Cast steel valve manufacturers: How to achieve comprehensive control from process to quality
Cast steel valves are indispensable key components in the industrial field and are widely used in industries such as petroleum, chemical, electric power, and water treatment.
Choosing a reliable cast steel valve manufacturer is crucial to ensure the safe operation and long-term stability of equipment.
This article will comprehensively analyze the core content of cast steel valve manufacturers from the aspects of valve casting types, casting processes, material selection, manufacturer evaluation, and quality control, to help you better understand this industry and make wise choices.
1.Types of valve castings
Valve castings can be divided into the following categories according to their functions and structural characteristics:
(1) Classification by function
1) Globe valve castings:
Used to cut off or connect the flow of media in the pipeline. The characteristics of the globe valve are good sealing performance, but the fluid resistance is large, and it is suitable for occasions where the medium needs to be completely cut off.
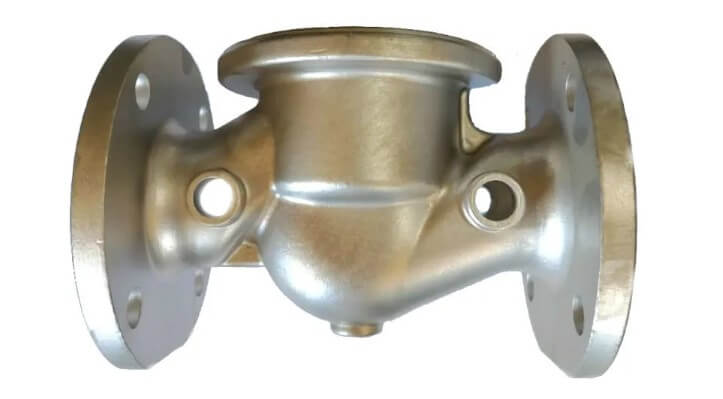
2) Gate valve castings:
Mainly used in full open or full closed occasions, suitable for large flow pipelines. The advantage of the gate valve is small fluid resistance, but the sealing performance is relatively poor.
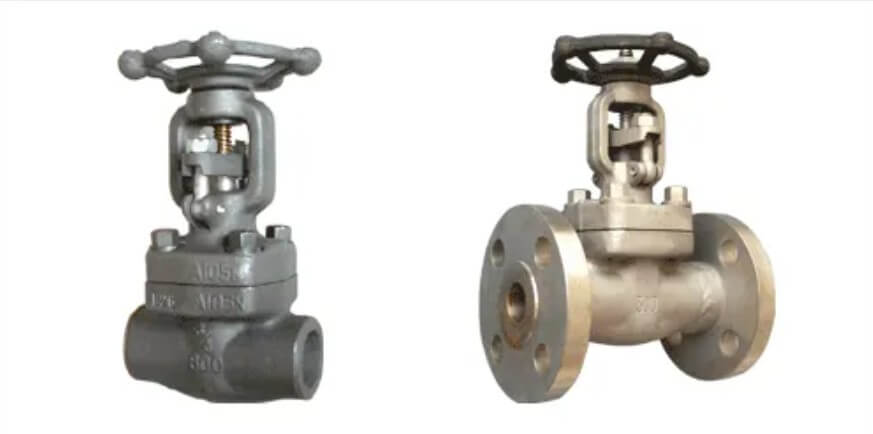
3) Ball valve castings:
Opening and closing are achieved by rotating the ball, and the sealing performance is good. Ball valves are suitable for occasions that require fast opening and closing, and the fluid resistance is small.
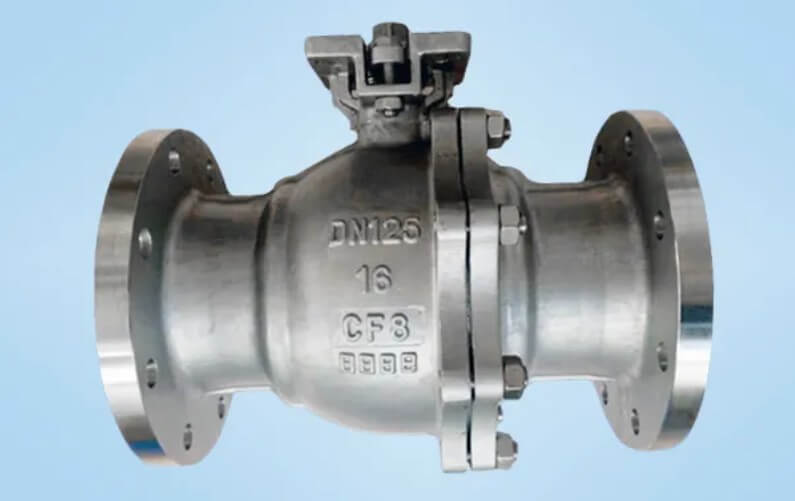
4) Butterfly valve castings:
Simple structure, suitable for large diameter pipes. The advantages of butterfly valves are small size and light weight, but the sealing performance is relatively poor.
