Casting aluminum: Lightweight and high strength industrial choice
The casting aluminum process is a technology that uses aluminum or aluminum alloy materials to make parts of specific shapes through casting methods. It is widely used in the fields of automobiles, aerospace, machinery manufacturing, etc. This article will explore the advantages, process methods, process flow, process key points, material analysis and application fields of casting aluminum in depth.
1.Definition
Casting aluminum is a process method that prepares pure aluminum or aluminum alloy ingots according to standard composition ratios, artificially heats them into aluminum alloy liquid or molten state, and then pours the aluminum liquid or molten aluminum alloy into the mold cavity through professional molds or corresponding processes, and cools them to form aluminum parts of the desired shape.
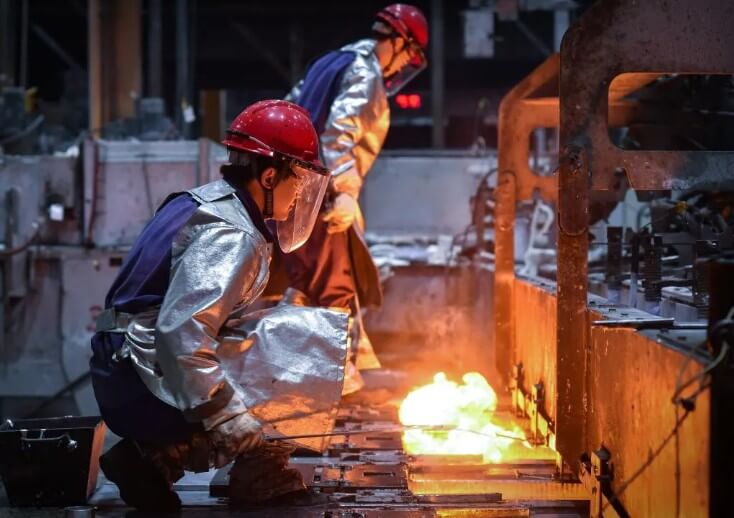
2.Advantages of casting aluminum
Casting aluminum has many advantages, which have made it widely used in many industries. The following are some of the main advantages:
(1) Good product quality:
Casting aluminum parts have high dimensional accuracy and good surface finish, generally equivalent to grade 5 to 8, high strength and hardness, stable dimensions, and good interchangeability.
(2) High production efficiency:
The machine has high productivity and is easy to achieve mechanization and automation. The die casting aluminum mold has a long life, which can reach hundreds of thousands or even millions of times.
(3) Excellent economic effect:
Due to the advantages of die casting aluminum parts such as precise size and smooth surface, they are generally used directly without mechanical processing, or the processing volume is very small, which improves metal utilization and reduces processing equipment and working hours.
(4) Low density and high specific strength:
The density of casting aluminum alloy is lower than that of cast iron and cast steel, but the specific strength is higher. Therefore, under the same load conditions, the use of aluminum alloy castings can reduce the weight of the structure and is suitable for the aviation industry and power machinery and transportation machinery manufacturing.
(5) Good corrosion resistance:
Aluminum alloy has good corrosion resistance, especially in the atmosphere and fresh water, as well as in oxidizing acid media such as nitric acid and acetic acid, so it is also used in the chemical industry.
(6) Good thermal conductivity:
Aluminum alloy has good thermal conductivity and is suitable for manufacturing heat exchange devices used in chemical production, as well as parts in power machinery that require good thermal conductivity.
