Die Casting and Sand Casting: Differences and Selection Guide
Die casting and sand casting are two common metal casting processes, each with its own advantages and disadvantages. When choosing between them, you need to consider factors such as product type, budget and performance. This article will detail the differences between die casting and sand casting and how to choose the right casting method.
1.Die Casting Process
(1) Definition
Die casting is the process of injecting molten metal into a metal mold under high pressure. When the hot molten metal is injected, the steel mold is formed into the desired product shape. After the metal cools, the mold is removed and can be used again.
(2) Advantages
1) Short production cycle, the average production time for one product is 30 seconds to 1 minute.
2) Short downtime, enabling efficient and continuous production.
3) The product structure is uniform, suitable for mass production, cost-effective, and the product surface finish is good.
(3) Disadvantages
1) Due to its high melting point, it is not suitable for casting ferrous metals.
2) High cost.
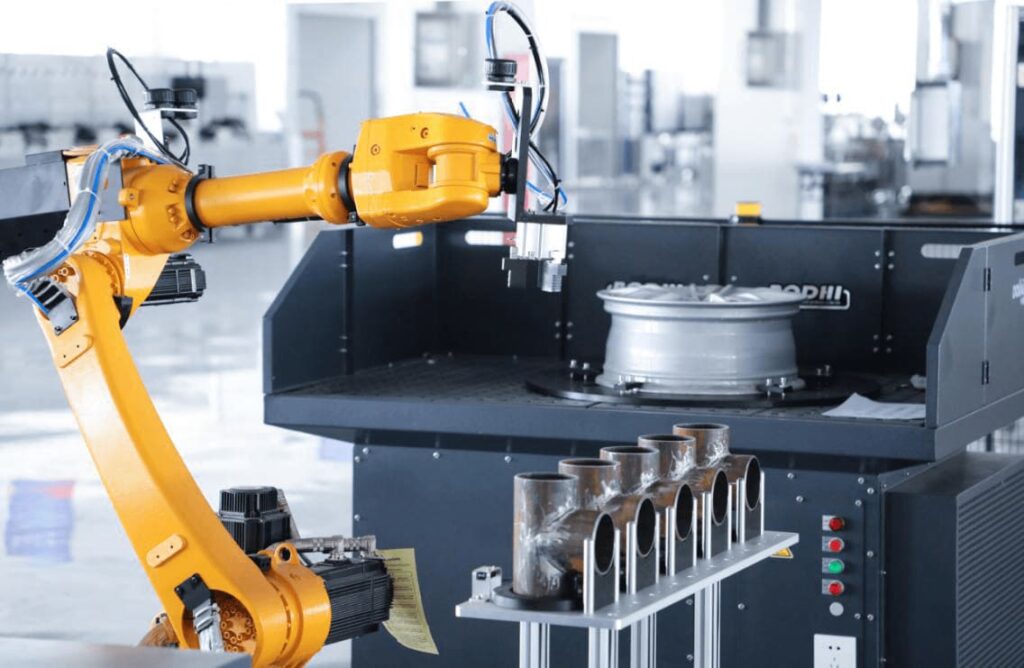
2.Sand casting process
(1) Definition
Sand casting molds are made of sand. Molten metal is poured into the sand mold through the metal. The process does not require high-pressure metal injection. Sand molds are made using a template made of plastic or wood. Sand is poured around the template and packed tightly. Once the template is removed, the molten metal fills the space. After molding, the mold is opened and the sand is brushed off.
(2) Advantages
1) Flexible design shape, can adapt to casting of complex shapes.
2) Large mold capacity, suitable for large castings.
3) Low production volume and high cost-effectiveness.
(3) Disadvantages
1) Surface finish is very rough and may require additional finishing.
2) Mold preparation time is long.
3) Product dimensional accuracy is low.
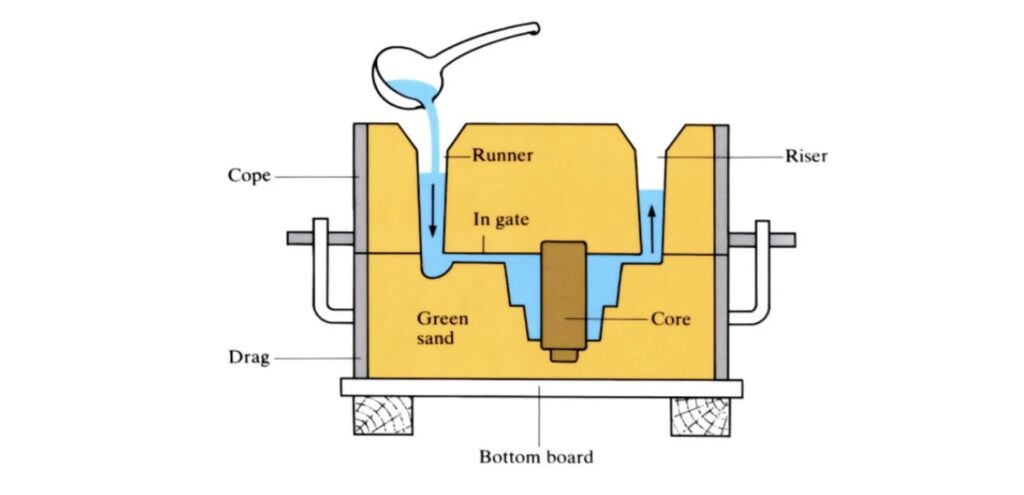
3.Die casting and sand casting differences
(1) Materials:
Die casting molds are made of metal, while sand casting molds are made of sand. Metal molds are more durable because the molten metal is injected under high pressure; sand molds are more difficult to design.
