Cast aluminum pan: production art and technological innovation
Cast aluminum pan is a pan made by casting aluminum liquid through a mold. It has exquisite craftsmanship, fast heat conduction, light weight, strong durability and other characteristics, and has gradually become the first choice for many families. This article will introduce in detail the history of cast aluminum pans, production process, technological innovation, key factors affecting the quality of cast aluminum pans, advantages and disadvantages, and methods to improve their service life.
1.History of cast aluminum pans
As a traditional cooking tool, the history of cast aluminum pans can be traced back to the beginning of the last century. Early cast aluminum pans were mainly made by hand with simple processes. With the advancement of the industrial revolution and the development of metal smelting technology, the production of cast aluminum pans gradually shifted from manual to mechanized.
The production process of cast aluminum pans has developed rapidly in the mid-20th century, especially in the research and development and application of aluminum alloy materials. The production of modern cast aluminum pans not only uses high-precision mechanical equipment, but also introduces computer-aided design and manufacturing technology, which has brought the dimensional accuracy and surface quality of the products to a new height.
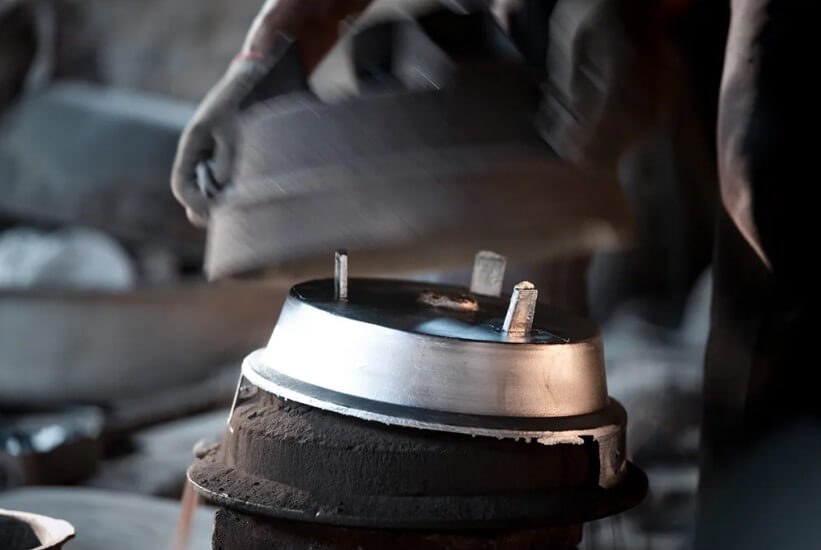
2.Production process of cast aluminum pans
(1) Raw material preparation and melting
The main raw material of cast aluminum pans is aluminum ingots, which usually need to be heated to above 600℃ to completely melt into aluminum water. In order to ensure that the composition of aluminum water meets the requirements, other elements such as silicon, copper, zinc, etc. are added to form a specific aluminum alloy. For example, in the commonly used aluminum-silicon alloy, aluminum accounts for about 85%, silicon accounts for about 11%, and other elements are configured according to the latest European aluminum alloy standard EN602.
(2) Die casting
During the die casting process, molten aluminum water is injected into the mold and formed into the basic shape of the pan through high pressure. The pressure, speed, temperature and holding time of the die casting machine are the key factors that determine the quality of the product. Insufficient pressure of the die casting machine will lead to a loose internal structure of the product, and too slow speed may prevent air and slag from being discharged cleanly, resulting in bubbles. The mold temperature generally needs to be maintained at around 280℃, and the aluminum water temperature is between 620-630℃ to ensure good molding and no defects.
