Die casting process parameters: the importance, methods and impact of design
The design of die casting process parameters is an important link to ensure that the performance of castings meets the requirements. Reasonable process parameters can not only improve the mechanical properties of castings, but also effectively prevent the occurrence of various defects.
This paper aims to explore the importance of die casting process parameter design. First, the influence of process parameters on the quality and production cost of die castings is analyzed to provide a certain theoretical basis for the following text. Then, key die casting process parameters and parameter optimization methods are introduced. Finally, different solutions are provided to deal with the specific process parameter requirements of die casting production in different industries, and the full text is summarized at the end of the article.
1.Overview of die casting process parameters
(1) Definition and scope
Die casting process parameters mainly include pouring temperature, mold temperature, filling speed and pressure, holding time and cooling time. These parameters play a decisive role in the die-casting process and directly affect the quality and production efficiency of die-castings.
(2) Importance
Reasonable die casting process parameter settings can not only improve the dimensional accuracy and surface quality of die-castings, but also effectively avoid defects such as pores and cracks. At the same time, optimizing process parameters can reduce production costs and improve production efficiency, thereby gaining an advantage in a highly competitive market.
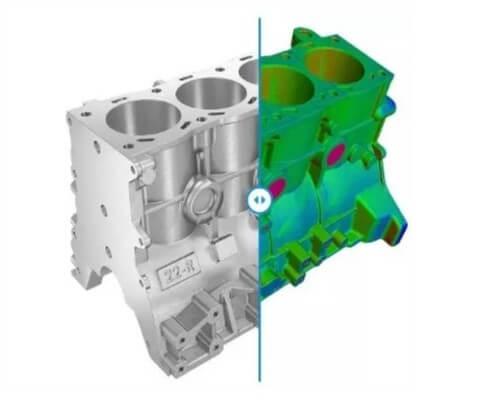
2.The impact of die casting process parameters on the quality of die castings
(1) Specific case analysis
For example, if the pouring temperature is too low, the fluidity of the molten metal will deteriorate, resulting in insufficient filling, which may cause cold shut or surface defects. On the contrary, if the pouring temperature is too high, it may cause oxidation of the molten metal, increase the porosity, and in severe cases may cause thermal cracking of the mold.
(2) Causes of quality defects
Irrational filling speed and pressure settings will also affect the quality of die-castings. Filling speed that is too fast may cause air entrainment and form pores; filling speed that is too slow may cause unclear casting contours and insufficient surface finish. Pressure regulation is also very critical. Insufficient pressure may cause insufficient density and reduced strength of the casting; excessive pressure may damage the mold and shorten the mold life.
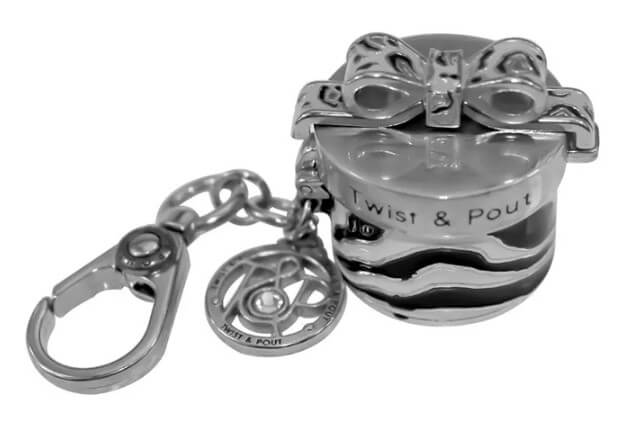
3.The impact of die casting process parameters on production costs
(1) Cost composition analysis
In die casting production, costs mainly include material costs, equipment depreciation, labor costs, energy consumption, etc. Optimization of die casting process parameters can significantly reduce these costs. For example, reasonable pouring temperature and mold temperature can extend the service life of the mold and reduce equipment depreciation costs.
(2) Economic benefit analysis
Optimizing filling speed and pressure can shorten the production cycle and improve production efficiency, thereby reducing labor costs and energy consumption. In addition, by reducing scrap rate and rework rate, it can further save material and production costs and improve the economic benefits of the enterprise.
