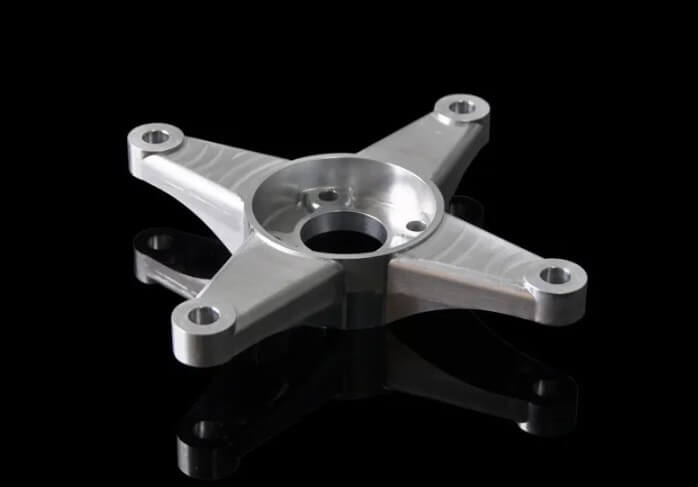
(5) Post-processing
The die-cast parts need to go through a series of post-processing processes, including deburring, grinding, polishing, heat treatment, etc. Deburring and grinding are to remove the flash and burrs on the surface of the parts and improve the surface finish; polishing is to further improve the surface finish and aesthetics of the parts; heat treatment is to improve the mechanical properties of the parts, such as hardness, strength and toughness.
(6) Quality inspection
Quality inspection is an important link to ensure the quality of die casting UAV parts. Common inspection methods include size inspection, surface quality inspection, mechanical property inspection, etc. Use advanced inspection equipment and technology, such as three-coordinate measuring machine, surface roughness tester, hardness tester, etc., to conduct comprehensive quality inspection of parts to ensure that they meet design requirements and industry standards.
(7) Surface treatment
Depending on the use environment and functional requirements of drone parts, surface treatment such as painting, anodizing, electroplating, etc. may be required. Surface treatment can not only improve the aesthetics of parts, but also enhance their corrosion resistance and wear resistance.
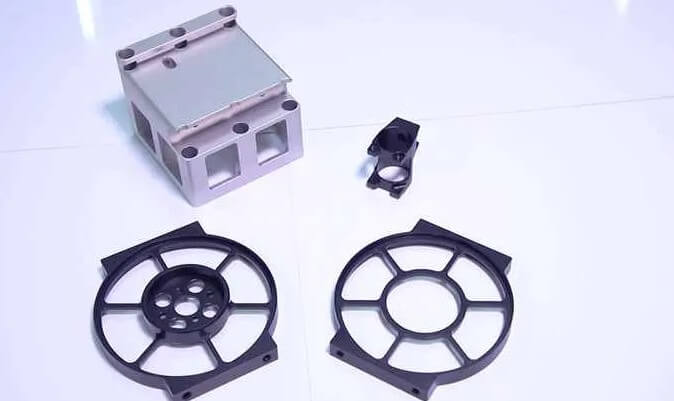
Summary:
Through the above key production processes, die-cast drone parts not only have the characteristics of high precision and high efficiency, but also meet the requirements of lightweight and high performance of drones.
4.Main challenges and solutions for Die casting uav parts
The main challenge of die casting uav parts is to ensure the precision, strength and lightweight requirements of parts, while ensuring production efficiency and economy. The following are some specific difficulties and their solutions:
(1) High precision requirements:
Drone parts often require high-precision dimensions and shapes to ensure flight performance and stability. The solution is to use advanced die casting technology and precise mold design, optimize mold design and process parameters through numerical simulation technology, reduce the number of mold trials and shorten the production cycle.
(2) Material selection:
Drone parts need to have high toughness, lightness, good heat transfer and corrosion resistance. Materials such as aluminum alloys and zinc alloys are often used in the production of die casting uav parts due to their comprehensive performance advantages.
(3) Structural complexity:
The structure of drone parts is often complex, and die casting technology is required to realize prefabricated components with complex geometric shapes. The solution is to use mold technology such as cores and sliders. Although this will increase costs and cycle time, it is essential for producing high-quality, high-complexity castings.
(4) Production efficiency and cost control:
The production of die casting uav parts requires a balance between efficiency and cost. Precision die casting technology can achieve efficient production, but at the same time it is necessary to control mold costs and scrap rates during the production process.
