A complete analysis of cast aluminum repair technology: a practical guide
Cast aluminum repair is a metal processing process widely used in the fields of automobiles, machinery manufacturing, etc. Through this process, the original performance and appearance of cast aluminum parts can be effectively restored. This article will introduce in detail the necessity of cast aluminum repair, the main technologies and repair methods, and the entire process of cast aluminum repair.
1.Necessity of cast aluminum repair
Cast aluminum repair can not only restore its function, ensure safety and improve efficiency, but also save resources and costs, which has important economic and environmental significance.
(1) Improve safety and production efficiency:
Cast aluminum parts may suffer from wear, corrosion or fracture during long-term use, which will seriously affect the safety of equipment. Through repair, the safe operation of equipment is ensured, downtime is reduced, and production efficiency is improved.
(2) Extend service life:
Repair can effectively extend the service life of cast aluminum parts, avoid frequent replacement due to part damage, and thus reduce production costs and maintenance costs.
(3) Save resources:
Repairing cast aluminum parts can reduce the demand for new materials, save resources, and reduce environmental pollution. This is in line with the concept of green manufacturing and sustainable development.
(4) Improve performance:
Modern repair technology can optimize the structure and performance of aluminum castings, so that they have better wear resistance, corrosion resistance and mechanical strength after repair.
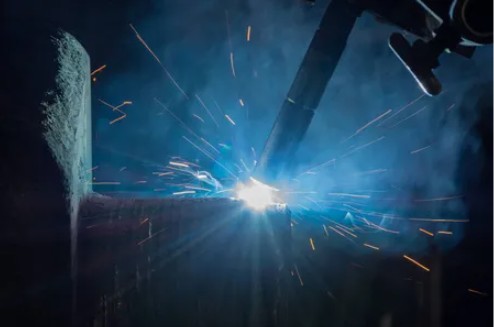
2.Main technologies and methods for cast aluminum repair
Aluminum castings are widely used in modern industry, but due to various reasons, such as casting defects, processing damage, etc., they often need to be repaired to extend their service life or maintain their performance.
The following will introduce traditional cast aluminum repair technology and modern cast aluminum repair technology.
Traditional cast aluminum repair technology
(1) Welding repair
Welding repair is to fuse the solder with the aluminum casting matrix by heating to form a strong connection, thereby repairing the defects of aluminum castings. Common welding repair methods include AC argon arc welding, DC welding machine and arc welding, gas welding, etc. These methods effectively reduce welding deformation and crack tendency by controlling heat input and welding parameters, and ensure the quality of repair.
Welding repair has the following advantages:
1) High repair accuracy:
Welding repair can accurately control heat input and welding area, so it can accurately repair small defects and avoid damage to surrounding materials.
2) Wide application range:
Welding repair can be flexibly applied to both small aluminum castings and large structural parts. In addition, this technology can also repair defects of various complex shapes, showing strong adaptability.
3) Low repair cost:
Compared with replacing new aluminum castings, welding repair has a lower cost and can make full use of existing materials to reduce resource waste.
4) High repair efficiency:
The welding repair process is relatively fast and can complete the repair work in a short time, reducing production downtime and improving production efficiency.
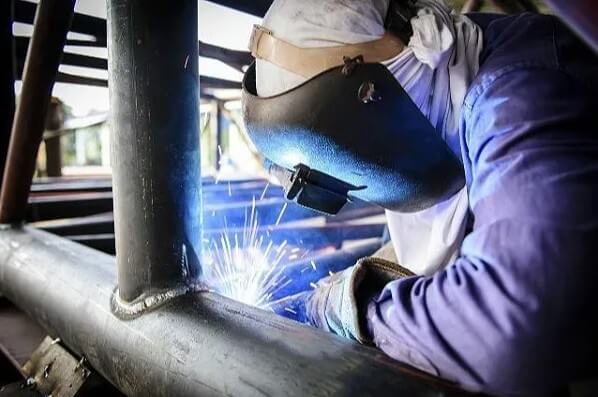
(2) Mechanical repair
Mechanical repair is to remove or repair the damaged part through mechanical processing methods such as drilling, tapping, and inserting metal studs, and re-establish its structural strength. This method is usually used to repair larger cracks or damage.
Mechanical repair has the following advantages:
1) High reliability:
Mechanical repair enhances the strength of the repaired part through physical connection, which can provide long-term stable performance and is particularly suitable for aluminum castings that are subjected to high stress or cyclic loads.
2) Good fatigue resistance:
Mechanical repair can effectively reduce stress concentration during the repair process, improve the fatigue resistance of the repaired part, and extend the service life of cast aluminum parts.
3) Flexible scope of application:
Mechanical repair can not only be used alone, but also in combination with other repair methods, such as first removing the damaged part by mechanical processing, and then welding repair to achieve better repair effect.
