Die Casting: The Core Technology of Precision Manufacturing
1.Overview of Die Casting
Die casting Process is an advanced precision metal casting process that forces molten metal into a mold cavity under high pressure. Its notable features are high speed and high quality of the finished product. The die casting process has become an indispensable key manufacturing process in the automotive, aerospace, electronics and other industries with its efficient production capacity and excellent ability to form a large number of complex shapes and small parts.
Compared with other metal forming methods, die casting stands out for its unique ability to achieve tight tolerances and smooth surfaces without secondary processing. Among them, high-pressure die casting and cast aluminum are particularly outstanding in producing strong and lightweight parts, which can significantly save costs and materials compared with technologies such as forging and sand casting. By using die castings of aluminum alloys and other alloys, manufacturers can meet specific performance and strength standards, making die castings a solid cornerstone of modern manufacturing.
2.Detailed Explanation of Die Casting Process
(1) Die Casting Process
Die casting is a dynamic casting process. First, the metal is prepared by melting the metal (usually aluminum or zinc alloy) in a furnace until it becomes liquid. After the metal is melted, it is quickly injected into a precision mold using a hydraulic or mechanical piston. During the die casting process, pressure is maintained until the metal hardens, accurately clamping complex parts and ensuring the structural integrity of the casting. The mold is then opened to squeeze the casting and quickly closed to prepare for the next cycle. This fast-flowing operation improves the production efficiency of complex metal parts with good surface finish and dimensional accuracy.
(2) The importance of form
Shape plays a key role in the die casting process. The mold is made of high-quality steel and can withstand extreme operating conditions. They are usually composed of two halves to achieve complex geometries. Die casting molds are often equipped with complex features such as cores and guides to create internal cavities and concave edges without the need for additional processing.
Mold design has a significant impact not only on the quality of the finished product, but also on the efficiency of the entire casting process. Efficient mold design can reduce waste, improve the mechanical properties of the casting, and significantly reduce production costs and time.
3.Types of die casting
(1) Hot chamber die casting
Hot chamber die casting is suitable for metals with lower melting points such as zinc and magnesium and some low-temperature aluminum alloys. In this process, a furnace is part of the casting machine and a piston forces the molten metal into the mold. The main advantage is fast cycle times, which is ideal for mass production of small parts.
(2) Cold Chamber Die Casting
In cold chamber die casting, the molten metal is poured into the machine’s injection system one part at a time. This method is more suitable for metals with higher melting points such as aluminum and copper. Although cold chamber die casting is relatively time-consuming, it reduces the interaction between the molten metal and the machine parts, which can improve the structural integrity of the casting.
(3) Low Pressure Casting
Low pressure casting is generally used for parts that require high metallurgical quality and surface finish. It is performed by slowly injecting molten metal from below into the mold under controlled pressure. It is often used for parts such as automotive wheels where the amount of pores needs to be kept to a minimum.количество воздушных отверстий.
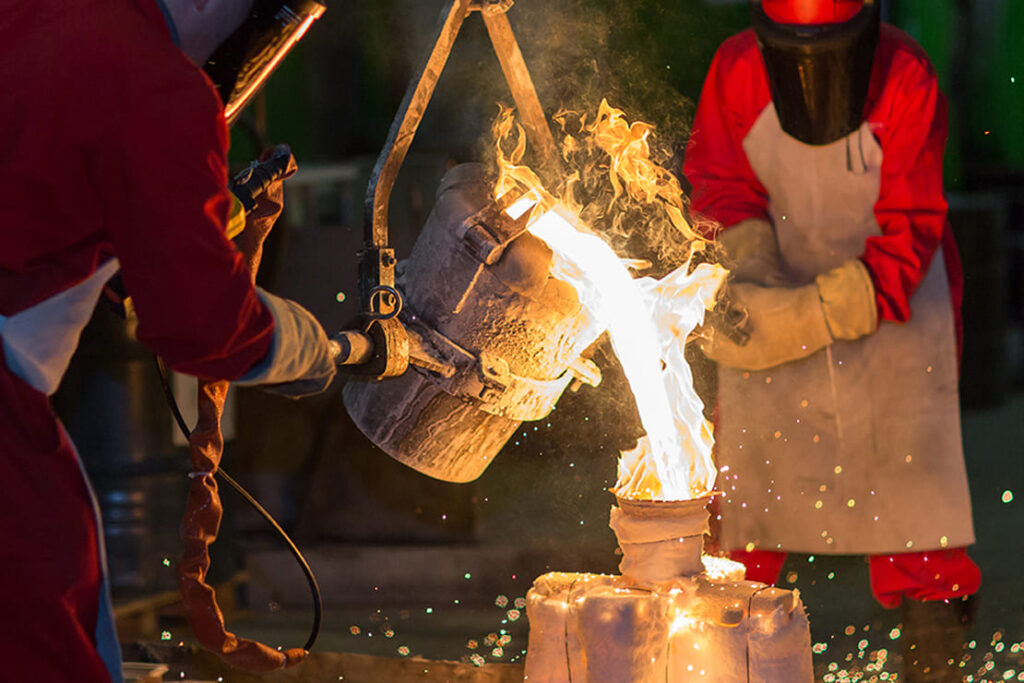
(4) High Pressure Casting
High pressure casting involves injecting molten metal into a mold under high pressure of up to 25,000 pounds per square inch. It is the most widely used injection molding method and is known for its ability to produce precise, complex shapes, tight tolerances and high-quality surface finishes. It is generally used to produce small to medium-sized parts.
