Detailed analysis of the application of corrosion resistant castings in the petrochemical industry
As the core components of petrochemical equipment, corrosion resistant castings are widely used in pump bodies, valves, pipelines, heat exchangers and other devices. Reasonable material selection, advanced manufacturing processes and effective protection measures are the key to ensuring the long-term stable operation of castings.
This article will focus on the material selection and performance optimization, manufacturing process, specific application, failure analysis and protection measures of corrosion resistant castings.
1.What are corrosion resistant castings?
(1) Definition
Corrosion resistant castings refer to casting parts that can work stably and for a long time in a corrosive environment through special material selection, manufacturing process and surface treatment technology. These castings are usually used in industrial equipment exposed to acids, alkalis, salts, gases or other corrosive media, and can effectively resist chemical corrosion, electrochemical corrosion, stress corrosion cracking and other forms of corrosion.
(2) Characteristics of corrosion resistant castings:
1) Material properties:
● Use corrosion-resistant alloys such as stainless steel, nickel-based alloys, titanium alloys, high-silicon cast iron, etc.
●The material has high corrosion resistance, high strength and good mechanical properties.
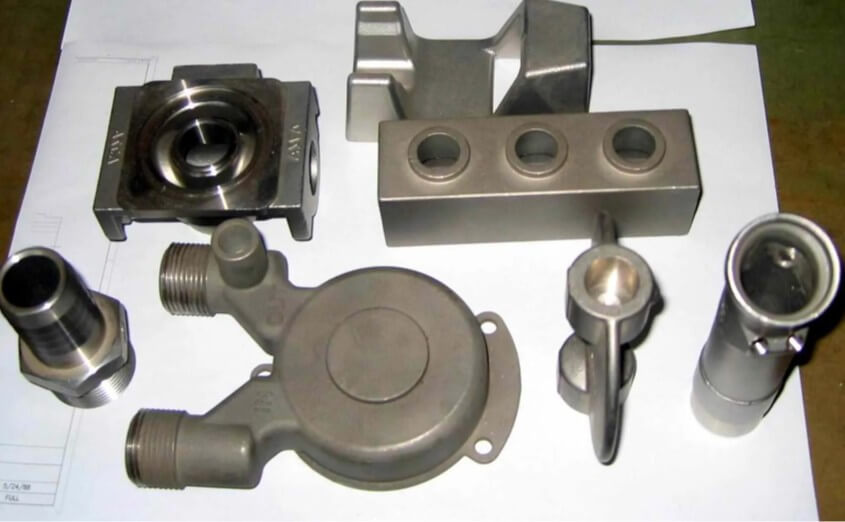
2) Manufacturing process:
●Adopt precision casting technology, such as investment casting, gravity casting, low-pressure casting, die casting (widely used in aluminum metal materials), etc., to ensure the high quality and complex shape of the castings.
●Further improve the corrosion resistance through heat treatment and surface treatment (such as spraying and electroplating).
3) Application environment:
●Suitable for extreme working conditions of high temperature, high pressure and highly corrosive media.
●Commonly used in petrochemical, marine engineering, power, pharmaceutical and other industries.
2.Common corrosion forms of parts in the petrochemical industry
(1) Uniform corrosion
The metal surface corrodes uniformly as a whole, resulting in a gradual decrease in the thickness of the material.
Common scenarios:
The inner wall of the storage tank or pipeline is in contact with acidic or alkaline media.
The inner wall of the reactor is in contact with corrosive chemicals.
(2) Pitting (local corrosion)
Deep corrosion occurs in a local area of the metal surface, forming small holes or pits.
Common scenarios:
Stainless steel equipment in chloride ion environments (such as seawater and salt water).
Pipes, valves, heat exchangers and other components.
