Copper mold casting: process, application, advantages and challenges
Copper mold casting is a widely used process for manufacturing metal parts, and is highly favored for its high precision and good surface finish. This article will explore the definition, characteristics, historical development, process flow, application areas, advantages and challenges of copper mold casting.
1.Definition and characteristics of copper mold casting
Copper mold casting is a technology that uses molds made of copper alloys for metal casting. Due to its excellent thermal conductivity, the copper mold can quickly absorb and dissipate the heat of the molten metal during the casting process, thereby achieving rapid cooling. This rapid cooling feature enables the casting to obtain a high surface finish and fine microstructure. The main characteristics of copper mold casting include:
(1) Fast cooling rate:
Due to the excellent thermal conductivity of copper, heat can be quickly conducted away from the liquid metal, thereby accelerating the cooling rate. This not only improves production efficiency, but also improves the microstructure and mechanical properties of the casting.
(2) High casting quality:
Rapid cooling helps to form a uniform microstructure, reduce casting defects, and improve the mechanical properties and surface finish of the casting.
(3) Wide range of applications:
It is suitable for a variety of metal materials, such as aluminum alloys, iron-based amorphous alloys, etc., and can produce castings with complex shapes and high dimensional accuracy.
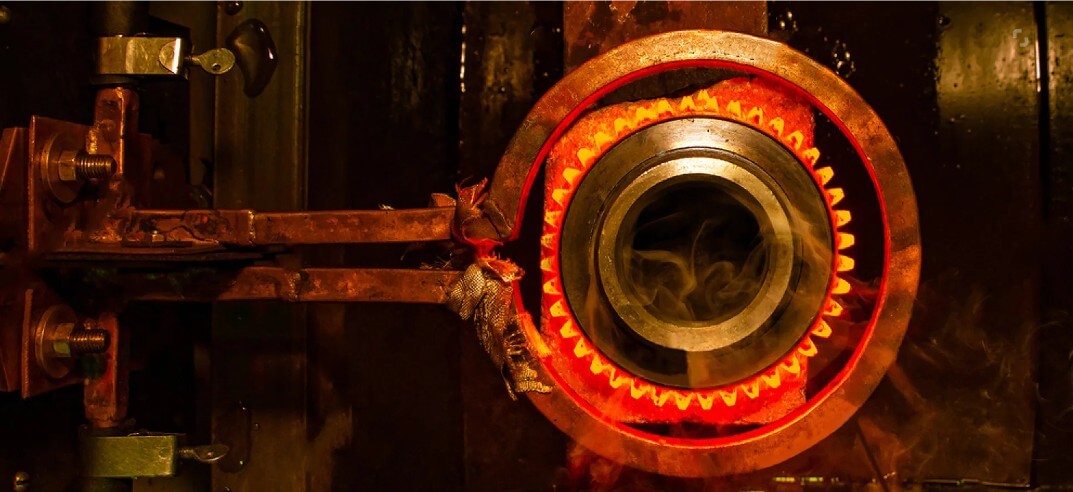
2.Historical development of copper mold casting
Copper mold casting technology originated in ancient times and was first used to make simple copperware and decorations. With the advent of the industrial revolution and the development of metallurgical technology, this technology has gradually been applied to a wider range of industrial fields. In the early 20th century, with the increasing application of aluminum alloys, it has been widely used and developed in aluminum alloy casting.
Entering the 21st century, with the advancement of computer technology and materials science, this technology has been further improved. Modern copper mold casting technology can not only produce high-quality aluminum alloy castings, but also can be used for the casting of new materials such as iron-based amorphous alloys, showing broad application prospects.
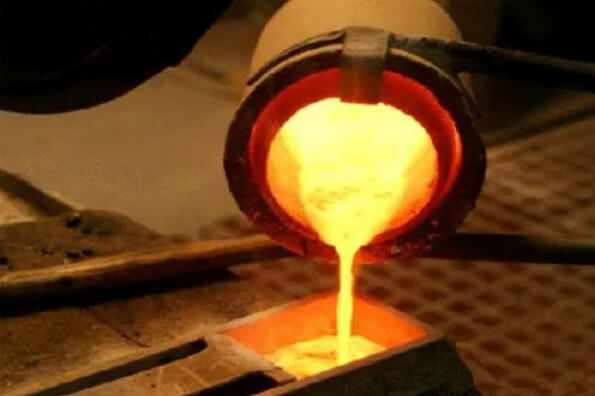
3.Design and manufacturing of copper molds
As an indispensable part of industrial production, the design and manufacturing process of copper molds has extremely high technical requirements and strict process flow. The following are the main steps and key considerations for mold design and manufacturing.
(1) Design stage:
1) Demand analysis:
According to product requirements, determine the basic parameters of the mold, such as size, shape, and structure.
