Customized die casting service: shaping excellent quality
Customized die casting service refers to the manufacturer providing one-stop service and solutions for die-casting production according to the specific needs of customers. This service model is beneficial to both parties. Based on this, this article will elaborate on the overview, process, advantages and other aspects of customized die casting services to help everyone understand the principles of customized manufacturing.
1.Overview of customized die casting services
(1) Definition and importance
Customized die casting service is a full range of services from design, mold manufacturing to product die casting completion according to the specific needs of customers. This service is particularly important in modern industrial production because it can provide high-precision and high-efficiency parts production to meet various complex and specific industrial application needs. Customized die casting services can not only shorten the product development cycle, but also effectively reduce production costs and improve the market competitiveness of products.
(2) Service scope
Customized die casting services cover the entire process from preliminary product design to final product delivery. Specific contents include but are not limited to:
1) Product design: Detailed product design is carried out according to customer needs to ensure that the design meets functional and aesthetic requirements.
2) Mold making: Use high-quality materials and advanced processing technology to manufacture precision molds.
3) Die casting production: Use efficient die casting equipment and technology to produce products.
4) Post-processing: Including deburring, surface treatment, assembly, etc., to ensure that the product meets the required appearance and functional standards.
5) Quality control: Through strict quality inspection procedures, ensure that every product meets or exceeds customer quality expectations.
6) Logistics and delivery: Provide timely logistics services to ensure that products are delivered to customers on time.
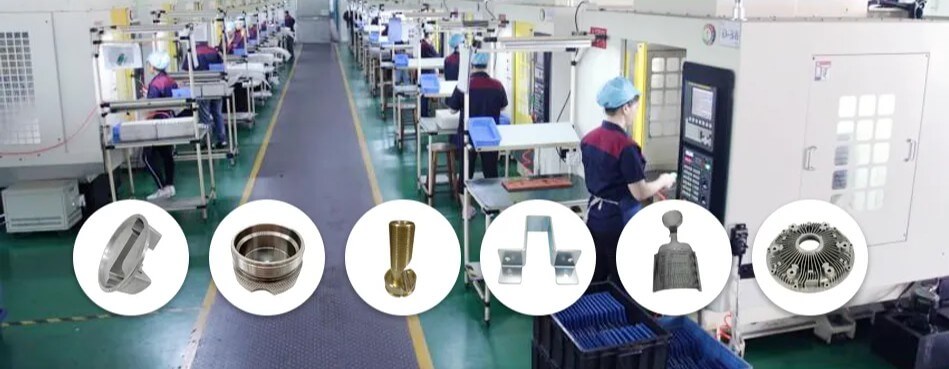
2.Die casting technology analysis
(1) Introduction to die casting process
The die casting process is a highly efficient metal forming technology that mainly injects molten metal into the mold cavity under high pressure and then cools and solidifies to form precision parts. This process is suitable for a variety of alloy materials such as aluminum, zinc, and magnesium. Die casting machines are generally divided into two categories: cold chamber die casting machines and hot chamber die casting machines. The specific choice depends on the type of alloy used and the characteristics of the product.
(2) Technical advantages
Die casting technology has many significant advantages, making it an indispensable part of the manufacturing industry. The main advantages include:
1) High precision: Die castings have high dimensional accuracy and good surface finish, which can reduce or eliminate subsequent machining.
2) High production efficiency: Suitable for mass production, it can produce a large number of parts of the same specifications in a short time.
3) Low cost: Although the initial investment cost of the mold is high, the cost per unit product is low in the long run due to high production efficiency.
4) High material utilization: The material utilization rate of the die casting process is relatively high, which reduces material waste.
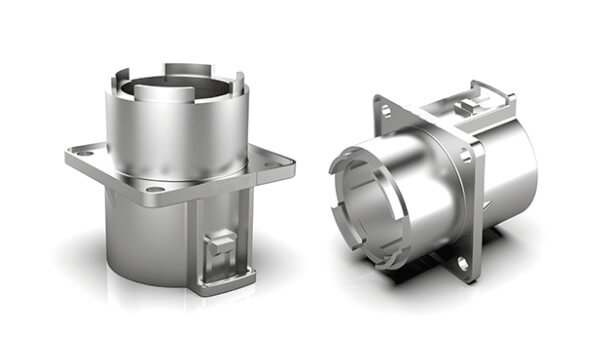
3.Common problems and solutions
Although die casting technology has many advantages, some problems may also be encountered during the production process, such as pores, cracks, and inaccurate dimensions. These problems can usually be solved by the following measures:
(1) Optimize mold design:
Ensure that the cooling system and exhaust system of the mold are reasonably designed to avoid pores and cracks.
