Die casting: In-depth analysis of the working principle
Die casting is an efficient metal forming process that is widely used to manufacture parts with complex shapes. This article will explore the working principle of die casting in depth, including its basic definition, process parameter details, mechanism principle analysis, die casting pressure and speed regulation, and the characteristics of commonly used die casting alloys.
1.Definition of die casting
Die casting is a casting process in which molten metal is injected into the head of a high-pressure casting machine, and then the molten metal is injected into the mold under high pressure to form metal castings under specific temperature and pressure conditions. The main characteristics of die casting are: its forming equipment has a high degree of automation and production efficiency, and the finished product has the characteristics of high precision, high strength, high fatigue resistance, and high surface finish.
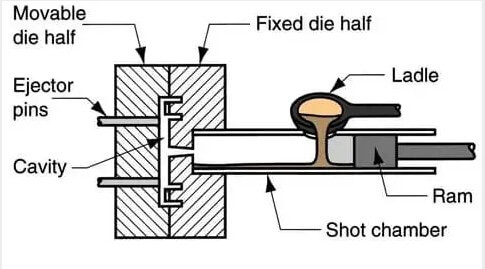
2.Explanation of die casting process parameters
(1) Filling time: refers to the time required for molten metal to enter the mold cavity.
(2) Filling speed: refers to the speed at which the molten metal fills the mold cavity.
(3) Filling pressure: the starting pressure and the maximum pressure when the filling is completed.
(4) Mold temperature: the mold temperature determines the surface quality and microstructure of the casting.
(5) Cooling time: the time required for the casting to cool in the mold cavity.
3.The mechanism of die casting
To understand the working principle of die casting, the most important thing is to understand how the metal jet and high-pressure filling solidification occur?
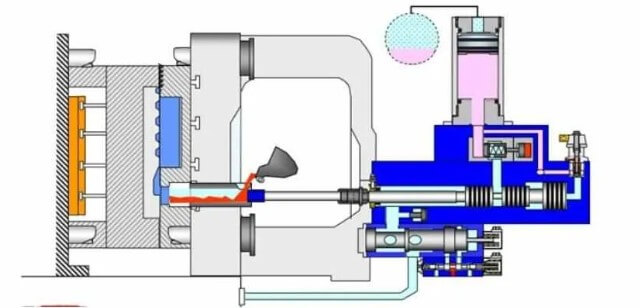
(1) Metal jet
The molten metal enters the mold cavity under high pressure. At this time, the molten metal forms a metal jet at the front end. As the metal jet flows further into the mold cavity, the pressure gradually decreases and the speed gradually slows down. Therefore, in the internal channel of the mold cavity, when the speed and pressure reach the maximum value, the metal jet will be deformed due to the reaction force of the mold cavity.
When the shape of the molten metal flowing through the mold cavity changes, that is, it suddenly increases or decreases, the molten metal will be sheared to form a flow zone. These flow zones have an important influence on the microstructure and surface defects of the casting.
(2) Solidification process
When the temperature of the molten metal entering the mold cavity is higher than the melting point, the molten metal begins to flow. As the molten metal cools and solidifies, the number of crystals gradually increases. During the process of grain growth, metal atoms may fall on the surface of the formed grains or on the interface between the liquids.
When the number of grains reaches a sufficient number, the corresponding nuclei will form on the interface. For alloys with general solidification rules, the number of crystals will gradually increase as the molten metal drops below the solidus line, so the higher the degree of refinement of the casting, the better the quality of the casting.
4.Regulation of die casting pressure and speed
The pressure and speed in the die casting process are the key factors that determine the quality of the casting.