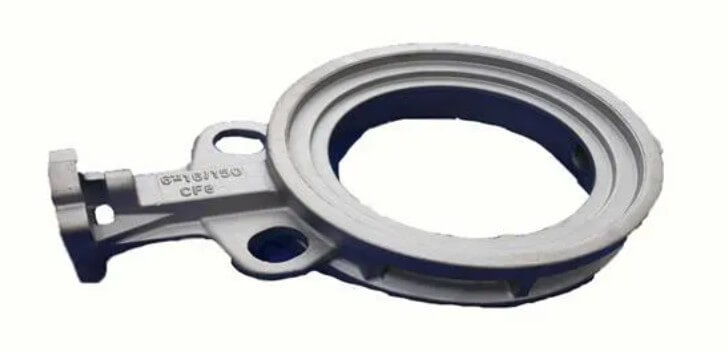
5) Check valve castings:
Prevent medium backflow and ensure one-way flow. Check valves are widely used in occasions such as pump outlets and compressor outlets.
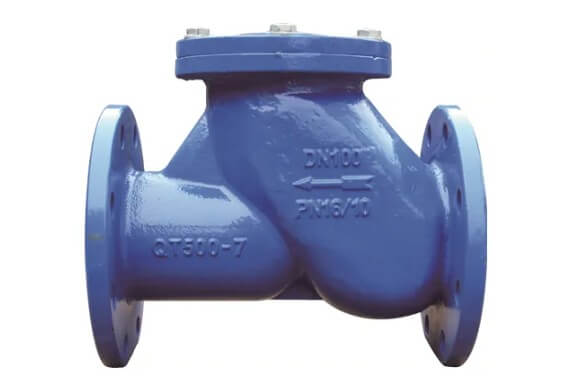
(2) Classification by structure
1) One-piece castings:
The valve body and valve cover are cast as one piece, with high structural strength. One-piece castings are suitable for harsh working conditions such as high pressure and high temperature.
2) Split castings:
The valve body and valve cover are cast separately, which is easy to repair and replace. Split castings are suitable for occasions that require frequent maintenance.
(3) Classification by application field
1) General valve castings:
Applicable to general industrial occasions, such as tap water, HVAC, etc.
2) Special valve castings:
Used in special environments such as high temperature, high pressure, and corrosive media, such as petrochemical, power and other industries.
2.Types of valve castings
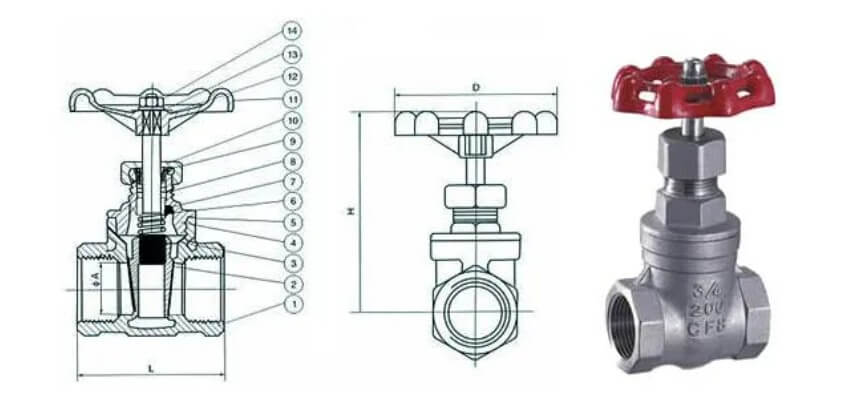
(1) Valve body:
The main pressure-bearing component of the valve, usually made of cast steel or alloy steel, and can withstand high temperature and high pressure conditions. Different types of valve body designs determine the purpose of the valve, such as gate valves, ball valves, butterfly valves, etc.