(5) Performance consistency:
The performance consistency of die casting uav parts is essential to ensure flight safety. The solution is to adopt a stable production process and strict quality control to ensure that each component meets the design requirements.
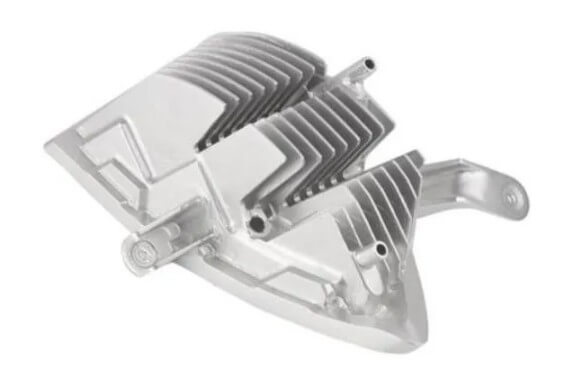
5.Does DJI drone use die-cast products?
Yes, DJI drones do use die casting technology in their manufacturing process. According to the results, die casting technology plays an important role in the production of DJI drones. DJI’s main die casting uav parts include but are not limited to the following:
(1) Drone housing:
Aluminum die casting technology is widely used in the manufacture of drone housings because aluminum is light and strong, which can meet the drone’s requirements for lightness and high toughness.
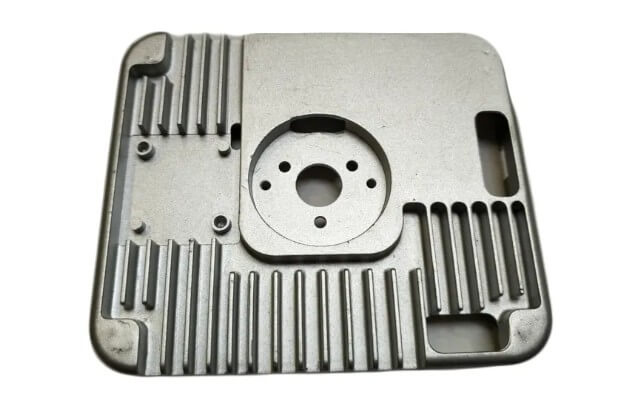
(2) Flight controller:
Aluminum die casting technology is also used to manufacture flight controllers, which are key components in drones and are responsible for controlling the drone’s flight attitude and navigation.
(3) Rechargeable battery heat pipe radiator:
In order to improve heat dissipation efficiency, the rechargeable battery heat pipe radiator is also manufactured using aluminum die casting technology to ensure that the drone battery maintains a suitable temperature during operation.
(4) Motor base:
The motor base is an important component that supports and fixes the motor, and is usually also manufactured using aluminum die casting technology to provide sufficient strength and stability.
(5) Servo motor gear:
Servo motor gear is a key component in the drone transmission system. Aluminum die casting technology can ensure the accuracy and durability of the gear.
(6) UAV bracket:
The magnesium alloy die casting and baking varnishing process is used to manufacture UAV brackets. This process can provide high precision and good appearance, meet the lightweight requirements, and at the same time, the process complies with the new EU ROHS standard, with high precision and good environmental performance.
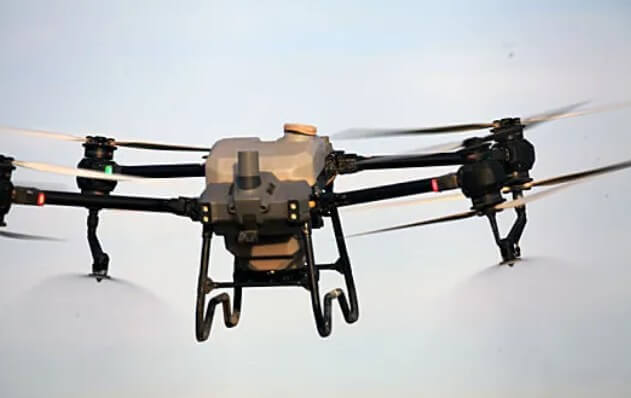
6.Summary
Die casting uav parts, with their unique advantages, occupy an increasingly important position in UAV production. Through the precise die casting process, UAV parts with high precision, high strength and good surface quality can be produced. Die casting uav parts not only greatly improve the flight stability and safety of UAVs, but also effectively reduce production costs and manufacturing cycles, thereby contributing to the development of the low-flying economy.