(2) Complexity of results:
Sand casting is more flexible in object shape, but its dimensional accuracy is not as high as that of die casting. Die casting has limited design complexity, but high dimensional accuracy.
(3) Wall thickness:
Sand casting usually requires thicker walls to facilitate subsequent process adjustments; die casting has thinner walls and higher dimensional accuracy. Small objects are not suitable for sand casting.
(4) Production capacity:
Die casting has a fast production cycle, but long initial delivery time; sand casting is relatively easy to build, but has a longer production cycle. Die casting is suitable for large-scale production, while sand casting is suitable for small-scale production.
(5) Cost-effectiveness:
Die casting molds are expensive to manufacture, but large-scale production can reduce costs; sand casting is cheaper and suitable for small-scale production.
(6) Surface finish:
Die casting has a smooth surface; sand casting may result in a rough surface that requires additional polishing.
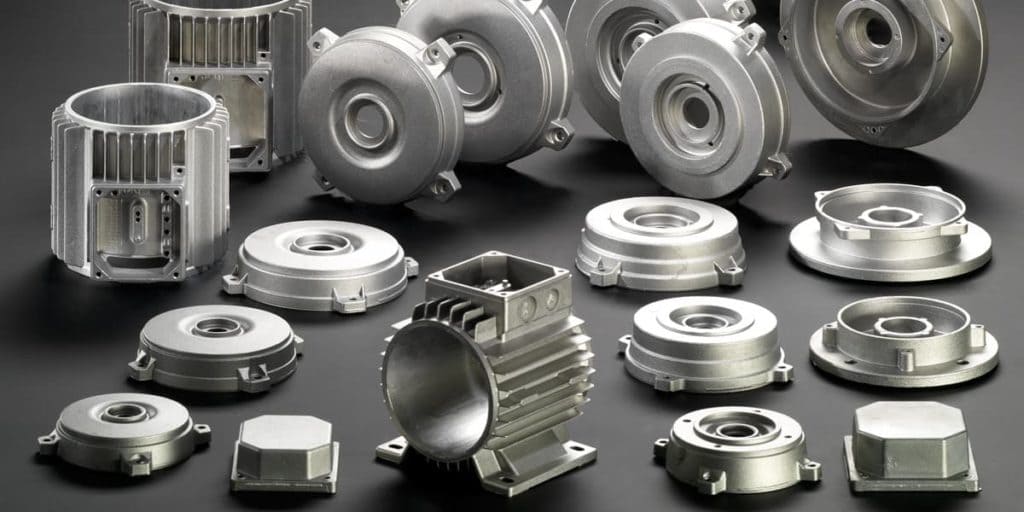
4.How to choose between die casting and sand casting?
(1) Specific selection
Die casting is the best choice for producing small, precise and durable objects such as medical devices.
Sand casting is more suitable for the production of large objects.
For mass production of small and medium-sized objects, choose die casting.
For small-scale production of medium and large objects, sand casting is more suitable.
(2) Notes
The choice between die casting and sand casting depends on the end use and product output.
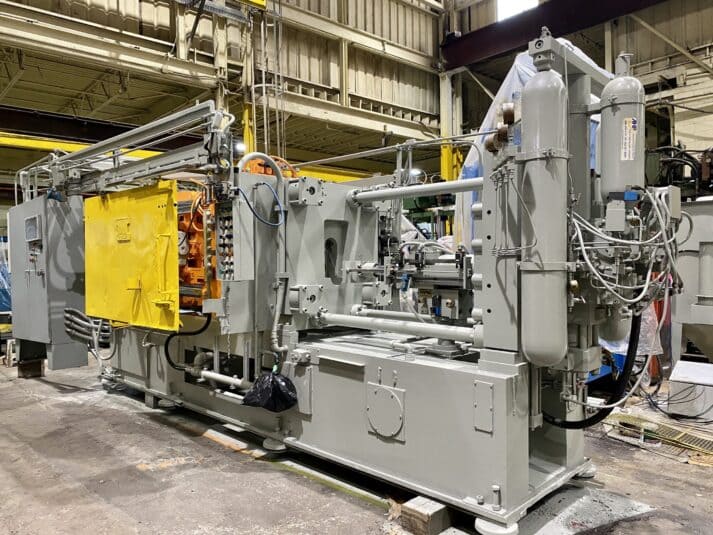
5.Conclusion
When choosing between die casting and sand casting, factors such as product characteristics, budget and performance must be considered. If you have questions about the casting project, you can seek support from a professional team. LVXUN has a team of engineers who can answer your questions about metal casting systems, equipment and processes at any time.