(5) Vacuum casting
Vacuum casting is an advanced process based on the principle of high-pressure casting by excluding air from the mold cavity. This process can reduce porosity and produce parts with higher integrity, mechanical properties and cleaner surfaces, making it ideal for more demanding applications.
(6) Die casting
The die casting process combines the characteristics of forging and casting, applying pressure throughout the metal solidification process. This method is very suitable for parts that require high density and no pores.
(7) Semi-solid die casting
Semi-solid die casting is a casting process in which the alloy is partially melted into a slurry. This condition can better control the flow of metal into the mold, reduce porosity and enable production., снижает пористость и может производить более прочные и жаропрочные детали.
4.Materials suitable for die casting process
Die casting uses a variety of metal materials, each of which is suitable for different production requirements due to its specific properties.
Aluminum and its alloys are one of the most commonly used materials in die casting. Its lightweight characteristics combined with excellent mechanical properties and corrosion resistance make it an ideal choice for automotive, aerospace and consumer electronics applications. Zinc, known for its low melting point and ease of casting, is also widely used in die casting. As the lightest structural metal, magnesium is also one of the commonly used die castings, with strength comparable to that of aluminum.
The field of die casting continues to evolve as new materials and technologies are constantly being developed. Recent innovations include the use of materials such as titanium and silicon alloys in die casting, which have unique properties such as higher strength, lighter weight or better corrosion resistance. Researchers are also actively exploring semi-solid metal alloys, which have higher strength and lower porosity than traditional liquid casting methods.
In the die casting process, each material has its own unique advantages and challenges that affect everything from production speed to final part performance. Therefore, the choice of materials is critical and must meet the specific requirements of the intended application to ensure optimal performance and cost-effectiveness.
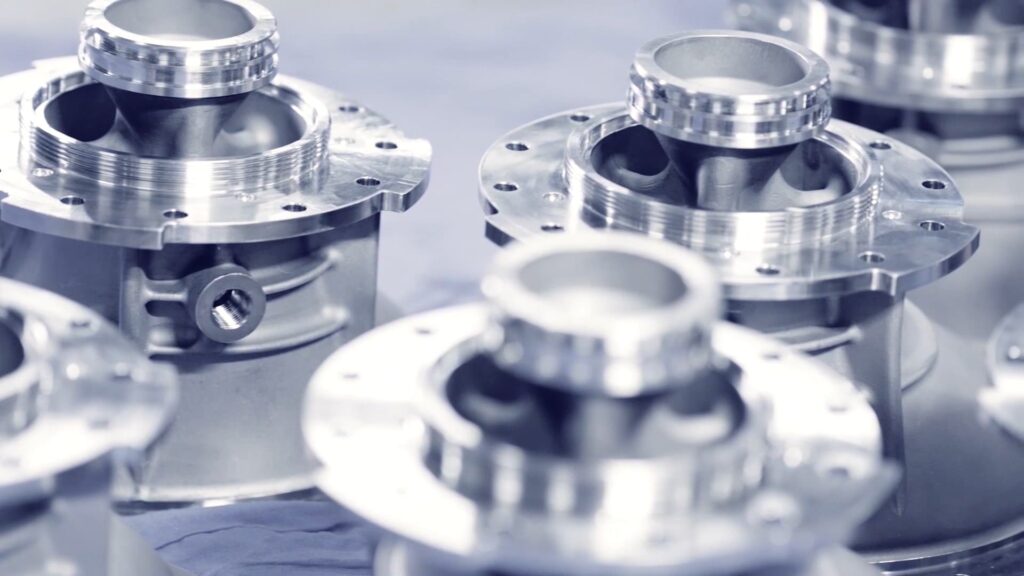
5.Application of die casting process
Die casting plays a key role in industries such as automotive, aerospace, and consumer electronics due to its ability to produce precise and durable parts. In the automotive industry, die casting is needed to produce lightweight, strong components such as engine blocks and transmission housings, thereby improving vehicle performance and fuel efficiency. The aerospace industry uses aluminum die casting to produce critical components that require a high strength-to-weight ratio, such as aircraft structural components.