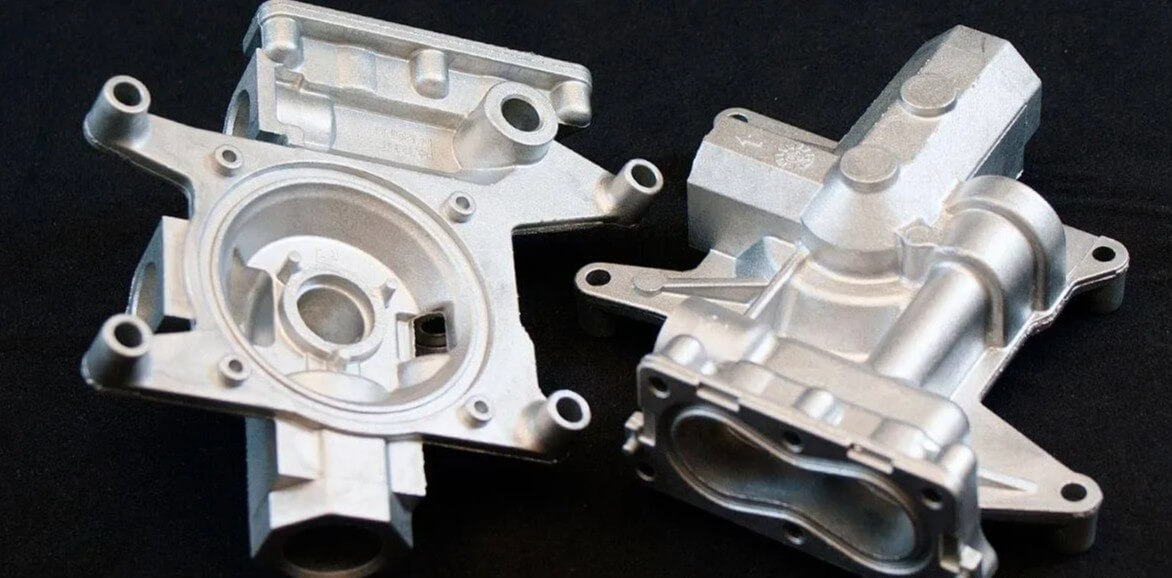
4.Detailed explanation of key die casting process parameters
(1) Pouring temperature
1) The influence of molten metal temperature on fluidity and filling effect
Pouring temperature is one of the most critical parameters in die casting process parameters. Appropriate molten metal temperature can ensure its good fluidity and help to fully fill every detail of complex molds. Too high temperature may cause oxidation of molten metal, increase the risk of pore formation, and may cause thermal damage to the mold; too low temperature may cause insufficient filling, surface cold shut and other defects.
2) Problems with improper temperature setting
In actual production, it is necessary to accurately control the pouring temperature according to the specific alloy characteristics and casting structure. For example, the pouring temperature of aluminum alloy is usually controlled between 620°C and 680°C to ensure good fluidity and filling effect.
(2) Mold temperature
1) The influence of mold preheating and reasonable setting of working temperature on production efficiency
The control of mold temperature is equally important, which affects the solidification speed of molten metal and the quality of castings. Mold preheating can prevent defects such as cold shut and cracks caused by rapid cooling of molten metal in the early stage of filling. Reasonable mold working temperature can improve production efficiency and casting quality.
2) The relationship between mold temperature and molten metal temperature and its influence on casting quality
Excessive mold temperature may make it difficult to demold the casting and increase the risk of mold sticking; excessively low mold temperature may cause the molten metal to solidify too quickly, resulting in insufficient filling. Therefore, the mold temperature usually needs to be controlled within a certain range. For example, for aluminum alloy die casting, the mold temperature is generally set at 180°C to 220°C.
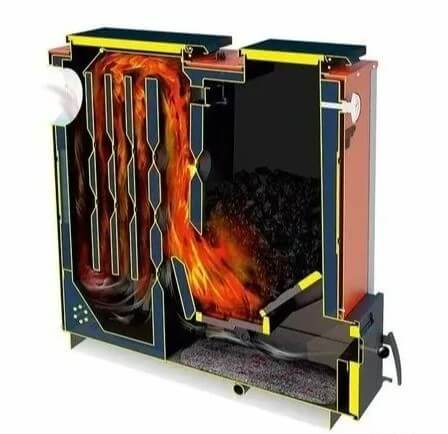
(3) Filling speed and pressure
1) The effect of filling speed on the surface quality and internal structure of castings
The filling speed determines the speed at which the molten metal enters the mold cavity, affecting the surface quality and internal structure of the casting. Low-speed filling is suitable for simple or thick-walled castings, which can reduce the formation of pores and inclusions; high-speed filling is suitable for thin-walled or complex-structured castings to ensure complete filling and good surface finish.