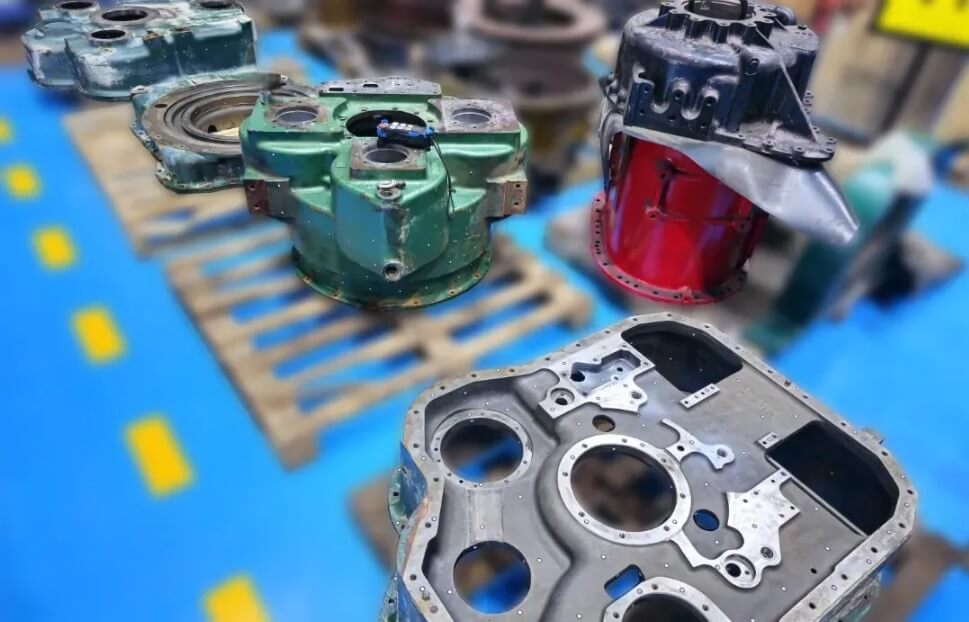
(3) Stress corrosion cracking (SCC)
Under the combined action of tensile stress and corrosive media, cracks are generated and extended on the metal surface.
Common scenarios:
Reactors and pipelines in high temperature and high pressure environments.
Equipment exposed to corrosive media such as hydrogen sulfide and chloride ions.
(4) Intergranular corrosion
Corrosion occurs along the metal grain boundaries, resulting in preferential corrosion of the grain boundary area.
Common scenarios:
Welded joints or improperly heat-treated components.
Equipment exposed to acidic media.
(4) Erosion corrosion
The high-speed flow of fluid causes the combined action of mechanical erosion and chemical corrosion on the metal surface.
Common scenarios:
Pipeline elbows, pump casings, impellers and other components.
Fluid transport systems containing solid particles.
(5) Hydrogen embrittlement
Metals absorb hydrogen atoms in a hydrogen environment, causing the material to become embrittled and cracked.
Common scenarios:
Hydrogenation reactors, high-pressure hydrogen pipelines.
Equipment in acidic environments (such as hydrogen sulfide).
Summary:
In the petrochemical industry, there are various forms of corrosion of parts and components, mainly due to the presence of high temperature, high pressure, highly corrosive media (such as acid, alkali, salt, hydrogen sulfide, chloride ions, etc.) and complex working conditions in the environment.
Therefore, it is necessary to improve the corrosion resistance of castings and extend the service life of equipment through reasonable material selection, advanced manufacturing processes and effective protection measures. The following will introduce in detail how to improve the performance of corrosion resistant castings to extend the service life of chemical equipment:
3.Material selection and performance optimization of corrosion resistant castings
(1) Main corrosion resistant materials and characteristics
The corrosion resistant casting materials commonly used in the petrochemical industry mainly include the following categories:
1) Stainless steel (304, 316L, 2205 duplex stainless steel)
It has good acid and alkali corrosion resistance, especially 316L containing molybdenum performs well in strong acid environment. Duplex stainless steel has advantages in pitting and stress corrosion resistance, and is suitable for pipelines, heat exchangers and other equipment.
