Carbon steel vs cast iron: an in-depth comparison of material properties and processing technology
In modern industry, the selection of metal materials is crucial. Carbon steel vs cast iron, as two common iron-carbon alloys, are widely used in machinery manufacturing, building structures, automotive industry and other fields. This article will explore in depth the differences between carbon steel vs cast iron in material properties and processing technology to help readers better understand these two materials and make more appropriate choices in practical applications.
1.Basic characteristics of carbon steel vs cast iron
(1) Carbon steel
Carbon steel is an iron-carbon alloy with a carbon content of 0.0218% to 2%. According to the carbon content, it can be divided into low carbon steel, medium carbon steel and high carbon steel. The carbon content directly affects the mechanical properties of carbon steel: as the carbon content increases, the strength and hardness of the steel increase, but the plasticity and toughness decrease.
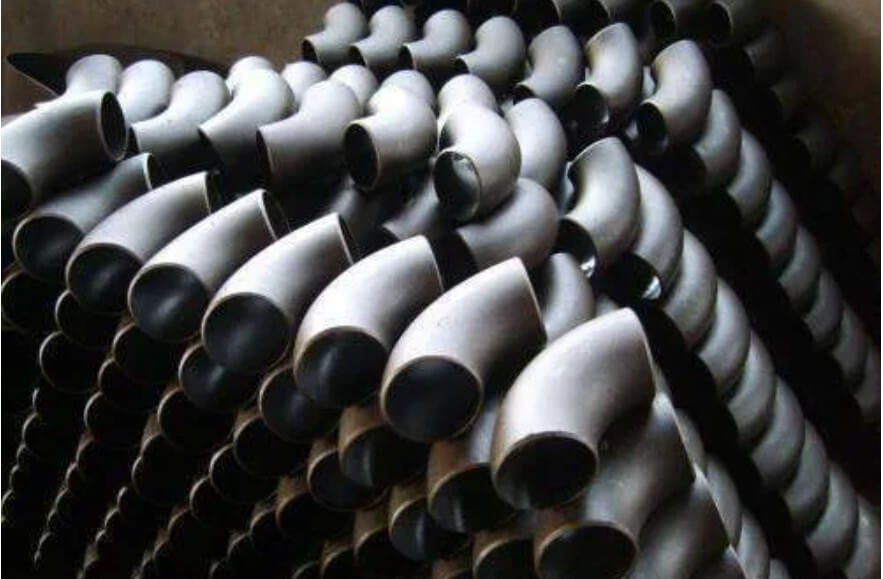
1) Low carbon steel:
The carbon content is less than 0.25%, with good plasticity and weldability, and is widely used in building structures and ordinary mechanical parts, such as bolts and nuts.
2) Medium carbon steel:
Carbon content is between 0.25% and 0.6%, with moderate strength and hardness, and is widely used in the manufacture of medium-strength mechanical parts, such as gears, shafts, etc.
3) High carbon steel:
Carbon content is higher than 0.6%, with high hardness and good wear resistance, and is mainly used to manufacture high-strength parts such as tools and springs.
(2) Cast iron
Cast iron is an iron-carbon alloy with a carbon content greater than 2%, in which carbon mainly exists in the form of graphite. The presence of graphite makes cast iron have good shock absorption, wear resistance and casting properties, but low tensile strength and plasticity. According to the different forms of graphite, cast iron can be divided into gray cast iron, ductile cast iron, vermicular cast iron, etc.
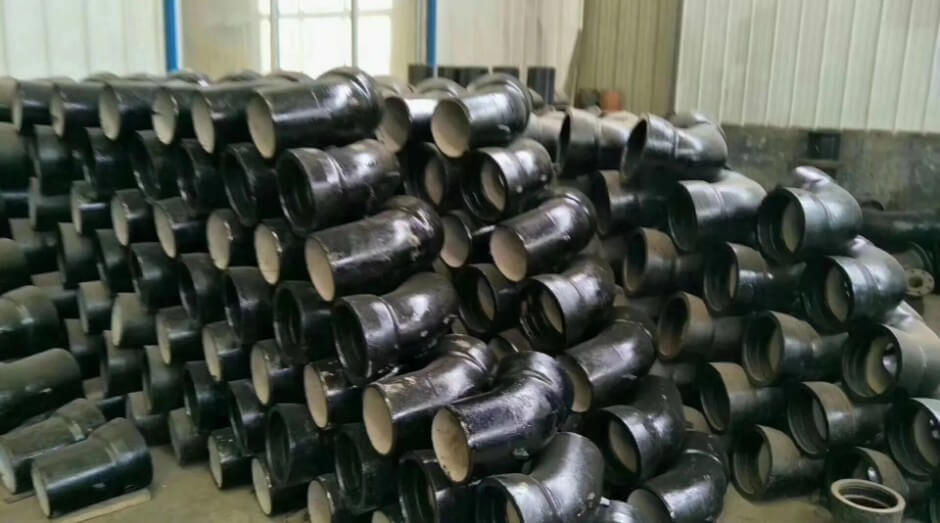
1) Gray cast iron:
Graphite is in the form of flakes and is widely used in the manufacture of machine tool beds, engine cylinders and other parts that require good shock absorption.