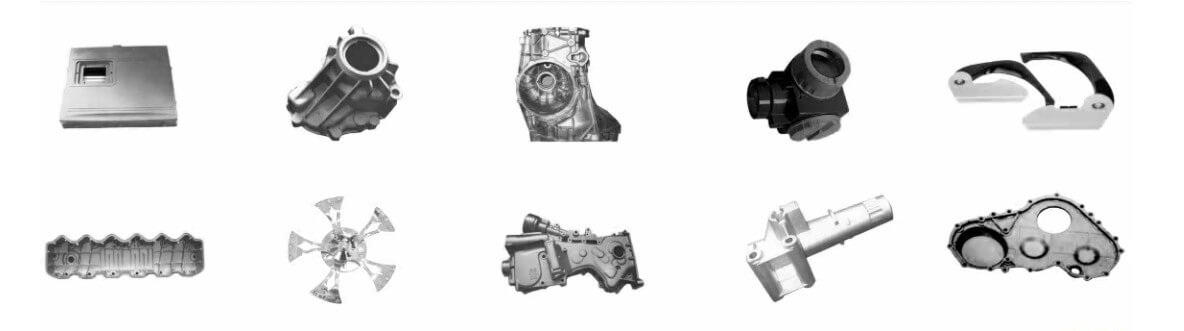
3.Main process methods of casting aluminum
Depending on different production requirements and casting characteristics, casting aluminum can adopt a variety of methods. The following are several main process methods:
(1) Sand casting:
1) Principle:
Pour the molten aluminum into a mold made of sand, and wait for it to cool and solidify to obtain a casting.
2) Features:
The process is simple and low-cost, suitable for the production of large and medium-sized castings. However, the casting accuracy and surface quality are relatively low.
(2) Metal mold casting:
1) Principle:
Casting is performed using a metal mold (usually cast iron or steel). The aluminum liquid is injected into the preheated metal mold under the action of gravity.
2) Features:
The metal mold can be reused, the casting size accuracy and surface quality are high, and the production efficiency is also high. It is suitable for mass production of small and medium-sized castings.
(3) Pressure casting:
1) Principle:
The molten aluminum is pressed into the mold under high pressure, and quickly cooled and solidified to form a casting.
2) Features:
High production efficiency, excellent casting dimensional accuracy and surface quality. However, the cost of equipment and molds is high, and defects such as pores and shrinkage holes are easily generated.
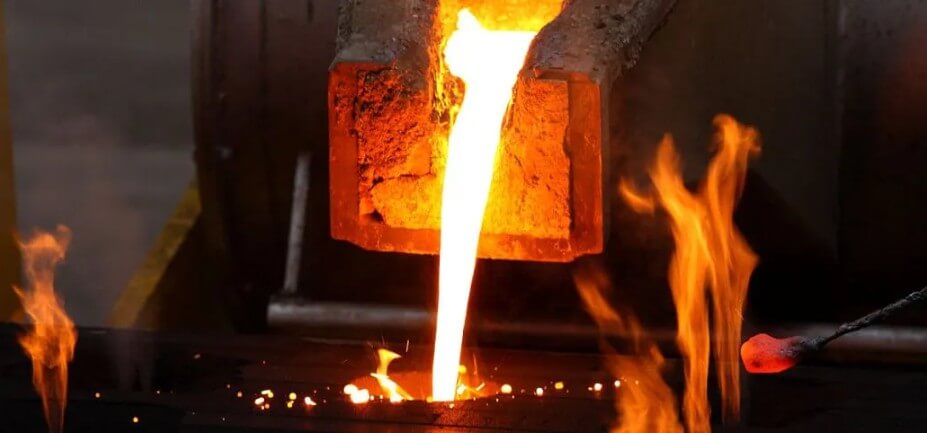
(4) Low pressure casting:
1) Principle:
Aluminum is pressed into the mold under low pressure (usually 0.02-0.07MPa), and then the pressure is slowly increased to solidify the aluminum liquid under pressure.
2) Features:
Compared with pressure casting, the cost of equipment and molds for low-pressure casting is lower, and the internal quality of the casting is better. It is suitable for the production of large thin-walled castings.
(5) Centrifugal casting:
1) Principle:
The molten aluminum liquid is injected into a high-speed rotating mold, and the centrifugal force is used to evenly distribute the aluminum liquid on the inner wall of the mold. After cooling and solidification, the casting is formed.
2) Features:
Suitable for the production of hollow rotating castings, such as pipe fittings, wheels, etc. The casting has a dense structure and is free of defects such as pores and shrinkage holes.
(6) Investment casting:
1) Principle:
Casting is performed using wax molds and ceramic shells. First, a wax mold is made, and then multiple layers of refractory material are coated on its surface to form a ceramic shell. The wax mold is heated to melt and flow out, and then aluminum liquid is injected for casting.