2) 3D modeling:
Use CAD software to perform 3D modeling of the mold to ensure that the dimensional accuracy and shape complexity of the mold meet the product requirements. Key structures such as cooling water channels and casting systems must be considered during design.
3) Simulation analysis:
Use CAE software to perform thermodynamic and fluid mechanics simulations to optimize the mold structure and reduce thermal stress and casting defects.
(2) Material selection:
Select appropriate copper alloy materials according to the use environment and functional requirements of the copper mold. Common materials include beryllium copper, chromium copper, etc. These materials have good thermal conductivity, strength and wear resistance.
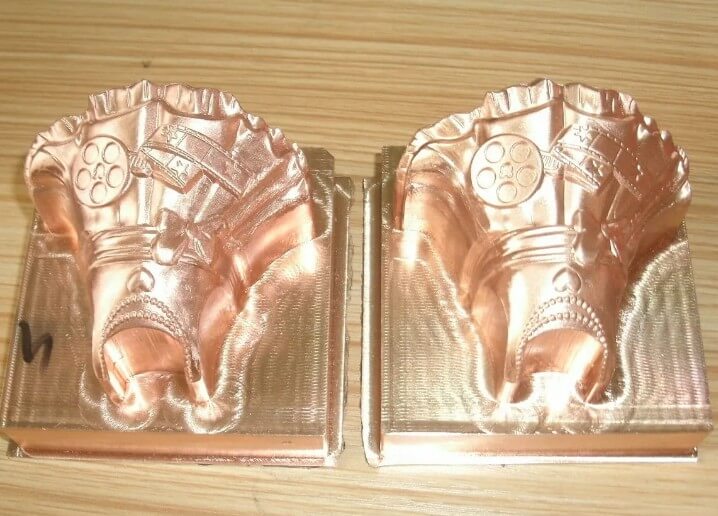
(3) Manufacturing process:
1) Processing:
Use CNC machining centers for rough and fine processing to ensure that the dimensional accuracy and surface roughness of the mold meet the requirements.
2) Heat treatment:
Perform appropriate heat treatment on the mold to improve its mechanical properties and increase its service life.
3) Surface treatment:
According to the needs, the mold surface is treated with nickel plating, chrome plating and other treatments to improve its wear resistance and corrosion resistance.
(4) Quality inspection:
1) Dimension inspection:
Use precision inspection equipment such as three-coordinate measuring machine to fully inspect the dimensions of the mold.
2) Surface inspection:
Use surface roughness meter to inspect the surface quality of the mold to ensure that it meets the process requirements.
3) Functional test:
Carry out trial mold to inspect the actual use effect of the copper mold, and make timely adjustments and improvements.
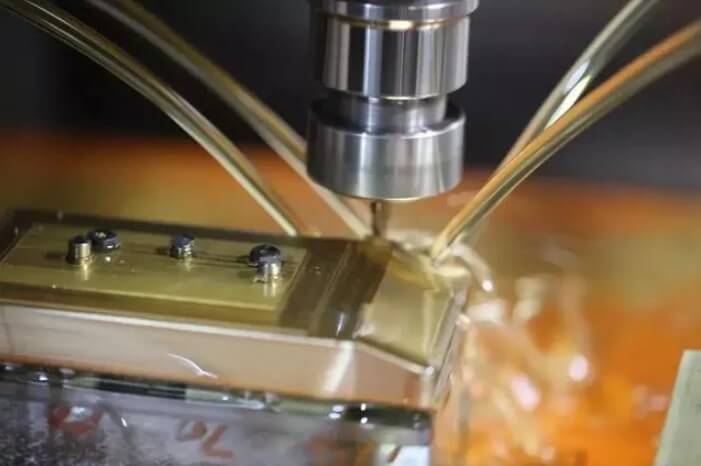
(5) Subsequent processing and maintenance:
Perform proper maintenance and maintenance on the copper mold, check its status regularly, and deal with problems found in time to extend the service life of the copper mold.
4.Process flow of copper mold casting
The process flow of copper mold casting is complex and delicate, mainly including the following steps:
(1) Mold preparation:
The first step in copper mold casting is to prepare the mold. The mold is usually made of high-temperature resistant metal materials, such as copper alloy. The mold design must be precise to ensure that the size and shape of the final casting meet the requirements.
(2) Melting metal:
Put the copper alloy raw materials into a furnace for melting. The temperature needs to be controlled during the melting process to ensure that the metal is completely melted and no excessive impurities are produced. Common copper alloys include brass (alloy of copper and zinc) and bronze (alloy of copper and tin).
(3) Pouring:
Pour the molten metal liquid into a preheated copper mold. The pouring speed and temperature need to be controlled during pouring to avoid pores or cracks. The high thermal conductivity of the copper mold helps the metal solidify quickly.