(2) Control die casting parameters:
Precisely control parameters such as temperature, pressure and speed during the die casting process to improve product quality.
(3) Select high-quality materials:
Use high-quality metal alloy materials to improve the mechanical properties and service life of the product.
(4) Improve post-processing process:
Through effective post-processing processes such as heat treatment and surface treatment, product performance can be further improved.
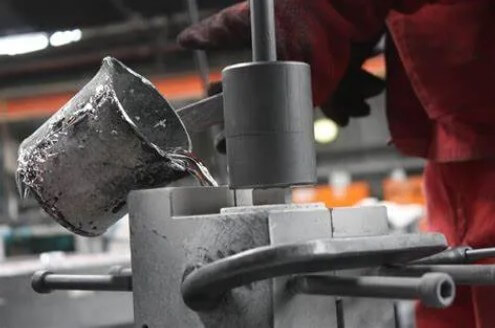
4.Customized die casting service process
(1) Demand analysis
The first step in customized die casting services is to communicate in depth with customers to understand their specific needs. This includes key information such as product functional requirements, application environment, and expected life. The goal of this stage is to ensure that the service provider can accurately grasp the customer’s needs and lay a solid foundation for subsequent design and production.
(2) Design and simulation
After clarifying the customer’s needs, the service provider will carry out detailed design of the product. This usually involves 3D modeling using advanced CAD software. In addition, CAE software may be used for simulation analysis to predict the performance of the product under actual use conditions. These simulations can help identify potential design problems, thereby optimizing them at the design stage and avoiding costly modifications in production.
(3) Mold making
The mold is the core tool in the die-casting process, and its quality directly affects the quality and production efficiency of the final product. The mold making process includes multiple steps such as material selection, determination of processing technology, and mold trial. At this stage, it is crucial to use high-quality materials and precision processing equipment. In addition, mold trial is an essential step that helps verify the design and function of the mold to ensure that products that meet the design requirements can be produced.
(4) Production and quality control
During the production stage, the use of efficient production processes and strict quality control systems is the key to ensuring product quality. This includes quality control of raw materials, real-time monitoring during the production process, and final inspection of finished products. Through these measures, it can be ensured that every die-casting part meets or exceeds the customer’s quality expectations.
(5) Post-processing and delivery
Post-processing includes deburring, surface treatment (such as spraying, electroplating) and other processes for die-casting parts to improve the appearance and performance of the product. Afterwards, the product will undergo rigorous inspection to ensure that it meets all technical specifications and quality standards. Qualified products will be properly packaged and delivered to customers on time through a reliable logistics system.
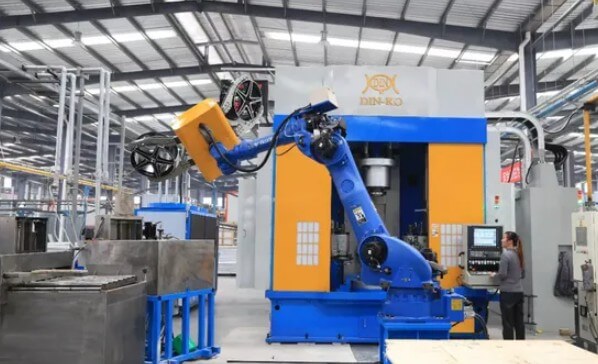
5.Advantages of customized die casting services
From the customer’s perspective, customized die casting services have many advantages, which are mainly analyzed from the following aspects:
(1) Meeting personalized needs:
Each customer’s product needs are unique, and customized die casting services can design and produce products according to the customer’s specific requirements. Whether it is the shape, size, material, or surface treatment of the product, it can be completely customized according to the customer’s needs to meet the customer’s personalized needs.
(2) Improving product performance:
Customized die casting services can optimize product design and material selection according to the actual use environment and functional requirements of the product, thereby improving product performance. For example, for products that require high strength and high corrosion resistance, the corresponding alloy materials can be selected for die-casting to improve the product’s service life and reliability.
(3) Reducing production costs:
For mass-produced products, customized die casting services can reduce the production cost of a single product by optimizing mold design and production processes. In addition, customized services can also reduce the cost of post-processing and assembly of products, further improving the cost performance of products.
(4) Shorten product development cycle:
Customized die casting service providers usually have rich experience and professional technical teams, and are able to complete product design and mold manufacturing in a short time, thereby shortening the product development cycle. For customers, this means that they can bring products to market faster and seize market opportunities.