2) Pressure regulation to improve the density and mechanical properties of castings
Filling pressure is the key to ensuring that the molten metal fills the mold at high speed. Appropriate filling pressure can improve the density of the casting and improve its mechanical properties. Too high pressure may cause mold damage and molten metal splashing, while too low pressure may cause insufficient filling and insufficient casting density.
(4) Holding time and cooling time
1) The effect of holding time on the density and internal quality of castings
The holding time refers to the time that pressure is continued to be applied to the casting after filling is completed to help the molten metal solidify and form better in the mold. Appropriate holding time can ensure the density and internal quality of the casting and avoid defects such as shrinkage cavities and shrinkage.
2) The impact of cooling time on production efficiency and mold life
Cooling time refers to the time from filling completion to mold opening and taking out the casting. Reasonable cooling time can ensure that the casting is fully solidified and avoid deformation or cracks caused by insufficient cooling. Too long cooling time will reduce production efficiency, while too short cooling time may affect the quality of the casting and the life of the mold.
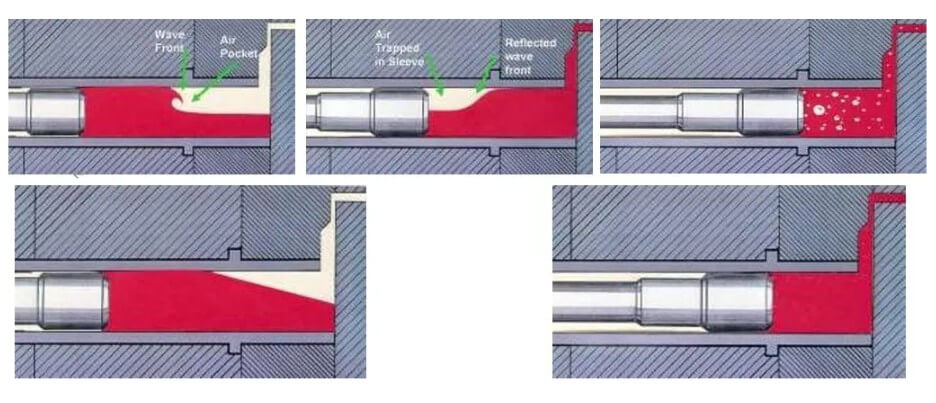
5.Die-casting process parameter optimization method
(1) Combination of experimental method and simulation method
In actual production, the optimization of die casting process parameters usually adopts a combination of experimental method and simulation method. The experimental method adjusts parameters and analyzes results through actual production tests; the simulation method predicts the casting quality and production efficiency under different parameter settings through computer simulation. Combining the two methods can more effectively optimize the process parameters.
(2) Utilization of historical data
The use of historical data is also an important method for optimizing die casting process parameters. By analyzing past die-casting data, the rules and problems of parameter settings can be discovered, providing a reference for the optimization of process parameters for new projects.
(3) Coordination between die-casting machine, die-casting mold and process parameters
Coordination between die-casting machine, die-casting mold and process parameters is another key to achieve efficient production. It is necessary to ensure that the performance of the die-casting machine matches the mold design, and the process parameter settings must also be adapted to both to achieve optimal production efficiency and casting quality.
(4) The influence of mold design on the selection of die casting process parameters
Mold design has a direct impact on the selection of die casting process parameters. For example, the design of the mold cooling system affects the control of cooling time and mold temperature; the design of the gate and runner affects the filling speed and pressure of the molten metal. Therefore, when optimizing the process parameters, the characteristics of the mold design must be considered.