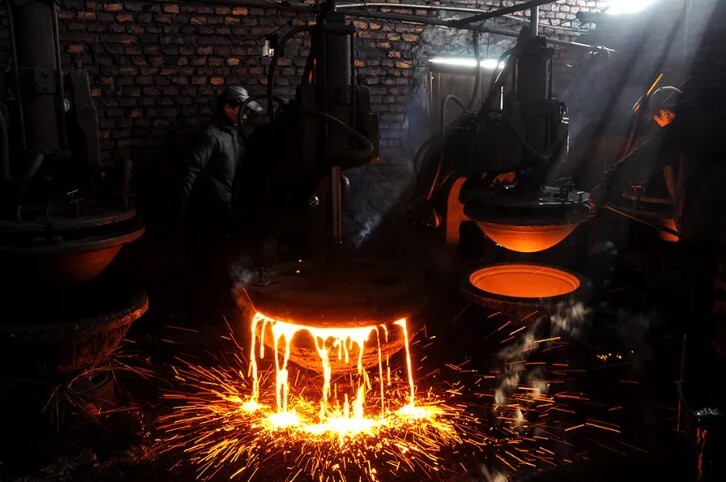
(3) Finishing and polishing
The pan body needs to be trimmed after die casting, mainly to remove burrs and flash. This step is usually done manually to ensure the smoothness of the product surface. Subsequently, the surface is further refined by mechanical polishing to ensure that there are no obvious defects and improve the appearance quality of the product.
(4) Rebottoming
Rebottoming is an important step in the production of cast aluminum pans. The rebottom sheet is embedded into the bottom surface of the pan by cold pressing. The rebottoming not only enhances the strength and durability of the pan bottom, but also improves the thermal conductivity and makes the temperature distribution of the pan body more uniform.
(5) Spraying
In the spraying workshop, the surface of the pan body will be sandblasted to peel off the oxide film and make the surface roughness uniform, which helps to improve the adhesion of the coating. Then spraying is carried out. The spraying materials include non-stick coatings and ceramic coatings, which need to be matured before use. The spraying process is completed by automated equipment to ensure that the coating is uniform and flawless.
(6) Baking and inspection
After spraying, the pan body needs to be baked in the baking oven. The baking oven is divided into low temperature zone, medium temperature zone and high temperature zone, and the baking time is generally 45 minutes. During the baking process, harmful substances in the coating volatilize to form a strong and durable coating. After baking, a series of quality inspections are carried out, including coating adhesion test, wear resistance test, non-stick test, etc., to ensure that each cast aluminum pan meets the quality standards.
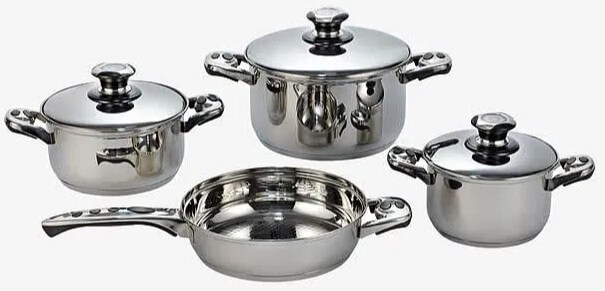
3.Technological innovation of cast aluminum pans
(1) Adopting computer simulation and automated production lines
Computer simulation technology can predict and optimize various parameters in the casting process, such as temperature, pressure and cooling rate, before actual production, thereby reducing defects and improving the yield rate. The automated production line integrates various advanced equipment and control systems to realize the automation of the entire process from smelting, pouring to cooling and mold opening, greatly improving production efficiency and product consistency.
(2) Developing new aluminum alloy materials
In terms of aluminum alloy materials, 6063 aluminum alloy is widely used in the production of cast aluminum pans due to its good casting performance and corrosion resistance. By precisely controlling the melting and casting production process, the quality and performance of the pan can be further improved. For example, by controlling the chemical composition and smelting process of aluminum alloy, the microstructure of the alloy can be optimized and its mechanical properties and corrosion resistance can be improved.
(3) Adopting advanced surface treatment technology
In addition, advanced surface treatment technologies such as ceramic coating technology have also been applied to the production of cast aluminum pans to improve their non-stick properties and durability. Ceramic coating not only has good non-stick properties, but also has high temperature stability and corrosion resistance, which can significantly improve the service life and safety of pans.
