In-depth Analysis and Applications of Die Casting
As an important manufacturing process, die casting occupies an important position in the industrial field, especially in industries with strict requirements for high-precision parts. The die casting process is basically to inject liquid metal into a mold under high pressure to produce parts with complex shapes, precise dimensions and smooth surfaces.
1.Key components of the die casting process
(1) Shape:
It is made of high-quality steel or aluminum and can withstand the extreme pressure and temperature during the casting process. The mold is divided into two halves: the cover and the top mold.
(2) Injection system:
Includes the injection mechanism and the chamber. After the molten metal is sucked in and heated, it is injected into the mold under controlled pressure through a fast hydraulic or electrical system.
(3) Heating and cooling system:
Temperature control is essential. The heating system keeps the metal at the optimal pouring temperature of about 700°C-800°C, while the cooling channels in the mold help to quickly dissipate heat after injection and promote solidification.
(4) Ejection system:
Composed of pins and plates. Once the casting is completely cooled and hardened, the finished part can be removed without damage, thus reducing cycle time and improving production efficiency.
(5) Metal alloys:
Casting performance depends on the alloy used. Common alloys include copper, zinc, magnesium and aluminum, etc., which are selected according to the mechanical properties and corrosion resistance level required for a specific application.
(6) Quality control equipment:
Inspection instruments consisting of coordinate measuring machines (CMMs) and non-destructive testing (NDT) technology are used to verify that the casting meets strict quality requirements.
2.Advantages of die casting process
(1) High precision and complex shapes:
Die casting can repeatedly manufacture complex shapes with extremely high precision, and the steel molds used can withstand thousands of cycles, ensuring dimensional stability during large-scale production. Tolerances can be close to ±0.1mm to meet the needs of complex design applications.
(2) Good surface finish:
The surface finish is generally comparable to that of machined parts, with a minimum average roughness (Ra) of 0.8 µm, which reduces the need for post-processing, reduces costs and shortens production time.
(3) Efficient materials:
Compared with traditional casting technology, injection molding can reduce waste generation. The molten metal enters the mold under controlled conditions, filling all the space, with a utilization rate of more than 90%, which is more environmentally friendly.
(4) High production efficiency:
It has high throughput potential and is suitable for large-scale industrial mass production per unit time. Parts can sometimes be produced in a few minutes, thus shortening delivery time and speeding up the supply chain process.
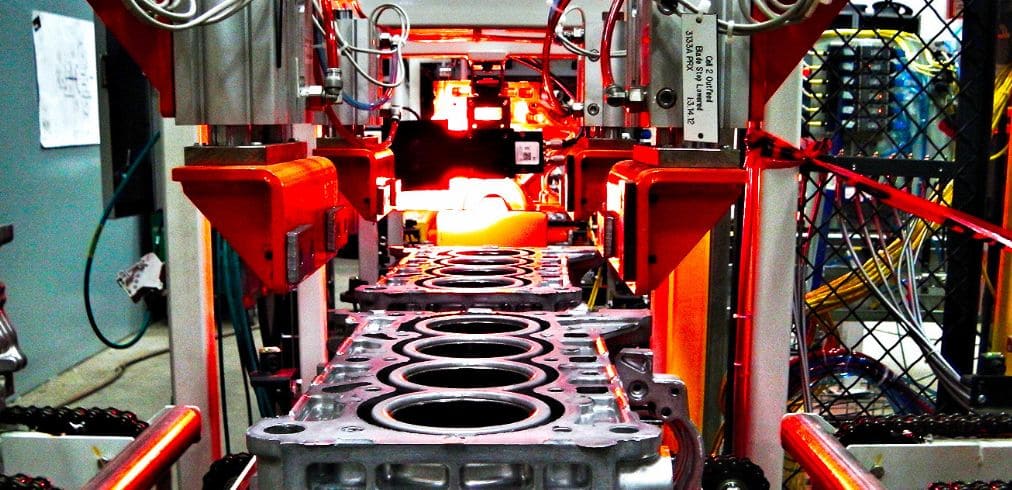
3.How to achieve high-quality die casting?
(1) Ensure dimensional accuracy and surface finish
In order to achieve high dimensional accuracy and good surface finish in die casting, many factors must be controlled. These include maintaining the correct molten metal and mold temperature, precise die casting timing to prevent turbulence, designing a unified mold to eliminate variations, regular mold maintenance, and careful quality control throughout the casting process. At the same time, choosing the right alloy will also affect the final surface quality and dimensional integrity of the casting.
(2) Solve common problems such as pores
Porosity is a common injection molding defect that can be solved by the following methods:
1) Filling dynamics optimization:
Use modeling software to predict the flow pattern in the mold, find potential air pockets, modify the gating system to reduce turbulence risks and improve flow.
