Cold chamber die casting: the most complete process guide
As an important metal forming technology, cold chamber die casting has attracted much attention for its high efficiency, high precision and wide application. This article will deeply explore the working principle, technical elements, structure and type, process steps, process parameters, materials and application fields of cold chamber die casting. Finally, on this basis, we will discuss the advantages and challenges of cold chamber die casting technology. In addition, through the comparative analysis of the differences between cold chamber and hot chamber die casting, everyone can have a deeper understanding of these two technologies.
1.Basic principles and main technical elements of cold chamber die casting technology
(1) Basic principles
Cold chamber die casting technology is a metal casting process. Its basic principle is to pour molten metal liquid into an independent injection chamber, and then use the injection punch to push the metal liquid into the mold cavity at high speed, and cool and solidify it under high pressure to form a casting. This process involves precise pouring of molten metal, rapid movement of the injection punch and opening and closing of the mold, and finally obtains a casting with complete appearance and high strength.
(2) Main technical elements
1) High-pressure injection and rapid filling
Cold chamber die casting is centered on high-pressure injection and rapid filling processes. The molten metal fills the mold cavity at high speed under extremely high pressure to ensure the integrity and accuracy of the casting structure. This high-pressure and high-speed feature enables cold chamber die casting to produce castings with high dimensional accuracy and surface finish.
2) Cooling system design
The cooling and solidification process has a decisive influence on the quality of the casting. A reasonable cooling system design can effectively avoid casting defects such as shrinkage and pores. The design of the cooling system needs to take into account factors such as the heat conduction performance of the mold, the selection of cooling media, and the layout of the cooling channels.
3) Mold design and material selection
Mold design and material selection are extremely important in cold chamber die casting. The mold needs to withstand high pressure and high temperature, and the material should have high thermal stability and wear resistance. Commonly used mold materials include high-strength alloy steel and heat-resistant alloy steel. These materials can withstand repeated high temperature and high pressure to ensure the service life of the mold and the quality of the casting.
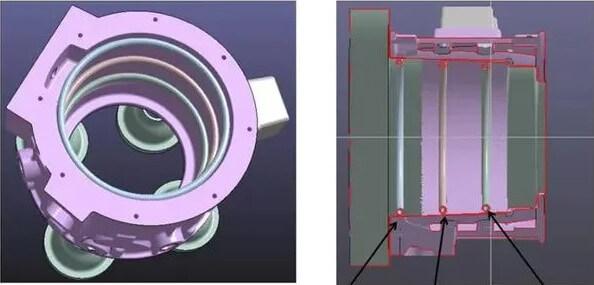
2.Structure and type of cold chamber die casting machine
(1) Structure
1) Clamping mechanism:
Responsible for the opening and closing and locking of the die, ensuring that the die is stably closed during the die casting process. This part usually includes the moving die plate, fixed die plate, pull rod, elbow mechanism, etc.
2) Injection mechanism:
Inject the molten metal into the mold cavity and pressurize it. It is mainly composed of injection punch, injection hydraulic cylinder, etc.
3) Hydraulic system:
Provide power source for the die casting machine and control the actions of clamping and injection. Contains hydraulic pump, oil tank, accumulator, various control valves, etc.
4) Electrical control system:
Controls the operation program and safety protection of the die casting machine. Including main electrical box, PLC controller, sensor, etc.
5) Auxiliary system:
Such as lubrication system, cooling system, safety protection device, etc., to ensure the normal operation and safe operation of the equipment
(2) Types
1) Vertical cold chamber die casting machine:
The injection method is placed vertically, suitable for the production of small and medium-sized castings, with the characteristics of simple structure and easy maintenance.
2) Horizontal cold chamber die casting machine:
The injection method is placed horizontally, with the advantages of high degree of automation and high production efficiency, and is widely used in the production of large and complex castings.
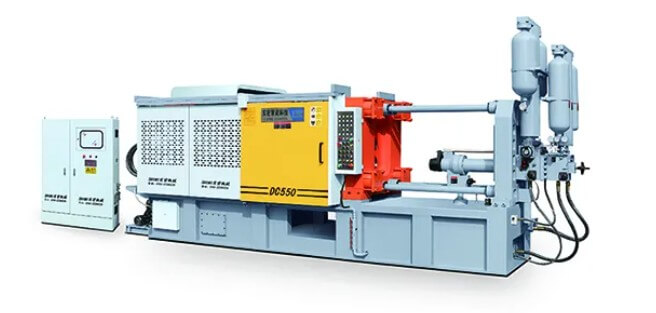
3.Analysis of the main steps of cold chamber die casting process
(1) Mold closing and metal pouring:
First, the mold of the die casting machine is closed, and then the liquid metal is injected into the pressure chamber of the die casting machine manually or automatically.