2) Features:
The dimensional accuracy and surface quality of the casting are extremely high, which can reach a level close to that of mechanical processing. However, the process is complex and the cost is high. It is suitable for producing castings with complex shapes and high precision requirements.
Summary:
Each casting aluminum process has its own unique advantages and limitations. The selection of a suitable process method requires comprehensive consideration of factors such as the size, shape, precision requirements and production cost of the casting.
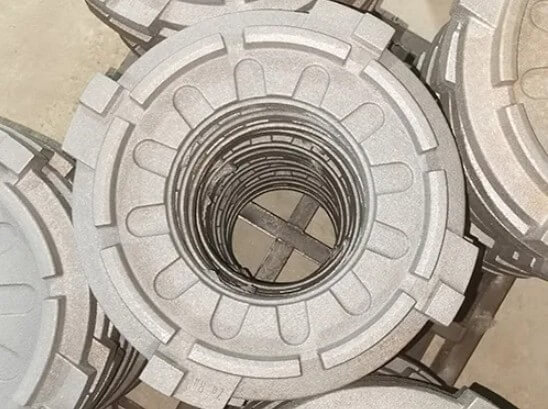
4.Main process flow of casting aluminum.
Casting aluminum is a common metal processing process. The process mainly includes three main stages: smelting, casting and post-processing. The following will introduce these three process flows in detail:
(1) Smelting process
Smelting is the first step in casting aluminum. The purpose is to heat aluminum or aluminum alloy to a molten state for subsequent casting operations. The specific steps are as follows:
1) Batching:
According to the grade of aluminum castings to be produced, calculate and match the proportions of various alloy components. Common alloy components include silicon, copper, magnesium, etc.
2) Melting:
Put the prepared raw materials into a melting furnace and heat them to a molten state. The melting furnace can be a resistance furnace, an induction furnace or a gas furnace, etc.
3) Refining:
In the molten state, the aluminum liquid needs to be refined to remove impurities and gases. Commonly used refining agents include hexachloroethane and DSG aluminum alloy slag degassing agent, etc.
4) Adjusting the composition:
After refining, it may be necessary to adjust the alloy composition in the aluminum liquid according to the actual situation to ensure that the performance of the final product meets the requirements.
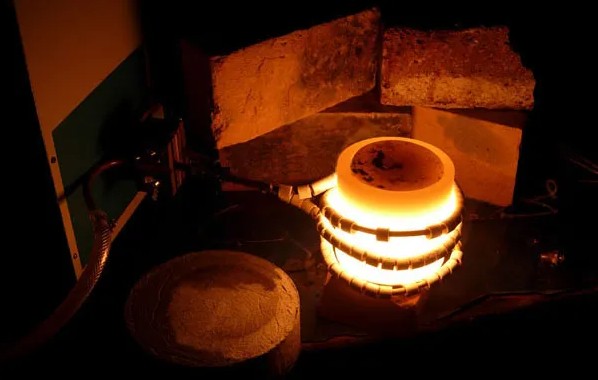
(2) Casting process
Casting is to pour the molten aluminum liquid into a pre-designed mold and form a casting of the desired shape after cooling and solidification. The specific steps are as follows:
1) Mold design:
Design the mold according to the structural characteristics, wall thickness, shrinkage rate and other factors of the casting. The design of the mold has an important influence on the quality and shape of the final casting.
2) Pouring:
Pour the molten aluminum into the preheated mold. The pouring speed, temperature and pressure need to be controlled during the pouring process to avoid defects such as pores and inclusions.
3) Cooling and solidification:
The aluminum liquid cools and solidifies in the mold to form the desired casting shape. The cooling rate has an important influence on the structure and performance of the casting.
4) Demolding:
After the casting is cooled and solidified, it is removed from the mold.
(3) Post-processing process
Post-processing is to further treat the finished casting to improve its performance and quality. The specific steps are as follows:
1) Deburring:
After casting, there are usually some burrs and oxide scales on the surface of the casting, which need to be removed by mechanical methods to improve the surface quality.