2) Metal temperature control:
Maintain the molten metal at an appropriate temperature during the filling stage to reduce the possibility of air lock.
3) Improve vacuum conditions:
Use vacuum injection molding technology to eliminate air pockets in the mold and reduce porosity.
4) Choose the right material:
Reduced gas solubility in the alloy and reduced porosity trend.
5) Regular maintenance and inspection:
Continuously inspect and maintain the mold to prevent defects and ensure it is in optimal condition.
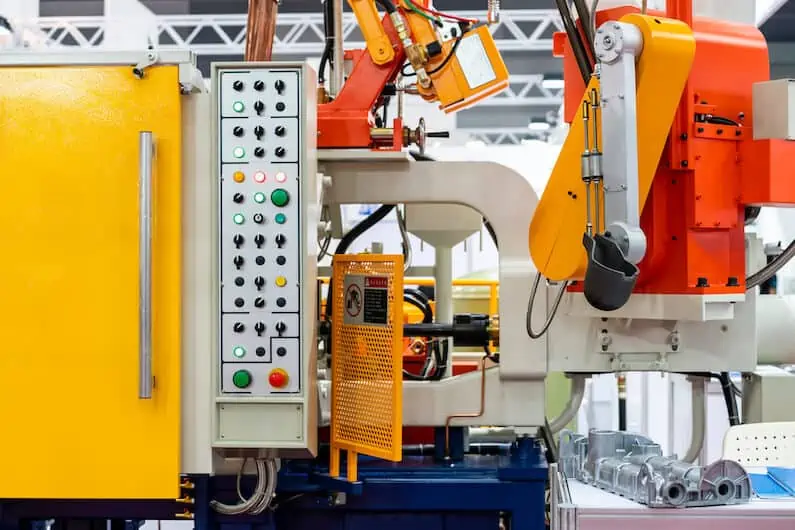
4.How to achieve excellent finished products through die casting
(1) Introduction to advanced technology:
Implement automation and advanced technologies such as computer numerical control (CNC) machining and robotic machining to improve accuracy, reduce human errors and increase production efficiency.
(2) Pay special attention to design optimization:
Use finite element analysis (FEA) tools in the design stage to simulate flow dynamics, identify potential defects and achieve efficient design to obtain excellent casting results.
(3) Introduce sustainable practices:
Implement sustainable practices in injection molding, such as using recycled materials and energy-saving methods, to protect the environment and ensure cost-effectiveness.
Industries that benefit most from die casting
(1) Automobile industry
In the automobile industry, injection molding is widely used to produce high-precision parts such as engine blocks, gearbox housings, suspension components, interior and exterior trims, heat exchangers, etc. to ensure the strength, durability, lightness and aesthetics of automotive parts, and also improve the overall power output of the engine.
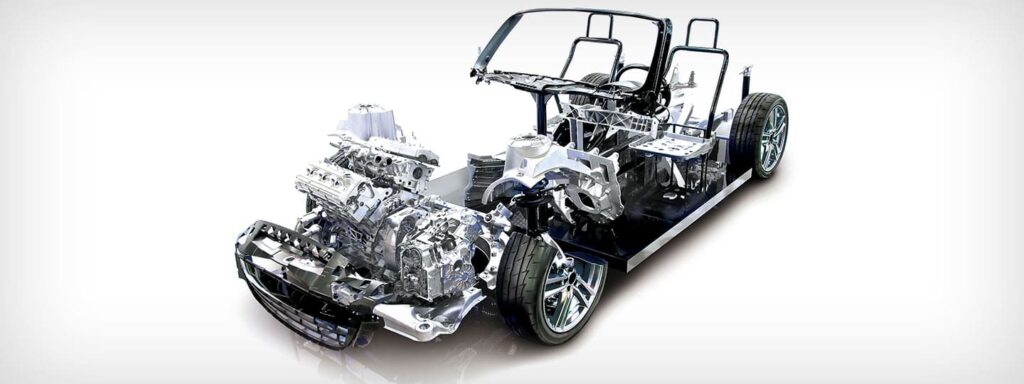
(2) Electronics and communications industry
In the electronics and telecommunications industry, injection molding is used to produce high-performance and complex lightweight parts such as housings, radiators, connectors, PCB housings, etc. to protect sensitive electronic equipment, improve heat dissipation performance, provide reliable connections and support printed circuit boards, and improve equipment reliability.
What do you think?
[…] pressure chamber is separated from the furnace. During die casting, the molten metal needs to be taken out of the insulated furnace and poured into the pressure […]
Comments are closed.