Casting Line Shrinkage: Understanding and Application
During the casting process, castings undergo a transition from liquid to solid, which is accompanied by a decrease in volume, the so-called shrinkage phenomenon.
Casting line shrinkage is an important parameter to describe this phenomenon, which directly affects the dimensional accuracy and final performance of castings. This article will discuss in detail the concept, influencing factors, control methods and solutions to common problems of casting line shrinkage.
1.What is casting line shrinkage?
Casting line shrinkage refers to the percentage of reduction in the size of each part of the casting during solidification and cooling. Specifically, it is the ratio of the shrinkage in the length direction to the original length when the casting is cooled from the linear shrinkage starting temperature to room temperature, usually expressed as a percentage. This parameter is crucial for controlling the dimensional accuracy and geometry of the casting.
2.Casting shrinkage process
The shrinkage process of castings can be divided into three stages: liquid shrinkage, solidification shrinkage and solid shrinkage. The shrinkage characteristics and influencing factors of each stage are different.
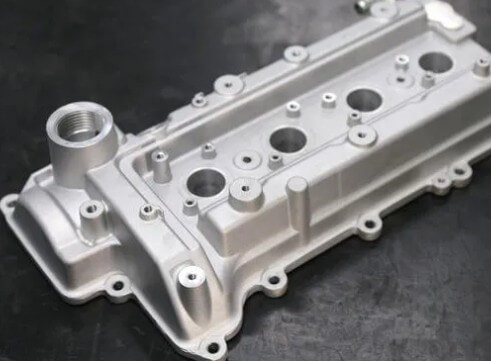
(1) Liquid shrinkage:
The reduction in alloy volume during cooling from the pouring temperature to the solidification start temperature. The shrinkage at this stage is mainly affected by the type of alloy and the pouring temperature.
(2) Solidification shrinkage:
From the beginning to the end of solidification, the volume of the alloy decreases due to phase change. The shrinkage at this stage is closely related to the solidification characteristics and solidification method (layer-by-layer solidification or volume solidification) of the alloy.
(3) Solid-state shrinkage:
After solidification, the volume of the casting decreases as it continues to cool to room temperature. The shrinkage at this stage mainly affects the final size and shape of the casting and is the main cause of casting stress, deformation and cracks.
3.Casting Line Shrinkage: Factors affecting its change
The Casting Line Shrinkage is affected by many factors, including alloy properties, pouring conditions, casting conditions and casting design.
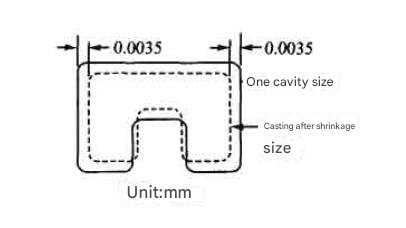
Dimensional changes of zinc alloy castings after shrinkage
(1) Alloy properties:
The linear shrinkage of different alloys varies significantly. For example, the linear shrinkage of gray cast iron is usually 0.7%-1.0%, while the linear shrinkage of cast carbon steel is 1.3%-2.0%. This is because the atomic structure and physical properties of different alloys are different, resulting in different shrinkage characteristics.
(2) Casting conditions:
Pouring temperature and pouring speed directly affect the cooling rate and solidification process of the casting, thereby affecting the shrinkage rate. Higher pouring temperatures will lead to greater liquid shrinkage, while slower pouring speeds are conducive to reducing shrinkage stress during solidification.
(3) Casting conditions:
Mold materials and preheating temperature will affect the cooling rate and solidification mode of the casting. For example, metal molds have a higher cooling rate than sand molds, resulting in a larger shrinkage rate. In addition, the permeability and yield of the mold will also affect the shrinkage behavior of the casting.
(4) Casting design:
The size, shape and structural complexity of the casting will affect the temperature gradient and stress distribution during its cooling process, thereby affecting the shrinkage rate. Complex structure castings are more prone to defects caused by uneven shrinkage due to uneven cooling, such as shrinkage cavities, shrinkage porosity and cracks.
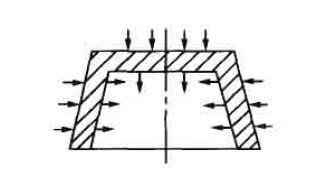
Shrinkage direction
4.Casting Line Shrinkage: Calculation and Measurement Method
The calculation of linear shrinkage is usually carried out by the following formula:
E=(L(mold)-L(casting))/L(casting)*100%
Wherein, E represents linear shrinkage, L(mold) is the size of the mold, and L(casting) is the size of the casting.
There are many methods to measure the Casting Line Shrinkage, including direct measurement and indirect measurement. The direct measurement method calculates the shrinkage by measuring the dimensional changes of the casting at different temperatures. Commonly used tools include vernier calipers, micrometers, etc. The indirect measurement method calculates the shrinkage by measuring the dimensional difference between the mold and the casting. In addition, high-precision dimensional measurement of castings can be performed through three-dimensional scanning technology to improve the accuracy and reliability of measurement.