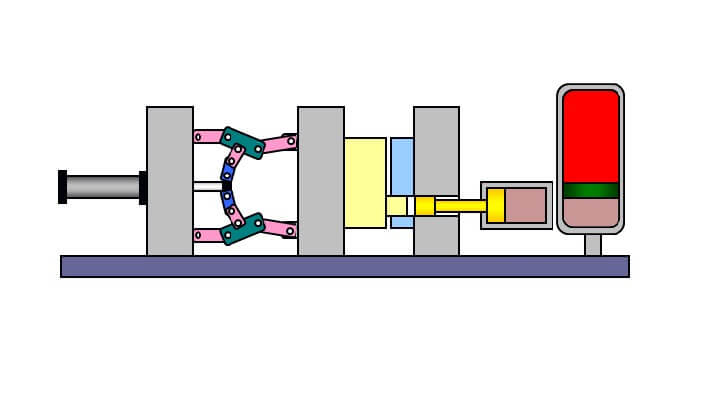
(1) Die casting pressure
1) Injection force:
The injection force is the force used by the injection mechanism of the die casting machine to push the injection piston to move, which is determined by the cross-sectional area of the injection cylinder and the pressure of the working fluid. The size of the injection force directly affects the filling capacity of the molten metal.
2) Injection pressure ratio:
The injection pressure ratio is the pressure per unit area of the molten metal in the injection chamber, that is, the ratio of the injection force to the cross-sectional area of the injection chamber. The larger the injection pressure ratio, the finer the alloy crystals, the better the surface quality of the die casting, and the less pore defects.
(2) Die casting speed
1) Injection speed:
The speed at which the die-casting punch pushes the molten metal in the die casting chamber. The injection speed is divided into a slow sealing stage and a high-speed filling stage. The slow sealing stage prevents air from being drawn in, and the high-speed filling stage fills the mold cavity in a shorter time.
2) Filling speed:
The linear speed at which the molten metal enters the cavity through the inner gate under the action of the die-casting punch. The filling speed is affected by the injection speed, injection pressure ratio and inner gate area.
5.Commonly used die casting alloys and their characteristics
Common alloys in die casting process include aluminum alloys, zinc alloys, magnesium alloys, etc. These alloys have the following characteristics:
(1) Aluminum alloy
1) Characteristics:
Good performance, good electrical and thermal conductivity, low density, high specific strength and specific stiffness. Good high and low temperature mechanical properties, small crystallization temperature range, good filling performance, small linear shrinkage, and low tendency to thermal cracking.
2) Application:
Widely used in automobiles, aerospace, electronic equipment and other fields.
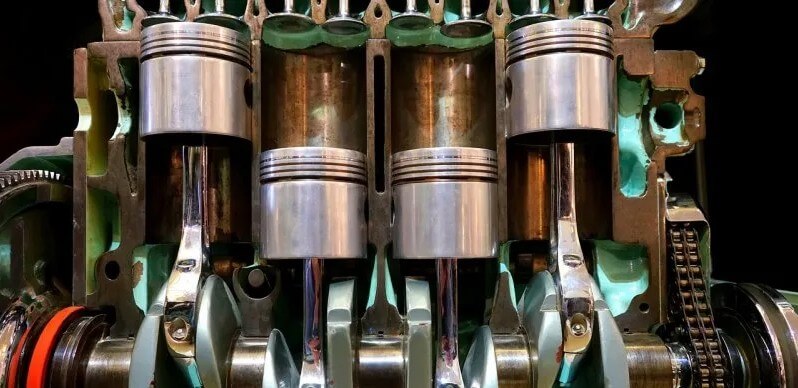
(2) Zinc alloy
1) Characteristics:
High relative density, small crystallization temperature range, not prone to porosity, good performance. Can die-cast complex and thin-walled precision parts, smooth casting surface.
2) Application:
Commonly used to make decorations, toys, home appliance housings, etc.
(3) Magnesium alloy
1) Characteristics:
Low density, high strength, good heat dissipation, strong shock resistance. Good performance, can make thin-walled and complex parts.
2) Application:
Mainly used for automotive parts, laptop computer housings, camera housings, etc.
6.Summary
The die-casting process can produce complex parts with precise dimensions and smooth surfaces by filling molten metal at high pressure and high speed, and is widely used in various industries. A deep understanding of the working principle of die-casting will help optimize process parameters and improve casting quality and production efficiency.