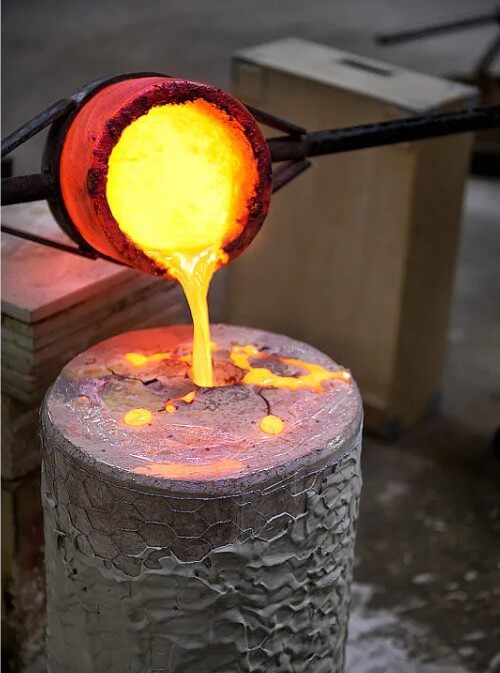
(4) Cooling and solidification:
The molten metal cools and solidifies quickly in the copper mold. This process requires strict time control to ensure that the casting is fully solidified and does not deform.
(5) Demolding:
After the casting is completely solidified, it is removed from the copper mold. Be careful when demolding to avoid damaging the casting or the mold.
(6) Post-processing:
Perform necessary post-processing on the casting, including cleaning the surface burrs, oxide scale, etc. Heat treatment may also be required to improve the mechanical properties of the casting.
(7) Inspection:
The casting is inspected for size and appearance to ensure that it meets the design requirements. Mechanical property tests such as tensile test and hardness test are carried out when necessary.
(8) Machining:
As required, the casting is further machined, such as drilling, milling, etc., to achieve the final accuracy requirements.
5.Application of copper mold casting in different fields
(1) Application in aluminum alloy casting
Aluminum alloys are widely used in aviation, automobile and construction fields due to their lightweight and high strength characteristics. Copper mold casting technology is particularly suitable for casting aluminum alloys because the rapid cooling ability of the copper mold can refine the grain structure of the aluminum alloy and improve its mechanical properties.
In the actual case of aluminum alloy copper mold casting, complex-shaped aluminum alloy parts with high precision and low porosity can be produced by precisely controlling the cooling rate and pouring technology. These parts excel in strength and durability and are widely used in important fields such as aircraft structural parts and automobile engine parts.
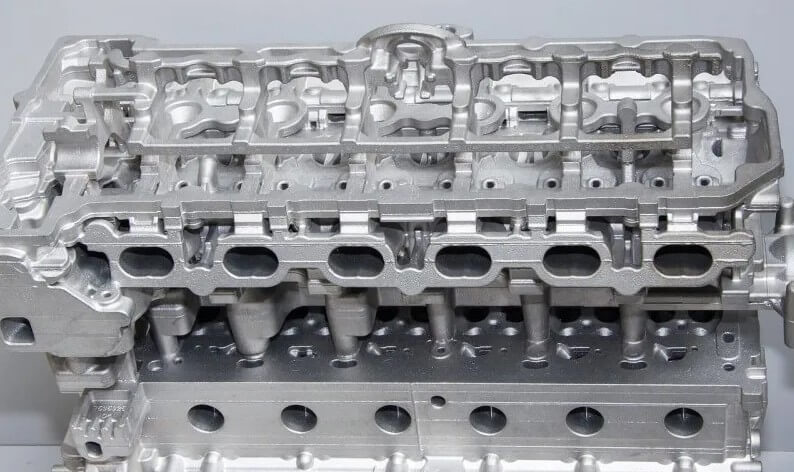
(2) Application in iron-based amorphous alloy casting
Iron-based amorphous alloys have shown great potential in the fields of electronic devices and structural materials due to their excellent soft magnetic properties and corrosion resistance. Copper mold casting technology plays a key role in the production of iron-based amorphous alloys. The rapid cooling effect of the copper mold can effectively inhibit grain growth and maintain the amorphous structure of the material.
Application examples show that iron-based amorphous alloy parts produced by copper mold casting have higher magnetic permeability and lower loss, and are very suitable for manufacturing high-performance transformer cores and sensor components.