(2) Injection and filling:
The upper punch first contacts the metal liquid surface at a low speed, and then presses down at high speed to inject the metal liquid into the mold cavity through the gate system at high speed. In this process, the metal liquid quickly fills the mold cavity under high pressure to form the basic shape of the casting.
(3) Solidification and mold opening:
After the filling is completed, the punch maintains pressure to solidify the metal liquid under pressure. After solidification is completed, the upper punch is reset and the mold is opened. At this point, the casting and gate residues remain on the movable mold (moving mold part).
(4) Casting ejection and cleaning:
After the mold is opened, the casting is ejected from the mold by the ejection mechanism. After ejection, the mold cavity and gate system are cleaned to prepare for the next die-casting cycle. Then, the mold is closed and the next cycle begins.
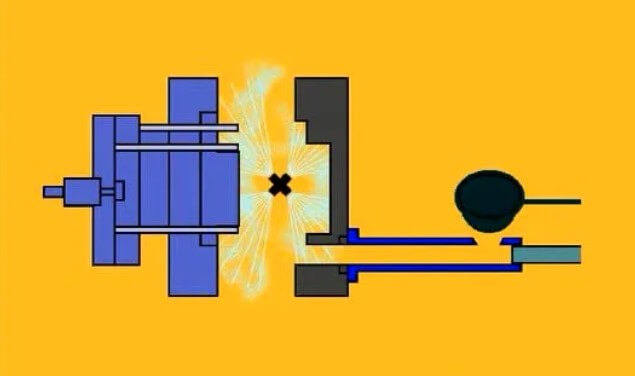
4.Key technical parameters of cold chamber die casting
(1) Pressure parameters
1) Specific pressure and boost specific pressure
In cold chamber die casting, specific pressure and boost specific pressure are key factors in determining the quality of castings. The selection of specific pressure is usually adjusted according to the material and structural complexity of the casting to ensure that the molten metal can completely fill every detail of the mold. The boost specific pressure is the additional pressure applied to the molten metal after filling is completed to help the molten metal better fill the fine structure before solidification.
2) Expansion force and clamping force
The calculation of expansion force and clamping force is also very important. They ensure that the mold will not open during high-pressure filling, thereby ensuring the dimensional accuracy and surface quality of the casting. The expansion force refers to the expansion force exerted by the molten metal on the mold cavity during the filling process, while the clamping force refers to the locking force applied by the die casting machine to the mold in order to overcome the expansion force.
(2) Speed parameters
1) Ingate speed and filling speed
The ingate speed and filling speed directly affect the quality and performance of the casting. Fast filling can reduce the cooling time of the molten metal and avoid the occurrence of cold shuts and defects. The ingate speed refers to the speed at which the molten metal enters the mold cavity through the ingate, while the filling speed refers to the speed at which the molten metal fills the entire cavity.
2) Injection speed
The injection speed is adjusted according to the wall thickness and structural complexity of the casting. Optimizing the injection speed can reduce defects such as pores and shrinkage. Too fast an injection speed may cause unstable filling of the molten metal, resulting in vortices and air entrainment, while too slow an injection speed may cause the molten metal to cool too quickly and fail to completely fill the cavity.
(3) Temperature control
1) Pouring temperature
Optimizing the pouring temperature is the key to ensuring casting quality and production efficiency. Too high a pouring temperature may cause oxidation and burning of the molten metal, while too low a pouring temperature may cause poor fluidity of the molten metal and inability to completely fill the cavity.
2) Mold working temperature
The mold working temperature affects the cooling rate of the molten metal and the solidification process of the casting. Temperature control not only affects the fluidity of the metal, but also affects the cooling rate and final physical properties of the casting. Reasonable temperature control can reduce the internal stress and deformation of the casting and improve the dimensional stability and mechanical properties of the casting.