2) Ductile iron:
Graphite is spherical and has high strength and toughness. It is widely used in the manufacture of crankshafts, connecting rods and other parts with large forces.
3) Vermicular cast iron:
Graphite is worm-shaped, with strength and toughness between gray cast iron and ductile iron. It is widely used in the manufacture of automobile engine cylinder heads and other parts.
2.In-depth comparison of material properties of carbon steel vs cast iron
(1) Carbon steel vs cast iron: mechanical properties comparison
1) Strength and plasticity:
The strength of carbon steel is usually higher than that of cast iron, especially high carbon steel, but its plasticity is lower than that of cast iron. The graphite in cast iron splits the matrix, resulting in lower tensile strength but better plasticity.
2) Hardness and wear resistance:
High carbon steel can obtain high hardness and wear resistance after proper heat treatment, which is suitable for manufacturing tools, molds, etc. The graphite in cast iron has a certain self-lubricating effect, so it also has good wear resistance.

3) Toughness and fracture toughness:
The toughness of carbon steel is generally better than that of cast iron, especially low carbon steel and medium carbon steel. Graphite in cast iron can easily become a crack source, resulting in lower toughness and fracture toughness.
(2) Carbon steel vs cast iron: comparison of physical properties
1) Density:
The density of carbon steel is generally 7.85 g/cm³, while the density of cast iron is slightly lower, 7.2-7.4 g/cm³.
2) Thermal conductivity:
The thermal conductivity of carbon steel is higher than that of cast iron, and it is suitable for manufacturing parts that require rapid heat transfer or heat dissipation.
3) Linear expansion coefficient:
The linear expansion coefficient of carbon steel is slightly higher than that of cast iron, and its influence needs to be considered in environments with large temperature changes.
(3) Carbon steel vs cast iron: comparison of chemical properties
1) Corrosion resistance:
Carbon steel has poor corrosion resistance and is prone to rust. Graphite in cast iron has a certain protective effect, making its corrosion resistance slightly better than that of carbon steel.
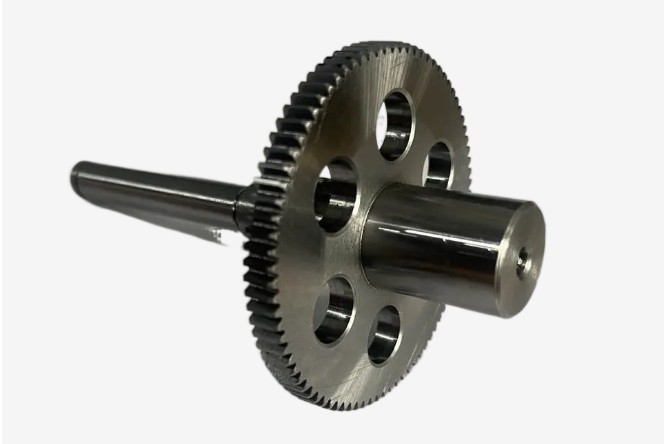
2) Antioxidation:
Carbon steel has poor oxidation resistance and is easily oxidized at high temperatures. The graphite in cast iron has a certain antioxidant effect, making its oxidation resistance slightly better than that of carbon steel.
3.Comparison of processing technology of carbon steel vs cast iron
(1) Processing technology of carbon steel:
1) Cold processing:
Including cold rolling, cold drawing, cold forging and other processes, which can improve the strength and hardness of carbon steel, but will reduce its plasticity and toughness.
2) Hot processing:
Including hot rolling, hot forging and other processes, which can improve the microstructure of carbon steel and improve its comprehensive mechanical properties.