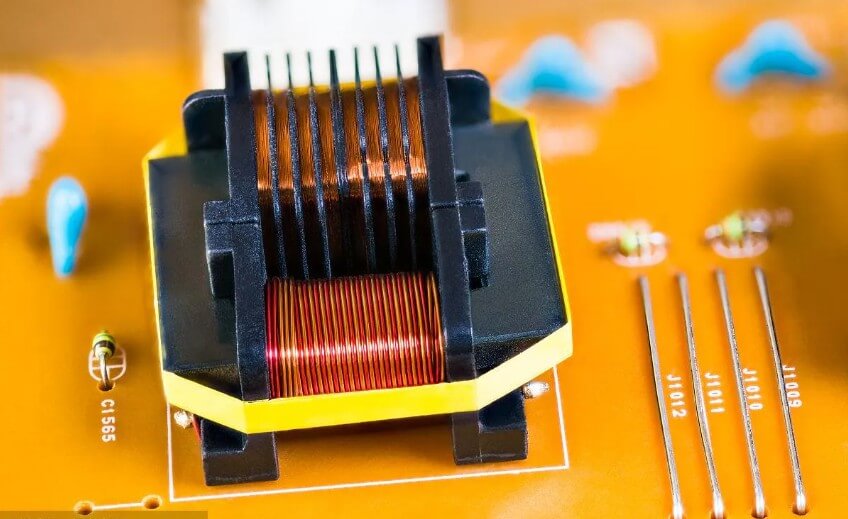
(3) Application cases of other metal materials
In addition to aluminum alloys and iron-based amorphous alloys, copper mold casting technology is also applied to other metal materials, such as copper and magnesium. In the casting process of these materials, copper mold casting technology also shows its unique advantages and can produce complex-shaped castings with excellent performance.
Comparison of copper mold casting technology for different metal materials shows that although the physical and chemical properties of various metals are different, copper mold casting technology can optimize the quality and performance of castings by adjusting process parameters such as temperature, speed and cooling method.
6.Technical advantages and challenges of copper mold casting
(1) Main advantages
The main advantages of copper mold casting technology include fast cooling speed and high product quality. Due to the excellent thermal conductivity of the copper mold, the molten metal can be cooled quickly after pouring, which not only improves production efficiency, but also helps to improve the microstructure of the casting, improve its mechanical properties and surface finish.
In addition, copper mold casting also has the advantages of production efficiency and cost-effectiveness analysis. Rapid cooling shortens the production cycle and improves production efficiency. At the same time, due to the durability and reusability of the copper mold, it reduces production costs and improves economic benefits.
(2) Technical challenges and solutions
1) Porosity and inclusions:
During the copper mold casting process, gas may be trapped in the molten metal, forming pores. In addition, impurities may also be included in the casting, affecting its quality. The solution is to fully preheat the mold before casting and add a degassing agent to the molten metal.
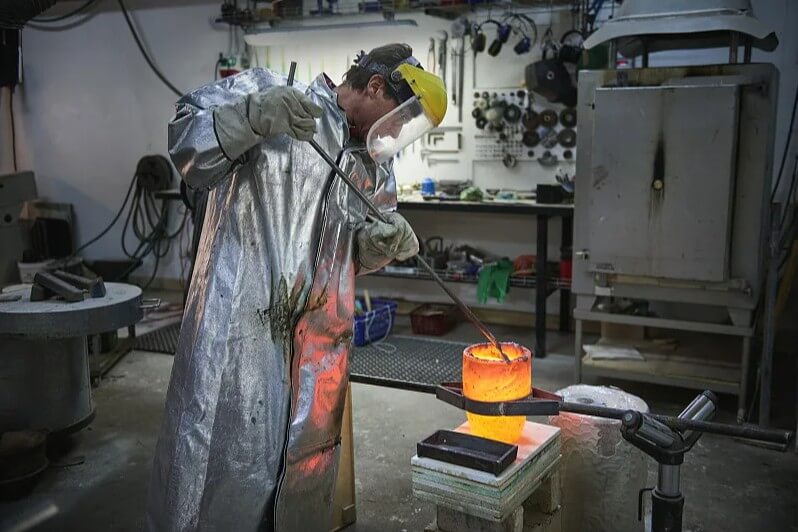
2) Shrinkage and deformation:
When the molten metal cools and solidifies, volume shrinkage may occur, resulting in inaccurate or deformed casting dimensions. To solve this problem, casting process parameters such as cooling rate and mold temperature can be optimized to reduce shrinkage. In addition, using high-precision molds and proper casting design can also help reduce deformation.
3) Surface roughness:
The surface of copper mold castings may not be smooth enough. The surface quality can be improved by improving the finish of the mold and using advanced casting techniques such as pressure casting or vacuum casting.
4) Hot cracking:
Due to thermal stress during cooling, cracks may appear in the casting. The solution is to control the cooling rate and add appropriate reinforcement ribs in the mold design or change the casting structure to reduce the tendency of hot cracking.
5) Mold life:
Copper molds work at high temperatures and are easily damaged, resulting in a shortened mold life. The mold life can be extended by selecting high-temperature resistant materials, regularly maintaining and servicing the mold, and optimizing the casting process parameters.
7.Summary
The copper mold casting process is widely used in industrial production due to its high efficiency and stable casting quality. By strictly controlling the process parameters of each link, high-quality alloy castings can be obtained to meet various application requirements.