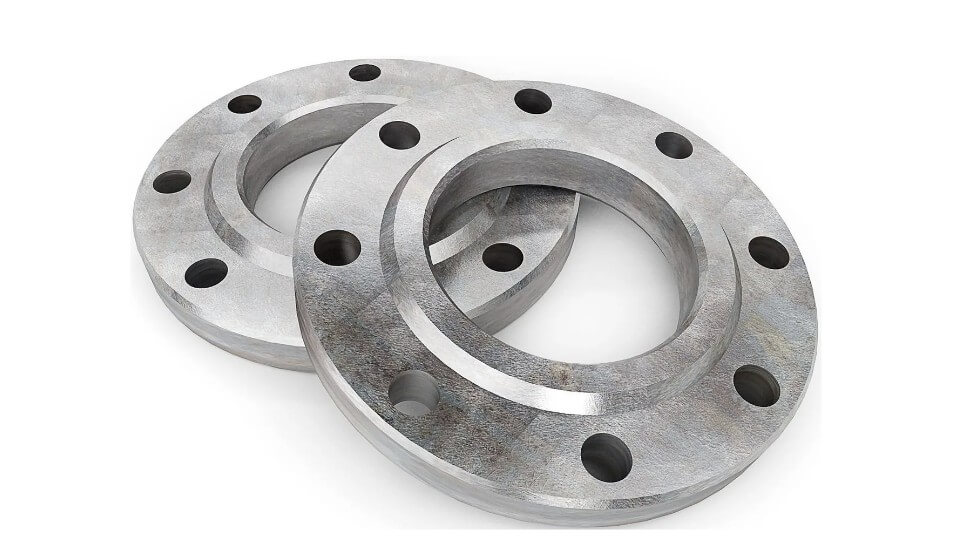
2) High silicon cast iron (Si≥14%)
High silicon cast iron has excellent corrosion resistance in strong acid media such as concentrated sulfuric acid, and is often used in pumps and pipelines for conveying strong acids, but it is relatively brittle.
3) Nickel-based alloys (Inconel, Hastelloy, Monel)
It has excellent resistance to high-temperature oxidation and chloride ion corrosion, and is widely used in catalytic cracking equipment, heat exchanger pipelines, etc.
4) Cobalt-based alloy (Stellite)
Mainly used in high-temperature wear-resistant parts, such as valve sealing surfaces, bearings, etc., and performs well under high-temperature conditions.
5) Titanium and titanium alloys
Due to their strong resistance to chloride corrosion, they are widely used in key corrosion resistant castings such as offshore oil platforms, cooling systems, and pipelines.
(2) Material performance optimization methods
1) Alloy element optimization:
Add alloy elements such as Cr, Mo, and Ni to improve the corrosion resistance and high-temperature stability of the material.
2) Heat treatment process:
Optimize the microstructure of the material through solid solution and tempering treatment to improve the stress corrosion resistance.
3) Surface modification technology:
Use nitriding, PVD/CVD coating, ceramic spraying and other methods to improve corrosion resistance and wear resistance.