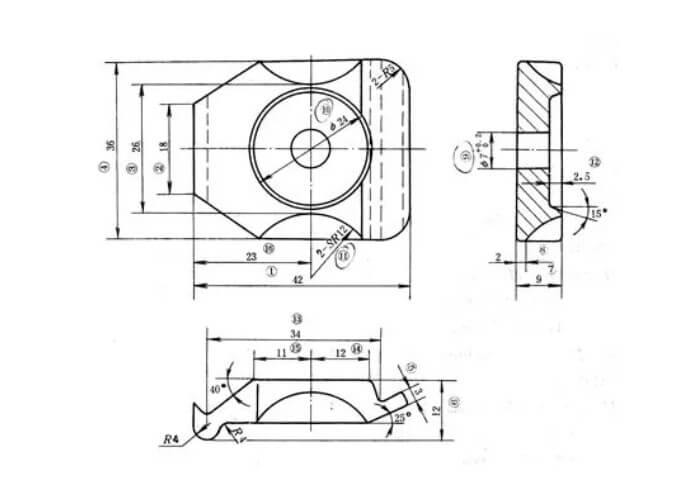
Mould design drawing
6.Specific process parameter requirements for die-casting production in different industries and their implementation effects
As a metal forming technology widely used in modern manufacturing, the reasonable selection and control of its process parameters are of great significance to ensure the quality and production efficiency of die-castings. Due to differences in product uses and performance requirements, different industries have specific requirements for process parameters for die-casting production. The following is a specific analysis of several typical industries.
(1) Automotive industry
The automotive industry has a large demand for die-casting parts, and requires die-casting parts to have high strength, light weight and good dimensional stability. Key die casting process parameters include high-pressure injection speed (to ensure that the molten metal quickly fills the cavity and reduces pores and shrinkage), mold temperature (usually controlled at 200℃±30℃ to reduce thermal cracks and improve surface quality) and cooling time (to ensure the dimensional stability of the casting and avoid deformation). By precisely controlling these parameters, automotive die-casting parts can meet the needs of high-strength structural parts such as engine blocks and gearbox housings.
(2) Aerospace industry
The aerospace industry has extremely strict performance requirements for die-casting parts, which require high strength and excellent corrosion resistance. The selection of die casting process parameters focuses on alloy properties (such as the selection of high-temperature alloys and aluminum alloys), injection pressure (usually high to ensure complete filling of complex structures) and temperature control (precisely control the temperature of the molten metal and mold to reduce internal defects). The result is a die-casting with extremely high reliability and long life, which is suitable for manufacturing aircraft structural parts and engine components.
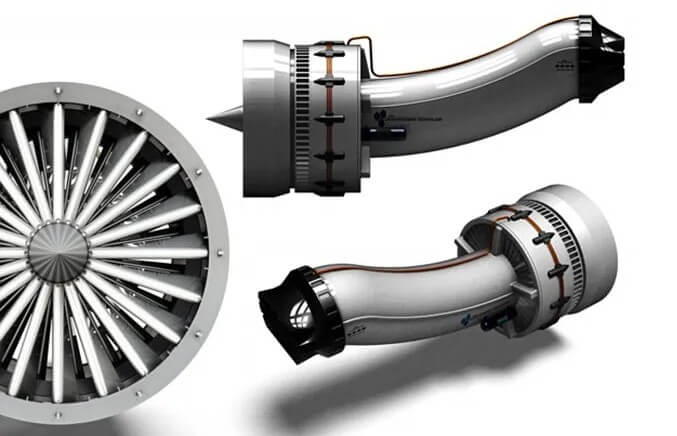
(3) Electronics Industry
Die castings in the electronics industry usually require high precision, thin walls and good surface finish. Important die casting process parameters include low-speed injection (to reduce surface defects), mold temperature (controlled in a low range to improve dimensional accuracy) and pouring temperature (moderate to avoid surface oxidation and sticking). The control of these parameters enables die castings to meet the needs of precision electronic products, such as mobile phone housings, tablet computer frames, etc.
(4) Home Appliance Industry
The home appliance industry focuses on mass production efficiency and cost control of die castings. Key die casting process parameters include high-speed injection (to improve production cycle), mold life (to reduce mold wear by optimizing mold temperature and paint use) and degree of automation (to achieve fast mold change and continuous production). By setting these parameters reasonably, home appliance die castings can achieve efficient and low-cost production while ensuring quality.
7.Summary
In summary, the design of die casting process parameters has an important impact on factors such as the quality and production efficiency of die castings. Only by reasonably designing and strictly controlling these parameters can high-quality die casting products be obtained to meet the development needs of modern manufacturing industry.