Casting and forging: How to distinguish, identify and choose
Casting and forging are two important metal processing processes, each with its own unique characteristics and scope of application. In actual production, the choice between casting and forging should be based on specific needs and conditions to achieve the best production results and economic benefits.
This article is a comprehensive guide to the fundamental differences between casting and forging. This article will help you thoroughly understand them. If you are looking for the right metal manufacturing process for your metal parts, then I believe this article will give you the answer. First, we will introduce the definitions, common methods, advantages, disadvantages and application fields of casting and forging respectively. Then, we will distinguish the specific differences between casting and forging through detailed introductions of various aspects.
1.Casting
(1) Definition
Casting is a metal hot working process that pours molten metal into a casting mold cavity that is adapted to the shape of the part and waits for it to cool and solidify to obtain a part or blank. This process has a history of about 7,000 years and is one of the important metal processing technologies in ancient China.
However, the mold is a dedicated chamber composed of different gating systems and cavities. This cavity ultimately creates different metal shapes. Depending on the type of casting method, the mold can be permanent or temporary.
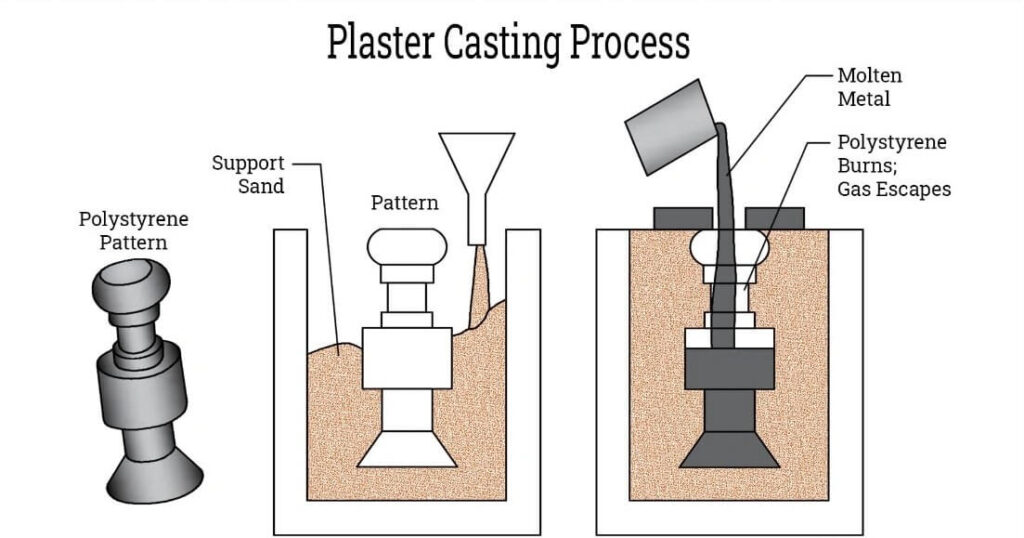
(2) Common casting methods
1) Sand casting:
Using sand as the main molding material, molten metal is injected into the mold by gravity. It is suitable for castings of various sizes and complex shapes, but the dimensional accuracy and surface quality are relatively low.
2) Investment casting:
Also known as lost wax casting, it uses fusible materials to make a pattern, and the surface is coated with refractory materials to make a shell. After the pattern is melted and discharged, it forms a casting. It is suitable for the production of small parts with complex shapes and high precision requirements.
3) Pressure casting:
Using high pressure to press molten metal into the metal mold cavity at high speed, and then cool and solidify to form a casting. It is suitable for mass production, the casting size is stable, and the interchangeability is good, but it is easy to produce pores and shrinkage.
4) Low-pressure casting:
The liquid metal is filled into the mold under low pressure, and crystallized under pressure to form a casting. It is suitable for various castings, and the casting has a dense structure, clear contours, and a smooth surface.
5) Centrifugal casting:
Pour the molten metal into a rotating mold, fill the mold and solidify under the action of centrifugal force. It is suitable for producing hollow castings and improving the process yield, but the quality of the inner hole of the casting is poor.