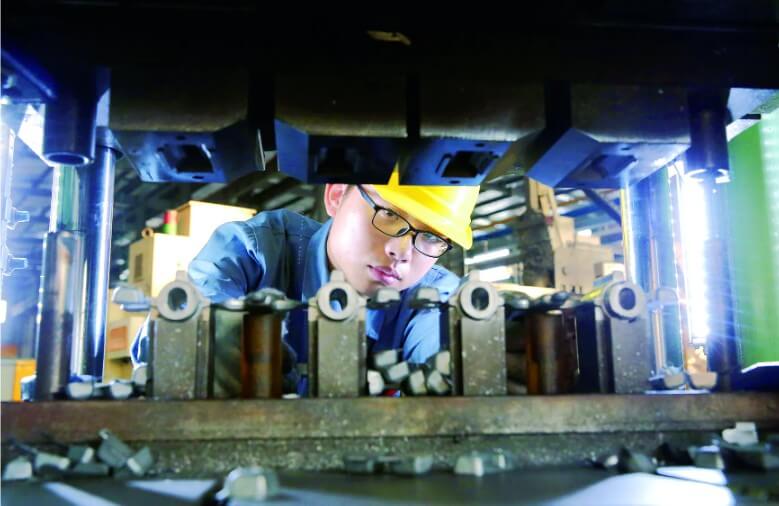
Modern cast aluminum repair technology
(1) Cold welding technology
Cold welding technology is a method of repairing casting defects by using high-frequency electric spark instantaneous discharge and heatless surfacing principle. Traditional welding methods such as electric welding and argon welding are prone to side effects such as thermal deformation due to large heat release, and cannot meet the requirements of repair welding. Cold welding technology uses high-frequency discharge to melt the repair material and the substrate at the same time and then solidify, which is a strong combination with high welding strength.
Cold welding technology has the following advantages:
1) Small heat-affected zone:
The heat-affected zone of cold welding technology is very small, which will not cause annealing deformation of the substrate, cracks, hard spots, and hardening. This makes cold welding technology particularly important when repairing precision aluminum castings.
2) Easy operation:
The cold welding repair machine is easy to operate and does not require complicated pre-processing and post-processing steps. During the repair process, the choice of welding materials is also very flexible and can be selected according to the material and defect conditions of the aluminum casting.
3) Wide range of applications:
Cold welding technology can not only repair defects such as pores, sand holes, and cracks in aluminum castings, but can also be used to repair defects in other metal materials, such as stainless steel and copper.
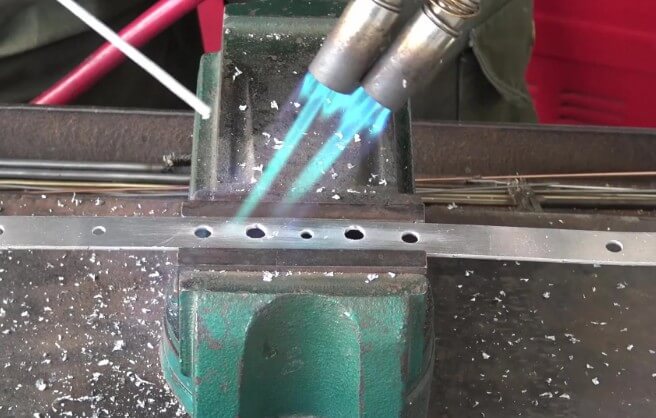
(2) Laser deposition repair technology
Laser deposition repair technology is a method that uses a laser beam to melt metal powder and deposit it on the surface of aluminum castings to form a new metal layer to repair defects. This technology has the advantages of high precision, small deformation, and high bonding strength.
Laser deposition repair technology has the following advantages:
1) High precision:
Laser deposition repair technology can achieve micron-level repair accuracy, which is very suitable for the repair of precision aluminum castings. By accurately controlling the power and scanning speed of the laser beam, high-quality cast aluminum repair effects can be obtained.
2) Small deformation:
Due to the high energy density of the laser beam and the small heat input during the repair process, the deformation of the aluminum casting is also very small. This avoids the problem of subsequent processing due to thermal deformation in traditional welding methods.
3) High bonding strength:
In laser deposition repair technology, the deposited metal powder forms a metallurgical bond with the base material, and the bonding strength is very high. This enables the repaired aluminum casting to meet its original performance requirements.
4) Flexible material selection:
Laser deposition repair technology can use a variety of metal powders for repair, and the appropriate metal powder can be selected according to the material and performance requirements of the aluminum casting. This provides greater flexibility for cast aluminum repair.