Emerging markets are also embracing die casting for its precision and versatility, with applications ranging from solar panel frames for renewable energy to complex surgical instruments in medical technology. Advances in die casting materials and technologies, such as semi-solid injection molding and aluminum alloy casting, are expanding its applications to high-performance applications that require specific properties.
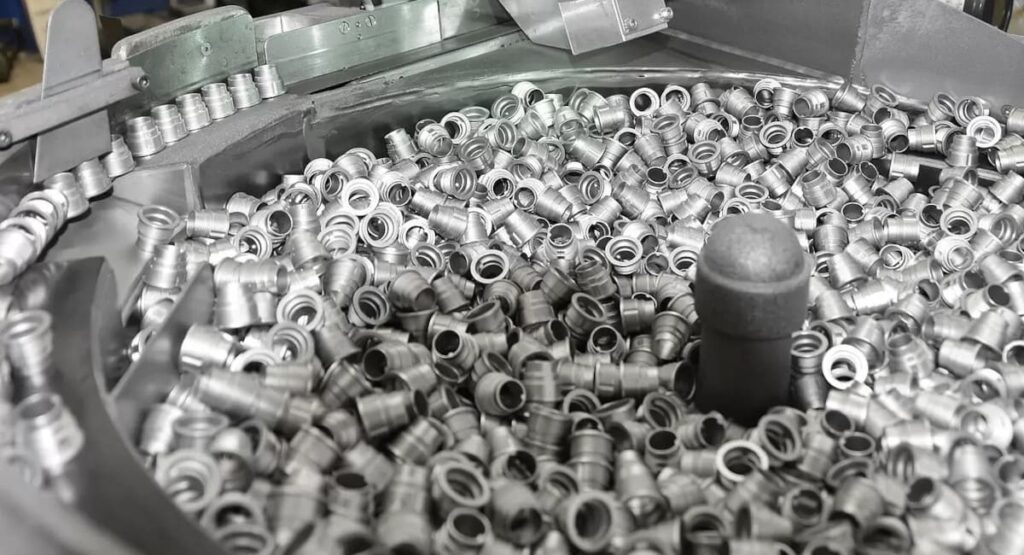
6.Advantages of the Die Casting Process
Die casting stands out in the manufacturing industry for its cost-effectiveness and productivity, and is particularly suitable for large-scale production. The process can produce complex parts without additional machining, thereby significantly reducing unit costs. Aluminum die castings exhibit excellent mechanical properties due to the rapid cooling in the mold, which achieves a finer microstructure. This makes the parts stronger, lighter, and more resistant to deformation and thermal fatigue.
In addition, the versatility of die casting allows for a high degree of customization. Metal die casting can produce complex designs, including complex parts and integrated functions. This capability enables manufacturers to tailor parts to specific needs, providing functional and aesthetic solutions that effectively meet the needs of a variety of industrial applications.
7.Conclusion
Die casting has always occupied an important position in the manufacturing industry, meeting industrial needs with its precision and efficiency through advanced metal casting processes. Future trends highlight the shift towards sustainability and smart technology in injection molding machines, which promises to achieve greater precision and reduce environmental impact. As these innovations continue to advance, the die casting process will continue to play a key role in various fields such as automotive and aerospace, highlighting its core position in modern manufacturing.