6) Metal mold casting:
The liquid metal fills the metal mold under the action of gravity and cools and solidifies in the mold. The casting has high dimensional accuracy and smooth surface, but the metal mold manufacturing cycle is long and the cost is high.
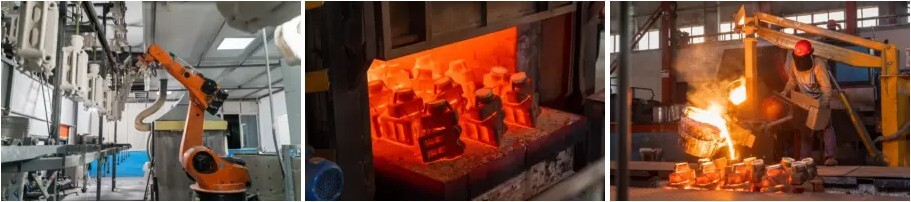
(3) Advantages
1) Shape complexity:
It is possible to produce rough workpieces with complex shapes, especially parts with complex inner cavities.
2) Material adaptability:
All metal materials commonly used in industry can be used for casting, and the quality of castings can range from a few grams to hundreds of tons.
3) Cost-effectiveness:
The raw materials are widely available and inexpensive, and old machine parts can be directly used, so the cost of castings is relatively low.
4) Reduced processing:
The casting roughcast has high quality finish because it is almost formed, which can reduce mechanical processing or a small amount of processing, reduce costs and shorten production time.
(4) Disadvantages
1) Mechanical properties:
The casting structure is loose, the grains are coarse, and it is easy to produce shrinkage holes, shrinkage, pores and other defects inside, resulting in low mechanical properties of the casting, especially the impact toughness.
2) Quality stability:
The quality of the casting is not stable enough, there are many processes, the influencing factors are complex, and defects are easy to occur.
(5) Application
1) Mechanical manufacturing:
In various machinery and equipment, the quality of castings accounts for a large proportion. For example, in tractors and other agricultural machinery, the proportion of casting quality is as high as 40% to 70%; in metal cutting machine tools and internal combustion engines, it is as high as 70% to 80%; in heavy machinery and equipment, it can be as high as 90%.
2) Automobile industry:
Castings such as automobile engine cylinder blocks, cylinder heads, crankshafts, etc. are usually produced by sand casting or pressure casting.
3) Aerospace:
Due to its high precision and surface quality, investment casting is suitable for the production of small parts with complex shapes and high precision requirements, such as turbine engine blades.
4) Electronics industry:
Die castings are widely used in the electronics industry due to their dimensional stability and good interchangeability, such as computer housings, connectors, etc.
5) Shipbuilding industry:
In the field of shipbuilding, castings have also been widely used. Castings have appeared on many large ships, such as propellers, anchors, etc., which are large castings that are corrosion-resistant and durable.
6) Medical equipment:
There are many stainless steel parts with extremely complex shapes on medical devices, and these complex shapes and high surface accuracy requirements can only be achieved through casting technology. For example, some surgical instruments, implants, etc.
2.Forging
(1) Definition
Forging is a processing method that uses a forging machine to apply pressure to a metal blank to cause it to undergo plastic deformation to obtain a forging with certain mechanical properties, a certain shape and size. The main principle of forging is to use external force to cause the metal blank to undergo plastic flow at high or normal temperature, thereby changing its shape and size, while improving its internal structure and improving its mechanical properties.
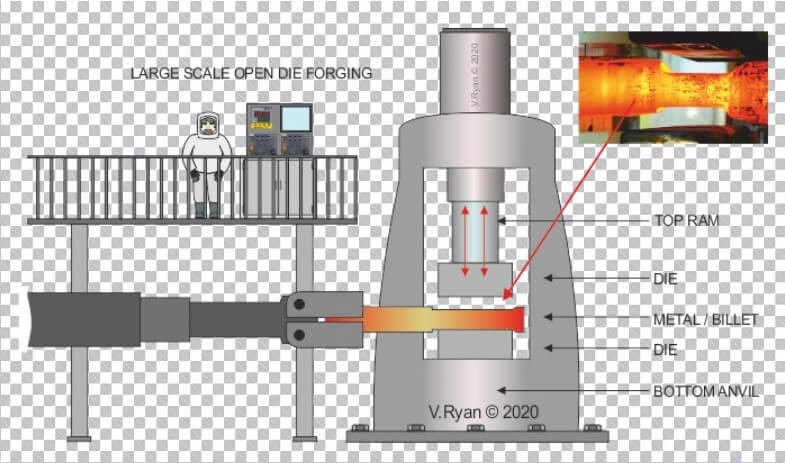
(2) Classification of forging methods
Forging is a metal processing method that improves the mechanical properties of metal materials and forms the desired shape through plastic deformation. According to the temperature of the metal during processing, forging can be divided into two categories: hot forging and cold forging.