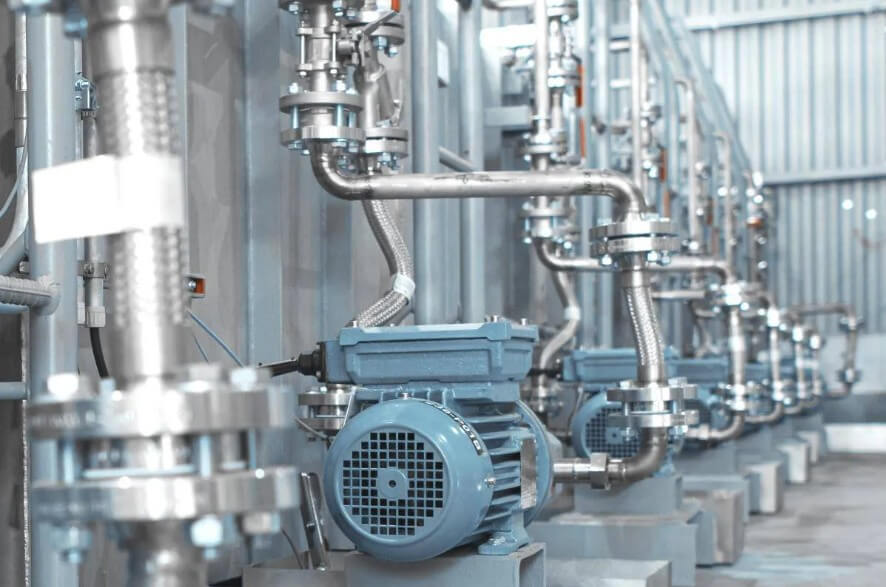
4.Overview of the processing technology of corrosion resistant castings in petrochemical industry
According to the different requirements of petrochemical equipment for corrosion resistant castings, the following casting processes are mainly used:
(1) Gravity casting
1) Applicable parts:
Large pump bodies, valve housings, heat exchanger brackets, reactor base parts and other thick-walled corrosion resistant castings.
2) Process characteristics:
● Relying on the gravity of the molten metal to fill the cavity, no additional pressure is required, and the process is relatively simple.
● Suitable for the production of large-sized castings with relatively uniform wall thickness, suitable for carbon steel, stainless steel and some high-alloy materials.
● Due to the slow cooling rate, the internal structure of the casting is uniform, reducing the risk of stress concentration and cracking.
● It can be formed by sand molds, metal molds, etc., with high flexibility.
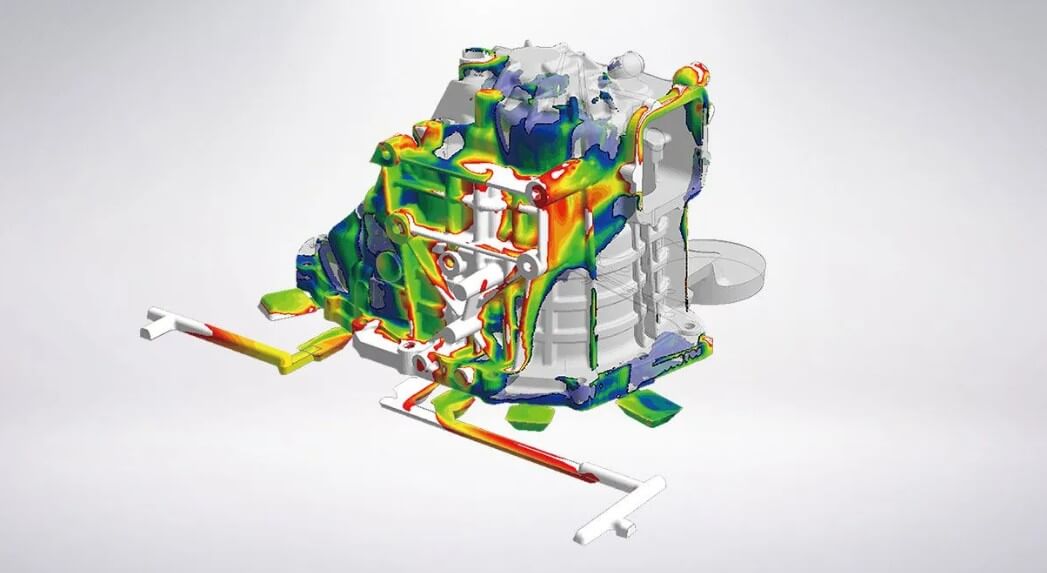
3) Application cases:
● Large petrochemical pump casing:
Required to withstand long-term high temperature and high pressure and corrosive medium erosion, gravity casting is used to ensure the strength and corrosion resistance of the casting.