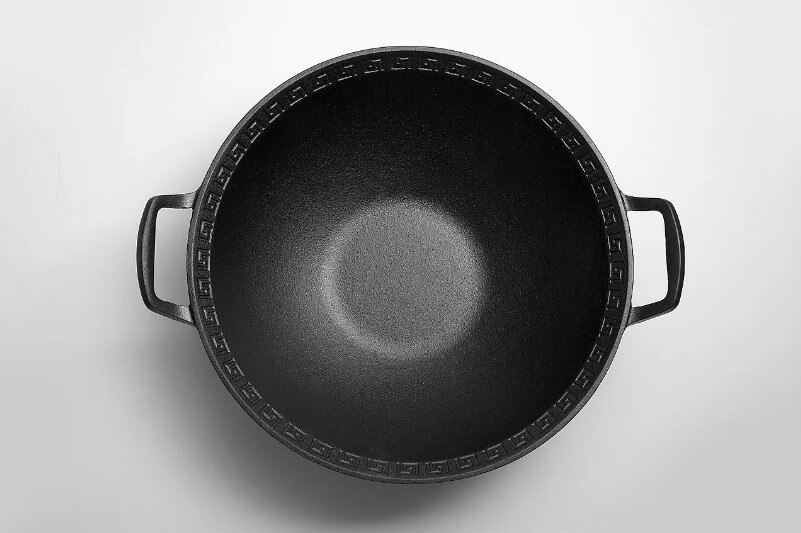
4.Key factors affecting the quality of cast aluminum pans
(1) Selection of raw materials
The main material of cast aluminum pans is aluminum alloy. The purity and alloy composition of aluminum have a direct impact on the quality of the pan. Pans made of high-purity aluminum have better thermal conductivity, and the right amount of alloying elements such as copper, magnesium, silicon, etc. can improve the strength and wear resistance of aluminum pans. The selection of high-quality aluminum alloy materials is the basis for ensuring the quality of cast aluminum pans.
(2) Casting process
The casting process is the core link that determines the quality of cast aluminum pans. Common casting processes include gravity casting, pressure casting and low-pressure casting. Pressure casting and low-pressure casting can improve the filling capacity of aluminum liquid and reduce defects such as pores and shrinkage, thereby obtaining a pan body with dense structure and high strength. Advanced casting equipment and control of process parameters are crucial to improving the quality of cast aluminum pans.
(3) Mold design
Mold design has an important influence on the dimensional accuracy and surface quality of cast aluminum pans. Reasonable mold design can ensure that the shape and size of the pan body meet the requirements and reduce casting defects. High-quality mold materials and advanced processing technology can extend the service life of the mold, thereby improving the consistency and quality stability of the aluminum pan.
(4) Heat treatment process
Heat treatment is a key process to improve the mechanical properties of cast aluminum pans. Through appropriate heat treatment processes, the microstructure of the aluminum pan can be improved, and its hardness, strength and wear resistance can be improved. Different aluminum alloy materials require different heat treatment specifications to ensure that the heat treatment effect reaches the best state.
(5) Surface treatment
Surface treatment not only affects the appearance of cast aluminum pans, but also has an important influence on their corrosion resistance and service life. Common surface treatment methods include anodizing, sandblasting and coating. Anodizing can form a hard oxide film on the surface of the aluminum pan, improving its wear resistance and corrosion resistance. Coating treatment can give the aluminum pan special functions such as non-stick.
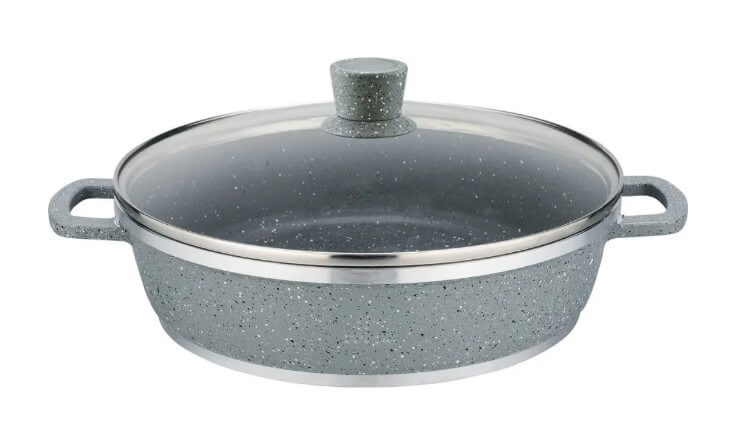
5.Analysis of the advantages and disadvantages of cast aluminum pans
(1) Advantages
1) Good thermal conductivity:
The cast aluminum pan has excellent thermal conductivity, which can evenly heat food in a short time and save energy.
