Casting quality control: a necessary means to ensure excellent product performance
Casting quality control is a key step to ensure the quality of castings. Through reasonable quality control, product quality can be effectively improved and customer needs can be met. In actual operation, adjustments and optimizations should be made according to specific circumstances to achieve the best quality control effect.
This article will explore the significance of casting quality control and the specific aspects of quality control.
1.The significance of casting quality control
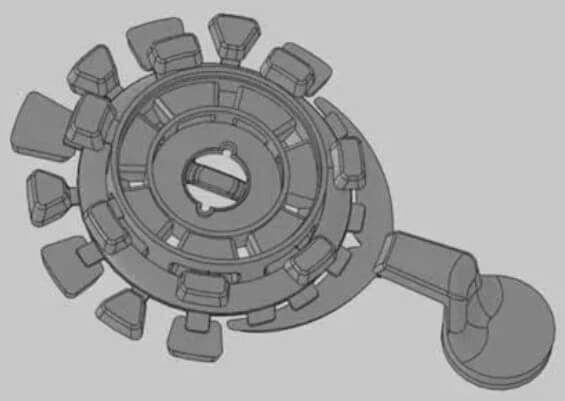
(1) Improving product performance and service life:
High-quality casting products can improve product service life and reliability, reduce failure rate, and thus improve customer satisfaction and loyalty.
(2) Ensuring production efficiency and reducing costs:
Effective casting quality control can reduce the generation of scrap and defective products, increase the first-time pass rate, and reduce production costs. At the same time, it reduces the number of rework and recasting, shortens the production cycle, improves production efficiency, and helps companies quickly respond to market demand.
(3) Enhance corporate competitiveness:
In the fierce market competition, high-quality casting products can win more market share and customer trust for companies. High-quality casting products can establish a good brand image for the company and enhance the company’s market position and competitiveness.
(4) Ensure production safety:
The casting process involves dangerous factors such as high temperature, noise, and dust. Effective quality management can ensure operational safety, reduce work-related accidents, and protect the personal safety of employees.
(5) Promote technological progress and innovation:
Casting quality control requires enterprises to continuously optimize production processes and introduce new technologies and equipment to improve the company’s technical level and innovation capabilities.
(6) Meet environmental protection requirements:
Casting quality control also includes the control of environmental pollutants generated during the casting process to ensure that the company complies with environmental protection regulations and achieves green casting.
(7) Maintain corporate reputation and customer relationships:
High-quality products help maintain the company’s reputation, establish long-term customer relationships, and promote the stable development of the company.
2.Aspects of casting quality control
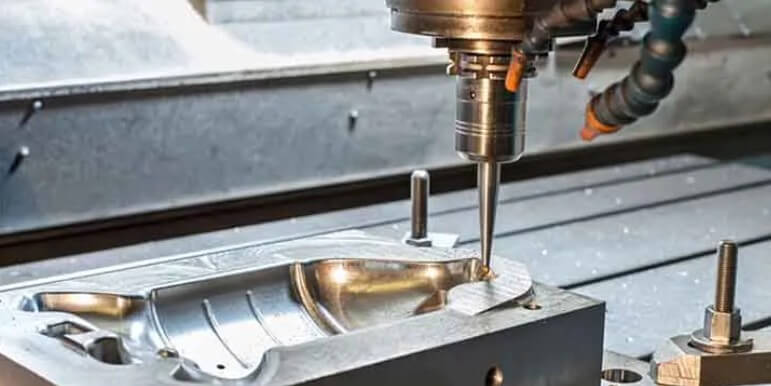
(1) Raw material control
Casting raw materials are the basis of casting product quality. High-quality materials that meet the requirements must be selected and strictly inspected for incoming goods. For example, raw materials such as metals, sand molds, and coatings used for casting must undergo chemical composition analysis and mechanical property tests to ensure that they meet design requirements. In addition, reasonable storage and use of raw materials to prevent materials from being contaminated or deteriorating are also key to ensuring casting quality.
(2) Process control
The casting process is an important factor affecting product quality. Process control includes formulating a reasonable casting process flow, controlling parameters such as pouring temperature and cooling speed. For example, key process parameters such as melting temperature, pouring speed, and cooling time need to be strictly controlled to ensure that each parameter meets the design requirements.
(3) Equipment control
Casting equipment is the key to realizing the casting process. Equipment control includes equipment selection, maintenance, and upkeep. For example, melting equipment, pouring equipment, sand processing equipment, etc. need to be regularly inspected and maintained to ensure their normal operation and avoid production problems caused by equipment failure. At the same time, necessary disinfection and cleaning of equipment to prevent cross contamination is also an important measure to ensure product quality.
(4) Environmental control
The casting environment is another aspect of casting quality control. Environmental control includes controlling parameters such as temperature, humidity, and cleanliness of the workshop. Keep the workshop clean and tidy, clean and disinfect it regularly, and avoid problems such as dust and oil pollution that affect the quality of castings. In addition, studying the impact of environmental conditions such as climate, humidity, and temperature on casting quality and taking corresponding measures in the process plan are also important means to improve casting quality.