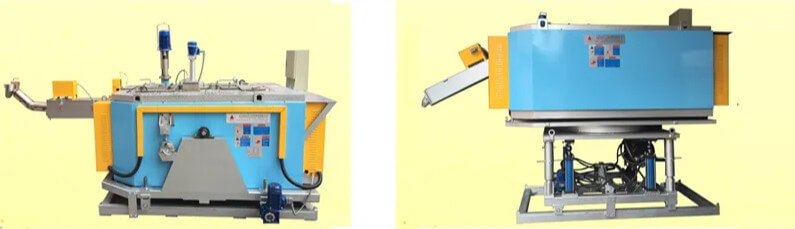
(4) Time factor
1) Filling time and holding time
Filling time and holding time are two important time parameters in cold chamber die casting. Filling time refers to the time required for the molten metal to fill the cavity completely from the beginning, while holding time refers to the time the molten metal maintains a high pressure state in the cavity. Reasonable filling time and holding time can ensure the density and dimensional accuracy of the casting.
2) Mold retention time
The control of mold retention time affects the final performance of the casting. Properly extending the mold retention time can help the casting fully cool and solidify, reducing the risk of deformation and cracks. Too long a mold retention time may cause the casting to stick to the mold, while too short a mold retention time may cause insufficient cooling of the casting, resulting in internal stress and deformation.
5.Analysis of common materials and application fields of cold chamber die casting technology
(1) Application in the automotive industry
Since cold chamber die casting can produce large castings with complex structures and precise dimensions, it is widely used in the production of key parts such as automotive engine parts, gearbox housings, and steering system parts.
Driven by the demand for lightweighting, cold chamber die castings of magnesium alloys and aluminum alloys are increasingly favored by automobile manufacturers. Magnesium alloys and aluminum alloys have the advantages of low density, high strength, and good rigidity, which can effectively reduce the weight of automobiles, reduce fuel consumption and emissions.
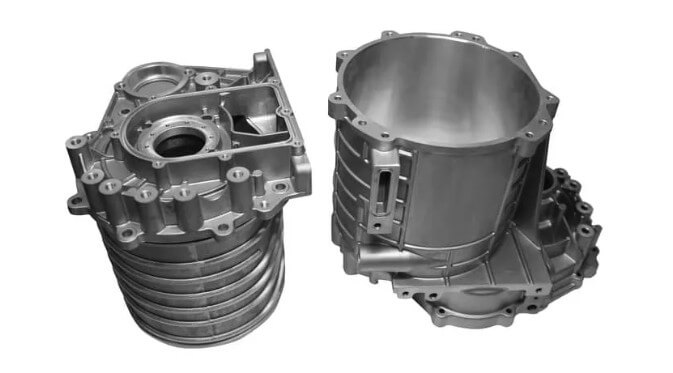
(2) Electronic product manufacturing
Cold chamber die casting technology is also widely used in the manufacturing of electronic products, especially 3C products with extremely high precision requirements (such as mobile phones, computers, and cameras). The outer shells and internal structural parts of these products usually require high-precision dimensions and complex geometric shapes.
Cold chamber die casting can produce precision parts with a thickness of only a few millimeters by precisely controlling the filling and cooling process of the molten metal. These parts have high dimensional accuracy and low surface roughness, which can meet the requirements of electronic products for lightweight and precision.
(3) Aerospace field
In the aerospace field, cold chamber die casting technology is used to produce high-strength, heat-resistant castings, such as aircraft engine parts and structural frames. These parts need to work in extreme temperature and high pressure environments, so the performance requirements of the materials are extremely high.
Special alloy materials such as titanium alloys and high-temperature alloys are also increasingly used in cold chamber die casting. These alloy materials have excellent mechanical properties and corrosion resistance, and can maintain stable performance in extreme environments. They are ideal material choices in the aerospace field. Through cold chamber die casting technology, these high-performance alloy materials can be made into complex parts for the manufacture of aircraft and spacecraft.
6.Advantages and challenges of cold chamber die casting technology
(1) Technical advantages
1) High production efficiency:
Due to its high pressure and high-speed filling characteristics, cold chamber die casting can produce a large number of high-quality castings in a short time to meet the needs of large-scale production. For example, the horizontal cold chamber die casting machine adopts pre-pressurization technology, which can greatly improve production efficiency and produce hundreds of castings per hour.
2) Strong adaptability:
It is suitable for a variety of metal alloys, such as aluminum, zinc, magnesium, copper, etc., and can produce large and medium-sized castings. The injection position of the horizontal cold chamber die casting machine is easy to adjust, adapting to eccentric gates and center gates, and flexibly meeting different process requirements.
3) High casting accuracy:
This technology can produce castings with dimensional accuracy, dense structure and smooth surface by accurately controlling the injection process, reducing the workload of subsequent processing.
4) High material utilization rate
By accurately controlling the filling and cooling process of the molten metal, cold chamber die casting can maximize the use of raw materials, reduce waste generation and reduce production costs.