3) Heat treatment:
Including quenching, tempering, normalizing, annealing and other processes, which can change the structure and performance of carbon steel to meet different use requirements.
(2) Processing technology of cast iron:
It is the main processing technology of cast iron, including sand casting, metal mold casting, pressure casting and other methods. Casting process can produce parts with complex shapes and large sizes.
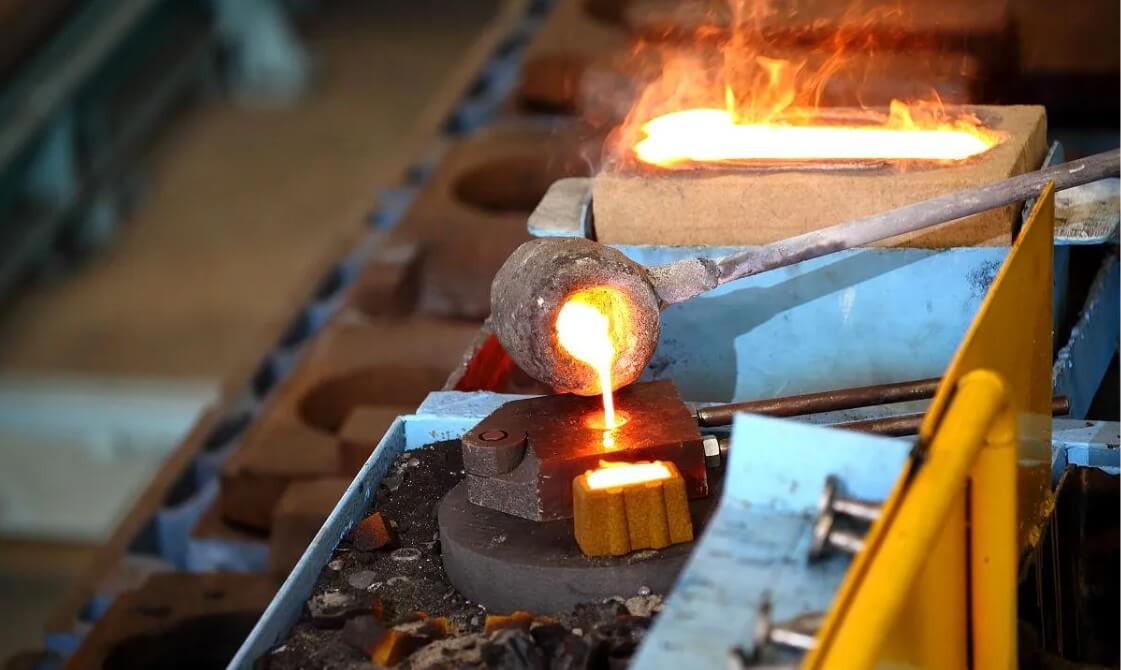
2) Cutting:
Cast iron has good cutting properties and can be processed by turning, milling, drilling and other methods.
3) Heat treatment:
The heat treatment of cast iron mainly includes annealing, normalizing, quenching, tempering and other processes, which can improve the structure and performance of cast iron and increase its strength and toughness.
4.Comparison of the application fields of carbon steel vs cast iron
(1) Application of carbon steel:
1) Construction industry:
Low carbon steel is widely used to manufacture steel bars, threaded steel, steel sections and other construction steel.
2) Machinery manufacturing:
Medium carbon steel is often used to manufacture important mechanical parts such as shafts and gears; high carbon steel is often used to manufacture tools such as knives and molds.