(2) Valve cover:
Used in conjunction with the valve body, it plays a role in sealing and protecting the internal structure, usually bolted, welded or pressure sealed.
(3) Valve disc:
Used to control fluid flow, commonly seen in stop valves, gate valves and other types, different structural designs affect flow control and sealing performance.
(4) Valve seat:
A key component that provides a sealing surface, usually made of wear-resistant and corrosion-resistant materials to ensure long-term stable operation.
(5) Bracket:
A structural component that connects the actuator and the valve body, used to support the valve stem and transmission mechanism to ensure normal operation of the valve.
(6) Valve stem:
Used to transmit operating force to open or close the valve. The material is generally stainless steel or high-strength alloy steel, which is required to have high corrosion resistance and wear resistance.
3.Valve casting process
The manufacturing process of cast steel valves directly affects their performance and quality. Cast steel valve manufacturers should focus on process optimization. The following are several common casting processes:
(1) Sand casting
Using sand molds as molds, it is suitable for large and complex valve castings.
The production cost is low and suitable for mass production.
Subsequent processing is required to improve surface quality and dimensional accuracy.
Suitable for the production of high-strength and high-wear-resistant valve castings.
(2) Precision casting
Also known as investment casting, it uses wax molds and ceramic shells for precision manufacturing.
Suitable for small castings with high precision requirements, such as stainless steel valves.
It has excellent surface finish and high dimensional accuracy.
Due to the complex process, the cost is high, but it can reduce subsequent processing.
(3) Lost wax casting
Suitable for valve components with complex shapes, especially small and precision valves.
Able to achieve thin-walled structures and improve material utilization.
Long production cycle and high cost, but suitable for high-performance valves.
(4) Die casting
Suitable for small valves made of non-ferrous alloys (such as aluminum and copper alloys).
High production efficiency and good dimensional accuracy, but suitable for valves under low pressure conditions.
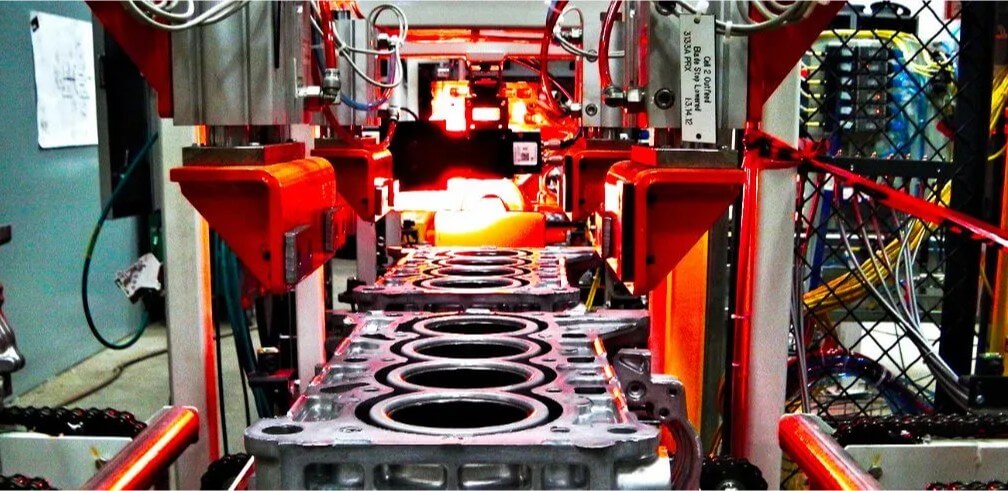
(5) Continuous casting
Mainly used to produce tubular or rod-shaped parts, suitable for specific types of valve components.
Since the continuous casting process reduces metallurgical defects and improves the uniformity of the material, it is suitable for valves that require high-performance materials.