● Reactor base and bracket:
Large support structures require high load-bearing capacity and corrosion resistance. Gravity casting can ensure their integrity and mechanical strength.
● Petrochemical equipment valve body:
Gravity casting can reduce defects such as shrinkage holes and improve the sealing and service life of the valve body.
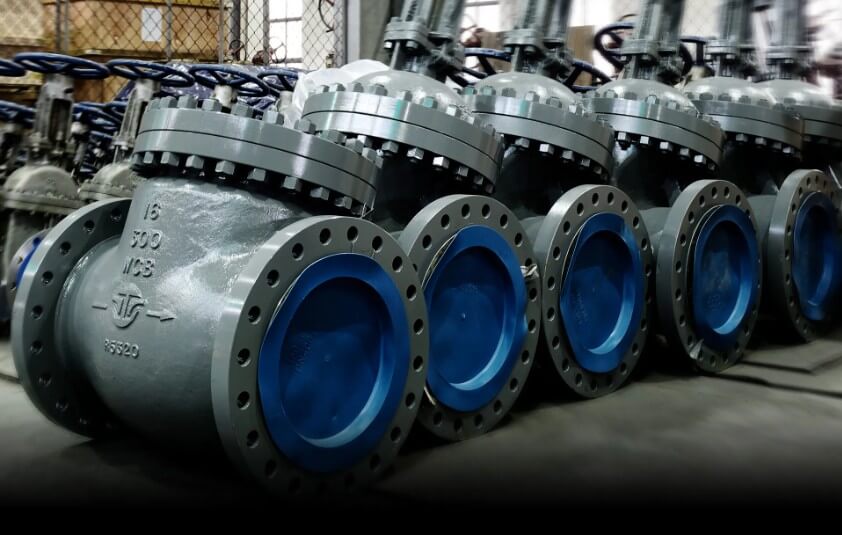
(2) Investment casting (precision casting)
1) Applicable parts:
High-precision complex castings such as valve body, impeller, pump housing, flange, etc.
2) Process characteristics:
● Using wax molds to make precision shell molds, it can produce castings with complex shapes and thin walls.
● High dimensional accuracy of castings (up to ±0.05mm), reducing machining volume and improving material utilization.
● Applicable to highly corrosion-resistant materials such as stainless steel, duplex stainless steel, and nickel-based alloys.
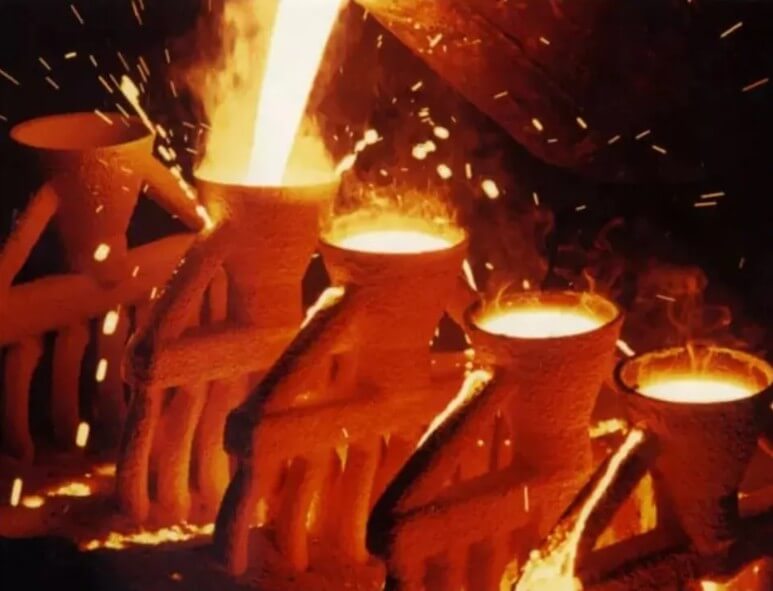
3) Application cases:
● High-pressure valve body castings:
Need to withstand high temperature, high pressure and highly corrosive media. Investment casting can achieve defect-free dense molding and avoid microcracks during machining.