1) Hot forging:
A forging process performed at a temperature higher than the recrystallization temperature of the metal. For steel, temperatures above 800°C are generally considered to be the temperature range for hot forging.
Advantages: The plasticity of metal increases at high temperatures, the deformation resistance decreases, and it is easy to form complex shapes. At the same time, it can refine the grains, optimize the internal structure, and improve the mechanical properties.
Application: Suitable for large and complex forgings, as well as materials that can only be effectively deformed at high temperatures, such as stainless steel and high-temperature alloys.
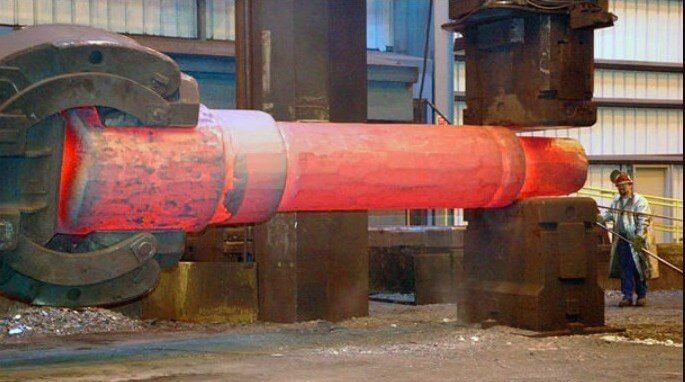
2) Cold forging:
A forging process performed at room temperature or near room temperature.
Advantages: The metal surface quality after cold forging is good and the dimensional accuracy is high. It can replace some cutting processes. At the same time, cold forging can strengthen the metal and improve the strength of parts.
Application: Suitable for small forgings with high precision requirements, as well as materials with good plasticity in the cold state, such as aluminum, copper and its alloys, and some low-carbon steel and medium-carbon steel.
(3) Advantages:
1) Improve metal structure:
Forging can eliminate the as-cast looseness of the metal, weld holes, optimize the microstructure, and improve the mechanical properties of forgings.
2) Improve material properties:
Forgings have high density, good strength and toughness, and good wear resistance and corrosion resistance.
3) High dimensional accuracy:
Forging can make the shape, size and surface quality of metal materials precisely controlled.
4) Wide application:
Forging is suitable for the production of workpieces of various shapes and sizes, and can produce larger and more complex parts.
(4) Disadvantages:
Although forging has a wide range of advantages, it also has some disadvantages. Due to these disadvantages, people choose casting. The following are the four main reasons why people choose casting and forging.
1) Shape restriction:
This is the main reason why people choose casting instead of forging. Metal forging is not suitable for manufacturing complex shapes. It can produce relatively simpler shapes than metal casting. Therefore, it cannot meet the requirements of many applications.
2) High requirements for raw materials:
Forging has high requirements for raw materials and is more difficult to process more brittle metal materials.
3) Low production efficiency:
Free forging has much lower production efficiency than model forging, and the forgings have simple shapes, low dimensional accuracy, and rough surfaces.
4) Additional operations:
Forging may require additional processing to achieve better results. Compared with other metal manufacturing processes, forging requires more additional machining.
(5) Applications:
1) Automobile manufacturing:
Automobile clutch engagement gear ring, automobile transmission input shaft parts, bearing rings, automobile constant velocity joint sleeve series products, automobile differential gears, automobile front axles, etc.