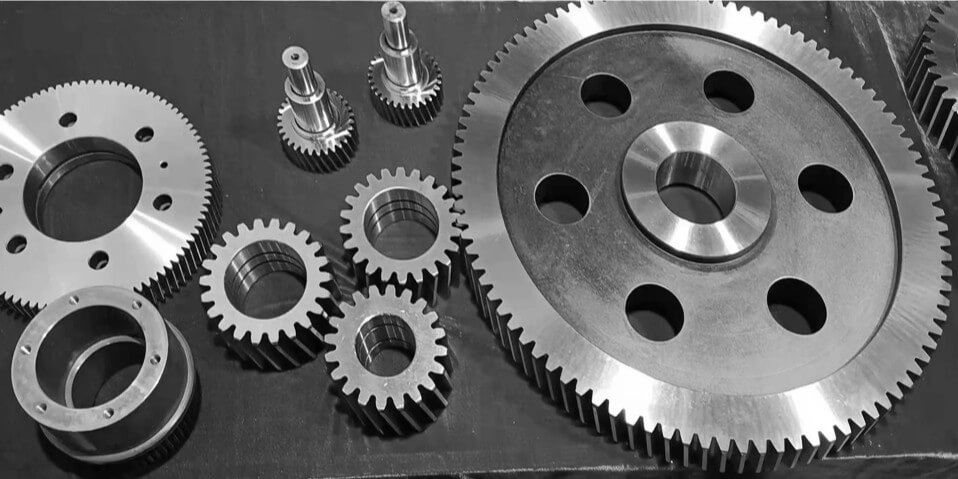
3) Automobile manufacturing:
Carbon steel is used to manufacture components such as frames and suspension systems in automobile manufacturing.
4) Aerospace:
High-strength carbon steel is used in the aerospace field to manufacture aircraft structural parts and engine components.
(2) Application of cast iron:
1) Mechanical manufacturing:
Gray cast iron is widely used to manufacture machine tool beds, engine cylinder blocks and other parts; ductile iron is often used to manufacture crankshafts, connecting rods and other important mechanical parts.
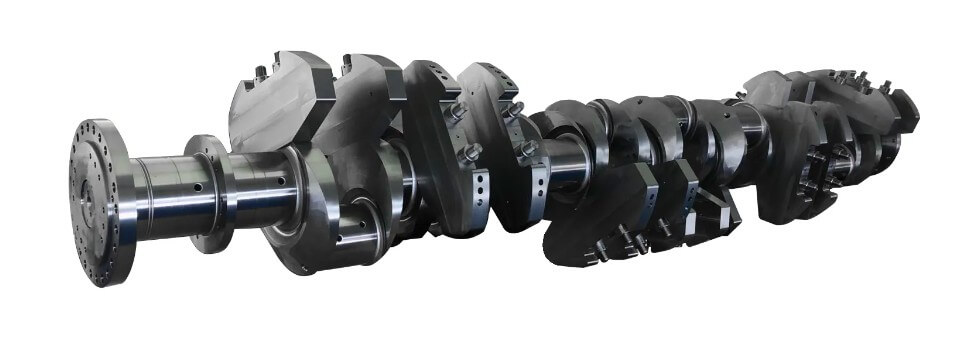
2) Pipeline system:
Cast iron pipes are widely used in urban water supply, drainage, gas and other pipeline systems.
3) Automobile manufacturing:
Cast iron is used to manufacture engine cylinder blocks, cylinder heads and other parts in automobile manufacturing.
4) Construction industry:
Cast iron is used to manufacture construction parts such as sewer covers and radiators.
5.Carbon steel vs cast iron: Which one to choose?
Choosing between these two metals requires understanding their advantages and disadvantages. The following is a summary of the advantages and disadvantages of carbon steel vs cast iron:
(1) Advantages and disadvantages of carbon steel
1) Advantages
●High strength, suitable for bearing large loads.
●Low manufacturing cost, raw materials are widely available and easy to obtain.
●Good processing performance, different parts can be formed through a variety of processing methods.
●Excellent welding performance, suitable for various welding methods
●Corrosion resistance can be improved through surface treatment.
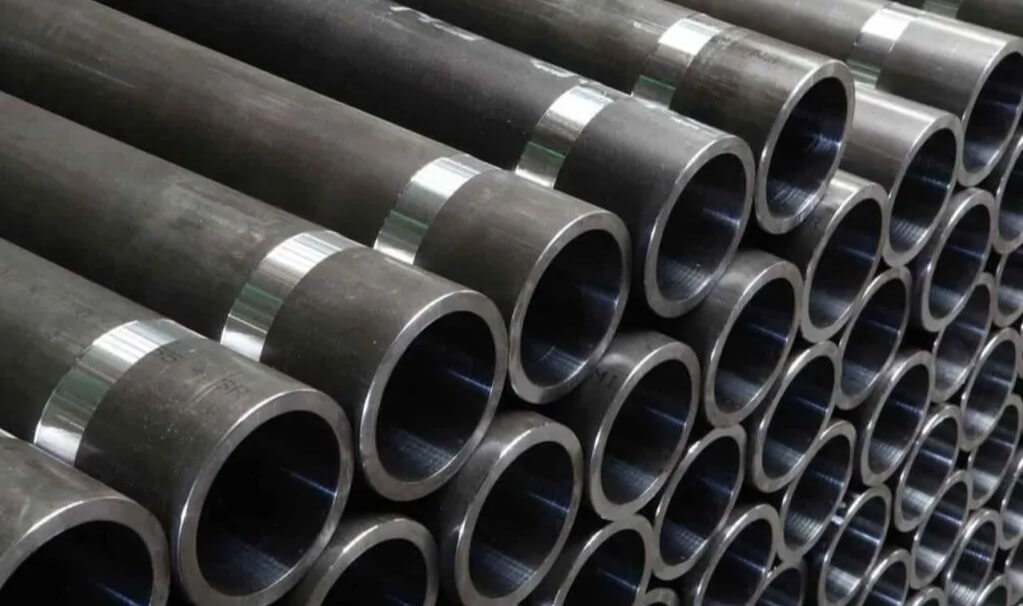
2) Disadvantages
●Easy to rust, especially in humid environment.