2) Heat treatment:
Casting Aluminum usually need to be heat treated to eliminate residual stress, improve the structure and increase the hardness. Common heat treatment processes include aging treatment, solution treatment and quenching treatment.
3) Surface treatment:
In order to improve the corrosion resistance and decorative properties of aluminum castings, surface treatment is also required. Common surface treatment processes include anodizing, spraying, electroplating, etc.
4) Inspection:
Quality inspection of the treated casting aluminum is carried out to ensure that they meet the relevant standards and performance requirements.
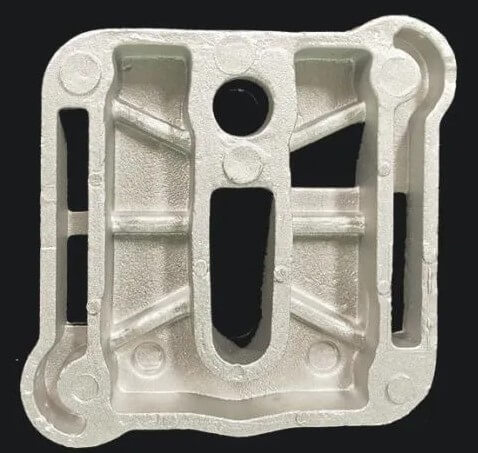
5.Key process points of casting aluminum.
(1) Importance of temperature control:
Temperature control is a key factor in the casting aluminum process because it directly affects the fluidity of the aluminum liquid, the solidification process and the performance of the final casting. If the temperature is too high, the aluminum liquid will oxidize more, forming oxide inclusions and affecting the quality of the casting; if the temperature is too low, the fluidity of the aluminum liquid will deteriorate, and defects such as cold shut and insufficient pouring will easily occur.
In actual production, it is necessary to determine the appropriate pouring temperature according to different aluminum alloy materials and casting structures, and take effective insulation measures to reduce temperature fluctuations and ensure that the temperature of the aluminum liquid is stable during the pouring process.
(2) Mold design and manufacturing:
Mold design and manufacturing is the core link of casting aluminum process. The design of mold is directly related to the dimensional accuracy and surface quality of castings. The selection of mold materials, the rationality of structure, the design of cooling system and the setting of exhaust system will affect the molding effect of castings.
During the mold manufacturing process, it is necessary to ensure the dimensional accuracy and surface roughness of the mold to meet the quality requirements of castings. At the same time, the strength and toughness of the mold must be sufficient to ensure that it will not deform or damage under high temperature and high pressure.
(3) Selection and ratio of alloy components:
The selection and ratio of alloy components determine the mechanical properties and physical properties of aluminum castings. Different applications require different aluminum alloy materials. For example, Al-Si alloys have good casting properties and thermal cracking resistance, which are suitable for making castings with complex shapes; while Al-Cu alloys have good strength and hardness, which are suitable for making castings that bear large loads.
When selecting alloy components, factors such as alloy fluidity, shrinkage, thermal cracking tendency, etc. need to be considered to ensure the quality and production efficiency of castings. At the same time, the alloy ratio must also be precisely controlled to ensure the stable performance of castings.
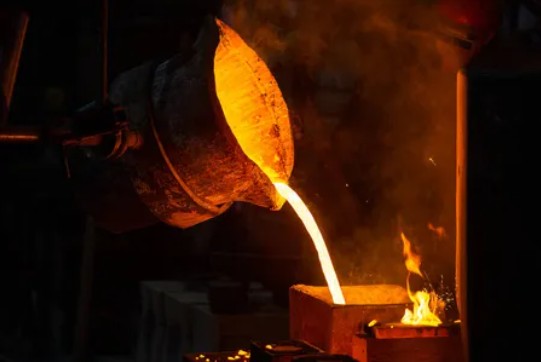
Summary:
In summary, temperature control, mold design and manufacturing, and the selection and ratio of alloy components are the three key points in the casting aluminum process. They influence each other and jointly determine the final quality and performance of the casting. In actual production, it is necessary to comprehensively consider these factors and improve the quality and production efficiency of aluminum castings by optimizing process parameters and strictly controlling the production process.