4.Valve casting materials
The material selection of valve castings directly affects its corrosion resistance, high temperature resistance and mechanical properties. The following are common valve casting materials and their characteristics:
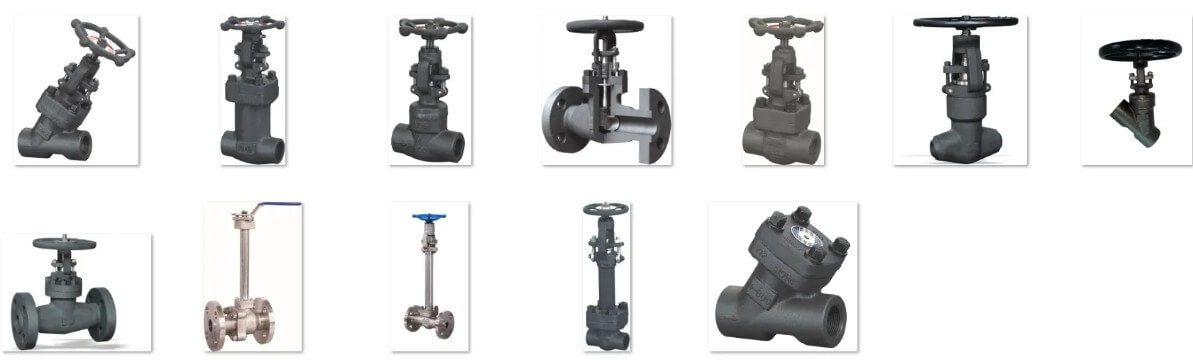
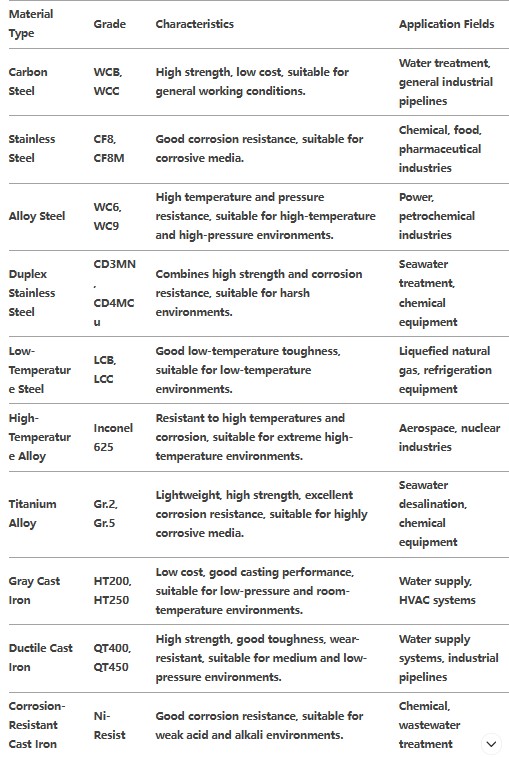
Key points for material selection:
Corrosion resistance: Select appropriate materials according to the corrosiveness of the medium, such as stainless steel, duplex stainless steel, titanium alloy, etc.
High temperature resistance: In high temperature environments, select high temperature alloys or alloy steels.
Low temperature resistance: In low temperature environments, choose low temperature steel or ductile iron.
Wear resistance: For high wear environments, choose ductile iron or alloy steel.
Cost-effectiveness: Under the premise of meeting performance requirements, choose cost-effective materials, such as carbon steel or gray cast iron.
5.How to evaluate cast steel valve manufacturers
Selecting a reliable cast steel valve manufacturer requires evaluation from multiple aspects:
(1) Company qualifications and experience
Qualification certification: such as ISO 9001 quality management system certification, API 6D valve certification, etc.
Industry experience: The manufacturer’s history and service years in the industry.
Whether it complies with domestic and international petrochemical, power, shipbuilding and other industry standards.
(2) Production capacity
Equipped with modern casting, processing, heat treatment, assembly and other production lines.
Whether the production equipment meets the needs of large-scale or customized production.
Delivery capability, whether orders can be delivered on time.
Whether the supply chain management is perfect, including raw material procurement, inventory management, etc.
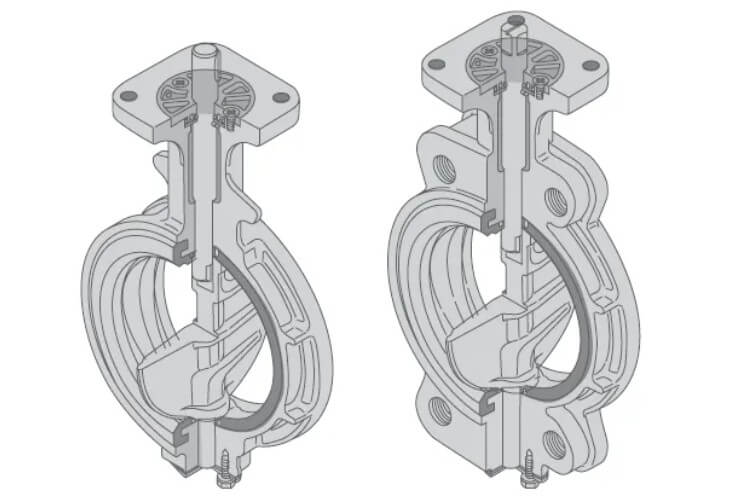
(3) Technical R&D capabilities
Does it have an independent R&D team with the ability to develop new products?