2) Machinery manufacturing:
Important parts with high loads and severe working conditions, such as steam turbine generator shafts, rotors, impellers, blades, rollers, internal combustion engine crankshafts, connecting rods, gears, bearings, etc.
3) Aerospace Industry:
Forgings are used in many parts of aircraft, such as engines and landing gear, as well as medium to large parts in other parts. Because forgings have excellent impact resistance.
4) Energy Industry:
In oil and gas production and power generation, forged parts are used for high-pressure valves, turbines and generators that require excellent performance and resistance to harsh environments.
5) Heavy Machinery and Construction:
Forgings are characterized by durability and load-bearing capacity, such as mining equipment and lifting equipment widely used in the construction industry. In harsh working environments, the wear resistance and weighing capacity of forgings are well demonstrated.
3.The main difference between casting and forging
Casting and forging are two different metal processing methods that differ in process, applicable materials, precision and surface quality, and cost.
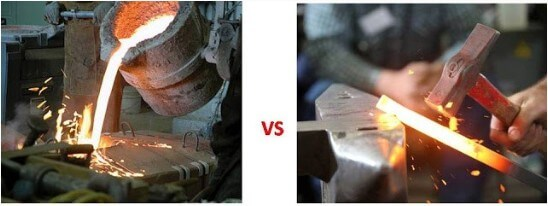
(1) Process:
Casting: The metal is melted and poured into a mold, cooled and solidified to form the desired shape.
Forging: The metal is heated to a plastic state and its shape is changed by striking or extruding.
(2) Applicable materials:
Casting: Applicable to metals with high melting points and difficult processing, such as iron, steel, copper, etc.
Forging: Applicable to metals with high strength and high toughness, such as steel, aluminum, titanium, etc.
(3) Precision and surface quality:
Casting: High shape complexity, suitable for manufacturing large castings, but poor surface quality and precision.
Forging: High precision and surface quality, but high shape complexity and size requirements.
(4) Cost:
Casting: Suitable for mass production, low cost.
Forging: High energy and process costs, suitable for small batch production.
Through these differences, you can choose which of casting and forging is the most suitable process according to the characteristics and requirements of the required products.
content | Metal Forging | Metal Casting |
definition | It is a metal fabrication process that uses combined forces to create metal shapes. | It is a metal fabrication process that involves pouring molten metal into molds to form different metal shapes. |
Compressive strength | Forged products have high compressive strength | Cast products have low compressive strength. |
Fatigue strength | Metal forging products have high fatigue strength. | Casting products have low fatigue strength. |
Shape and size | Metal forging has limitations in creating complex metal shapes. | Different casting methods can produce various types of metal shapes. |
tolerance | Metal forging products generally have lower tolerances | Cast products with high tolerances |
Need labor | Metal forging is more labor intensive than casting. | Metal casting requires less labor than metal forging. |
4.How to distinguish between cast and forged parts?
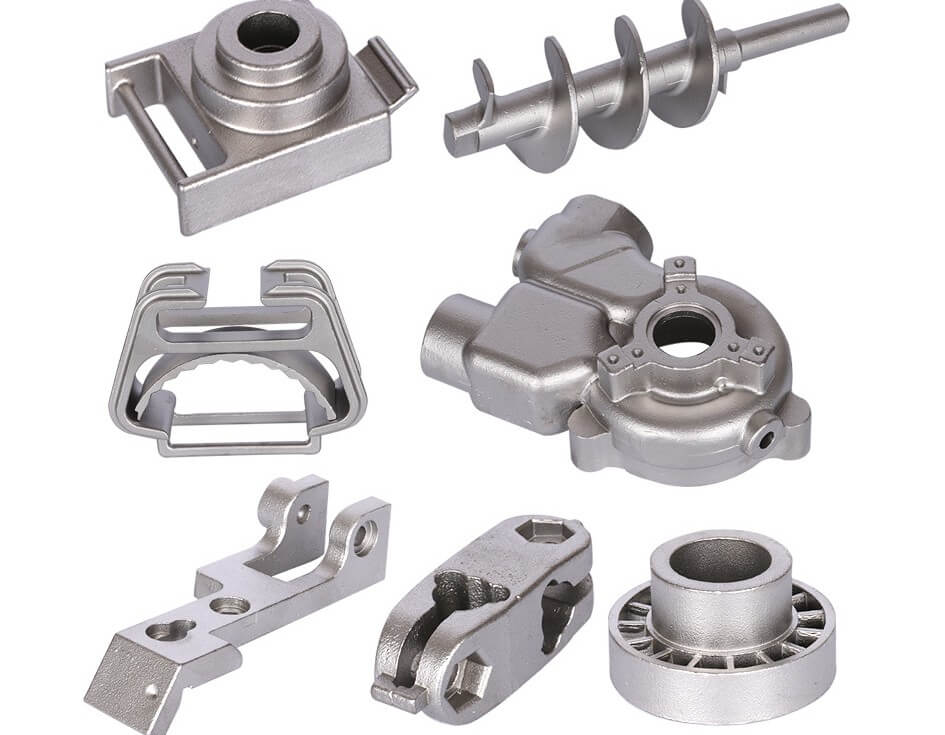
(1) Surface brightness
The surface of the casting should be thicker, and the surface of the forging should be brighter.