6.Aluminum casting materials: tradition and innovation
As an important industrial material, aluminum materials are widely used in automobiles, aviation, instrumentation and other fields due to their light weight, high strength and good corrosion resistance. The development of casting aluminum materials has undergone an evolution from traditional to modern, and continues to meet the growing performance requirements.
(1) Traditional casting aluminum materials
1) Aluminum silicon alloy (ZL104, etc.):
This type of alloy has excellent casting properties and low cost, and is suitable for the production of complex parts such as cylinder blocks, water pump housings, etc. Its main components include aluminum and silicon, and sometimes a small amount of magnesium and copper are added to improve mechanical properties.
2) Aluminum-copper alloy (ZL201, etc.):
Based on aluminum, copper and other elements (such as manganese and nickel) are added. It is suitable for parts that require high heat resistance, such as internal combustion engine cylinder heads and pistons. Aluminum-copper alloys show good performance in high temperature environments.
3) Aluminum-magnesium alloy (ZL301, etc.):
Aluminum-magnesium alloys have excellent corrosion resistance and high strength, and are suitable for components working in the atmosphere or seawater, such as pump bodies and ship accessories.
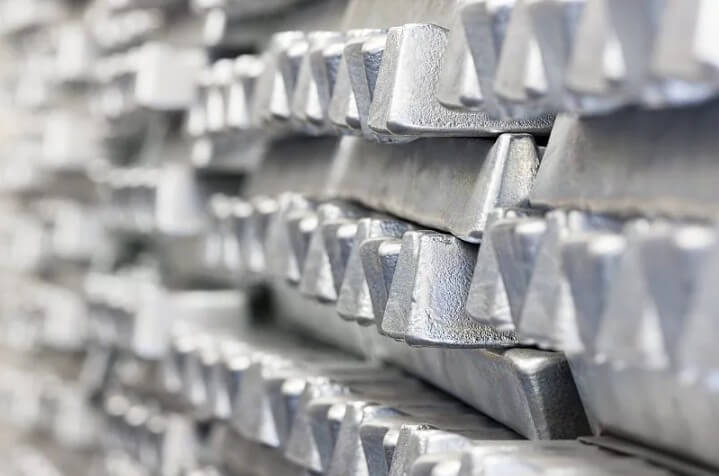
(2) Innovative casting aluminum materials
1) High-strength and toughness aluminum alloys:
By optimizing the alloy composition and heat treatment process, the latest high-strength and toughness aluminum alloys have higher strength and toughness, and can meet more stringent application requirements. This type of material has broad application prospects in the fields of lightweight automobiles and aviation.
2) Aluminum rare earth alloys:
Adding rare earth elements to aluminum alloys can significantly improve the thermal stability, corrosion resistance and mechanical properties of the materials. Aluminum rare earth alloys perform well in high temperatures and harsh environments, and are suitable for manufacturing gas turbine blades and engine components.
3) Aluminum-lithium alloy:
Aluminum-lithium alloy has lower density and higher specific strength, and is one of the ideal materials in the aerospace field. The latest aluminum-lithium alloy has solved the anisotropy problem of traditional aluminum-lithium alloy by improving the production process, further improving its comprehensive performance.
7.Analysis of the application fields of casting aluminum
(1) Automobile industry
In automobile manufacturing, it is mainly used to produce key components such as engine cylinder block, cylinder head, transmission housing, wheel hub, etc. The addition of casting aluminum helps to reduce the overall weight of the car, improve the fuel efficiency and overall performance of the car, and reduce energy consumption and emissions.