5.Casting Line Shrinkage: Possible Control Methods
In order to reduce the adverse effects of Casting Line Shrinkage, the following control methods can be adopted:
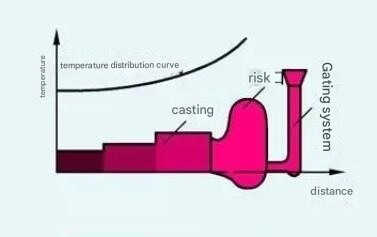
Use of risers
(1) Use of risers and chillers:
The reasonable setting of risers and chillers can adjust the solidification sequence and cooling rate of castings, thereby reducing the formation of shrinkage cavities and shrinkage. Riser is mainly used to supplement the volume shrinkage of castings during solidification, while chillers are used to accelerate local cooling and reduce heat nodes.
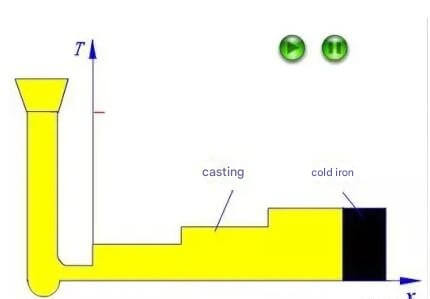
Use of chill iron
(2) Control of pouring temperature and speed:
Appropriately lowering the pouring temperature can reduce liquid shrinkage; while controlling the pouring speed can improve the filling and solidification process of castings and reduce shrinkage stress.
(3) Optimizing casting design:
Simplifying the casting structure, reducing thick and large sections and complex geometric shapes can reduce temperature gradients and stress concentration during cooling, thereby reducing shrinkage. In addition, reasonable setting of the wall thickness and transition radius of the casting can also reduce defects caused by uneven shrinkage.
(4) Use alloys with low shrinkage:
Choosing alloy materials with low shrinkage can fundamentally reduce the dimensional changes of castings. For example, gray cast iron with a high silicon content has a low shrinkage and is suitable for castings with high dimensional accuracy requirements.
6.Solutions to common problems
During the casting process, shrinkage, shrinkage and cracks are common problems related to the linear shrinkage of castings. Understanding the causes of these problems and taking corresponding countermeasures are the key to improving the quality of castings.
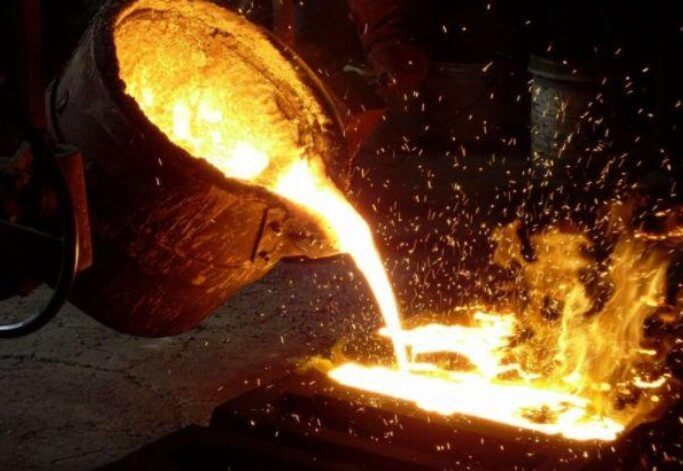
(1) Shrinkage and shrinkage:
This is mainly caused by the fact that the liquid shrinkage and solidification shrinkage of the alloy are greater than the solid shrinkage, and the last solidified part of the casting is not fully compensated for shrinkage. By reasonably setting the riser and chill, optimizing the pouring system and casting structure, the formation of shrinkage and shrinkage can be effectively reduced. In addition, the principle of sequential solidification is adopted to make the casting gradually solidify from the part away from the riser to the riser, which can also improve the shrinkage compensation effect.
(2) Cracks in castings:
During the cooling process, castings are prone to stress due to the restrained shrinkage. When the stress exceeds the strength limit of the alloy, cracks will form. By controlling the pouring temperature and cooling rate and reducing the temperature difference between the inside and outside of the casting, the shrinkage stress can be reduced. In addition, optimizing the casting design and reducing the stress concentration areas can also effectively prevent the occurrence of cracks.
7.Summary
Casting Line Shrinkage is a critical parameter in the casting process, which directly affects the dimensional accuracy and performance of the castings. By deeply understanding the factors affecting the linear shrinkage rate of castings and taking effective control measures, the quality and production efficiency of castings can be significantly improved. In actual production, it is necessary to comprehensively consider multiple factors to achieve the best control effect.