Cast stainless steel: characteristics, applications and manufacturing process
Cast stainless steel is a stainless steel material formed by the casting process. It not only inherits the excellent corrosion resistance of stainless steel, but also has the unique mechanical properties and processing advantages brought by the casting process. Cast stainless steel plays an increasingly important role in modern industry, and its application range covers many fields. This article will introduce this special stainless steel material to you.
1.Definition and classification of cast stainless steel
Cast stainless steel refers to cast steel that can resist environmental corrosion. It usually contains a high chromium content and sometimes contains elements such as nickel and molybdenum to enhance its corrosion resistance. According to different standards, cast stainless steel materials can be divided into the following categories:
(1) Classification by metallographic structure:
Austenitic stainless steel: It has an austenitic structure at room temperature, usually contains high chromium and nickel, and has good corrosion resistance and plasticity.
Ferritic stainless steel: It is mainly composed of ferrite structure, has a high chromium content, has a body-centered cubic crystal structure, and has good corrosion resistance and oxidation resistance.
Martensitic stainless steel: Its mechanical properties can be adjusted by heat treatment. The typical grade is Cr13, which is mainly used in occasions requiring higher strength.
Duplex stainless steel: It has the advantages of both austenitic and ferritic stainless steels, has superplasticity, and significantly improves intergranular corrosion resistance and welding performance.
Precipitation hardening stainless steel: It improves strength through precipitation hardening treatment and is commonly used in aerospace and chemical industries.
(2) Classification by corrosion resistance type:
Stress corrosion resistant stainless steel: It can resist stress corrosion cracking under certain conditions.
Pitting corrosion resistant stainless steel: It has good pitting corrosion resistance.
Intergranular corrosion resistant stainless steel: It improves intergranular corrosion resistance by controlling carbon content and adding stabilizing elements.
(3) Classification by functional characteristics:
Non-magnetic stainless steel: It has low magnetic permeability and is suitable for occasions where magnetic interference needs to be avoided.
Free-cutting stainless steel: It has elements such as sulfur and calcium added to improve cutting performance.
Low-temperature stainless steel: It can still maintain good toughness in low-temperature environments.
High-strength stainless steel: It obtains higher strength through special treatment.
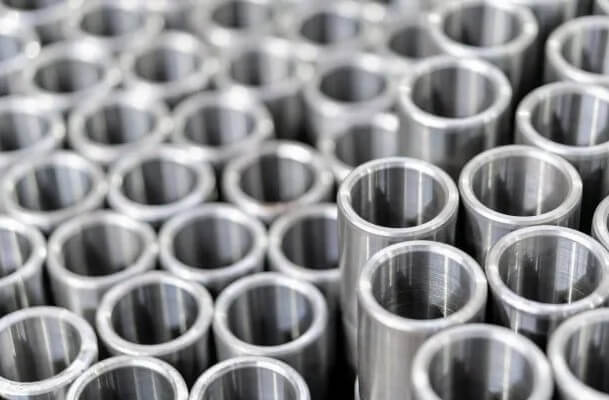
Summary:
These classification methods help to select suitable cast stainless steel materials according to specific application requirements. In practical applications, the selection of stainless steel materials needs to comprehensively consider factors such as environmental media, temperature, and stress to ensure that the material can perform well under specific working conditions.
2.What are the main components of cast stainless steel materials?
(1) Iron (Fe):
As the basic element of stainless steel, iron constitutes the main body of stainless steel.
(2) Chromium (Cr):
Chromium is the most important alloying element in stainless steel, and its content is usually not less than 10.5%. Chromium can form a dense chromium oxide film on the surface of stainless steel, which can effectively prevent erosion from the external environment, thereby improving the corrosion resistance of stainless steel.
(3) Nickel (Ni):
The addition of nickel can improve the strength and toughness of stainless steel, and can also improve the corrosion resistance of stainless steel in certain environments.
(4) Carbon (C):
The role of carbon in stainless steel is to increase hardness, but too high a carbon content will increase the brittleness of the material, so its content needs to be precisely controlled.