(5) Inspection and control
Inspection is an important means of casting quality control. A strict inspection plan should be formulated, and the products should be inspected at the beginning, in the process and at the end. For example, the first casting of each batch should be strictly inspected to ensure that it meets the design requirements; inspection should be carried out after each process link to timely discover and solve potential problems; and final inspection should be carried out after production to ensure that all castings meet the quality requirements. Unqualified products should be reworked or scrapped in time to avoid affecting the overall quality.
(6) Continuous improvement
Continuous improvement is the key to ensuring the quality of casting products. By collecting and analyzing quality data, we can find out the existing problems and improvement points, and take corresponding measures to improve them. In addition, regular review and update of the casting quality control system to adapt to changes in market and customer needs is also an important way to improve product quality.
Summary:
In short, casting quality control is a necessary means to ensure the quality of the final product. By controlling raw materials, processes, equipment, environment, inspection and continuous improvement, the quality and performance of casting products can be effectively improved.
3.Specific measures for some important processes of casting quality control
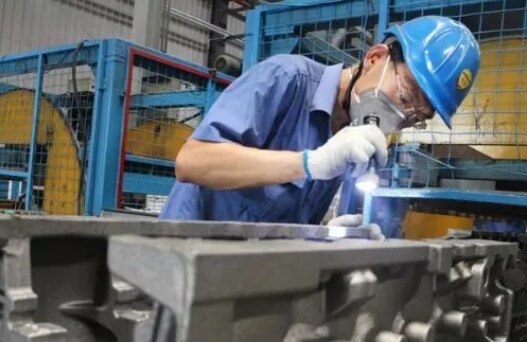
(1) Sand mixing/molding process
1) Key control points: composition, humidity, compactness, etc. of the molding sand.
2) Specific measures: formulate strict sand mixing and molding operating procedures, control the ratio and performance of the molding sand, and regularly test the water content and strength of the molding sand.
(2) Melting/pouring process
1) Key control points: chemical composition of the molten metal, pouring temperature and speed.
2) Specific measures: formulate a reasonable smelting process according to different casting requirements, control the chemical composition and temperature of the molten metal, ensure a smooth pouring process, and avoid defects such as pores and shrinkage holes.
(3) Cleaning process
1) Key control points: surface quality and dimensional accuracy of the casting.
2) Specific measures: select appropriate cleaning tools and methods to avoid damage to the casting, and conduct strict inspections on the cleaned castings to ensure that the surface finish and dimensional accuracy meet the requirements.
(4) Heat treatment process
1) Key control points: heat treatment process parameters.
2) Specific measures: According to the material and performance requirements of the casting, formulate a reasonable heat treatment process, control the heating temperature, holding time and cooling rate, and ensure that the casting achieves the required mechanical properties.
(5) Casting inspection process
1) Key control points: internal and surface defects of the casting.
2) Specific measures: Use advanced testing equipment and methods to conduct comprehensive inspections of castings, including dimensional inspections, surface inspections, non-destructive inspections, etc., to ensure that the castings meet quality standards.
(6) Connection and coordination between processes
1) Key control points: coordination and coordination between processes.
2) Specific measures: Establish a complete process conversion management system to ensure smooth connection between processes, avoid quality problems caused by improper coordination between processes, and implement effective casting quality control measures.
Summary:
Casting quality control is the core link in the product production process. Casting quality control is not only the inspection of the final product, but should run through the entire production process. Every step requires strict management and control.
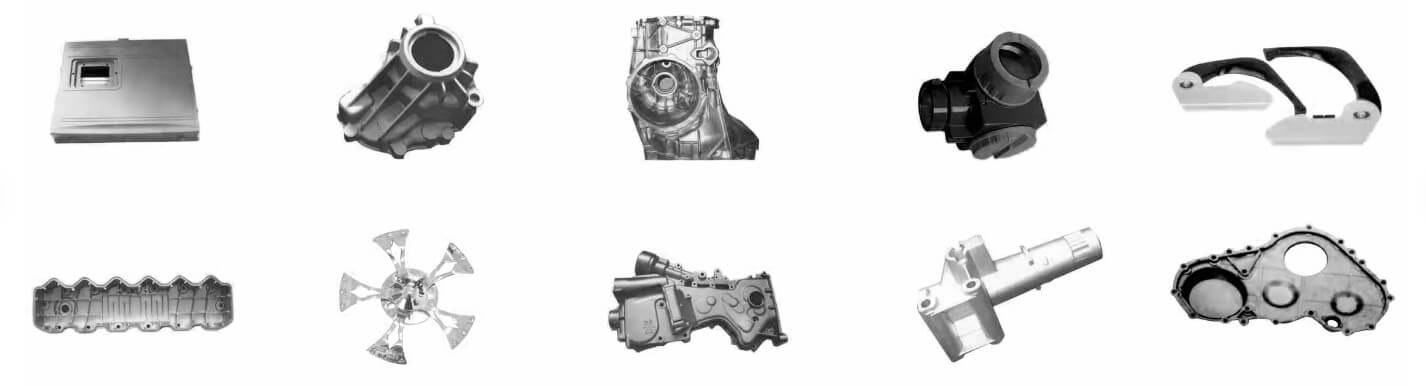
4.Summary
Casting quality control is a systematic project. It needs to start from every detail. Only through the whole process of casting quality control can high-quality castings be produced and be in a high position in the fierce competition of the casting market.