2) Lightweight and durable:
Compared with iron pans, aluminum pans are lighter, easier to carry and operate, and have good durability after proper treatment.
3) Beautiful and diverse:
Cast aluminum pans can be made into a variety of shapes and colors through various processes, with exquisite appearance, which can meet the needs of different consumers.
4) Not easy to rust:
Aluminum itself is not easy to rust, reducing the trouble of maintenance.
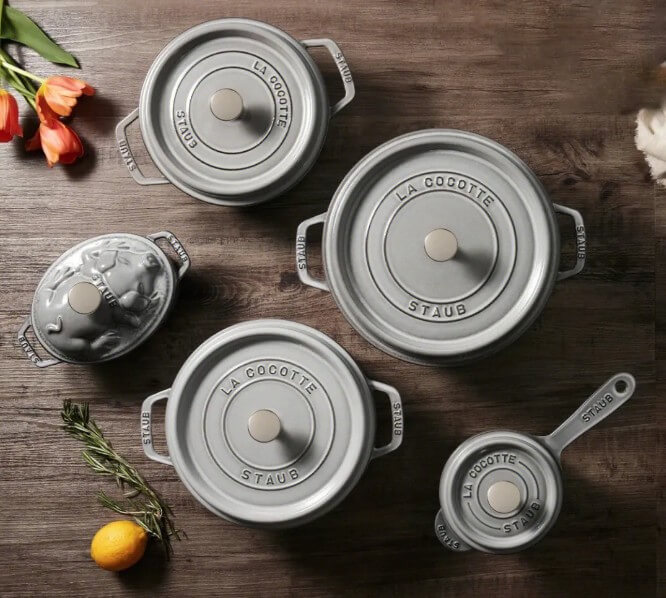
(2) Disadvantages
1) Risk of aluminum precipitation:
When cooking acidic or alkaline foods, aluminum pans may precipitate aluminum. Long-term excessive intake of aluminum may have adverse effects on human health.
2) Not suitable for high-temperature cooking:
Aluminum pans are not suitable for high-temperature cooking and are prone to burnt.
3) Low hardness:
Aluminum has a low hardness and is prone to dents and bumps, which affects the appearance and service life.
4) High maintenance requirements:
Although it is not easy to rust, it is necessary to avoid using hard tools to clean it to avoid damaging the surface protective layer.
6.Methods to increase the service life of cast aluminum pans
Cast aluminum pans are favored by many families because of their light weight and rapid heat conduction. In order to extend their service life, we can take the following methods:
(1) Avoid dry burning:
Cast aluminum pans have a low melting point. When using, make sure there is enough water in the pan to avoid dry burning, otherwise it is easy to damage the bottom of the pan.
(2) Prevent acid and alkali corrosion:
Aluminum is afraid of acid and alkali corrosion, so it is best not to place acid and alkali food in the pan overnight. When not using the pan, do not put flour or other substances that are prone to corrosion.
(3) Protective oxide film:
The surface of cast aluminum pans usually has an oxide film, which has a protective effect. Do not wipe the pan with rough tools such as steel wool to avoid damaging the oxide film. If light yellow rust appears on the pan, do not remove it deliberately, as this layer of rust protects the pan.
(4) Handle with care:
Avoid bumping the pan, especially when the temperature is high. Sudden temperature changes may cause the pan to deform or damage.
(5) Clean regularly:
Clean the pan promptly after use to avoid food residues adhering to the pan for a long time, which makes it difficult to clean and damages the pan. It can be cleaned with a mild detergent and a soft cloth.
(6) Avoid high-temperature heating:
Try to control the heat and avoid long-term high-temperature heating. This not only saves energy but also reduces the loss of the pan.
7.Conclusion
As a traditional cooking tool, cast aluminum pans have many advantages, such as fast heat conduction and light weight. However, in the face of market competition and consumers’ requirements for health and safety, the cast aluminum pan industry needs to continue to innovate technology and improve processes. By introducing new materials and new technologies, the durability and health and safety of cast aluminum pans can be improved. For example, the application of ceramic coating technology and advanced aluminum alloy materials can significantly improve the safety and service life of cast aluminum pans.