(5) Silicon (Si):
Silicon can enhance the strength of stainless steel, but in some cases, too high a silicon content may affect the plasticity and toughness of stainless steel.
(6) Manganese (Mn):
Manganese can be used as an alloying element to replace nickel, reducing costs, while also improving the strength and hardness of stainless steel.
(7) Phosphorus (P) and sulfur (S):
These elements are generally regarded as harmful elements because they may reduce the plasticity and toughness of stainless steel, especially at high temperatures.
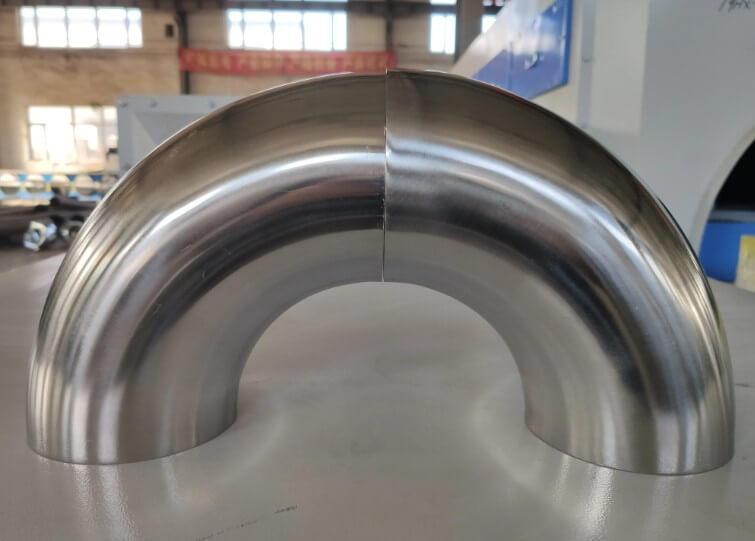
3.Basic properties of cast stainless steel
Cast stainless steel is an engineering material widely used in many industries. Its basic properties can be described from three aspects: corrosion resistance, mechanical properties and high temperature properties:
(1) Corrosion resistance:
One of the most prominent characteristics of cast stainless steel is its excellent corrosion resistance in a variety of corrosive media. This is mainly due to the high content of chromium in stainless steel, which can react with oxygen to form a dense oxide film that effectively prevents further oxidation and corrosion.
(2) Mechanical properties:
Cast stainless steel has high strength and toughness and can maintain structural integrity when subjected to high pressure or impact. Its high tensile strength and yield strength, as well as good plasticity and toughness, make stainless steel an ideal material for manufacturing high-load components and structures.
(3) High temperature performance:
Cast stainless steel can maintain its stable performance under high temperature environment, with a high melting point and good thermal stability. This makes stainless steel advantageous in manufacturing high-temperature equipment, furnaces and pipelines.
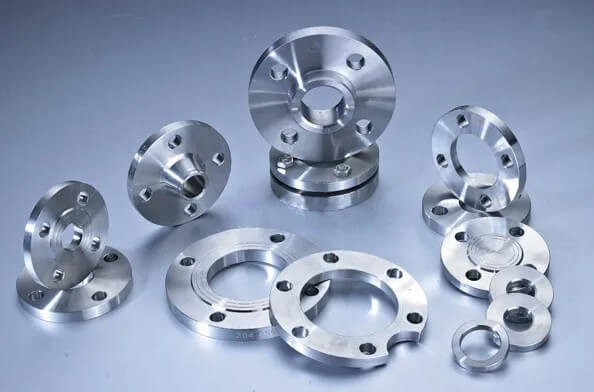
4.Manufacturing process of cast stainless steel
(1) Raw material preparation and manufacturing
The first step in casting stainless steel is to prepare the raw materials, which includes selecting the appropriate steel grade and strictly controlling the chemical composition. Commonly used types of stainless steel include austenitic stainless steel, martensitic stainless steel and ferritic stainless steel, each type is selected according to its specific application scenario.