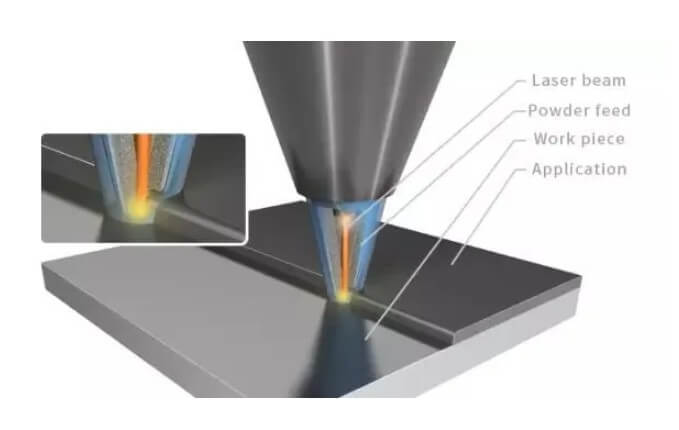
3.Operation and practice of cast aluminum repair technology
(1) Preparation before repair
1) Surface cleaning:
First, the surface of the aluminum casting needs to be thoroughly cleaned to remove oil, rust and other impurities. Common cleaning methods include mechanical cleaning and chemical cleaning to ensure that the cast aluminum repair surface is clean and pollution-free.
2) Defect detection:
Use non-destructive testing technology (such as X-ray, ultrasonic testing, etc.) to conduct comprehensive defect detection on cast aluminum parts, determine the location and size of defects, and provide data support for subsequent cast aluminum repair.
3) Preparation of tools and materials:
Prepare the tools and materials required for cast aluminum repair, including welding guns, welding wires, grinding wheels, protective equipment, and cast aluminum materials for repair. Ensure that all equipment and materials are in good condition.
(2) Specific repair operation process
1) Preheating treatment:
In order to reduce internal stress and deformation during the repair process, the cast aluminum parts need to be preheated, usually heating the workpiece to 150-200°C.
2) Selection of repair method:
When repairing cast aluminum, the appropriate repair method should be selected according to the defect size and repair requirements. When the casting has cracks or fractures, pores, shrinkage and other defects, and the casting size is poor, choose welding repair technology; when there are defects such as cracks, holes or dents, and the cast aluminum parts are damaged due to accidental collision or impact, mechanical repair technology is required for repair.
When the aluminum casting has surface defects such as wear, scratches, pores, and sand holes, cold welding repair technology is suitable; when the aluminum casting has cracks or fractures, severe surface wear, dimensional tolerances, and needs to improve local hardness or wear resistance, laser deposition repair technology is suitable.
3) Cooling after welding:
After welding, let the aluminum casting cool naturally. Avoid rapid cooling to prevent new cracks and deformation.
4) Machining:
After cooling, use tools such as grinding wheels and milling machines to machine the repaired parts to restore their shape and size to their original state.
5) Quality inspection:
Use non-destructive testing technology to inspect the aluminum casting repair part again to ensure that the repair quality meets the standards. If defects are found, it needs to be repaired again.
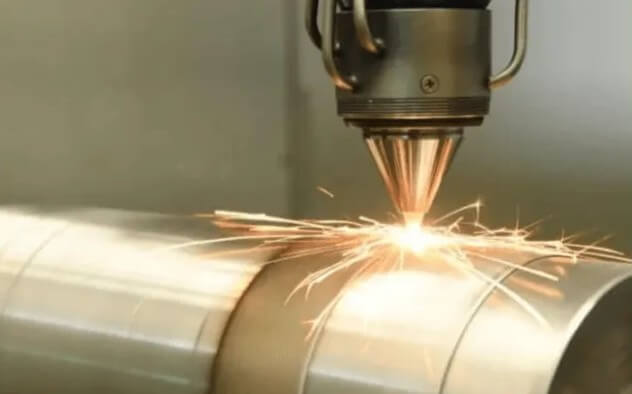
(3) Treatment after repair
1) Post-heat treatment:
In order to further eliminate internal stress and improve the mechanical properties of the aluminum casting repair part, the aluminum casting needs to be post-heat treated. It is usually carried out at a low temperature (such as 200-300°C), kept for a period of time, and then slowly cooled.
2) Surface treatment:
Sandblasting, polishing and other treatments are performed on the repaired surface to make it smooth and flat, and restore the original appearance.
3) Anti-corrosion treatment:
In order to improve the corrosion resistance of aluminum castings, surface coating or plating treatment can be performed, such as spraying anti-corrosion paint or anodizing.
4) Final inspection:
The repaired aluminum castings are fully inspected, including dimensional accuracy, surface quality and mechanical properties tests, to ensure that all indicators meet the requirements.
4.Summary
Through the above repair techniques and treatment methods, various defects of aluminum castings can be effectively repaired, and their service life and performance can be improved. In practical applications, the appropriate repair method should be selected according to the specific situation of the aluminum casting to ensure the repair effect and economic benefits of the aluminum casting.