(2) Color
The cast iron part is gray and dark, while the forged steel part is silver and bright.
(3) Sound
Listen to the sound, the forged is dense, the sound is crisp after knocking, and the casting sound is dull.
(4) Grinding
Use a grinder to grind and see if the sparks are different (generally forgings are brighter), etc.
5.The relationship between machining, casting and forging
Machining, casting and forging are three different processes in the field of metal processing. They each have their own characteristics and advantages, and in practical applications they often complement each other to complete the manufacturing process of complex parts. This can be reflected in the following aspects;
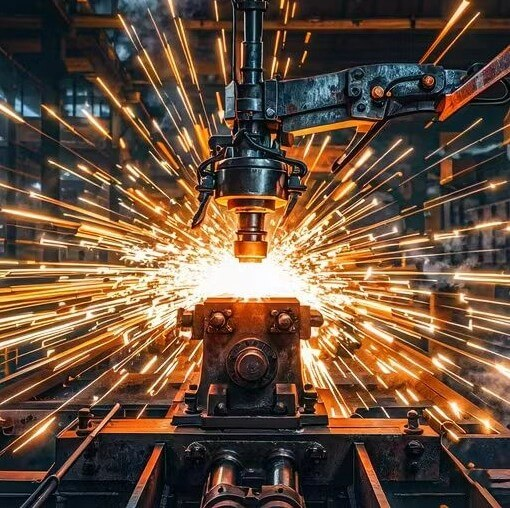
(1) Shape and size adaptability:
Casting is suitable for making parts with complex shapes and large sizes, such as boxes and cylinders.
Forging is suitable for making parts with small sizes and relatively simple shapes, such as shafts and gears.
Machining is suitable for further size and shape refinement of castings or forgings.
(2) Mechanical properties:
The mechanical properties of castings are generally poor, especially for parts that bear high loads.
Forging can improve the internal structure of the metal and improve its mechanical properties and toughness.
Machining can improve the precision and surface quality of parts by removing materials.
(3) Cost considerations:
The production cost of casting is relatively low and is suitable for mass production.
The production cost of forging is higher, but it can provide higher material utilization and performance.
The cost of machining depends on the complexity and precision requirements of the processing.
(4) Manufacturing process
In actual production, machining, casting and forging often cooperate and complement each other. Casting and forging provide blanks or semi-finished products, and machining processes these blanks to meet the design requirements of the final product. The three together constitute an important part of the metal processing field and are widely used in many industries such as automobiles, aerospace, and machinery manufacturing.
6.Summary
In summary, casting and forging are both industrial processes for metal forming and shaping. Different processes are used under different conditions. The main difference between casting and forging is that casting is to pour molten metal into a mold and cool it to shape it. It is suitable for complex-shaped parts and has a lower cost, but the surface is rough and the strength is poor. Forging is to apply pressure to solid metal to plastically deform it. It has a simple shape, but excellent mechanical properties, smooth surface, and high cost. The specific choice between casting and forging should be determined according to the actual processing needs and processing conditions.