●Poor wear resistance and high temperature resistance.
●Easy to corrode in extreme environments, such as strong acid and strong alkali.
(2) Advantages and disadvantages of cast iron
1) Advantages
●Good fluidity, smooth casting surface, suitable for mass production.
●Low cost and simple production process.
●Strong pressure resistance, suitable for bearing static pressure.
●Good wear resistance and high oil storage capacity.
●Excellent casting performance, can manufacture parts with complex shapes.
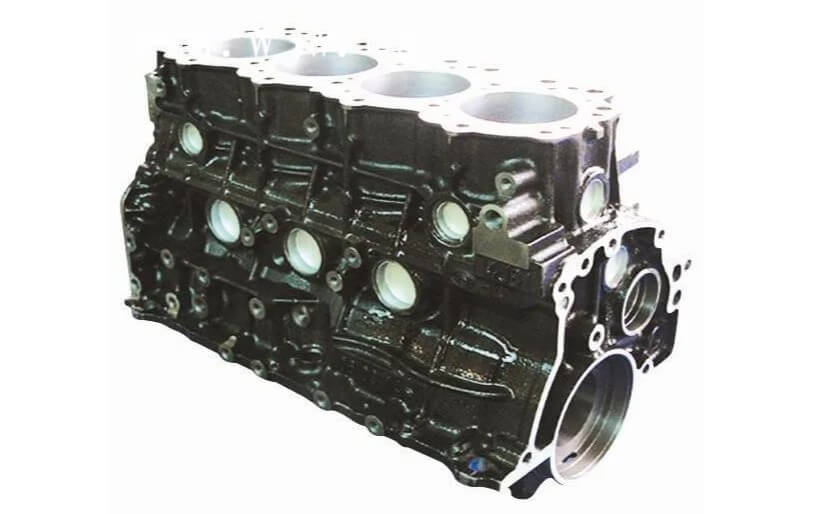
2) Disadvantages
●Poor tensile and impact resistance, not suitable for bearing dynamic loads.
●Low plasticity and toughness, cannot be forged.
●Poor welding performance, difficult welding.
After understanding the advantages and disadvantages of cast iron and steel, which material you ultimately choose to use will depend on your product requirements.
5.Summary
Carbon steel vs cast iron each have their own advantages and disadvantages in terms of material properties and processing technology. Carbon steel has the advantages of high strength, good plasticity, and good welding performance, but poor corrosion resistance and oxidation resistance. Cast iron has the advantages of good shock absorption, good wear resistance, and good casting performance, but low strength and plasticity.
In practical applications, appropriate materials should be selected according to specific needs. For example, parts that require high strength and high toughness should choose carbon steel, while parts that require good shock absorption and wear resistance should choose cast iron.
What do you think?
[…] choosing between cast iron vs stainless steel, the following factors need to be […]
[…] Stainless steel has very strong anti-oxidation and anti-corrosion properties, especially in special environments such as chemicals and oceans. […]
[…] with a certain proportion of alloying elements (such as Cr, Ni, Mo, Mn, V, etc.) added to ordinary carbon steel to improve its mechanical properties, corrosion resistance or other characteristics. Alloy steel is […]
[…] Low temperature resistance: In low temperature environments, choose low temperature steel or ductile iron. […]
[…] reason why cast iron casting is important is that the cast iron material itself has excellent mechanical properties, such as high strength, wear resistance and […]