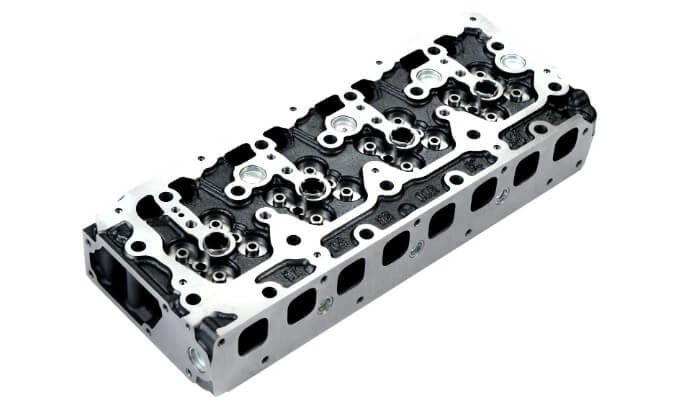
(2) Aerospace
In the aerospace field, casting aluminum are used to manufacture aircraft structural parts and aircraft engine parts due to their light weight and high strength. These parts need to maintain reliable performance under extreme conditions, and casting aluminum can meet these requirements, thereby improving the safety and efficiency of aircraft.
(3) Mechanical equipment
It is also widely used in various types of mechanical equipment, including machine tool housings, gear boxes, etc. These castings aluminum not only improve the performance of the equipment, but also enhance its durability and reliability, which helps to reduce maintenance costs.
(4) Electronics and home appliances
In the electronics and home appliances industry, it is often used to produce radiators and electrical connectors. In electronic equipment, aluminum parts can effectively improve the heat dissipation effect and ensure that electronic components work at an appropriate temperature. In home appliances, aluminum parts are used to produce housings and internal components to improve the quality and appearance of home appliances.
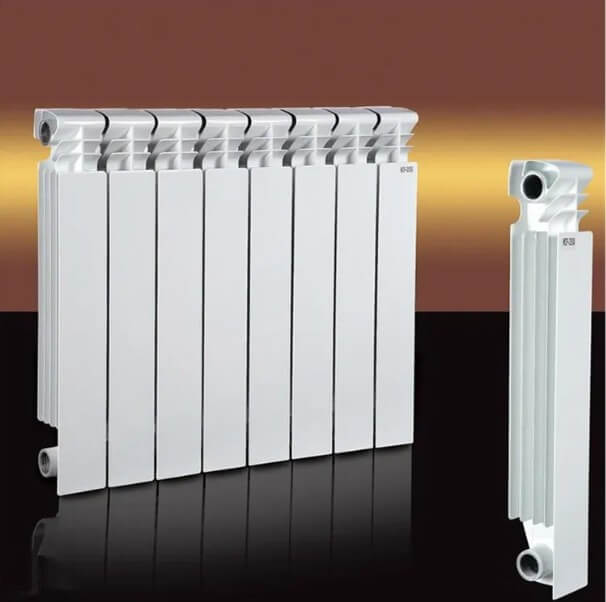
(5) Construction and decoration
In the construction industry, casting aluminum parts are mainly used to produce door and window frames, decorative parts, etc. Its corrosion resistance and easy processing make aluminum parts have high application value in the field of architectural decoration and can meet the needs of different design styles.
8.Summary
In summary, aluminum plays an important role in modern industry with its advantages of light weight, high strength, good casting performance, corrosion resistance, and economic efficiency. Casting aluminum technology has significant advantages in product quality, production efficiency, economy, and application range, making it one of the indispensable materials and processes in modern industrial production.
What do you think?
[…] daily household items to high-tech products, casting aluminum is indispensable. However, the public’s understanding of the basic question of whether cast […]
[…] is an effective method to achieve connections between cast aluminum parts or between cast aluminum and other materials. Through welding, complex structures and […]
[…] machinery manufacturing, etc. Through this process, the original performance and appearance of cast aluminum parts can be effectively restored. This article will introduce in detail the necessity of cast […]
[…] basic process of sand casting aluminum includes making a model, preparing a sand mold, melting aluminum alloy, pouring, cooling, sand […]
[…] The production of aluminum metal castings is mainly carried out through the following casting processes: […]
[…] production processes, application fields, economy and environmental protection of cast iron vs cast aluminum, in order to provide a scientific basis for understanding the selection and application of these […]
[…] production processes, application fields, economy and environmental protection of cast iron vs cast aluminium, in order to provide a scientific basis for understanding the selection and application of these […]