Can it provide customized valve solutions?
Does it have modern design capabilities such as 3D modeling and simulation?
LVXUN Casting has the qualifications, production capabilities, and technical R&D capabilities you need.
In the process of casting valves, we use high-quality materials: stainless steel, carbon steel, and other alloy steels.
In addition, our advanced casting processes such as investment casting and pressure casting can achieve high-quality valve casting. If you are looking for price details that meet your casting valve needs, please contact us directly.
6.How do cast steel valve manufacturers conduct quality control and testing?
Cast steel valve manufacturers use strict quality control and testing methods to ensure the high quality and reliability of their products.
(1) Raw material testing
Chemical composition analysis: Ensure that the material composition meets the standards.
Mechanical property testing: Test the strength, hardness and other properties of the material.
(2) Casting process control
Process parameter monitoring: Real-time monitoring of parameters such as temperature and pressure during the casting process.
Defect prevention: Reduce defects such as pores and shrinkage by optimizing the process.
(3) Nondestructive testing
Radiological testing (RT): Detect internal defects of castings.
Ultrasonic testing (UT): Detect internal cracks and inclusions of castings.
Magnetic particle testing (MT): Detect surface and near-surface defects of castings.
Penetrant testing (PT): Detect opening defects on the surface of castings.
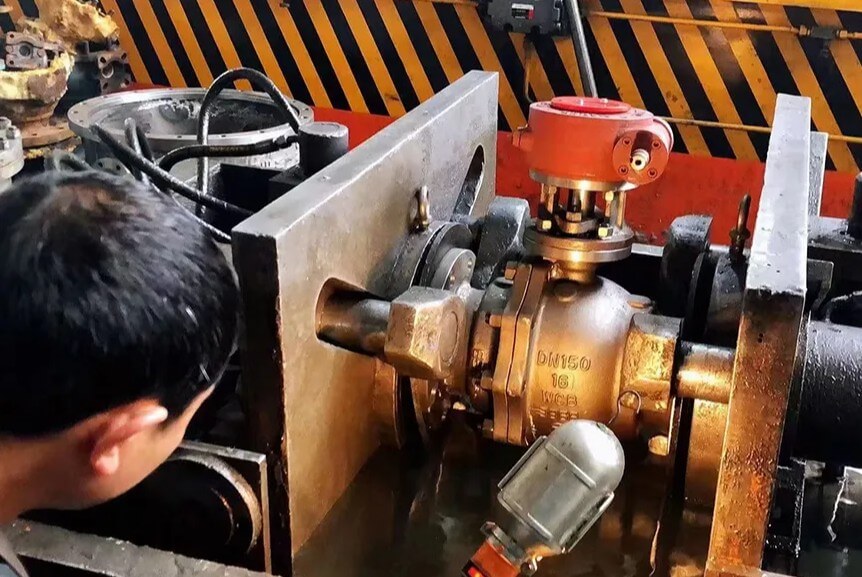
(4) Pressure testing
Shell test: Detect the strength and sealing of the valve body.
Seal test: Detect the sealing performance of the valve.
(5) Dimensional testing
Three-coordinate measurement: Detect the dimensional accuracy of castings.
Surface roughness testing: Detect the smoothness of the casting surface.
(6) Final inspection
Appearance inspection: Ensure that there are no defects on the casting surface.
Functional testing: Simulate actual working conditions and test the switching performance of the valve.
We can ensure that our valve castings undergo nondestructive testing, pressure testing, dimensional testing, etc. to verify product integrity. We guarantee that all manufactured products have leak-free performance.
And we have mature casting technology to ensure excellent surface finish and dimensional accuracy of the products to meet your drawing requirements. If you want to know more details, please contact us, lvxun casting will have professional technicians to answer you.
7.Summary
The selection of cast steel valve manufacturers is not only related to product quality, but also directly affects the safety and operating efficiency of the equipment. By understanding the type of valve castings, casting process, material selection and quality control methods, you can better evaluate the manufacturer’s capabilities and choose the most suitable partner.
I hope this article provides you with valuable information to help you make wise decisions in the purchase of cast steel valves.