(2) Melting and casting
The melting process is usually carried out in an electric furnace to ensure the purity and uniformity of the metal. Casting methods include sand casting and precision casting, among which precision casting processes such as investment casting and pressure casting can produce stainless steel castings with complex shapes, high precision and good surface finish.
(3) Heat treatment
Heat treatment is a key step in the manufacturing process of cast stainless steel. Through processes such as solution treatment and aging treatment, the mechanical properties and corrosion resistance of the material can be optimized.
Solution treatment usually involves heating the stainless steel to a high temperature to dissolve its carbides and then rapidly cooling it to form a uniform austenite structure.
Aging treatment involves maintaining the material at a lower temperature for a period of time to allow the precipitation phase to precipitate from the supersaturated solid solution, thereby increasing the hardness and strength of the material.
(4) Subsequent processing
Subsequent processing includes mechanical processing and surface treatment. Mechanical processing such as turning and milling is used to achieve the final dimensional accuracy and shape requirements.
Surface treatment such as polishing and electroplating can not only improve the appearance, but also further improve the corrosion resistance and other special properties. For example, the surface of stainless steel can be brushed, mirrored or embossed to obtain different decorative effects and functionality.
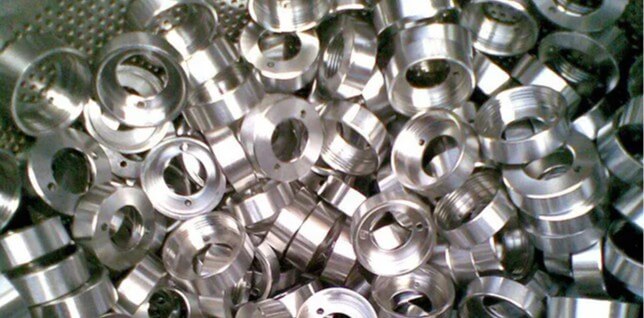
5.Application areas of cast stainless steel
Cast stainless steel plays an important role in many industries with its excellent corrosion resistance, heat resistance and mechanical properties. The following are the main application industries of cast stainless steel:
(1) Medical industry:
Due to its corrosion resistance and biocompatibility, it is often used to manufacture medical devices such as surgical instruments and implants.
(2) Construction industry:
In terms of architectural decoration, it is mainly used for interior and exterior decoration and components such as exterior walls, interior and exterior columns, handrails, floors, elevator sidings and curtain walls of high-rise buildings.
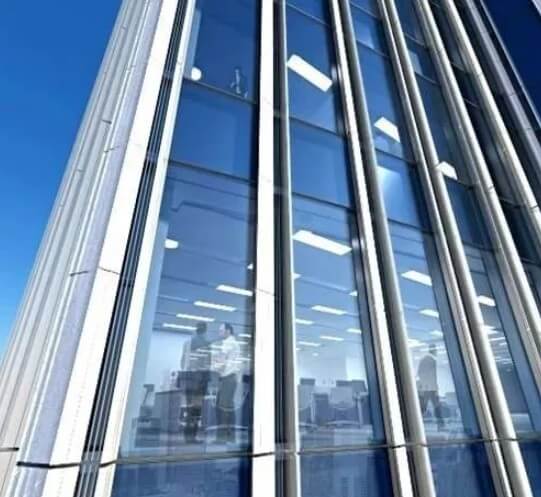
(3) Transportation industry:
Its application in the transportation field includes the manufacture of automotive panels and decorative parts, as well as for automotive exhaust systems due to its heat resistance.
(4) Water industry:
Stainless steel plates are the preferred materials for water industries such as water production, storage, transportation, purification and desalination due to their corrosion resistance, earthquake resistance, light weight, low maintenance, low life cycle cost, and a recyclable green and environmentally friendly material.
(5) Chemical industry:
Due to its corrosion resistance, it is suitable for the manufacture of chemical equipment, valves, pipes, etc.