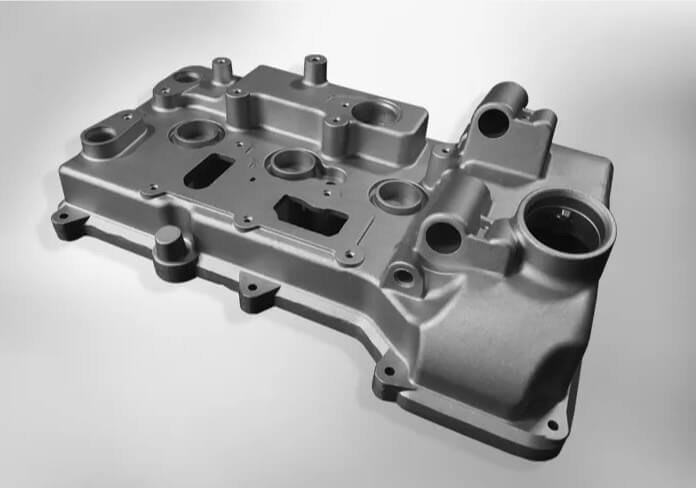
(2) Challenges
1) Equipment complexity and maintenance:
The structure of the cold chamber die casting machine is complex, especially the vertical die casting machine, which is inconvenient to operate and maintain. For example, the injection mechanism of the vertical die casting machine is at the bottom, which is inconvenient to replace the pressure chamber and repair work.
2) Production cost:
The initial investment of cold chamber die casting machines and their automation peripheral equipment is high, which is a considerable expense for small and medium-sized enterprises.
3) High process control requirements:
In order to ensure the quality of castings, it is necessary to accurately control parameters such as the temperature, injection speed and pressure of the molten metal. Any slight deviation in any parameter may lead to casting defects such as pores and inclusions.
4) Metal loss and environmental pollution:
During the die casting process, the molten metal is easily exposed to air and oxidized inclusions, resulting in increased metal loss. In addition, the waste and exhaust gas generated during the die casting process have a certain impact on the environment, and effective environmental protection measures need to be taken.
7.Comparative analysis of cold chamber die casting and hot chamber die casting
(1) Working principle and structure:
1) Cold chamber die casting machine:
Its injection chamber and injection punch are not immersed in the molten metal. During operation, a certain amount of molten metal needs to be taken out from the insulation furnace and poured into the injection chamber before injection. It is suitable for high-temperature alloys such as aluminum alloys and copper alloys.
2) Hot chamber die casting machine:
The injection chamber is immersed in the liquid metal of the insulated crucible, and the injection parts are installed above the crucible. Hot chamber die casting machines are mainly suitable for low melting point alloys such as zinc and magnesium alloys. Because their injection parts are immersed in the metal liquid for a long time, their service life is affected.
(2) Production efficiency and cost:
1) Cold chamber die casting machine
Since each die casting requires manual pouring, the production efficiency is lower than that of the hot chamber die casting machine, but it can process high temperature alloys and has a wider range of applications.
2) Hot chamber die casting machine
High degree of automation, simple production process, low metal consumption, stable process parameters, suitable for mass production.
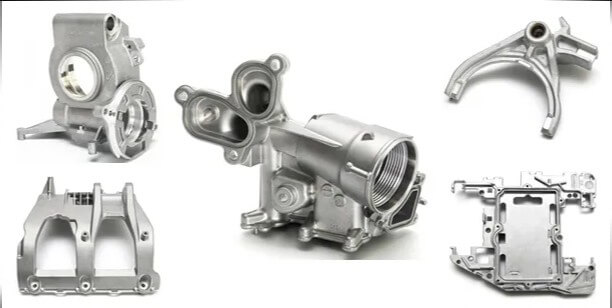
(3) Casting quality:
1) Cold chamber die casting machine
Air and oxide inclusions are easily involved in the injection process, which may affect the quality of the casting, but it can be improved through technical means.
2) Hot chamber die casting machine
Due to the long metal liquid flow and large pressure loss, the pressurization effect is not as obvious as that of the cold chamber die casting machine, but the metal liquid quality is higher and it is suitable for the production of thin-walled die castings.
8.Conclusion
As an advanced metal forming technology, cold chamber die casting technology will make greater breakthroughs in improving efficiency, reducing costs, improving quality and environmental protection performance in the future.
What do you think?
[…] Cold chamber die casting […]
Comments are closed.