(5) Provide one-stop service:
Customized die casting service providers can usually provide one-stop service from product design, mold manufacturing, die-casting production to post-processing. This not only reduces the burden on customers, but also ensures product quality and delivery time.
(6) Enhance competitiveness:
Through customized die casting services, customers can obtain unique product designs and increase the added value of products, thereby occupying an advantageous position in market competition. In addition, customized services can also help customers differentiate their products and avoid product homogeneity with competitors.
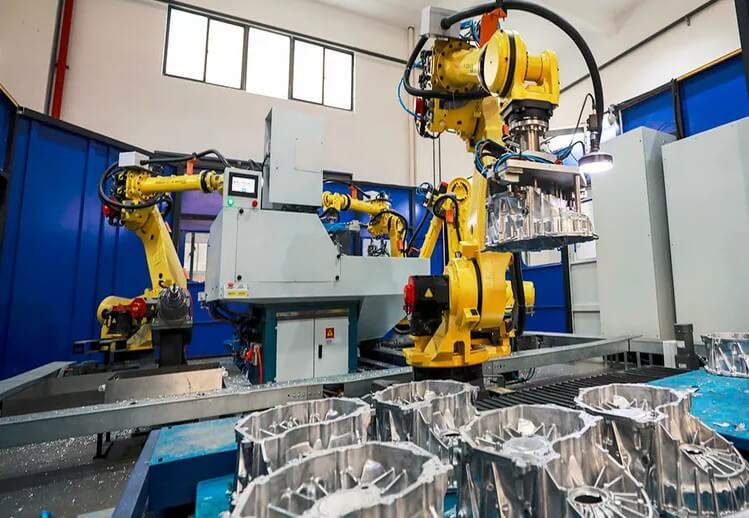
6.When do customers need customized die casting services?
(1) Product category restrictions:
When customers cannot find suitable standard parts for the products they need on the market, or when standard parts cannot meet specific needs, customized die casting services may be required.
(2) Lightweight demand:
In industries such as new energy vehicles, lightweighting is a development trend. Integrated die-casting technology can reduce the number of parts and reduce weight, thereby reducing energy consumption and improving efficiency. In this case, customers may need customized die casting services to achieve lightweight products.
(3) Personalized services:
The customized services provided by Lvxun can customize die-casting products that meet the requirements of customers according to their different needs, so that customers can enjoy high-quality, high-performance products while also getting more intelligent and personalized services.
(4) Technical strength requirements:
Excellent technical strength is an important guarantee for providing high-quality products. Lvxun is equipped with advanced production equipment and testing equipment, and has an excellent team and experienced technicians, which can provide customers with all-round, one-stop technical support and services.
(5) Strict quality control:
Die-castings are complex components with high strength, high toughness and high precision. Their quality directly affects the customer’s product performance, safety, market competitiveness and other aspects. Therefore, customers may need customized die casting services to ensure product quality.
(6) Continuous innovation:
In the context of increasingly fierce global market competition, scientific and technological strength and innovation capabilities have become the key to corporate competition. Lvxun pays attention to new market trends and follows up on the latest technology and material changes, thereby obtaining new technology, new quality upgrades, and new markets.
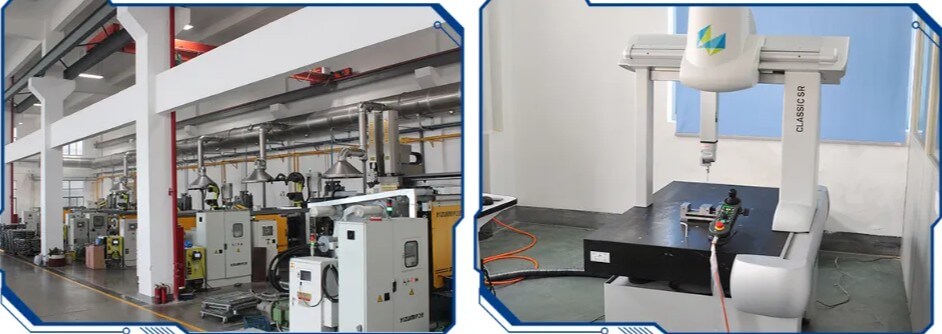
7.Summary
In short, customized die casting services can meet customers’ personalized needs, improve product performance and cost-effectiveness, shorten product development cycles, provide one-stop services, and enhance market competitiveness. These advantages can help customers achieve product innovation and differentiation and improve the market competitiveness of enterprises.