(6) Food industry:
In the food industry, it is mainly used to manufacture kitchen utensils and food processing equipment.
(7) Home appliance industry:
Cast stainless steel is also widely used in the home appliance industry, such as the manufacture of water heaters, boilers, etc.
(8) Marine equipment field:
316 stainless steel precision castings can be used to manufacture ship accessories, offshore platforms, etc., due to their better corrosion resistance and heat resistance.
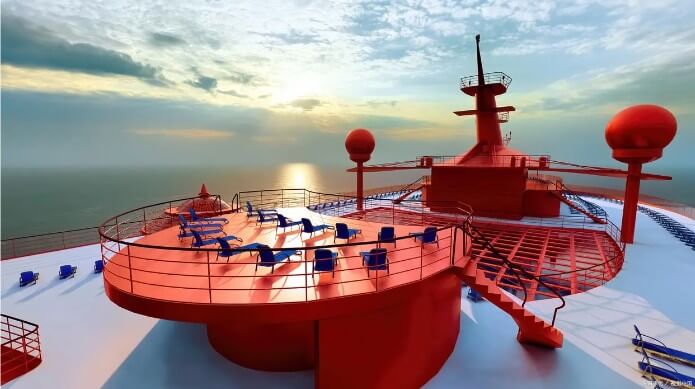
(9) Machinery industry:
Cast stainless steel is also used in metal products industries such as tableware, utensils, hardware, sanitary ware, as well as machinery industry, automobile industry, construction industry, home appliance industry and elevator industry.
5.The difference between cast stainless steel materials and stainless steel materials
(1) Manufacturing process:
Cast stainless steel is manufactured by pouring stainless steel liquid into a mold and cooling and solidifying it.
Stainless steel materials can be made through a variety of processes such as casting, forging, rolling, etc.
(2) Performance characteristics:
Cast stainless steel usually has good corrosion resistance and high temperature resistance, but the strength and plasticity may be lower.
Stainless steel materials have different mechanical properties, such as strength, plasticity and toughness, depending on the different manufacturing processes and alloy compositions.
(3) Application fields:
Cast stainless steel is often used in chemical equipment, food machinery, medical equipment, etc. due to its good corrosion resistance and high temperature resistance.
Stainless steel materials are widely used in many fields such as construction, decoration, automobiles, and home appliances.
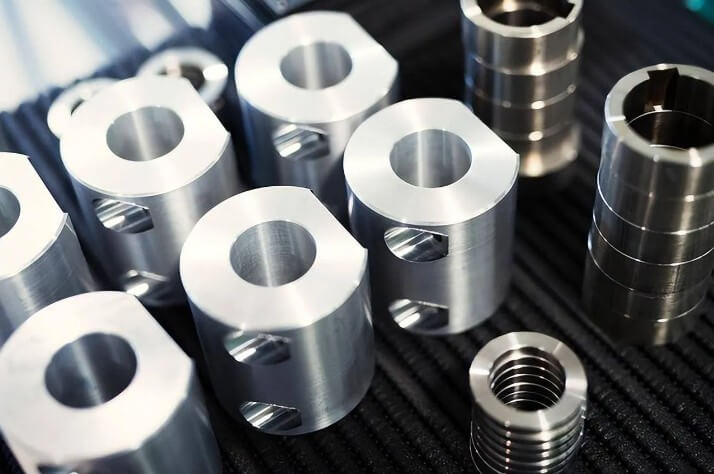
(4) Cost and price:
Cast stainless steel is usually more expensive due to its complex manufacturing process and high material requirements.
The cost of stainless steel materials varies according to different processes and alloy compositions.
6.Summary
With the continuous advancement of science and technology, cast stainless steel is developing towards low-carbon and ultra-low-carbon, high-performance special steels, and composite alloying. Duplex stainless steel will also usher in rapid development due to its high yield strength and good corrosion resistance, especially in terms of stress corrosion cracking resistance. In addition, the method of improving the performance of stainless steel by adding trace elements such as rare earths shows broad application prospects.