●Chemical pump impeller:
Using CD4MCu duplex stainless steel casting, it improves the resistance to chloride ion corrosion and prolongs the service life.
(3) Low-pressure casting
1) Applicable parts:
Heat exchanger shell, reactor accessories, petrochemical pipeline joints and other corrosion resistant castings with high density requirements.
2) Process characteristics:
●Use low pressure (usually 0.02-0.06MPa) to slowly fill the mold cavity with molten metal, reduce pores and improve the density of castings.
●Can produce castings with uniform wall thickness and excellent corrosion resistance, suitable for high temperature and high pressure environment.
●Mainly used for casting special corrosion-resistant materials such as high-alloy stainless steel, nickel-based alloy, titanium alloy, etc.
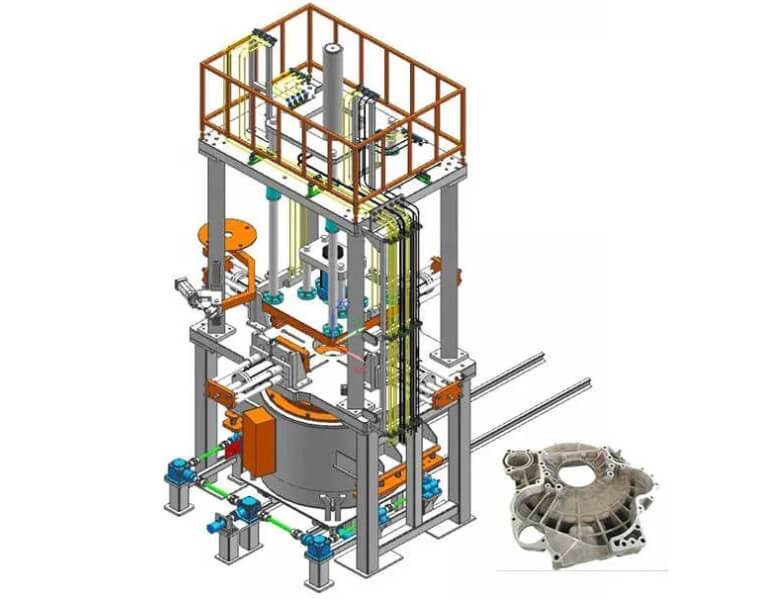
3) Application cases:
●Heat exchanger shell:
The heat exchanger is in contact with corrosive media for a long time. Low-pressure casting can improve the uniformity and corrosion resistance of the material and reduce the risk of leakage.
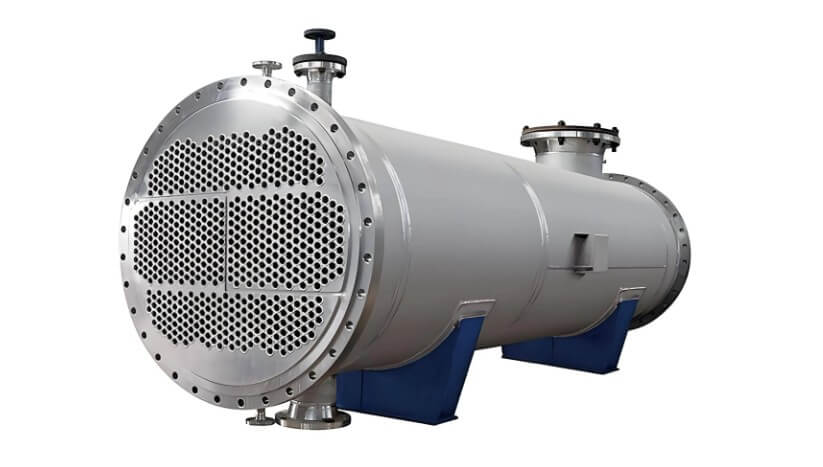
● Reactor agitator:
The stirring parts used for catalytic reactions require high corrosion resistance. Low-pressure casting can ensure a smooth surface without defects and increase service life.
5.Quality control measures for corrosion resistant castings
In order to ensure the long-term stable operation of corrosion resistant castings in the petrochemical industry, it is necessary to strictly control quality throughout the manufacturing process.
(1) Raw material control
● Use high-purity alloy materials to reduce the content of harmful impurities such as sulfur and phosphorus to improve corrosion resistance.
● Conduct metallographic analysis to ensure that the corrosion resistant casting has uniform structure and no dendrite segregation or precipitation phase.
(2) Casting process optimization
● Rationally design the pouring system, optimize the flow channel and riser design, reduce inclusions and shrinkage holes, and improve the density of the casting.
● Strictly control the temperature and pouring speed to prevent metal liquid cooling and improve the molding quality.
● Use protective gas or vacuum environment to reduce oxidation inclusions and improve the corrosion resistance of the casting.
(3) Nondestructive testing and mechanical property testing
●X-ray testing (RT): Check internal defects such as pores and shrinkage holes.
●Ultrasonic testing (UT): Detect inclusions and cracks inside the casting.
●Penetrant testing (PT): Detect tiny cracks and holes on the surface of the casting.
●Mechanical property testing: Perform tensile, impact, and hardness tests to ensure that the casting meets the use requirements.
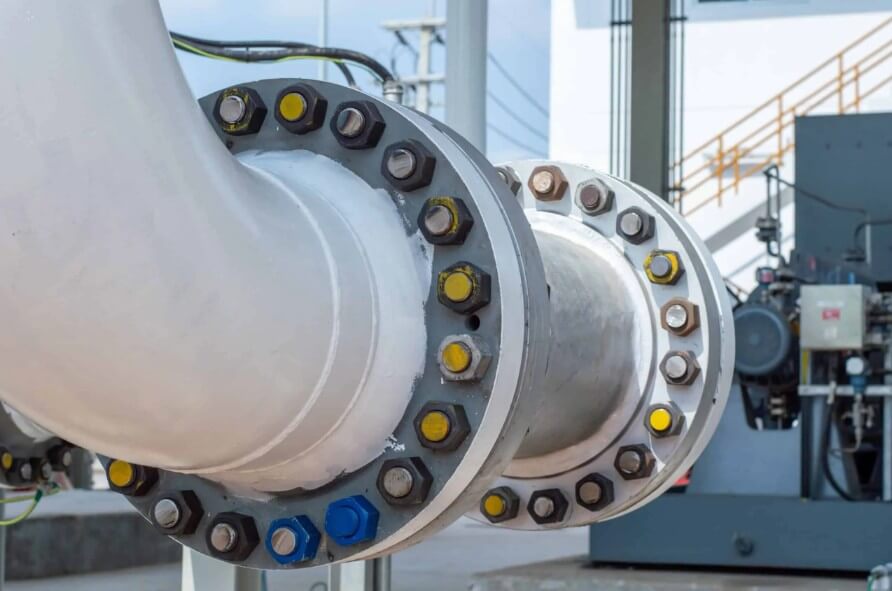
(4) Corrosion resistance testing
●Salt spray test: Evaluate the corrosion rate of castings in chloride environments.
●Electrochemical corrosion test: Test the pitting potential and corrosion resistance of castings.
●High temperature corrosion test: Simulate actual working conditions and test the corrosion resistance of castings under high temperature and high pressure environments.
6.Summary
The key role of corrosion resistant castings in the petrochemical industry cannot be ignored. Reasonable material selection, advanced manufacturing processes, and efficient protection measures are the core to ensure the long-term stable operation of equipment.